What are HASL and ENIG?
When it comes to printed circuit board (PCB) manufacturing, the choice of surface finish plays a critical role in the performance, reliability, and longevity of the final product. Two of the most commonly used surface finish methods in the industry are Hot Air Solder Leveling (HASL) and Electroless Nickel Immersion Gold (ENIG).
Hot Air Solder Leveling (HASL)
HASL is a traditional surface finish method that involves dipping the PCB into a molten solder bath, typically consisting of a tin-lead alloy. The excess solder is then blown off using hot air knives, resulting in a flat, solderable surface. HASL has been widely used in the PCB industry for decades due to its cost-effectiveness and ease of application.
Electroless Nickel Immersion Gold (ENIG)
ENIG is a more modern surface finish method that has gained popularity in recent years. In this process, a thin layer of nickel is first deposited onto the copper pads of the PCB through an electroless plating process. Subsequently, a thin layer of gold is deposited on top of the nickel layer through an immersion process. The resulting surface is flat, solderable, and offers excellent corrosion resistance.
HASL vs ENIG Comparison
While both HASL and ENIG are viable options for PCB surface finishes, they have distinct differences that make them suitable for different applications. Here are ten key differences between HASL and ENIG:
1. Flatness
One of the most significant differences between HASL and ENIG is the flatness of the resulting surface.
Surface Finish | Flatness |
---|---|
HASL | Uneven surface due to the solder dipping process |
ENIG | Flat surface due to the thin layers of nickel and gold |
The HASL process can result in an uneven surface due to the nature of the solder dipping and hot air leveling process. This unevenness can lead to issues with component placement and solderability, especially for fine-pitch components.
In contrast, ENIG provides a flat surface because of the thin layers of nickel and gold deposited onto the copper pads. This flatness makes ENIG ideal for applications that require high-density component placement or have strict flatness requirements.
2. Solderability
Both HASL and ENIG offer good solderability, but there are some differences in their performance.
Surface Finish | Solderability |
---|---|
HASL | Good solderability, but can be affected by surface oxidation over time |
ENIG | Excellent solderability due to the presence of the gold layer |
HASL provides good solderability immediately after the surface finish process. However, the exposed solder surface can oxidize over time, leading to a decrease in solderability. This oxidation can be mitigated by proper storage and handling of the PCBs.
ENIG, on the other hand, offers excellent solderability due to the presence of the gold layer. Gold is a noble metal that does not oxidize easily, ensuring that the surface remains solderable for an extended period. This makes ENIG a preferred choice for applications that require long shelf life or exposure to harsh environments.
3. Shelf Life
The shelf life of a PCB refers to the period during which it can be stored without significant degradation in its properties.
Surface Finish | Shelf Life |
---|---|
HASL | Limited shelf life due to the risk of surface oxidation |
ENIG | Extended shelf life due to the protection provided by the gold layer |
As mentioned earlier, the exposed solder surface in HASL can oxidize over time, leading to a decrease in solderability. This oxidation can occur even during storage, limiting the shelf life of HASL-finished PCBs.
ENIG, with its gold layer, provides an excellent barrier against oxidation. This protection extends the shelf life of ENIG-finished PCBs, making them suitable for applications that require long-term storage or have unpredictable production schedules.
4. Cost
Cost is often a critical factor in choosing a surface finish method.
Surface Finish | Cost |
---|---|
HASL | Lower cost compared to ENIG |
ENIG | Higher cost due to the use of gold and additional processing steps |
HASL is generally less expensive than ENIG because it uses a simple solder dipping process and does not require the use of precious metals like gold. The raw materials used in HASL, such as tin and lead, are also less costly than nickel and gold.
ENIG, on the other hand, involves the use of gold, which is a more expensive material. Additionally, the ENIG process requires more processing steps, including the electroless nickel plating and immersion gold deposition, which contribute to the higher cost.
5. Environmental Impact
The environmental impact of a surface finish method is an increasingly important consideration in PCB manufacturing.
Surface Finish | Environmental Impact |
---|---|
HASL | Use of lead in the solder alloy raises environmental concerns |
ENIG | Lead-free and compliant with RoHS regulations |
Traditionally, HASL has used a tin-lead solder alloy, which contains lead, a harmful substance that poses environmental and health risks. The use of lead in electronic products is now regulated by various directives, such as the Restriction of Hazardous Substances (RoHS) in the European Union.
ENIG is a lead-free surface finish method that complies with RoHS regulations. The use of nickel and gold in the ENIG process does not pose the same environmental concerns as lead.
6. Thermal Shock Resistance
Thermal shock resistance refers to a PCB’s ability to withstand sudden changes in temperature.
Surface Finish | Thermal Shock Resistance |
---|---|
HASL | Limited thermal shock resistance due to the thick solder layer |
ENIG | Better thermal shock resistance due to the thin layers of nickel and gold |
The thick solder layer in HASL can be susceptible to cracking under thermal stress, especially during rapid temperature changes. This vulnerability can lead to reduced thermal shock resistance in HASL-finished PCBs.
ENIG, with its thin layers of nickel and gold, offers better thermal shock resistance. The nickel layer acts as a barrier, absorbing stress and preventing cracks from propagating to the underlying copper.
7. Fine-Pitch Compatibility
Fine-pitch components are electronic components with closely spaced leads, requiring a high degree of precision in PCB manufacturing.
Surface Finish | Fine-Pitch Compatibility |
---|---|
HASL | Limited compatibility due to uneven surface and solder bridging |
ENIG | Excellent compatibility due to flat surface and precise gold thickness |
The uneven surface resulting from the HASL process can pose challenges when working with fine-pitch components. The variations in solder thickness can lead to solder bridging between closely spaced leads, causing short circuits and other issues.
ENIG, with its flat surface and precisely controlled gold thickness, is well-suited for fine-pitch applications. The flat surface ensures proper component placement, while the thin gold layer prevents solder bridging.
8. Aluminum Wire Bonding
Aluminum wire bonding is a process used in the packaging of certain electronic components, such as integrated circuits.
Surface Finish | Aluminum Wire Bonding |
---|---|
HASL | Not suitable for aluminum wire bonding |
ENIG | Suitable for aluminum wire bonding due to the presence of the gold layer |
HASL is not suitable for aluminum wire bonding because the solder surface does not provide a compatible bonding interface for the aluminum wire.
ENIG, with its gold layer, offers a suitable surface for aluminum wire bonding. The gold layer provides excellent adhesion and electrical conductivity, making it compatible with the aluminum wire bonding process.
9. Solder Joint Strength
Solder joint strength is a measure of the mechanical integrity of the solder connection between a component and the PCB.
Surface Finish | Solder Joint Strength |
---|---|
HASL | Good solder joint strength due to the thick solder layer |
ENIG | Adequate solder joint strength, but may be slightly lower than HASL |
The thick solder layer in HASL can provide good solder joint strength, as the solder forms a strong mechanical bond with the component leads and the PCB pads.
ENIG, with its thin gold layer, can also provide adequate solder joint strength. However, the strength may be slightly lower compared to HASL due to the thinner solder layer formed during the assembly process.
10. Rework and Repair
Rework and repair refer to the processes of removing and replacing components on a PCB.
Surface Finish | Rework and Repair |
---|---|
HASL | Easier rework and repair due to the thicker solder layer |
ENIG | More challenging rework and repair due to the thin gold layer |
The thick solder layer in HASL can make rework and repair processes easier. The excess solder can be easily removed, and new solder can be applied when replacing components.
ENIG, with its thin gold layer, can make rework and repair more challenging. The gold layer must be completely removed before new solder can be applied, requiring additional steps and precautions to avoid damaging the PCB.
FAQ
1. Which surface finish method is better, HASL or ENIG?
There is no definitive answer to this question, as the choice between HASL and ENIG depends on the specific requirements of the application. Factors such as cost, environmental impact, fine-pitch compatibility, and shelf life should be considered when making a decision.
2. Can HASL be used for lead-free applications?
Yes, lead-free HASL options are available, using solder alloys that do not contain lead. However, lead-free HASL may have different performance characteristics compared to traditional leaded HASL.
3. Is ENIG always more expensive than HASL?
In general, ENIG is more expensive than HASL due to the use of gold and additional processing steps. However, the cost difference may vary depending on the specific PCB manufacturer and the volume of production.
4. Can ENIG be used for high-temperature applications?
Yes, ENIG is suitable for high-temperature applications due to its good thermal shock resistance and the stability of the nickel and gold layers.
5. Is it possible to switch from HASL to ENIG in an existing PCB design?
Switching from HASL to ENIG in an existing PCB design is possible, but it may require some modifications to the PCB layout and the manufacturing process. It is important to consult with the PCB manufacturer to ensure a smooth transition and to verify compatibility with the existing design.
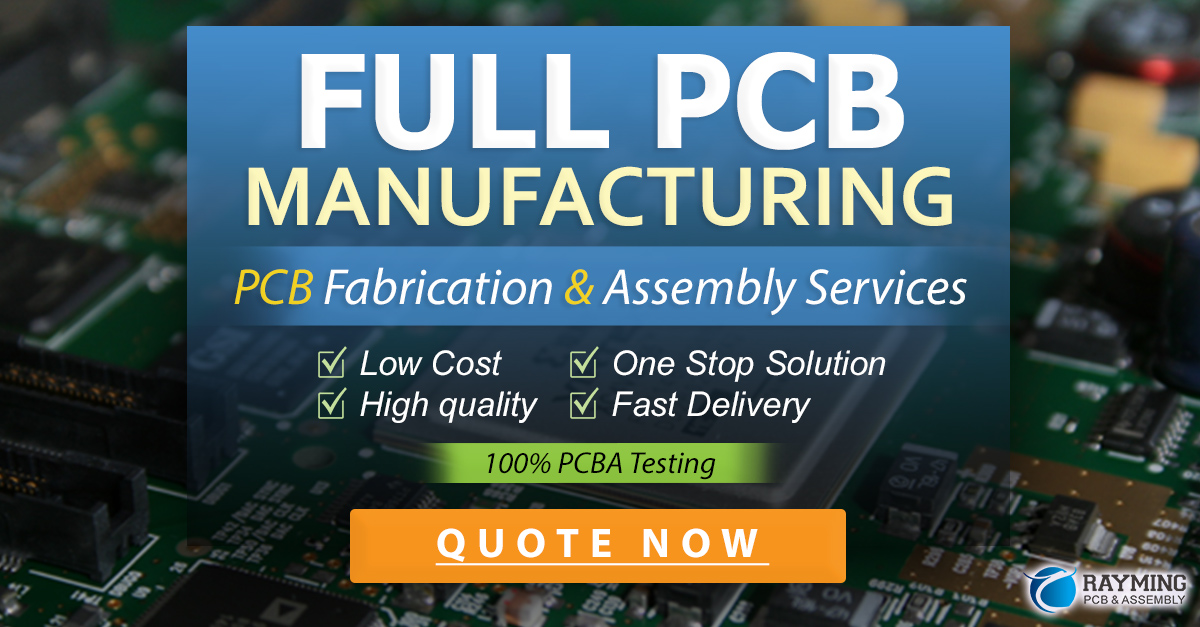
Conclusion
HASL and ENIG are two popular surface finish methods used in PCB manufacturing, each with its own advantages and disadvantages. The choice between HASL and ENIG depends on various factors, including cost, environmental impact, flatness, solderability, shelf life, thermal shock resistance, fine-pitch compatibility, aluminum wire bonding, solder joint strength, and rework and repair considerations.
Understanding the differences between HASL and ENIG is crucial for selecting the most suitable surface finish method for a given application. By carefully evaluating the specific requirements and priorities of a project, PCB designers and manufacturers can make an informed decision that balances performance, reliability, and cost-effectiveness.
As the electronics industry continues to evolve, with increasing demands for miniaturization, high-density packaging, and environmental sustainability, the choice between HASL and ENIG, or the adoption of newer surface finish technologies, will remain an important consideration in PCB manufacturing.
Leave a Reply