What is PCB Panelization?
PCB panelization is the process of grouping multiple printed Circuit Board Designs onto a single panel for manufacturing. This technique is used to maximize the efficiency and cost-effectiveness of PCB production by allowing multiple boards to be fabricated and assembled simultaneously.
Benefits of PCB Panelization
- Cost reduction: By producing multiple boards on a single panel, the overall manufacturing cost per board is reduced.
- Increased efficiency: Panelization streamlines the fabrication and assembly processes, reducing the time required to produce a large number of PCBs.
- Improved handling: Panelized PCBs are easier to handle during the manufacturing process, as they can be processed as a single unit rather than individual boards.
Types of PCB Panelization
There are two main types of PCB panelization:
- Tab routing: This method involves connecting individual PCBs with small tabs, which are later removed after the manufacturing process is complete.
- V-scoring: In this technique, shallow grooves are cut between the individual PCBs, allowing them to be easily separated after fabrication and assembly.
Panelization Method | Advantages | Disadvantages |
---|---|---|
Tab Routing | – Strong panel connections – Suitable for large panels |
– Additional process to remove tabs – Potential for damage during tab removal |
V-Scoring | – Easy separation of boards – No additional tab removal process |
– Less sturdy panel connections – Limited to smaller panel sizes |
Designing for PCB Panelization
When designing PCBs for panelization, there are several factors to consider to ensure optimal results:
1. Board Spacing
Adequate spacing between individual boards on the panel is crucial to prevent damage during the fabrication and assembly processes. The minimum spacing required depends on the specific manufacturing capabilities of the PCB fabricator.
2. Panelization Method
Choose the appropriate panelization method (tab routing or v-scoring) based on your project’s requirements, such as panel size, board complexity, and the intended use of the final product.
3. Fiducial Markers
Include fiducial markers on the panel to assist with alignment during the manufacturing process. These markers help ensure accurate placement of components and improve the overall quality of the assembLED PCBs.
4. Panel Size
Consider the dimensions of the panel when designing your PCBs. The panel size should be compatible with the manufacturing equipment used by the PCB fabricator to avoid any issues during production.
PCB Panelization at Screaming Circuits
At Screaming Circuits, we offer professional PCB panelization services to help our customers optimize their PCB designs for manufacturing. Our experienced team works closely with clients to determine the best panelization strategy for their specific projects.
Why Choose Screaming Circuits for PCB Panelization?
- Expertise: Our team has extensive knowledge and experience in PCB panelization, ensuring that your project is completed efficiently and to the highest quality standards.
- State-of-the-art equipment: We invest in the latest manufacturing technology to provide our customers with the best possible results.
- Customized solutions: We work with you to develop a panelization strategy tailored to your specific project requirements and goals.
- Quick turnaround times: Our streamlined processes and dedicated team enable us to deliver high-quality panelized PCBs within short lead times.
The Screaming Circuits Panelization Process
- Design review: Our team reviews your PCB design files to ensure they are optimized for panelization and manufacturing.
- Panelization strategy development: We collaborate with you to determine the best panelization method and panel layout for your project.
- Panel fabrication: Your PCBs are fabricated on panels using state-of-the-art equipment and strict quality control measures.
- Assembly and testing: The panelized PCBs are assembled and tested to ensure they meet your specifications and performance requirements.
- Shipping and delivery: The completed PCBs are packaged and shipped to you, ready for integration into your final product.
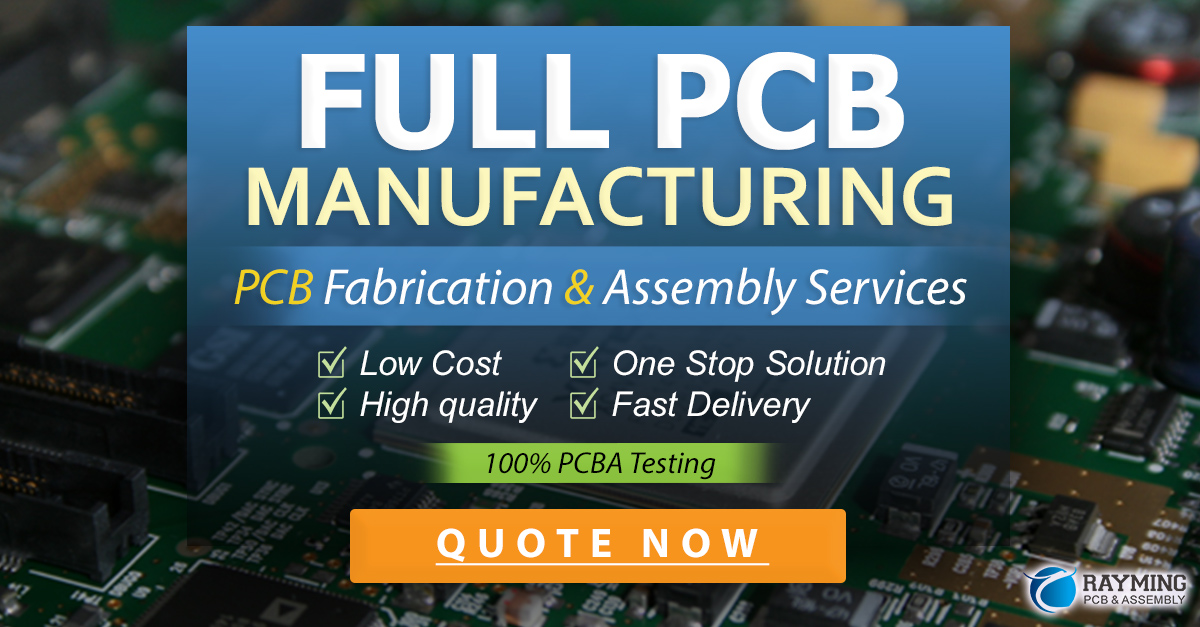
Frequently Asked Questions (FAQ)
1. What is the minimum spacing required between boards on a panel?
The minimum spacing between boards on a panel varies depending on the specific manufacturing capabilities of the PCB fabricator. At Screaming Circuits, we recommend a minimum spacing of 2mm to ensure optimal results and prevent damage during the fabrication and assembly processes.
2. Can I use different panelization methods for the same project?
Yes, it is possible to use different panelization methods within the same project, depending on your specific requirements. For example, you may choose to use tab routing for larger boards and v-scoring for smaller boards on the same panel. Our team at Screaming Circuits can help you determine the best combination of panelization methods for your project.
3. How does PCB panelization affect the cost of my project?
PCB panelization can help reduce the overall cost of your project by allowing multiple boards to be fabricated and assembled simultaneously. However, the specific cost savings will depend on factors such as the size of your boards, the complexity of your design, and the total number of boards being produced. Our team at Screaming Circuits can provide you with a detailed cost analysis based on your project requirements.
4. What files do I need to provide for PCB panelization?
To begin the PCB panelization process, you will need to provide us with your PCB design files, typically in Gerber or ODB++ Format. Additionally, you should include any necessary assembly files, such as pick-and-place files and bill of materials (BOM). Our team will review your files and work with you to ensure all necessary information is provided before proceeding with panelization.
5. How long does the PCB panelization process take?
The time required for PCB panelization depends on various factors, such as the complexity of your design, the panelization method chosen, and the overall workload of our manufacturing facility. At Screaming Circuits, we strive to provide quick turnaround times without compromising on quality. Our team will provide you with an estimated lead time based on your specific project requirements.
Conclusion
PCB panelization is a crucial aspect of the PCB manufacturing process, offering numerous benefits such as cost reduction, increased efficiency, and improved handling. By designing your PCBs with panelization in mind and working with an experienced PCB fabricator like Screaming Circuits, you can ensure that your project is completed successfully and to the highest quality standards.
Our team at Screaming Circuits is dedicated to providing our customers with expert PCB panelization services and support throughout the entire manufacturing process. Contact us today to learn more about how we can help optimize your PCB designs for panelization and bring your projects to life.
Leave a Reply