Introduction to PCB Material Selection
Printed Circuit Boards (PCBs) are the backbone of modern electronics. They provide the foundation for interconnecting electronic components and enable the functioning of complex electronic devices. The selection of the right PCB materials is crucial for ensuring the reliability, performance, and longevity of the final product. With a wide range of materials available, each with its own unique properties and characteristics, choosing the most suitable PCB material for your specific application can be a daunting task.
In this comprehensive guide, we will explore the key factors to consider when selecting PCB materials, the different types of materials available, and their respective advantages and disadvantages. By the end of this article, you will have a solid understanding of how to make informed decisions when it comes to PCB material selection for your manufacturing project.
Factors to Consider When Selecting PCB Materials
When choosing the right PCB materials, several critical factors must be taken into account to ensure optimal performance and reliability. These factors include:
Electrical Properties
The electrical properties of PCB materials play a vital role in determining the performance of the final product. Key electrical properties to consider include:
-
Dielectric Constant (Dk): The dielectric constant measures the material’s ability to store electrical energy. A lower Dk value is desirable for high-frequency applications to minimize signal loss and distortion.
-
Dissipation Factor (Df): The dissipation factor, also known as loss tangent, represents the amount of energy dissipated as heat in the material. A lower Df value is preferred to minimize signal attenuation and maintain signal integrity.
-
Electrical Conductivity: The electrical conductivity of the PCB material determines its ability to conduct electricity. Copper is the most commonly used conductive material in PCBs due to its excellent conductivity and cost-effectiveness.
Thermal Properties
The thermal properties of PCB materials are essential for managing heat dissipation and ensuring the long-term reliability of the electronic components. Important thermal properties to consider include:
-
Glass Transition Temperature (Tg): The glass transition temperature is the point at which the material transitions from a rigid, glassy state to a more flexible, rubbery state. A higher Tg value indicates better thermal stability and resistance to deformation at elevated temperatures.
-
Thermal Conductivity: Thermal conductivity measures the material’s ability to transfer heat. A higher thermal conductivity allows for better heat dissipation, preventing excessive heat buildup that can lead to component failure.
-
Coefficient of Thermal Expansion (CTE): The CTE represents the material’s dimensional change in response to temperature variations. A lower CTE is desirable to minimize stress on components and solder joints caused by thermal expansion mismatches.
Mechanical Properties
The mechanical properties of PCB materials determine their ability to withstand physical stresses and maintain structural integrity. Key mechanical properties to consider include:
-
Flexural Strength: Flexural strength measures the material’s ability to resist bending and maintain its shape under stress. Higher flexural strength is essential for applications that require mechanical robustness.
-
Tensile Strength: Tensile strength represents the material’s resistance to pulling forces. A higher tensile strength ensures that the PCB can withstand the stresses encountered during assembly and operation.
-
Impact Resistance: Impact resistance measures the material’s ability to absorb sudden impacts without cracking or breaking. This property is particularly important for portable devices and applications subject to drop or shock.
Environmental Factors
PCBs are often exposed to various environmental conditions that can affect their performance and longevity. Important environmental factors to consider when selecting PCB materials include:
-
Operating Temperature Range: The operating temperature range specifies the minimum and maximum temperatures at which the PCB material can function reliably. It is crucial to choose a material that can withstand the expected temperature extremes in your application.
-
Humidity Resistance: Humidity can lead to moisture absorption, which can degrade the electrical and mechanical properties of the PCB material. Selecting a material with good humidity resistance is essential for applications exposed to high humidity environments.
-
Chemical Resistance: In some applications, PCBs may be exposed to chemicals such as solvents, oils, or cleaning agents. Choosing a material with adequate chemical resistance ensures that the PCB can withstand exposure to these substances without deterioration.
Cost and Availability
Cost and availability are practical considerations when selecting PCB materials. While some high-performance materials may offer superior properties, they may also come at a higher cost and have limited availability. It is essential to strike a balance between performance requirements and cost-effectiveness while ensuring that the chosen material is readily available to meet production demands.
Types of PCB Materials
There are several types of PCB materials available, each with its own unique properties and suitability for different applications. The most common types of PCB materials include:
FR-4
FR-4 (Flame Retardant 4) is the most widely used PCB material. It is a composite material made of woven fiberglass cloth impregnated with an epoxy resin. FR-4 offers a good balance of electrical, mechanical, and thermal properties, making it suitable for a wide range of applications. It is cost-effective and has excellent dimensional stability.
High Tg FR-4
High Tg FR-4 is a variant of the standard FR-4 material with a higher glass transition temperature. This enhanced thermal stability makes it suitable for applications that require higher operating temperatures or increased resistance to thermal stresses. High Tg FR-4 is commonly used in automotive, aerospace, and military applications.
Polyimide
Polyimide is a high-performance PCB material known for its excellent thermal stability, chemical resistance, and mechanical strength. It can withstand high temperatures, making it suitable for applications that operate in extreme environments. Polyimide is often used in aerospace, military, and high-reliability industrial applications.
PTFE (Teflon)
PTFE (Polytetrafluoroethylene), commonly known as Teflon, is a low-loss dielectric material with excellent electrical properties. It has a low dielectric constant and dissipation factor, making it ideal for high-frequency applications such as RF and microwave circuits. PTFE is also known for its chemical inertness and thermal stability.
Rogers Materials
Rogers Corporation offers a range of high-performance PCB materials specifically designed for demanding applications. These materials, such as RO4000 and RT/duroid series, offer excellent electrical properties, low loss, and controlled dielectric constant. They are commonly used in high-frequency, automotive radar, and aerospace applications.
Flexible PCB Materials
Flexible PCB materials, such as polyimide and PET (Polyethylene Terephthalate), are used in applications that require flexibility and conformity. These materials allow for the creation of flexible circuits that can bend, fold, or twist without damaging the conductive traces. Flexible PCBs are commonly used in wearable devices, medical equipment, and consumer electronics.
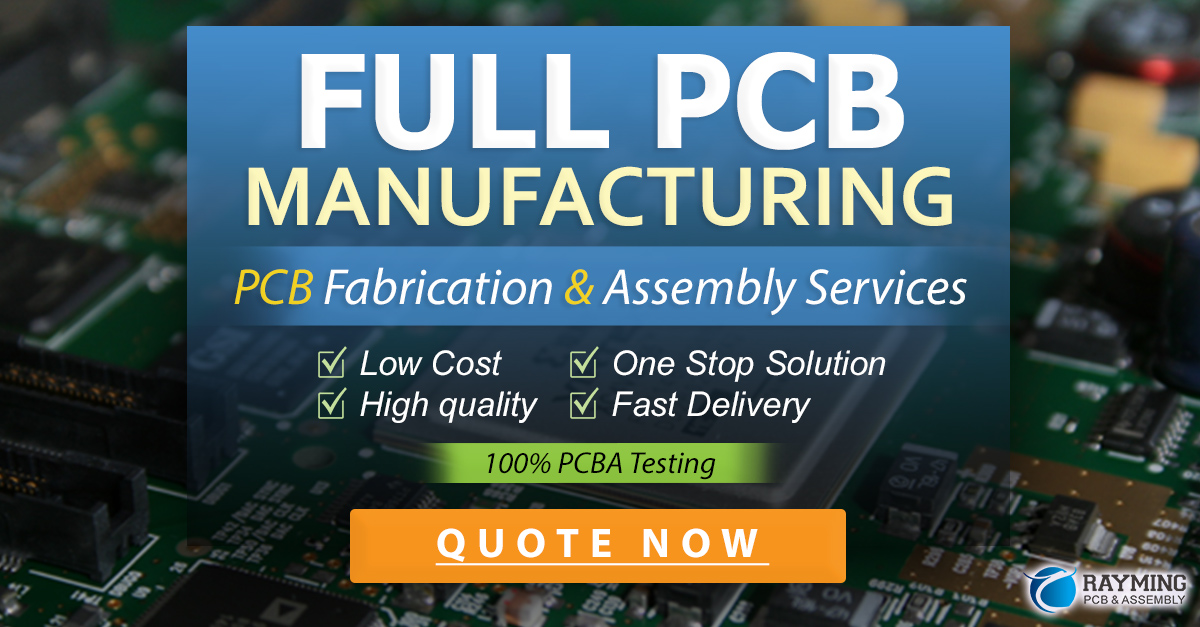
PCB Material Selection Considerations for Specific Applications
Different applications have specific requirements that influence the selection of PCB materials. Here are some common application areas and the key considerations for PCB material selection:
High-Frequency Applications
For high-frequency applications, such as RF and microwave circuits, the choice of PCB material is critical. Key considerations include:
- Low dielectric constant (Dk) to minimize signal loss and distortion
- Low dissipation factor (Df) to maintain signal integrity
- Controlled impedance to ensure proper signal propagation
- Thermal stability to maintain performance over temperature variations
Materials like PTFE, Rogers materials, and low-loss FR-4 variants are commonly used in high-frequency applications.
Automotive Electronics
Automotive electronics face demanding environmental conditions, such as extreme temperatures, vibrations, and exposure to chemicals. PCB material selection for automotive applications should consider:
- High glass transition temperature (Tg) for thermal stability
- Good mechanical strength and impact resistance
- Chemical resistance to automotive fluids and gases
- Compliance with automotive industry standards (e.g., AEC-Q100)
High Tg FR-4, polyimide, and specialized automotive-grade materials are often used in Automotive PCBs.
Medical Devices
PCB material selection for medical devices requires careful consideration of biocompatibility, reliability, and sterilization compatibility. Key factors to consider include:
- Biocompatibility to ensure patient safety
- Resistance to sterilization methods (e.g., autoclaving, gamma radiation)
- High reliability and long-term stability
- Compliance with medical device regulations and standards
Medical-grade FR-4, polyimide, and specialized biocompatible materials are commonly used in medical device PCBs.
Aerospace and Military Applications
Aerospace and military applications demand high-reliability PCBs that can withstand extreme environmental conditions. PCB material selection for these applications should consider:
- Wide operating temperature range
- Resistance to vibration and shock
- High mechanical strength and durability
- Compliance with aerospace and military standards (e.g., MIL-PRF-31032)
Materials like polyimide, high Tg FR-4, and specialized aerospace-grade materials are often used in aerospace and military PCBs.
PCB Material Selection Process
Selecting the right PCB material involves a systematic approach that takes into account the specific requirements of your application. Here is a step-by-step process for PCB material selection:
-
Define application requirements: Clearly identify the electrical, thermal, mechanical, and environmental requirements of your application.
-
Identify critical properties: Determine the key material properties that are critical for your application, such as dielectric constant, dissipation factor, glass transition temperature, and thermal conductivity.
-
Evaluate available materials: Research and compare the properties of different PCB materials that meet your application requirements.
-
Consider cost and availability: Assess the cost and availability of the potential materials to ensure they align with your budget and production needs.
-
Consult with PCB manufacturers: Engage with experienced PCB manufacturers to discuss your material selection and get their recommendations based on their expertise and manufacturing capabilities.
-
Perform testing and validation: Conduct necessary testing and validation to ensure that the selected material meets your application requirements and performs as expected.
-
Document and communicate: Document your material selection process and communicate the chosen material to all relevant stakeholders, including design teams, manufacturers, and suppliers.
Frequently Asked Questions (FAQ)
- What is the most commonly used PCB material?
-
FR-4 is the most widely used PCB material due to its good balance of electrical, mechanical, and thermal properties, as well as its cost-effectiveness.
-
How do I choose between FR-4 and high Tg FR-4?
-
The choice between FR-4 and high Tg FR-4 depends on your application’s temperature requirements. If your application operates at higher temperatures or requires increased thermal stability, high Tg FR-4 is the preferred choice.
-
What PCB materials are suitable for high-frequency applications?
-
For high-frequency applications, materials with low dielectric constant and low dissipation factor are preferred. PTFE, Rogers materials, and low-loss FR-4 variants are commonly used in high-frequency PCBs.
-
Are there specific PCB materials for medical devices?
-
Yes, medical devices require PCB materials that are biocompatible, reliable, and compatible with sterilization methods. Medical-grade FR-4, polyimide, and specialized biocompatible materials are often used in medical device PCBs.
-
How does the cost of PCB materials affect the overall project cost?
- The cost of PCB materials can have a significant impact on the overall project cost, especially for large-volume production. It is essential to consider the balance between material performance and cost-effectiveness when making material selections.
Conclusion
PCB material selection is a critical aspect of PCB manufacturing that directly impacts the performance, reliability, and cost of the final product. By understanding the key factors to consider, such as electrical, thermal, mechanical, and environmental properties, you can make informed decisions when selecting the most suitable PCB materials for your specific application.
This comprehensive guide has provided an overview of the different types of PCB materials available, their properties, and their suitability for various applications. It has also outlined the PCB material selection process and addressed common questions through the FAQ section.
When selecting PCB materials, it is crucial to engage with experienced PCB manufacturers who can provide valuable insights and recommendations based on their expertise. By following a systematic approach and considering all relevant factors, you can ensure that your PCB manufacturing project achieves optimal results in terms of performance, reliability, and cost-effectiveness.
PCB Material | Key Properties | Typical Applications |
---|---|---|
FR-4 | Good balance of electrical, mechanical, and thermal properties | General-purpose electronics, consumer devices |
High Tg FR-4 | Higher glass transition temperature, increased thermal stability | Automotive, aerospace, military |
Polyimide | Excellent thermal stability, chemical resistance, and mechanical strength | Aerospace, military, high-reliability industrial |
PTFE (Teflon) | Low dielectric constant, low dissipation factor, chemical inertness | High-frequency applications (RF, microwave) |
Rogers Materials | Excellent electrical properties, low loss, controlled dielectric constant | High-frequency, automotive radar, aerospace |
Flexible PCB Materials | Flexibility, conformity | Wearable devices, medical equipment, consumer electronics |
Remember, the right PCB material selection is essential for ensuring the success of your PCB manufacturing project. By carefully considering your application requirements and leveraging the expertise of PCB manufacturers, you can make informed decisions that lead to optimal performance, reliability, and cost-effectiveness.
Leave a Reply