Understanding PCB Copy
PCB copy, or printed circuit board copy, is the process of duplicating an existing PCB design. This technique is often used when a company needs to reproduce a legacy PCB for which the original design files are unavailable or when reverse engineering is required to create a functional replica of an existing board.
What is a PCB?
A printed circuit board (PCB) is a fundamental component of modern electronic devices. It is a flat board made of insulating materials, such as fiberglass or plastic, with conductive copper traces printed on its surface. These traces connect various electronic components, such as resistors, capacitors, and integrated circuits (ICs), to form a complete electronic circuit.
PCBs offer several advantages over traditional point-to-point wiring:
- Compact design
- Improved reliability
- Easier mass production
- Reduced electronic noise
Types of PCBs
There are several types of PCBs, each with its own unique characteristics and applications:
-
Single-layer PCBs: These boards have conductive traces on only one side and are typically used in simple, low-cost electronic devices.
-
Double-layer PCBs: With conductive traces on both sides, these boards offer more complex routing options and are used in a wide range of electronic devices.
-
Multi-layer PCBs: These boards have multiple layers of conductive traces separated by insulating layers. They are used in high-density, complex electronic systems that require a large number of interconnections.
-
Flexible PCBs: Made from flexible materials, these boards can bend and conform to various shapes, making them ideal for applications where space is limited or where the board needs to fit into a specific form factor.
The PCB Copy Process
The PCB copy process involves several steps to accurately replicate an existing PCB design. The main stages of the process are:
- PCB digitization
- PCB layout and design
- PCB fabrication
- PCB Assembly and testing
PCB Digitization
The first step in the PCB copy process is to digitize the original PCB. This involves using specialized equipment to capture the physical characteristics of the board, such as the dimensions, component placement, and trace routing.
There are two main methods for PCB digitization:
-
Manual digitization: This method involves manually measuring and recording the physical characteristics of the PCB using tools such as calipers, rulers, and microscopes. While this method is time-consuming and labor-intensive, it can be useful for simple PCBs or when automated methods are not available.
-
Automated digitization: This method uses specialized scanning equipment, such as 3D scanners or X-ray machines, to capture the physical characteristics of the PCB. The scanned data is then processed using software to create a digital model of the board. Automated digitization is faster and more accurate than manual methods, making it the preferred choice for complex PCBs.
PCB Layout and Design
Once the PCB has been digitized, the next step is to create a new PCB layout and design based on the captured data. This involves using PCB design software, such as Altium Designer or KiCad, to recreate the original PCB’s schematic and layout.
During this stage, engineers may make improvements to the original design, such as:
- Updating components to newer, more readily available alternatives
- Optimizing trace routing to improve signal integrity and reduce electromagnetic interference (EMI)
- Adding or removing features to meet new requirements or specifications
PCB Fabrication
After the PCB layout and design are complete, the next step is to fabricate the new PCB. This involves several sub-processes, including:
-
PCB printing: The PCB design is printed onto a copper-clad laminate using a photoresist process. The exposed areas of the photoresist are then developed and etched away, leaving the desired copper traces on the board.
-
Drilling: Holes are drilled into the PCB to accommodate through-hole components and to create vias that connect traces on different layers of the board.
-
Plating: The drilled holes are plated with copper to ensure electrical connectivity between layers.
-
Solder mask application: A protective solder mask is applied to the PCB to prevent accidental short circuits and to protect the copper traces from oxidation and damage.
-
Silkscreen printing: Text and symbols are printed onto the PCB using a silkscreen process to aid in component placement and identification.
PCB Assembly and Testing
The final stage of the PCB copy process is assembling the components onto the newly fabricated PCB and testing the completed board to ensure proper functionality.
PCB assembly can be done manually or using automated assembly lines, depending on the complexity of the board and the volume of production.
Testing typically involves a combination of visual inspection, automated optical inspection (AOI), and functional testing to verify that the copied PCB performs identically to the original.
Benefits of PCB Copy
PCB copy offers several benefits, particularly for companies dealing with legacy systems or in situations where the original PCB design files are unavailable.
-
Cost savings: Reproducing an existing PCB design can be more cost-effective than designing a new board from scratch, especially for low-volume production runs.
-
Time savings: By copying an existing design, companies can save time that would otherwise be spent on research, development, and prototyping.
-
Improved availability: PCB copy enables companies to replace obsolete or hard-to-find components with newer, more readily available alternatives, ensuring the long-term availability of the PCB.
-
Enhanced reliability: During the PCB copy process, engineers can identify and correct any design flaws or weaknesses in the original PCB, resulting in a more reliable and robust final product.
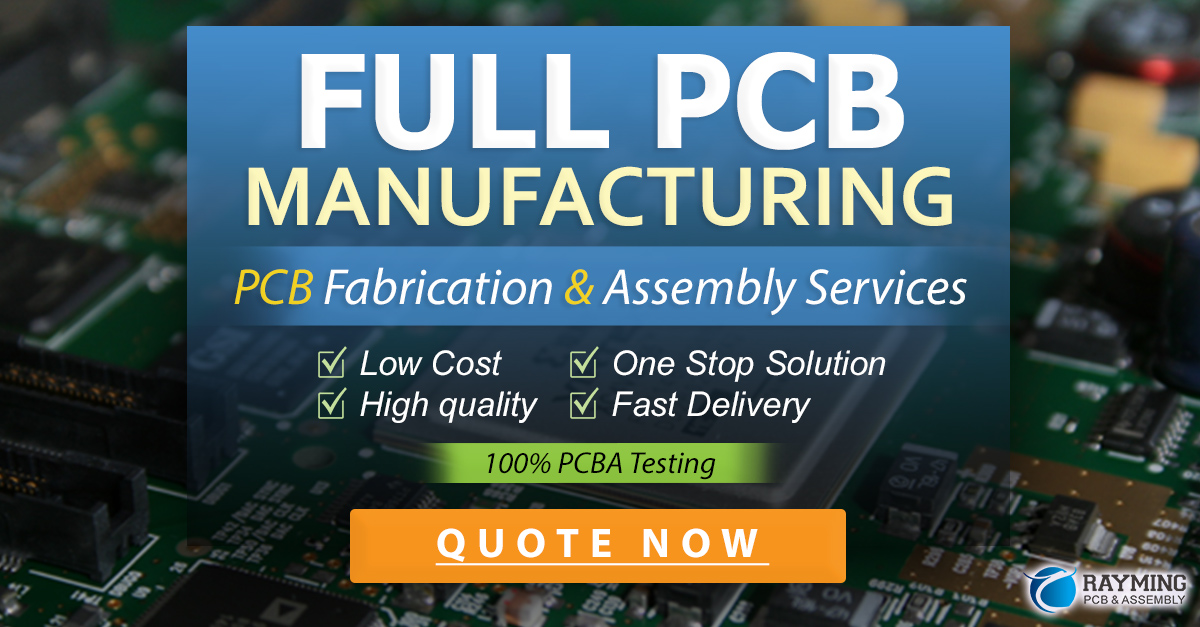
Challenges in PCB Copy
While PCB copy offers many benefits, there are also several challenges that companies may face during the process.
-
Design complexity: Copying complex, multi-layer PCBs can be challenging, as it requires accurate digitization and recreation of the original design.
-
Component obsolescence: Some components used in the original PCB may no longer be available, requiring engineers to find suitable replacements or redesign certain portions of the circuit.
-
Intellectual property concerns: In some cases, copying a PCB design may infringe upon the intellectual property rights of the original designer or manufacturer. Companies must ensure that they have the necessary legal rights or permissions before attempting to copy a PCB.
-
Quality control: Ensuring that the copied PCB performs identically to the original requires rigorous quality control measures and thorough testing.
PCB Copy vs. PCB Reverse Engineering
PCB copy and PCB reverse engineering are related but distinct processes. While PCB copy focuses on duplicating an existing PCB design as closely as possible, PCB reverse engineering involves analyzing an existing PCB to understand its functionality and design principles, often with the goal of improving upon the original design or creating a new, compatible design.
PCB reverse engineering typically involves the following steps:
-
Deconstruction: The original PCB is carefully disassembled to expose its internal components and layering.
-
Analysis: Engineers study the PCB’s components, trace routing, and overall design to understand its functionality and identify any potential improvements.
-
Documentation: The findings from the analysis stage are documented, often in the form of schematics, diagrams, and design files.
-
Redesign: Based on the analysis and documentation, engineers may create a new PCB design that incorporates improvements or modifications to the original design.
While PCB reverse engineering can be a valuable tool for understanding and improving existing designs, it is generally more complex and time-consuming than PCB copy.
Applications of PCB Copy
PCB copy is used in a wide range of industries and applications, including:
-
Aerospace and defense: Many aerospace and defense systems rely on legacy PCBs that are no longer in production. PCB copy enables these industries to maintain and repair their equipment without the need for costly redesigns.
-
Medical devices: Medical equipment often has strict regulatory requirements and long product life cycles, making PCB copy an attractive option for ensuring the long-term availability of critical components.
-
Industrial automation: Industrial control systems and machinery often use PCBs that are specific to a particular application. PCB copy allows companies to replace damaged or worn-out boards without the need for extensive redesigns.
-
Automotive industry: As vehicles become increasingly reliant on electronic systems, PCB copy can help automotive manufacturers maintain and repair older vehicles that use legacy PCBs.
-
Consumer electronics: In some cases, PCB copy can be used to create replacement parts for discontinued consumer electronic devices, such as vintage audio equipment or gaming consoles.
Future of PCB Copy
As technology continues to advance, the PCB copy process is likely to become more efficient and accurate. Some of the trends and developments that may shape the future of PCB copy include:
-
Advanced digitization techniques: Improvements in 3D scanning and X-ray technology may enable faster and more accurate digitization of complex PCBs.
-
Artificial intelligence and machine learning: AI and machine learning algorithms could be used to automate certain aspects of the PCB copy process, such as component identification and trace routing optimization.
-
Additive manufacturing: 3D printing technology may be used to create PCB Prototypes or even final products, enabling faster iteration and customization of copied PCBs.
-
Cloud-based collaboration: Cloud-based PCB design platforms could allow teams to collaborate remotely on PCB copy projects, streamlining the design and review process.
As these technologies mature, PCB copy is likely to become an even more valuable tool for companies looking to maintain and improve their electronic systems.
Conclusion
PCB copy is a powerful technique for duplicating existing PCB designs, offering benefits such as cost savings, improved availability, and enhanced reliability. By understanding the PCB copy process and its applications, companies can make informed decisions about when and how to use this valuable tool.
However, it is essential to consider the challenges and limitations of PCB copy, such as design complexity, component obsolescence, and intellectual property concerns. By carefully weighing these factors and working with experienced PCB copy professionals, companies can successfully navigate the PCB copy process and achieve their goals.
As technology continues to evolve, the future of PCB copy looks bright, with advanced digitization techniques, artificial intelligence, additive manufacturing, and cloud-based collaboration poised to revolutionize the process. By staying informed about these developments, companies can position themselves to take full advantage of the benefits of PCB copy in the years to come.
Frequently Asked Questions (FAQ)
-
What is the difference between PCB copy and PCB reverse engineering?
PCB copy focuses on duplicating an existing PCB design as closely as possible, while PCB reverse engineering involves analyzing an existing PCB to understand its functionality and design principles, often with the goal of improving upon the original design or creating a new, compatible design. -
How long does the PCB copy process typically take?
The duration of the PCB copy process can vary depending on the complexity of the PCB, the availability of components, and the workload of the PCB copy service provider. Simple PCBs may be copied in a matter of days, while more complex boards can take several weeks or even months. -
Is PCB copy legal?
The legality of PCB copy depends on the specific circumstances and intellectual property rights involved. In some cases, copying a PCB design may infringe upon the intellectual property rights of the original designer or manufacturer. Companies must ensure that they have the necessary legal rights or permissions before attempting to copy a PCB. -
Can PCB copy be used to replace obsolete components?
Yes, during the PCB copy process, engineers can identify obsolete components and replace them with newer, more readily available alternatives. This can help ensure the long-term availability and maintainability of the copied PCB. -
How much does PCB copy cost?
The cost of PCB copy can vary widely depending on factors such as the complexity of the PCB, the quantity required, and the specific services needed (e.g., digitization, design, fabrication, and assembly). In general, PCB copy is more cost-effective than designing a new board from scratch, especially for low-volume production runs. However, it is essential to request quotes from multiple PCB copy service providers to ensure competitive pricing and to find the best option for your specific needs.
Leave a Reply