What are PCB Pins?
PCB pins are small, conductive components that are soldered onto a printed circuit board (PCB) to create electrical connections between different parts of the board or to external devices. These pins come in various shapes, sizes, and configurations to suit different needs and applications.
Types of PCB Pins
There are several types of PCB pins available, each with its own unique features and benefits. Some of the most common types include:
-
Through-hole Pins: These pins have long legs that pass through holes drilled in the PCB and are soldered on the opposite side. They provide a strong mechanical connection and are suitable for high-stress applications.
-
Surface Mount Pins: Also known as SMD pins, these are designed to be soldered directly onto the surface of the PCB without requiring holes. They are smaller and more compact than through-hole pins, making them ideal for high-density designs.
-
Press-fit Pins: These pins are designed to be pressed into Plated-through Holes on the PCB, creating a secure connection without the need for soldering. They are often used in high-volume production and applications where soldering is not practical.
-
Spring-loaded Pins: Also called pogo pins, these pins contain a spring-loaded mechanism that allows them to compress and maintain contact with the mating surface. They are commonly used in test fixtures, programming jigs, and battery connectors.
Applications of PCB Pins
PCB pins find applications in a wide range of electronic projects and devices. Some common uses include:
Connectors
PCB pins are extensively used in various types of connectors, such as:
-
Header Connectors: These are rows of pins that mate with corresponding female sockets, allowing easy connection and disconnection of modules or peripherals to the main board.
-
Board-to-Board Connectors: PCB pins are used to create connections between two PCBs, enabling communication and power transfer between them.
-
Wire-to-Board Connectors: Pins are used to terminate wires or cables and provide a secure connection to the PCB.
Programming and Debugging
PCB pins play a crucial role in programming and debugging electronic devices. They are used to create temporary connections between the device and the programming or debugging tools, allowing access to the device’s firmware and hardware.
Test Points
Test points are strategically placed PCB pins that provide access to specific signals or nodes on the board for testing and measurement purposes. They enable engineers to probe and diagnose issues during development and troubleshooting.
Mechanical Support
In some cases, PCB pins are used for mechanical support rather than electrical connectivity. They can serve as standoffs, spacers, or mounting points to provide structural integrity to the PCB Assembly.
Choosing the Right PCB Pins
When selecting PCB pins for your project, consider the following factors:
-
Pin Pitch: The pitch refers to the distance between the centers of adjacent pins. Common pitches include 2.54mm (0.1 inches), 2.00mm, and 1.27mm. Choose a pitch that matches your PCB layout and the mating connectors or sockets.
-
Pin Length: Consider the required length of the pins based on your PCB Thickness, component heights, and any clearance requirements. Ensure that the pins are long enough to provide a secure connection but not so long that they introduce unnecessary signal integrity issues.
-
Current Rating: Select pins with an appropriate current rating to handle the expected current flow in your application. This is particularly important for power connectors and high-current circuits.
-
Plating Material: PCB pins are typically plated with materials like gold, tin, or nickel to improve conductivity and prevent oxidation. Choose a plating material that suits your environment and performance requirements.
-
Mechanical Strength: Consider the mechanical stress and strain that the pins will be subjected to during assembly and operation. Choose pins with adequate strength and durability to withstand the expected conditions.
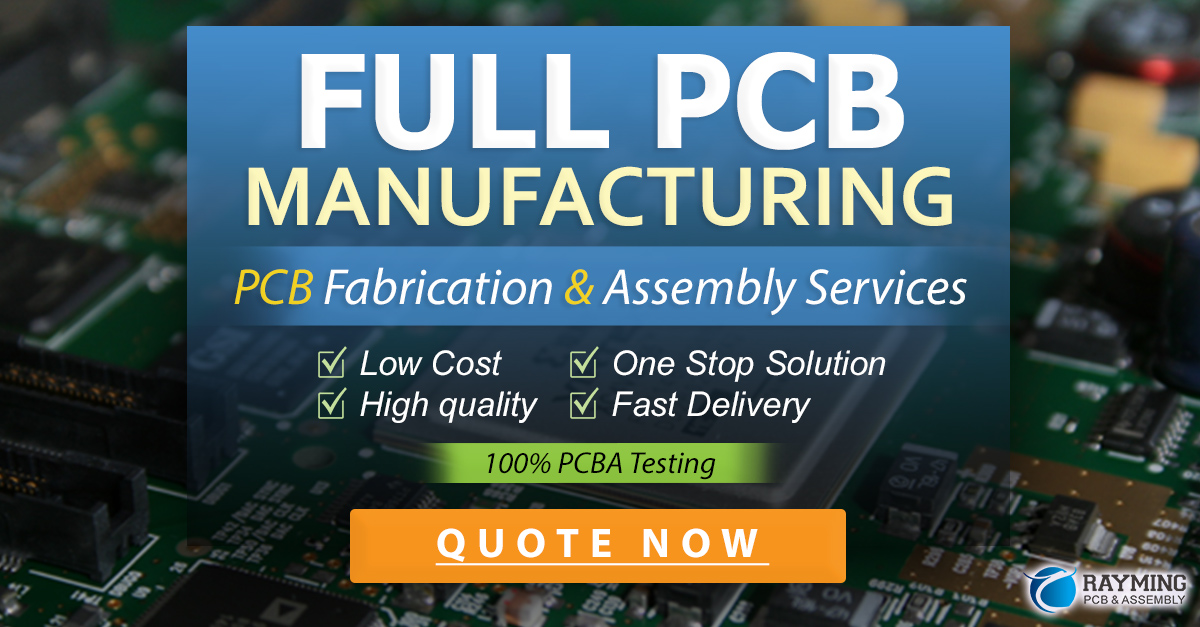
Soldering PCB Pins
Proper soldering techniques are essential for creating reliable connections between PCB pins and the board. Here are some tips for soldering PCB pins:
-
Use the Right Soldering Iron: Select a soldering iron with an appropriate wattage and tip size for your pins. A temperature-controlled iron is recommended for consistent results.
-
Apply Flux: Apply a small amount of flux to the pin and the PCB Pad before soldering. Flux helps to clean the surfaces, promote wetting, and prevent oxidation during the soldering process.
-
Preheat the Joint: Gently touch the soldering iron tip to both the pin and the PCB pad to preheat the joint. This helps to ensure even heat distribution and prevents thermal shock.
-
Apply Solder: Feed solder wire onto the joint while maintaining contact with the soldering iron. Allow the solder to flow around the pin and create a smooth, shiny fillet.
-
Inspect the Joint: After soldering, visually inspect the joint for any defects such as cold joints, bridging, or insufficient solder coverage. Use a magnifying glass or microscope for detailed inspection.
Best Practices for Using PCB Pins
To ensure the best performance and reliability of your PCB pin connections, follow these best practices:
-
Design for Manufacturability: When designing your PCB, consider the placement and spacing of pins to facilitate easy assembly and soldering. Provide adequate clearance around the pins for tools and inspection.
-
Use Appropriate Headers: Select headers with the correct number of pins, pitch, and orientation for your application. Consider using polarized headers or keyed connectors to prevent incorrect mating.
-
Maintain Signal Integrity: For high-speed or sensitive signals, choose pins with controlled impedance and minimize the pin length to reduce parasitic effects. Consider using ground pins or shielding to mitigate crosstalk and interference.
-
Implement Strain Relief: If your PCB will be subjected to mechanical stress or vibration, use strain relief techniques such as cable ties, clamps, or potting to prevent damage to the pin connections.
-
Perform Regular Maintenance: Periodically inspect and clean your PCB pin connections to ensure they remain in good condition. Look for signs of corrosion, loose pins, or damaged insulation, and take corrective action as needed.
Frequently Asked Questions (FAQ)
-
Q: Can I mix different types of PCB pins on the same board?
A: Yes, you can use different types of PCB pins on the same board, as long as they are compatible with your PCB design and the mating connectors or sockets. However, it’s important to consider the different soldering requirements and mechanical properties of each type of pin. -
Q: How do I determine the current rating of PCB pins?
A: The current rating of PCB pins depends on factors such as the pin size, material, and plating thickness. Manufacturers typically provide current rating information in their datasheets or specifications. As a general rule, larger pins with thicker plating can handle higher currents. -
Q: Can I replace a damaged PCB pin?
A: In some cases, it may be possible to replace a damaged PCB pin by desoldering the old pin and soldering a new one in its place. However, this process requires careful attention to avoid damaging the PCB or surrounding components. If the damage is extensive or the pin is part of a complex connector, it may be more practical to replace the entire connector or board. -
Q: What is the difference between male and female PCB pins?
A: Male PCB pins, also known as header pins, have exposed metal pins that protrude from the board and are designed to mate with corresponding female sockets or connectors. Female PCB pins, on the other hand, have receptacles or holes that accept the male pins. The choice between male and female pins depends on the specific application and the mating requirements. -
Q: How do I ensure proper alignment when mating PCB pins with connectors?
A: To ensure proper alignment, use headers and connectors with keying features or polarization. These features, such as notches, asymmetric shapes, or missing pins, prevent incorrect mating and ensure that the pins are aligned correctly. Additionally, use alignment tools or fixtures during assembly to maintain the correct position and orientation of the pins.
Conclusion
PCB pins are versatile components that play a crucial role in connecting and interfacing various parts of electronic systems. By understanding the different types of PCB pins, their applications, and best practices for using them, you can create robust and reliable connections in your projects.
When selecting PCB pins, consider factors such as pin pitch, length, current rating, plating material, and mechanical strength to ensure they meet your specific requirements. Proper soldering techniques and regular maintenance are essential for achieving optimal performance and longevity of your pin connections.
By following the guidelines and best practices outlined in this article, you can effectively use PCB pins to bring your electronic designs to life and ensure the success of your projects.
Pin Type | Description | Applications |
---|---|---|
Through-hole | Long legs that pass through holes in the PCB and are soldered on the opposite side | High-stress applications, strong mechanical connection |
Surface Mount | Designed to be soldered directly onto the surface of the PCB without requiring holes | High-density designs, compact size |
Press-fit | Pressed into plated-through holes on the PCB, creating a secure connection | High-volume production, soldering-free applications |
Spring-loaded | Contains a spring-loaded mechanism that allows compression and maintains contact | Test fixtures, programming jigs, battery connectors |
Remember, the world of PCB pins is vast and constantly evolving. As you gain more experience working with these components, you’ll develop a deeper understanding of their capabilities and how to leverage them effectively in your projects. Stay curious, experiment, and don’t hesitate to seek guidance from experienced professionals or resources when needed.
Happy pinning!
Leave a Reply