Introduction to Multi-layer Boards
Multi-layer boards, also known as multi-layer printed circuit boards (PCBs), are essential components in modern electronic devices. These boards consist of multiple layers of conductive material, typically copper, separated by insulating layers. The conductive layers are interconnected through vias, which are small holes drilled through the board and plated with conductive material. Multi-layer boards offer several advantages over single-layer boards, including increased circuit density, improved signal integrity, and better electromagnetic interference (EMI) protection.
Advantages of Multi-layer Boards
- Increased circuit density
- Improved signal integrity
- Better EMI protection
- Reduced board size
- Enhanced mechanical stability
Structure of Multi-layer Boards
A multi-layer board is composed of several layers of conductive material, usually copper, separated by insulating layers made of materials such as FR-4, a glass-reinforced epoxy laminate. The number of layers in a multi-layer board can vary depending on the complexity of the circuit and the specific requirements of the application.
Common Multi-layer Board Configurations
Layers | Description |
---|---|
4 | Two signal layers, one power layer, and one ground layer |
6 | Four signal layers, one power layer, and one ground layer |
8 | Six signal layers, one power layer, and one ground layer |
10 | Eight signal layers, one power layer, and one ground layer |
Layer Stackup
The layer stackup refers to the arrangement of the conductive and insulating layers in a multi-layer board. A typical 4-layer board stackup might look like this:
- Top signal layer
- Ground layer
- Power layer
- Bottom signal layer
The signal layers are used for routing traces, while the power and ground layers provide a stable reference plane and help to reduce EMI.
Manufacturing Process
The manufacturing process for multi-layer boards involves several steps, including:
- Design and layout
- Layer preparation
- Lamination
- Drilling
- Plating
- Etching
- Solder mask application
- Silkscreen printing
- Surface finishing
Design and Layout
The first step in manufacturing a multi-layer board is to create a design and layout using electronic design automation (EDA) software. The layout must take into account the specific requirements of the circuit, such as signal integrity, power distribution, and EMI protection.
Layer Preparation
Each layer of the multi-layer board is prepared separately. The conductive material, typically copper foil, is laminated onto the insulating substrate using heat and pressure.
Lamination
Once the individual layers are prepared, they are stacked together in the desired order and laminated under high pressure and temperature. This process bonds the layers together to form a single, solid board.
Drilling
After lamination, holes are drilled through the board to accommodate components and vias. The drilling process is usually performed using computer numerical control (CNC) machines to ensure precision and accuracy.
Plating
The drilled holes are then plated with a conductive material, typically copper, to create electrical connections between the layers. This process is known as through-hole plating.
Etching
The unwanted copper is removed from the outer layers of the board using a chemical etching process. This process creates the desired circuit pattern on the board.
Solder Mask Application
A solder mask, which is a protective coating, is applied to the outer layers of the board. The solder mask helps to prevent short circuits and provides insulation between the copper traces.
Silkscreen Printing
A silkscreen layer is printed onto the board to add labels, logos, and other identifying marks. This layer is typically white and is used to improve the readability of the board.
Surface Finishing
Finally, a surface finish is applied to the exposed copper areas of the board to protect them from oxidation and improve solderability. Common surface finishes include hot air solder leveling (HASL), electroless nickel immersion gold (ENIG), and organic solderability preservative (OSP).
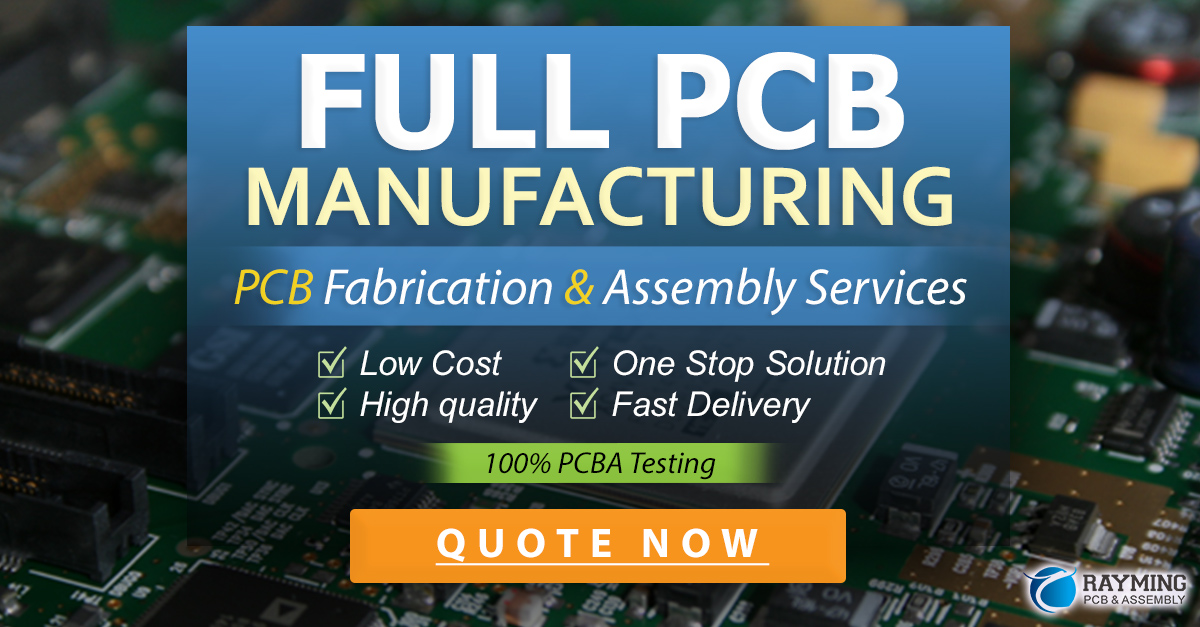
Applications of Multi-layer Boards
Multi-layer boards are used in a wide range of electronic devices, from consumer electronics to industrial and aerospace applications. Some common applications include:
- Smartphones and tablets
- Laptop and desktop computers
- Automotive electronics
- Medical devices
- Aerospace and defense systems
Consumer Electronics
Multi-layer boards are essential in consumer electronics, such as smartphones and laptops, where high circuit density and miniaturization are crucial. These boards enable manufacturers to pack more functionality into smaller devices while maintaining signal integrity and reducing EMI.
Industrial Applications
In industrial applications, multi-layer boards are used in control systems, automation equipment, and power electronics. These boards must be designed to withstand harsh environments, including extreme temperatures, vibrations, and exposure to chemicals.
Medical Devices
Multi-layer boards are used in various medical devices, such as patient monitors, imaging equipment, and implantable devices. These boards must meet strict regulatory requirements for safety and reliability.
Aerospace and Defense
In aerospace and defense applications, multi-layer boards are used in avionics, communications systems, and radar equipment. These boards must be designed to withstand extreme environmental conditions and meet stringent reliability and performance standards.
Design Considerations for Multi-layer Boards
Designing multi-layer boards requires careful consideration of several factors, including:
- Signal integrity
- Power distribution
- EMI protection
- Thermal management
- Manufacturing constraints
Signal Integrity
Maintaining signal integrity is crucial in multi-layer board design. Factors such as trace width, spacing, and impedance must be carefully controlled to minimize signal distortion and crosstalk.
Power Distribution
Proper power distribution is essential for ensuring the stable operation of the circuit. The power and ground layers in a multi-layer board help to distribute power evenly across the board and reduce voltage drops.
EMI Protection
Multi-layer boards must be designed to minimize electromagnetic interference (EMI) both within the board and with external devices. Techniques such as proper grounding, shielding, and filtering can help to reduce EMI.
Thermal Management
As circuit density increases, thermal management becomes increasingly important. Multi-layer boards must be designed to dissipate heat effectively to prevent component failure and ensure reliable operation.
Manufacturing Constraints
The design of a multi-layer board must also take into account manufacturing constraints, such as minimum trace width, hole size, and spacing requirements. Close collaboration between the design and manufacturing teams is essential to ensure a successful outcome.
Frequently Asked Questions (FAQ)
1. What is the difference between a multi-layer board and a single-layer board?
A single-layer board has only one layer of conductive material, typically copper, on one or both sides of the insulating substrate. In contrast, a multi-layer board has multiple layers of conductive material separated by insulating layers. Multi-layer boards offer several advantages over single-layer boards, including increased circuit density, improved signal integrity, and better EMI protection.
2. How many layers can a multi-layer board have?
The number of layers in a multi-layer board can vary depending on the complexity of the circuit and the specific requirements of the application. Common configurations include 4, 6, 8, and 10 layers, but boards with even more layers are possible. The practical limit is determined by factors such as manufacturing capabilities, cost, and design constraints.
3. What materials are used in the construction of multi-layer boards?
Multi-layer boards typically use copper as the conductive material and FR-4, a glass-reinforced epoxy laminate, as the insulating substrate. Other materials, such as polyimide or ceramic, may be used in specialized applications that require high temperature tolerance or low dielectric constant.
4. What is the purpose of vias in multi-layer boards?
Vias are small holes drilled through the multi-layer board and plated with conductive material, typically copper. Their purpose is to create electrical connections between the different layers of the board, allowing signals to be routed from one layer to another.
5. How does the manufacturing process for multi-layer boards differ from that of single-layer boards?
The manufacturing process for multi-layer boards is more complex than that of single-layer boards. It involves additional steps, such as layer preparation, lamination, and through-hole plating, to create the multiple layers and interconnections. The process also requires more advanced equipment and skilled personnel to ensure precision and reliability.
Conclusion
Multi-layer boards are essential components in modern electronic devices, offering increased circuit density, improved signal integrity, and better EMI protection compared to single-layer boards. The manufacturing process for multi-layer boards involves several steps, including design and layout, layer preparation, lamination, drilling, plating, etching, solder mask application, silkscreen printing, and surface finishing.
Designing multi-layer boards requires careful consideration of factors such as signal integrity, power distribution, EMI protection, thermal management, and manufacturing constraints. Close collaboration between the design and manufacturing teams is essential to ensure a successful outcome.
As electronic devices continue to become more complex and miniaturized, the importance of multi-layer boards will only continue to grow. By understanding the structure, manufacturing process, and design considerations of multi-layer boards, engineers and designers can create more advanced and reliable electronic systems to meet the evolving needs of various industries, from consumer electronics to aerospace and defense.
Leave a Reply