Types of PCB drilling defects
There are several types of drilling defects that can occur during the PCB Manufacturing process. These include:
Misaligned Holes
Misaligned holes occur when the drill bit does not enter the PCB Substrate at the correct location. This can be caused by a variety of factors, including:
- Incorrect drill file data
- Machine calibration issues
- Substrate material movement during drilling
Oversized or Undersized Holes
Oversized or undersized holes occur when the drill bit creates a hole that is either too large or too small for the intended component or via. This can be caused by:
- Worn or damaged drill bits
- Incorrect drill bit selection
- Improper machine settings
Burrs and Breakouts
Burrs and breakouts occur when the drill bit creates rough edges or protrusions around the hole. This can be caused by:
- Dull or worn drill bits
- Improper drilling speeds and feeds
- Inadequate cleaning of the drill bit during the drilling process
Smeared or Stretched Copper
Smeared or stretched copper occurs when the copper layer on the PCB substrate is deformed or stretched during the drilling process. This can be caused by:
- Excessive drilling pressure
- Improper drill bit geometry
- Inadequate cleaning of the drill bit during the drilling process
Causes of PCB Drilling Defects
There are several factors that can contribute to the occurrence of PCB drilling defects. These include:
Incorrect Drill File Data
The drill file contains the information necessary for the drilling machine to create the holes in the correct locations and sizes. If the drill file data is incorrect, it can lead to misaligned or oversized/undersized holes.
Machine Calibration Issues
If the drilling machine is not properly calibrated, it can lead to inaccuracies in the placement and size of the holes. Regular maintenance and calibration of the drilling machine are essential to prevent these issues.
Substrate Material Movement
If the PCB substrate is not securely held in place during the drilling process, it can shift or move, resulting in misaligned holes. Proper fixturing and clamping of the substrate are necessary to prevent this issue.
Worn or Damaged Drill Bits
As drill bits are used, they can become worn or damaged, leading to oversized or undersized holes, as well as burrs and breakouts. Regular inspection and replacement of drill bits are necessary to maintain the quality of the drilling process.
Improper Drilling Speeds and Feeds
The speed at which the drill bit rotates and the rate at which it moves through the substrate can have a significant impact on the quality of the holes. Improper drilling speeds and feeds can lead to burrs, breakouts, and smeared or stretched copper.
Inadequate Cleaning of the Drill Bit
During the drilling process, debris can accumulate on the drill bit, leading to poor hole quality. Adequate cleaning of the drill bit during the drilling process is necessary to prevent this issue.
Elimination Methods for PCB Drilling Defects
To eliminATE PCB drilling defects, several methods can be employed:
Proper Drill File Creation and Verification
Ensuring that the drill file data is accurate and complete is essential to preventing drilling defects. The drill file should be carefully created and verified before being used in the drilling process.
Regular Machine Maintenance and Calibration
Regular maintenance and calibration of the drilling machine are necessary to ensure that it is operating correctly and producing high-quality holes. This includes cleaning and lubricating the machine, as well as verifying its accuracy and repeatability.
Secure Substrate Fixturing
Properly securing the PCB substrate during the drilling process is essential to preventing misaligned holes. Fixtures and clamps should be used to hold the substrate in place and prevent movement.
Drill Bit Selection and Inspection
Selecting the appropriate drill bit for the specific application and regularly inspecting it for wear and damage are necessary to maintain hole quality. Worn or damaged drill bits should be replaced promptly.
Optimized Drilling Parameters
The drilling speeds and feeds should be optimized for the specifIC Substrate material and hole size to minimize burrs, breakouts, and smeared or stretched copper. This may require experimentation and adjustment to find the ideal settings.
Adequate Cleaning and Lubrication
Adequate cleaning and lubrication of the drill bit during the drilling process are essential to preventing the accumulation of debris and maintaining hole quality. Compressed air and specialized cleaning fluids can be used for this purpose.
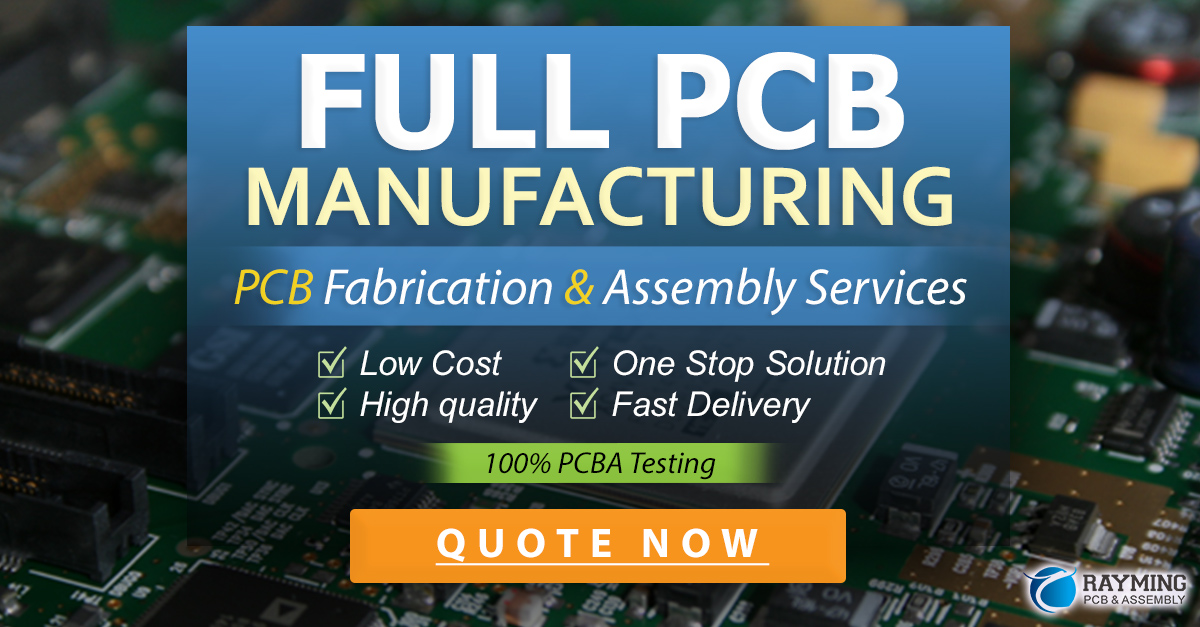
FAQ
- What is the most common cause of misaligned holes in PCBs?
-
Incorrect drill file data and machine calibration issues are the most common causes of misaligned holes in PCBs.
-
How can oversized or undersized holes be prevented?
-
Oversized or undersized holes can be prevented by selecting the appropriate drill bit, regularly inspecting and replacing worn or damaged drill bits, and ensuring proper machine settings.
-
What causes burrs and breakouts around drilled holes?
-
Burrs and breakouts around drilled holes are caused by dull or worn drill bits, improper drilling speeds and feeds, and inadequate cleaning of the drill bit during the drilling process.
-
How can smeared or stretched copper be avoided during PCB drilling?
-
Smeared or stretched copper can be avoided by optimizing drilling pressure, selecting drill bits with appropriate geometry, and ensuring adequate cleaning of the drill bit during the drilling process.
-
What steps can be taken to ensure high-quality PCB drilling?
- To ensure high-quality PCB drilling, proper drill file creation and verification, regular machine maintenance and calibration, secure substrate fixturing, appropriate drill bit selection and inspection, optimized drilling parameters, and adequate cleaning and lubrication should be implemented.
Defect Type | Causes | Elimination Methods |
---|---|---|
Misaligned Holes | Incorrect drill file data, machine calibration issues, substrate movement | Proper drill file creation and verification, regular machine maintenance and calibration, secure substrate fixturing |
Oversized/Undersized Holes | Worn or damaged drill bits, incorrect drill bit selection, improper machine settings | Drill bit selection and inspection, optimized drilling parameters |
Burrs and Breakouts | Dull or worn drill bits, improper drilling speeds and feeds, inadequate cleaning | Drill bit selection and inspection, optimized drilling parameters, adequate cleaning and lubrication |
Smeared or Stretched Copper | Excessive drilling pressure, improper drill bit geometry, inadequate cleaning | Optimized drilling parameters, drill bit selection and inspection, adequate cleaning and lubrication |
In conclusion, PCB drilling defects can have a significant impact on the functionality and reliability of printed circuit boards. By understanding the causes of these defects and implementing appropriate elimination methods, manufacturers can ensure the production of high-quality PCBs. Regular maintenance, calibration, and inspection of drilling equipment, as well as the use of optimized drilling parameters and adequate cleaning and lubrication, are essential to minimizing the occurrence of drilling defects and maintaining the integrity of the PCB manufacturing process.
Leave a Reply