Introduction to PCB Solver
PCB Solver is a powerful and user-friendly software tool designed to streamline the process of creating and editing printed circuit board (PCB) outlines and milling paths. This comprehensive solution offers a wide range of features and capabilities that cater to the needs of PCB designers, manufacturers, and hobbyists alike. With its intuitive interface and advanced algorithms, PCB Solver simplifies the complex task of designing and optimizing PCB layouts, enabling users to achieve high-quality results with ease.
Key Features of PCB Solver
- Intuitive Outline Editor
- Advanced Milling Path Generation
- Comprehensive Design Rule Checks (DRC)
- Extensive Library of Components and Footprints
- Seamless Integration with Popular CAD Tools
The Importance of Accurate PCB Outlines and Milling Paths
Printed circuit boards form the backbone of modern electronic devices, providing a reliable and efficient means of interconnecting various components. The accuracy and precision of PCB outlines and milling paths play a crucial role in ensuring the proper functioning, reliability, and manufacturability of these boards. Here are some key reasons why accurate PCB outlines and milling paths are essential:
1. Ensuring Proper Component Placement
PCB outlines define the physical boundaries of the board and the locations of components. Accurate outlines ensure that components are placed correctly and have sufficient clearance from the board edges and other components. This is particularly important for surface-mount devices (SMDs) and high-density designs where space is limited.
2. Facilitating Smooth Manufacturing Processes
Milling paths determine the routes that CNC machines follow when cutting and drilling the PCB. Precise milling paths are essential for achieving clean and accurate cuts, minimizing the risk of damage to the board or components during the manufacturing process. Well-defined milling paths also help to reduce manufacturing time and costs by optimizing the machine’s movements.
3. Maintaining Signal Integrity
The placement and routing of traces on a PCB can significantly impact signal integrity. Accurate outlines and milling paths help to ensure that traces are routed correctly, maintaining proper spacing and avoiding potential signal interference issues. This is particularly critical for high-speed and high-frequency designs where signal integrity is paramount.
4. Enhancing Reliability and Durability
Precise PCB outlines and milling paths contribute to the overall reliability and durability of the final product. By ensuring accurate cuts and proper component placement, the risk of mechanical stress, vibration-induced failures, and short circuits is minimized. This leads to higher quality products with longer lifespans and reduced maintenance requirements.
PCB Solver’s Outline Editor
The Outline Editor in PCB Solver is a comprehensive tool that allows users to create, modify, and optimize PCB outlines with ease. It offers a wide range of features and capabilities that cater to the needs of both novice and experienced PCB designers. Let’s explore some of the key features of the Outline Editor:
1. Intuitive User Interface
PCB Solver’s Outline Editor features a clean and intuitive user interface that makes it easy for users to navigate and access various tools and functions. The interface is designed to be user-friendly, with clear icons, tooltips, and context-sensitive menus that guide users through the design process.
2. Precise Drawing Tools
The Outline Editor provides a comprehensive set of drawing tools that enable users to create accurate and detaiLED PCB outlines. These tools include:
- Line and polyline tools for creating straight and angled edges
- Arc and circle tools for creating curved sections
- Rectangle and polygon tools for creating regular shapes
- Freehand drawing tools for custom shapes and contours
These tools offer precise control over the placement and dimensions of outline elements, ensuring accurate and consistent results.
3. Powerful Editing Capabilities
In addition to drawing tools, the Outline Editor offers a range of editing capabilities that allow users to modify and refine their PCB outlines. These include:
- Move, rotate, and scale tools for adjusting the position and size of outline elements
- Trim and extend tools for modifying the length and endpoints of lines and arcs
- Fillet and chamfer tools for adding rounded or angled corners to outline edges
- Boolean operations (union, subtraction, intersection) for combining or modifying multiple outline shapes
These editing tools provide users with the flexibility to make precise adjustments and refinements to their PCB outlines, ensuring optimal results.
4. Design Rule Checks (DRC)
PCB Solver’s Outline Editor includes a powerful Design Rule Check (DRC) engine that automatically verifies the PCB outline against a set of predefined design rules. These rules can be customized based on the specific requirements of the project or manufacturing process. The DRC engine checks for various issues, such as:
- Minimum and maximum board dimensions
- Clearance between outline elements and components
- Hole sizes and placement
- Manufacturability constraints (e.g., minimum slot width, corner radius)
By running DRC checks, users can quickly identify and resolve any design issues, ensuring that their PCB outlines are compliant with the necessary design rules and manufacturing constraints.
5. Collaborative Design Features
PCB Solver’s Outline Editor supports collaborative design workflows, enabling multiple users to work on the same PCB outline simultaneously. The software offers features such as:
- Real-time synchronization of changes made by multiple users
- Version control and revision history tracking
- User permissions and access control
- Comment and annotation tools for communication and feedback
These collaborative features streamline the design process, allowing teams to work together efficiently and effectively, regardless of their physical location.
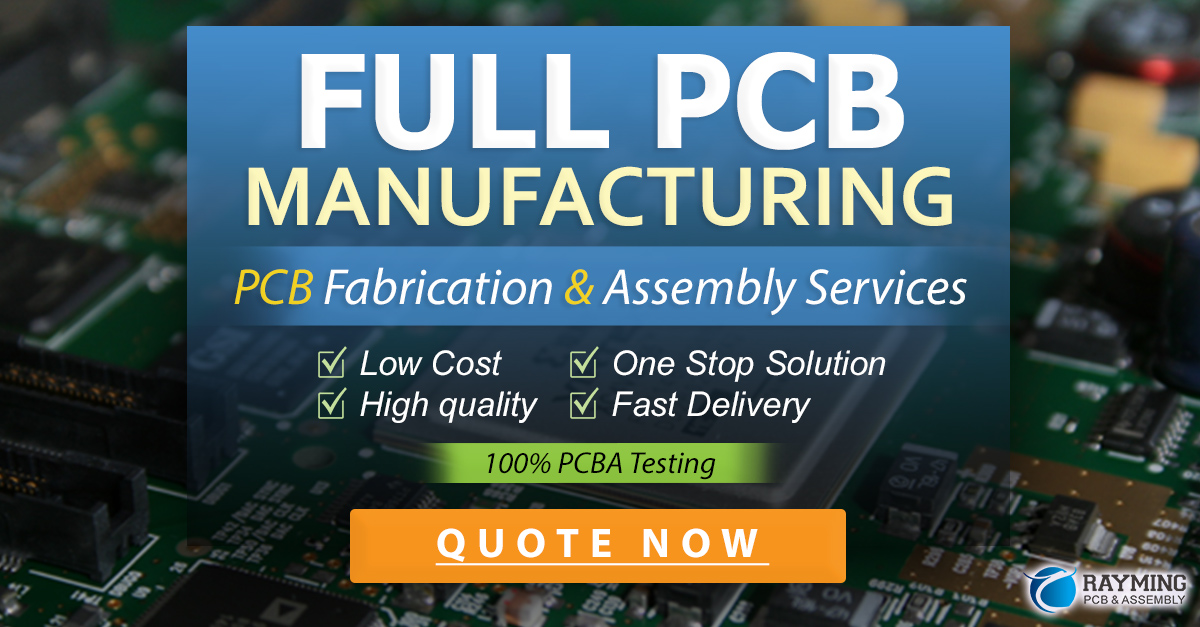
PCB Solver’s Milling Editor
In addition to the Outline Editor, PCB Solver offers a powerful Milling Editor that enables users to generate and optimize milling paths for their PCB designs. The Milling Editor uses advanced algorithms to calculate the most efficient and accurate milling paths, taking into account various factors such as tool diameter, cutting depth, and material properties. Let’s explore some of the key features of the Milling Editor:
1. Automatic Milling Path Generation
PCB Solver’s Milling Editor can automatically generate milling paths based on the PCB outline and the specified milling parameters. Users can define the tool diameter, cutting depth, and other relevant settings, and the software will calculate the optimal milling paths that ensure accurate and efficient cutting. This automated process saves significant time and effort compared to manual milling path creation.
2. Customizable Milling Strategies
The Milling Editor offers a range of customizable milling strategies that cater to different design requirements and manufacturing processes. These strategies include:
- Contour milling: Cuts along the outline of the PCB, following the exact shape of the board
- Pocket milling: Removes material within a specified area, creating cavities or pockets in the PCB
- Drill milling: Creates holes and vias in the PCB using specialized drill bits
- Isolation milling: Cuts around individual components or areas to electrically isolate them from the rest of the board
Users can select and configure the appropriate milling strategy based on their specific needs, ensuring optimal results and efficiency.
3. Tool Library and Management
PCB Solver’s Milling Editor includes a comprehensive library of milling tools, allowing users to select the appropriate tool for each milling operation. The library contains a wide range of tool types, including end mills, drill bits, and specialized cutters, each with its own dimensions and cutting properties. Users can also add custom tools to the library, ensuring flexibility and compatibility with their specific manufacturing setup.
4. Simulation and Visualization
The Milling Editor provides a powerful simulation and visualization environment that allows users to preview and analyze their milling paths before committing to the actual manufacturing process. The simulation features include:
- 3D visualization of the milling process, showing the tool movements and material removal in real-time
- Collision detection and avoidance, highlighting any potential issues with tool paths or PCB geometry
- Estimation of milling time and tool wear, helping users optimize their manufacturing process
- Generation of G-code or other machine-specific output for direct integration with CNC machines
By leveraging these simulation and visualization capabilities, users can identify and resolve any potential issues early in the design process, reducing the risk of costly mistakes and ensuring smooth manufacturing.
5. Post-Processing and Output Generation
Once the milling paths have been generated and optimized, PCB Solver’s Milling Editor offers a range of post-processing and output generation options. These include:
- Generation of G-code or other machine-specific output formats for direct integration with CNC machines
- Creation of detailed milling reports, including tool usage, milling time, and material consumption
- Export of milling paths and PCB geometry in various file formats (e.g., DXF, Gerber, ODB++) for use in other CAD or CAM software
These post-processing and output generation features ensure seamless integration with existing manufacturing workflows and equipment, streamlining the overall PCB Production process.
Integrating PCB Solver with Other CAD Tools
PCB Solver is designed to integrate seamlessly with popular CAD tools used in the electronics industry. This integration allows users to leverage the powerful features of PCB Solver while maintaining compatibility with their existing design workflows and software ecosystem. Here are some of the key integration capabilities of PCB Solver:
1. Import and Export of PCB Design Files
PCB Solver supports the import and export of various PCB design file formats, including:
- Gerber files (RS-274X)
- ODB++ files
- IPC-2581 files
- DXF and DWG files (AutoCAD)
- Altium Designer files
This wide range of file format support ensures that users can easily transfer their PCB designs between PCB Solver and other CAD tools, facilitating a smooth and efficient design process.
2. Direct Plugin Integration
PCB Solver offers direct plugin integration with popular CAD tools such as Altium Designer, KiCad, and Eagle. These plugins allow users to access PCB Solver’s features and functionality directly from within their preferred CAD environment. The plugins provide a seamless and intuitive workflow, enabling users to:
- Launch PCB Solver’s Outline and Milling Editors directly from the CAD tool’s interface
- Synchronize PCB design changes between the CAD tool and PCB Solver in real-time
- Access PCB Solver’s library of components and footprints directly from the CAD tool
- Run Design Rule Checks (DRC) and generate manufacturing outputs (e.g., G-code) from within the CAD environment
By leveraging these plugin integrations, users can take full advantage of PCB Solver’s capabilities without disrupting their existing design workflows or having to switch between multiple software tools.
3. API and Scripting Support
For users who require more advanced integration or automation capabilities, PCB Solver offers a comprehensive API (Application Programming Interface) and scripting support. The API allows developers to programmatically access and control various aspects of PCB Solver’s functionality, enabling the creation of custom plugins, scripts, and automated workflows. Some of the key features of the API include:
- Access to PCB Solver’s core functions and algorithms, such as outline creation, milling path generation, and DRC checks
- Ability to read, modify, and write PCB design data, including outlines, components, and milling parameters
- Integration with popular programming languages such as Python, C++, and JavaScript
- Comprehensive documentation and code samples to facilitate development and customization
By leveraging the API and scripting capabilities, users can create custom tools and workflows that are tailored to their specific needs, further enhancing the flexibility and power of PCB Solver.
Frequently Asked Questions (FAQ)
1. Is PCB Solver suitable for both beginners and experienced PCB designers?
Yes, PCB Solver is designed to cater to the needs of both novice and experienced PCB designers. The software offers a user-friendly interface and intuitive tools that make it easy for beginners to get started with PCB design. At the same time, it provides advanced features and customization options that allow experienced designers to tackle complex projects and optimize their workflows.
2. Can PCB Solver handle high-density and multi-layer PCB designs?
Absolutely. PCB Solver is capable of handling a wide range of PCB designs, including high-density and Multi-layer Boards. The software’s powerful algorithms and optimization techniques ensure accurate and efficient outline creation and milling path generation, even for complex designs with tight tolerances and numerous components.
3. Does PCB Solver support custom design rules and manufacturing constraints?
Yes, PCB Solver allows users to define and customize design rules and manufacturing constraints based on their specific requirements. The software’s Design Rule Check (DRC) engine can be configured to check for a wide range of parameters, such as minimum trace widths, clearances, hole sizes, and more. This flexibility ensures that PCB designs are compliant with the necessary standards and manufacturing processes.
4. Can I use PCB Solver with my existing CNC machines and manufacturing equipment?
PCB Solver is designed to be compatible with a wide range of CNC machines and manufacturing equipment. The software can generate machine-specific output files, such as G-code, that can be directly loaded and executed by your CNC machines. Additionally, PCB Solver’s post-processing options allow you to customize the output files to match the specific requirements of your manufacturing setup.
5. What kind of support and resources are available for PCB Solver users?
PCB Solver offers a comprehensive range of support and resources to help users get the most out of the software. These include:
- Detailed user documentation and tutorials that cover all aspects of PCB Solver’s functionality
- Online knowledge base and FAQ section for quick answers to common questions
- Community forums where users can connect, share experiences, and seek advice from peers
- Dedicated technical support team available via email, phone, or live chat to assist with any issues or inquiries
- Regular software updates and enhancements based on user feedback and industry trends
By leveraging these support and resource options, PCB Solver users can continuously improve their skills, stay up-to-date with the latest features, and overcome any challenges they may encounter during the PCB design and manufacturing process.
Conclusion
PCB Solver is a powerful and comprehensive software solution that streamlines the process of creating and editing PCB outlines and milling paths. With its intuitive Outline Editor, advanced Milling Editor, and seamless integration with popular CAD tools, PCB Solver empowers users to design and manufacture high-quality PCBs with ease and efficiency.
By leveraging PCB Solver’s wide range of features and capabilities, users can:
- Create accurate and detailed PCB outlines using precise drawing and editing tools
- Generate optimal milling paths that ensure efficient and accurate manufacturing
- Verify PCB designs against customizable design rules and constraints
- Simulate and visualize the milling process to identify and resolve potential issues
- Integrate seamlessly with existing CAD tools and manufacturing workflows
- Access comprehensive support and resources to continuously improve their skills and knowledge
Whether you are a novice designer looking to get started with PCB design or an experienced professional seeking to optimize your workflows, PCB Solver offers a robust and flexible solution that can adapt to your specific needs and requirements. With its commitment to innovation, user-centric design, and continuous improvement, PCB Solver is poised to revolutionize the way PCBs are designed and manufactured, empowering users to bring their electronic visions to life with unparalleled precision and efficiency.
Leave a Reply