What is a PCB Via?
A PCB via, short for Printed Circuit Board via, is a small hole drilled through a PCB to create an electrical connection between different layers of the board. Vias allow signals and power to pass from one layer of the PCB to another, enabling more complex routing and circuit design.
Vias are essential components in modern PCB design, as they allow for higher density layouts and more efficient use of board space. Without vias, PCBs would be limited to single-layer designs, severely restricting their functionality and applications.
Types of PCB Vias
There are several types of PCB vias, each with its own characteristics and applications:
Through-hole Vias
Through-hole vias are the most common type of via. They are drilled through the entire thickness of the PCB and are typically plated with a conductive material, such as copper, to create an electrical connection between layers. Through-hole vias are reliable and provide strong mechanical support, but they occupy more board space compared to other via types.
Blind Vias
Blind vias are drilled from one side of the PCB and terminate at a specific inner layer, rather than passing through the entire board. Blind vias are useful for connecting an outer layer to an inner layer, without the need for the via to extend to the opposite side of the board. This allows for more compact designs and improved signal integrity.
Buried Vias
Buried vias are located entirely within the inner layers of a PCB and do not extend to either outer layer. They are used to connect two or more inner layers without occupying space on the outer layers. Buried vias are typically more expensive to manufacture than through-hole or blind vias, as they require additional processing steps.
Micro Vias
Micro vias are small-diameter vias, typically less than 150 microns (0.15 mm) in diameter. They are used in high-density PCB designs to create connections between fine-pitch components and to minimize signal loss and distortion. Micro vias are usually laser-drilled and can be stacked to create complex interconnections between multiple layers.
PCB Via Size Guidelines
Choosing the appropriate via size is crucial for ensuring proper electrical connections, signal integrity, and manufacturability. The following table provides general guidelines for selecting PCB via sizes based on common PCB Thicknesses and drill bit sizes:
PCB Thickness | Drill Bit Size | Finished Hole Diameter | Annular Ring |
---|---|---|---|
0.8 mm | 0.2 mm | 0.4 mm | 0.2 mm |
1.6 mm | 0.3 mm | 0.6 mm | 0.3 mm |
2.4 mm | 0.4 mm | 0.8 mm | 0.4 mm |
The annular ring refers to the minimum width of the copper pad surrounding the via hole. It is important to maintain a sufficient annular ring to ensure proper electrical connection and mechanical strength.
When selecting via sizes, it is also essential to consider the current-carrying capacity of the via. The following table provides approximate current-carrying capacities for various via sizes, based on a 10°C temperature rise:
Via Diameter | Current-Carrying Capacity |
---|---|
0.2 mm | 0.5 A |
0.3 mm | 1.0 A |
0.4 mm | 1.5 A |
0.5 mm | 2.0 A |
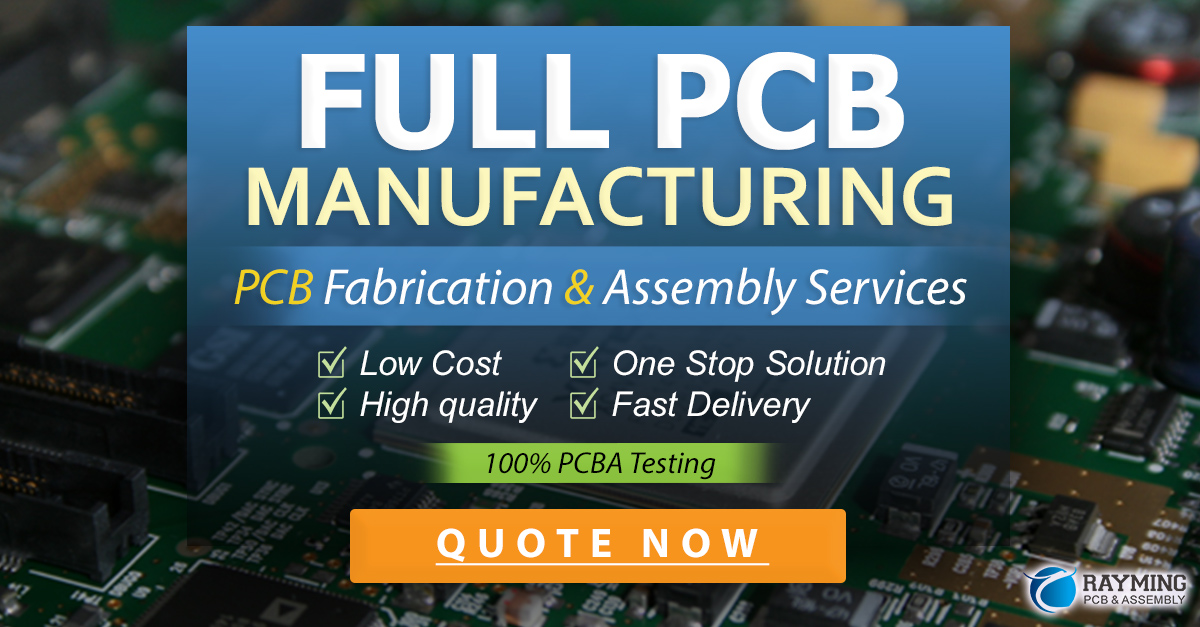
Via Placement and Routing Considerations
When placing and routing vias on a PCB, several factors should be considered to ensure optimal performance and manufacturability:
Via-to-Pad Clearance
Maintain adequate clearance between vias and component pads to prevent short circuits and to allow for proper soldering. The minimum via-to-pad clearance depends on the PCB manufacturing capabilities and the specific design requirements.
Via-to-Via Clearance
Ensure sufficient spacing between adjacent vias to prevent drilling and plating issues during manufacturing. The minimum via-to-via clearance is typically determined by the PCB manufacturer’s capabilities and the via size.
Signal Integrity
Consider the impact of vias on signal integrity, particularly for high-speed designs. Vias can introduce discontinuities in the signal path, leading to reflections, crosstalk, and other issues. To minimize these effects, use appropriate via sizes, maintain proper spacing, and employ techniques such as via stitching and ground shielding when necessary.
Thermal Management
Vias can be used to transfer heat from components to other layers of the PCB or to external heatsinks. Thermal vias, which are typically filled with a thermally conductive material, can improve heat dissipation and help maintain component temperatures within acceptable limits.
PCB Via Manufacturing Process
The manufacturing process for PCB vias involves several steps:
-
Drilling: Holes are drilled through the PCB substrate using specialized drilling machines. The drill bit size determines the initial via hole diameter.
-
Deburring: The drilled holes are deburred to remove any rough edges or debris that may interfere with the plating process.
-
Plating: The via holes are plated with a conductive material, typically copper, using an electroplating process. This creates the electrical connection between layers.
-
Filling (optional): For certain applications, such as high-density designs or thermal management, the vias may be filled with a non-conductive or thermally conductive material to improve performance and reliability.
-
Finish Coating: The PCB, including the vias, may receive a final finish coating, such as solder mask or surface finish, to protect the copper and enhance solderability.
Frequently Asked Questions (FAQ)
1. What is the minimum via size that can be manufactured?
The minimum via size depends on the PCB manufacturer’s capabilities and the specific design requirements. Most PCB manufacturers can produce vias with diameters as small as 0.2 mm, while some advanced facilities can produce micro vias with diameters down to 0.1 mm or less.
2. How do I calculate the current-carrying capacity of a via?
The current-carrying capacity of a via depends on several factors, including the via diameter, the thickness of the copper plating, and the allowable temperature rise. As a general rule of thumb, a 0.3 mm diameter via can carry approximately 1 A of current with a 10°C temperature rise. For more accurate calculations, consult the IPC-2221 standard or use online via current capacity calculators.
3. Can vias be used for thermal management?
Yes, vias can be used for thermal management by transferring heat from components to other layers of the PCB or to external heatsinks. Thermal vias, which are typically filled with a thermally conductive material, can improve heat dissipation and help maintain component temperatures within acceptable limits.
4. What is via stitching, and when is it used?
Via stitching is a technique used in high-speed PCB designs to minimize the impact of vias on signal integrity. It involves placing multiple small vias around a larger signal via to create a low-impedance path for the return current. Via stitching helps reduce the discontinuity caused by the signal via, minimizing reflections and improving signal quality.
5. How do I choose the appropriate via size for my PCB design?
When choosing the appropriate via size for your PCB design, consider factors such as the PCB thickness, the required current-carrying capacity, the component pad sizes, and the PCB manufacturer’s capabilities. Consult the PCB manufacturer’s design guidelines and use the general recommendations provided in this article as a starting point. For critical designs, perform simulations and testing to validate the via size selection.
Conclusion
PCB vias are essential components in modern PCB design, enabling the creation of complex, high-density layouts with multiple layers. Understanding the different types of vias, their sizes, and their manufacturing process is crucial for designing reliable and high-performance PCBs.
When selecting via sizes and placing them on a PCB, consider factors such as current-carrying capacity, signal integrity, thermal management, and manufacturability. Consult PCB manufacturer guidelines and industry standards, such as IPC-2221, to ensure your design meets the necessary requirements.
By following best practices for via selection and placement, you can create PCBs that are reliable, efficient, and cost-effective, while meeting the demands of today’s advanced electronic applications.
Leave a Reply