What are PCB CNC Machines?
PCB CNC machines are computer-controlled systems designed specifically for the manufacturing of printed circuit boards. These machines use a combination of advanced software, high-precision motors, and cutting-edge tools to automate various processes involved in PCB Production, such as drilling, routing, and milling.
The main components of a PCB CNC machine include:
- Computer Numerical Control (CNC) System: The brain of the machine, responsible for interpreting design files and controlling the movement of the machine’s tools.
- Spindle: A high-speed rotating device that holds the cutting tools used for drilling and routing.
- Worktable: A flat surface where the PCB material is securely held in place during the manufacturing process.
- Axes: The X, Y, and Z axes along which the spindle and worktable move to execute the desired operations.
Advantages of Using PCB CNC Machines
PCB CNC machines offer numerous advantages over traditional PCB manufacturing methods, such as manual drilling and etching. Some of the key benefits include:
1. Increased Accuracy and Precision
CNC machines are capable of producing PCBs with extremely high levels of accuracy and precision. They can consistently drill holes and route traces with tolerances as low as ±0.001 inches (0.0254 mm), ensuring that the final product meets the exact specifications required for optimal performance.
2. Faster Production Times
By automating the PCB manufacturing process, CNC machines can significantly reduce production times compared to manual methods. These machines can work continuously, 24/7, without the need for breaks or rest periods, allowing manufacturers to meet tight deadlines and increase overall output.
3. Improved Consistency and Repeatability
CNC machines follow precise, pre-programmed instructions, ensuring that each PCB produced is identical to the next. This consistency and repeatability are essential for maintaining high quality standards and reducing the likelihood of defects or errors in the final product.
4. Enhanced Design Flexibility
PCB CNC machines can handle a wide range of PCB designs, from simple single-layer boards to complex multi-layer structures. They can easily accommodate changes in design files, allowing manufacturers to quickly adapt to evolving customer requirements and market demands.
5. Cost Efficiency
While the initial investment in a PCB CNC machine may be higher than traditional manufacturing methods, the long-term cost savings can be substantial. By reducing labor costs, minimizing material waste, and increasing production speed, CNC machines can help manufacturers optimize their operations and improve their bottom line.
Types of PCB CNC Machines
There are several types of PCB CNC machines available, each designed to cater to specific manufacturing requirements and production scales. Some of the most common types include:
1. Drilling Machines
PCB Drilling machines are used to create the holes required for component placement and inter-layer connections. These machines can be further classified into two sub-categories:
a. Mechanical Drilling Machines: These machines use high-speed spindles and drill bits to physically create holes in the PCB material. They are suitable for producing larger holes and can handle a wide range of PCB Thicknesses.
b. Laser Drilling Machines: Laser drilling machines use high-powered lasers to vaporize the PCB material, creating precise, micro-sized holes. They are ideal for producing smaller, more intricate holes and can achieve higher drilling speeds compared to mechanical drilling machines.
2. Routing Machines
PCB routing machines are used to cut out the individual PCBs from larger panels and create the desired board shape. They use high-speed spindles and cutting tools to remove excess material, leaving behind the finished PCB. Routing machines can also be used to create slots, cutouts, and other features required for component placement and assembly.
3. Milling Machines
PCB Milling machines are used to remove the top layer of copper from a PCB, creating the desired circuit pattern. These machines use small, high-speed cutting tools called end mills to selectively remove the unwanted copper, leaving behind the desired traces and pads. Milling machines are particularly useful for prototyping and small-batch production, as they allow for quick and easy design changes without the need for expensive tooling.
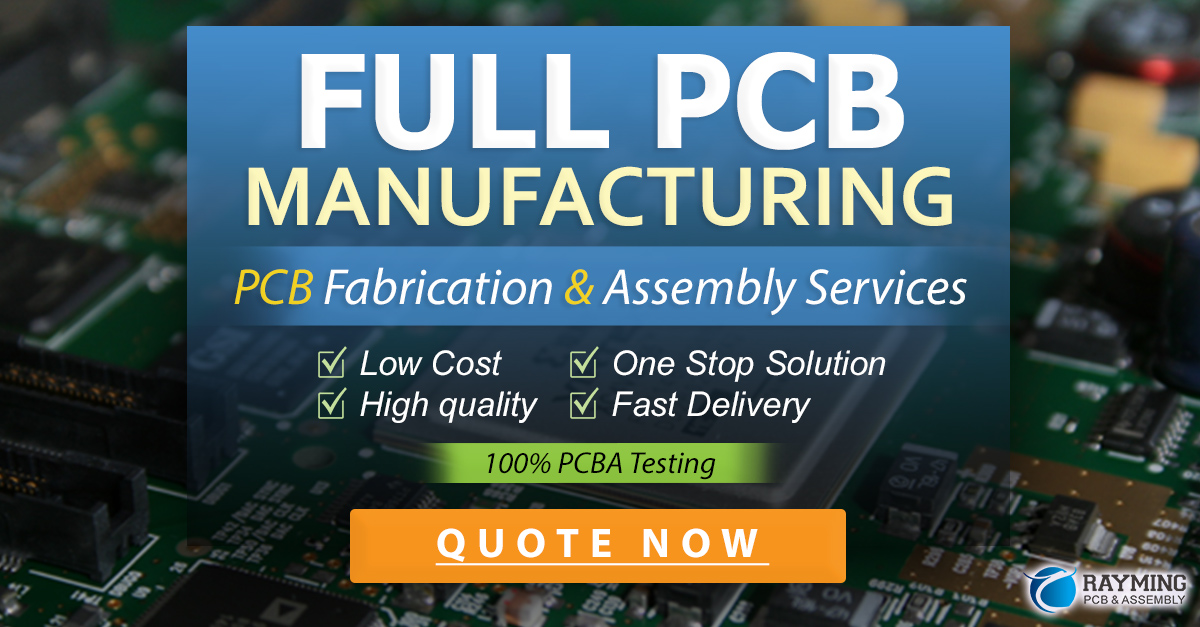
The PCB CNC Manufacturing Process
The PCB CNC manufacturing process typically involves the following steps:
-
Design: The PCB design is created using specialized software, such as Altium Designer or Eagle. The design file includes information about the board’s dimensions, component placement, and circuit layout.
-
File Preparation: The design file is converted into a format compatible with the CNC machine, such as Gerber or DXF. This file contains the necessary instructions for the machine to execute the required operations.
-
Material Preparation: The PCB material, typically a copper-clad laminate, is cut to the appropriate size and secured on the machine’s worktable.
-
Drilling: The CNC machine drills the required holes in the PCB material based on the design file. This process can be performed using either mechanical or laser drilling machines.
-
Routing: The CNC machine routes the individual PCBs from the larger panel, creating the desired board shape and any necessary cutouts or slots.
-
Milling (optional): If required, the CNC milling machine removes the top layer of copper from the PCB, creating the desired circuit pattern.
-
Inspection: The finished PCBs are inspected for quality and accuracy, ensuring that they meet the required specifications.
-
Lamination and Finishing: The PCBs undergo additional processes, such as lamination, solder mask application, and surface finish, to protect the circuits and prepare them for component assembly.
Choosing the Right PCB CNC Machine
When selecting a PCB CNC machine for your manufacturing needs, there are several factors to consider:
-
Production Volume: Consider the expected production volume and choose a machine that can efficiently handle your requirements. For high-volume production, faster, more automated machines may be necessary.
-
PCB Complexity: Evaluate the complexity of the PCBs you intend to produce. More complex designs may require machines with higher precision and more advanced features.
-
Material Compatibility: Ensure that the machine is compatible with the PCB materials you plan to use, such as FR-4, aluminum, or flexible substrates.
-
Software Integration: Choose a machine that is compatible with your existing design software and file formats to streamline the manufacturing process.
-
Budget: Consider your budget and the long-term cost-effectiveness of the machine. While higher-end machines may have a higher upfront cost, they can offer significant savings in the long run through increased efficiency and reduced waste.
PCB CNC Machines and Industry 4.0
As the electronics industry continues to evolve, PCB CNC machines are becoming increasingly integrated with Industry 4.0 technologies, such as the Internet of Things (IoT), artificial intelligence (AI), and machine learning. These advancements enable manufacturers to create smarter, more connected production environments, offering benefits such as:
-
Real-time Monitoring: IoT-enabLED PCB CNC machines can provide real-time data on machine performance, production status, and potential issues, allowing for proactive maintenance and optimization.
-
Predictive Maintenance: By analyzing data from connected machines, AI algorithms can predict potential equipment failures and schedule maintenance tasks accordingly, minimizing downtime and increasing overall equipment effectiveness (OEE).
-
Autonomous Operation: Advanced PCB CNC machines can be programmed to operate autonomously, adjusting their parameters based on real-time feedback and learned behavior, further enhancing efficiency and reducing the need for human intervention.
-
Cloud-based Collaboration: Cloud-connected PCB CNC machines enable seamless collaboration between design teams, manufacturers, and suppliers, allowing for faster design iterations and more agile production processes.
As Industry 4.0 technologies continue to mature, we can expect to see even more advanced PCB CNC machines that offer greater automation, flexibility, and intelligence, driving the future of electronics manufacturing.
Frequently Asked Questions (FAQ)
1. What is the difference between a PCB CNC machine and a traditional PCB manufacturing method?
PCB CNC machines are computer-controlled systems that automate the PCB manufacturing process, offering higher accuracy, faster production times, and improved consistency compared to traditional manual methods, such as hand drilling and etching.
2. Can PCB CNC machines handle complex PCB designs?
Yes, PCB CNC machines are capable of handling a wide range of PCB designs, from simple single-layer boards to complex multi-layer structures. They can easily accommodate changes in design files, allowing manufacturers to quickly adapt to evolving customer requirements.
3. What are the main types of PCB CNC machines?
The main types of PCB CNC machines include drilling machines (mechanical and laser), routing machines, and milling machines. Each type is designed to cater to specific manufacturing requirements and production scales.
4. How do PCB CNC machines contribute to cost efficiency in electronics manufacturing?
While the initial investment in a PCB CNC machine may be higher than traditional manufacturing methods, they can offer significant long-term cost savings by reducing labor costs, minimizing material waste, and increasing production speed, helping manufacturers optimize their operations and improve their bottom line.
5. What factors should be considered when choosing a PCB CNC machine?
When selecting a PCB CNC machine, factors to consider include the expected production volume, PCB complexity, material compatibility, software integration, and budget. It is essential to choose a machine that can efficiently handle your specific manufacturing requirements while offering long-term cost-effectiveness.
Conclusion
PCB CNC machines have revolutionized the electronics manufacturing industry, offering high-tech solutions for the production of printed circuit boards. These advanced machines provide increased accuracy, faster production times, improved consistency, and enhanced design flexibility, enabling manufacturers to meet the growing demands of the market.
As the electronics industry continues to evolve, PCB CNC machines are becoming increasingly integrated with Industry 4.0 technologies, such as IoT, AI, and machine learning. These advancements are driving the creation of smarter, more connected production environments, paving the way for even greater efficiency, automation, and intelligence in PCB manufacturing.
By understanding the capabilities, advantages, and applications of PCB CNC machines, electronics manufacturers can make informed decisions when selecting the right equipment for their production needs. Embracing these high-tech solutions can help manufacturers stay competitive in an ever-evolving industry, delivering high-quality PCBs that power the devices and technologies shaping our world.
Feature | Traditional PCB Manufacturing | PCB CNC Machines |
---|---|---|
Accuracy | Lower, manual processes | High, computer-controlled |
Production Speed | Slower, labor-intensive | Faster, automated |
Consistency | Variable, prone to human error | High, repeatable results |
Design Flexibility | Limited, requires tooling changes | High, easily accommodates changes |
Cost Efficiency | Lower upfront costs, higher long-term costs | Higher upfront costs, lower long-term costs |
PCB CNC Machine Type | Application |
---|---|
Drilling Machines | Creating holes for component placement and inter-layer connections |
Routing Machines | Cutting out individual PCBs and creating board shapes |
Milling Machines | Removing top layer of copper to create circuit patterns |
Leave a Reply