What is PCB Cross-Section Analysis?
PCB cross-section analysis is a crucial technique used in the quality control and failure analysis of printed circuit boards (PCBs). It involves cutting a small section of the PCB and examining it under a microscope to assess the internal structure, layer alignment, and potential manufacturing defects. This process provides valuable insights into the quality and reliability of the PCB, enabling manufacturers to identify and address issues before they lead to product failures.
Why is PCB Cross-Section Analysis Important?
PCB cross-section analysis is essential for several reasons:
- Quality assurance: By examining the internal structure of the PCB, manufacturers can ensure that the board meets the required specifications and standards.
- Failure analysis: In case of a PCB failure, cross-section analysis helps identify the root cause of the problem, such as manufacturing defects, material issues, or design flaws.
- Process improvement: The insights gained from cross-section analysis can be used to optimize the PCB manufacturing process, leading to improved quality and reliability.
The PCB Cross-Section Analysis Process
Step 1: Sample Preparation
The first step in PCB cross-section analysis is to prepare a sample of the board for examination. This involves:
- Cutting a small section of the PCB using a precision saw or Laser Cutter.
- Encapsulating the sample in a resin to protect it during the grinding and polishing process.
- Grinding and polishing the sample to expose the internal layers and structures.
Step 2: Microscopic Examination
Once the sample is prepared, it is examined under a microscope. Various types of microscopes can be used, depending on the level of detail required:
- Optical microscopes: These provide a magnification of up to 1000x and are suitable for examining the general structure and layer alignment of the PCB.
- Scanning electron microscopes (SEM): SEMs offer higher magnification (up to 100,000x) and better resolution, allowing for detailed examination of fine features and defects.
During the microscopic examination, the following aspects are assessed:
- Layer alignment and registration
- Copper thickness and uniformity
- Solder mask and solder paste coverage
- Drill hole quality and plating
- Void formation and delamination
- Contamination and foreign materials
Step 3: Data Analysis and Reporting
The data collected during the microscopic examination is analyzed to identify any issues or defects in the PCB. This information is then compiled into a detailed report, which includes:
- Images of the cross-sectioned sample
- Measurements of key features and dimensions
- Description of any defects or anomalies found
- Recommendations for process improvement or corrective actions
Defect Type | Possible Causes | Potential Impact |
---|---|---|
Layer misalignment | Incorrect artwork, manufacturing process issues | Signal integrity issues, short circuits |
Copper thickness variation | Plating process inconsistencies, Etching Issues | Increased resistance, reliability issues |
Void formation | Inadequate lamination, moisture trapped in layers | Delamination, signal integrity issues |
Drill hole defects | Dull drill bits, improper drilling parameters | Poor plating, open circuits |
Benefits of PCB Cross-Section Analysis
Implementing PCB cross-section analysis in the manufacturing process offers several benefits:
- Improved quality: By identifying and addressing issues early in the manufacturing process, cross-section analysis helps ensure that the final product meets the required quality standards.
- Reduced failure rates: Identifying and correcting defects before the PCBs are assembled into final products reduces the likelihood of field failures and product returns.
- Cost savings: Detecting issues early in the manufacturing process is more cost-effective than dealing with product failures and recalls later on.
- Faster time-to-market: By optimizing the manufacturing process based on the insights gained from cross-section analysis, manufacturers can reduce lead times and bring products to market faster.
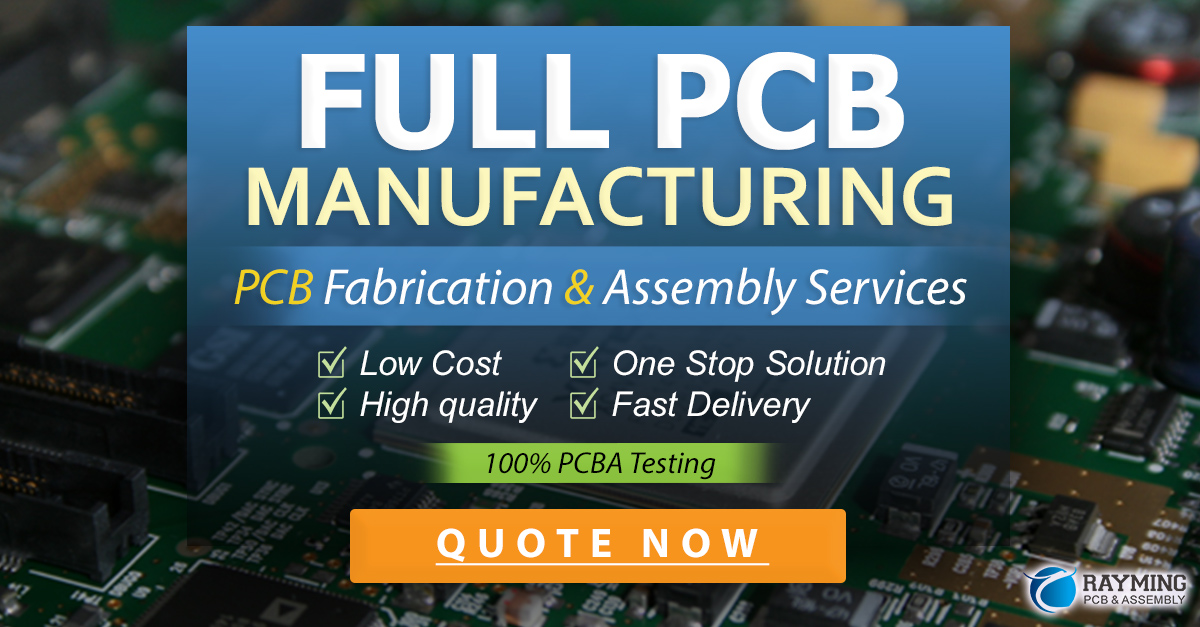
Advanced Techniques in PCB Cross-Section Analysis
As PCB technology continues to evolve, so do the techniques used in cross-section analysis. Some of the advanced techniques include:
3D X-ray Computed Tomography (CT)
3D X-ray CT is a non-destructive technique that allows for the visualization and analysis of the internal structure of a PCB without the need for physical sectioning. This technology uses X-rays to create a series of 2D images, which are then reconstructed into a 3D model of the PCB. This enables manufacturers to identify defects and analyze the board’s internal structure without damaging the sample.
Focused Ion Beam (FIB) Milling
FIB milling is a precise technique used for preparing cross-section samples of specific areas of interest on a PCB. It uses a focused beam of ions to mill away material, creating a clean and accurate cross-section. This technique is particularly useful for examining fine features, such as small vias or trace defects, that may be difficult to access using traditional sample preparation methods.
Atomic Force Microscopy (AFM)
AFM is a high-resolution imaging technique that uses a probe to scan the surface of a sample, providing detailed topographical information at the nanoscale level. In PCB cross-section analysis, AFM can be used to examine the surface roughness, uniformity, and defects of individual layers, as well as to measure the thickness of thin films and coatings.
FAQ
1. How long does the PCB cross-section analysis process typically take?
The duration of the PCB cross-section analysis process depends on the complexity of the board and the number of samples being analyzed. A simple analysis can be completed within a few hours, while more complex boards or multiple samples may take several days.
2. Can PCB cross-section analysis be performed on any type of PCB?
Yes, cross-section analysis can be performed on any type of PCB, including rigid, flexible, and rigid-flex boards. However, the specific techniques and equipment used may vary depending on the board’s material and construction.
3. Is PCB cross-section analysis a destructive testing method?
Yes, PCB cross-section analysis is a destructive testing method, as it requires cutting a small section of the board for examination. However, the insights gained from the analysis often outweigh the cost of the sacrificed sample.
4. Can PCB cross-section analysis detect all types of defects?
While PCB cross-section analysis is a powerful tool for identifying a wide range of defects, it may not detect every issue. Some defects, such as intermittent or timing-related issues, may require additional testing methods, such as functional testing or signal integrity analysis.
5. How often should PCB cross-section analysis be performed?
The frequency of PCB cross-section analysis depends on various factors, such as the complexity of the board, the critical nature of the application, and the manufacturing process maturity. Some manufacturers perform cross-section analysis on a regular basis as part of their quality control process, while others may only do so when issues arise or when introducing new products or processes.
Conclusion
PCB cross-section analysis is a vital technology for ensuring the quality, reliability, and performance of printed circuit boards. By providing detailed insights into the internal structure and potential defects of a PCB, cross-section analysis enables manufacturers to identify and address issues early in the manufacturing process, leading to improved product quality, reduced failure rates, and cost savings.
As PCB technology continues to advance, so do the techniques and tools used in cross-section analysis. From traditional optical microscopy to advanced methods like 3D X-ray CT, FIB milling, and AFM, manufacturers have access to a wide range of options for examining and optimizing their PCBs.
By incorporating PCB cross-section analysis into their quality control and failure analysis processes, manufacturers can stay ahead of the curve in today’s competitive electronics industry, delivering high-quality, reliable products to their customers.
Leave a Reply