What is an LED PCB?
An LED PCB, or Light Emitting Diode Printed Circuit Board, is a specialized type of circuit board designed to support and control LEDs. These boards are essential components in various applications, from simple indicator lights to complex lighting systems used in automotive, architectural, and industrial settings.
LED PCBs are designed to provide the necessary electrical connections, heat dissipation, and mechanical support for LEDs. They are typically made from a base material, such as FR-4, with conductive copper traces that connect the LEDs to power sources and control circuits.
Key Components of an LED PCB
- Substrate: The base material, usually FR-4, which provides mechanical support and electrical insulation.
- Copper Traces: Conductive pathways that carry electrical signals and power to the LEDs.
- Solder Mask: A protective layer that covers the copper traces, preventing short circuits and oxidation.
- Silkscreen: Text and symbols printed on the PCB for identification and assembly guidance.
- LEDs: The light-emitting components mounted on the PCB.
Advantages of Using LED PCBs
Energy Efficiency
One of the primary benefits of using LED PCBs is their energy efficiency. LEDs consume significantly less power compared to traditional lighting solutions, such as incandescent or fluorescent bulbs. This low power consumption translates to reduced energy costs and a smaller environmental footprint.
Long Lifespan
LEDs mounted on PCBs have a significantly longer lifespan compared to other lighting technologies. With proper thermal management and electrical design, LED PCBs can last for tens of thousands of hours, reducing maintenance costs and downtime.
Versatility
LED PCBs can be customized to suit a wide range of applications. They can be designed in various shapes, sizes, and configurations to fit specific requirements. Additionally, LEDs are available in a broad spectrum of colors, allowing for creative lighting designs and effects.
Durability
LED PCBs are solid-state devices, meaning they have no moving parts or fragile components. This inherent durability makes them resistant to vibration, shock, and extreme temperatures, making them suitable for use in harsh environments.
Designing LED PCBs
Thermal Management
One of the key challenges in designing LED PCBs is ensuring proper thermal management. LEDs generate heat during operation, and excessive heat can lead to decreased performance, color shifts, and premature failure. To mitigate these issues, LED PCBs must be designed with efficient heat dissipation in mind.
Some common thermal management techniques include:
- Using high-thermal-conductivity substrates: Materials like aluminum or Copper-Clad Laminates can help dissipate heat more effectively than standard FR-4.
- Incorporating thermal vias: These are conductive pathways that transfer heat from the LED to the opposite side of the PCB, where it can be dissipated by a heatsink or other cooling solution.
- Designing adequate copper pour: Increasing the amount of copper on the PCB can help spread heat more evenly and improve overall thermal performance.
Electrical Considerations
Proper electrical design is critical for ensuring the optimal performance and longevity of LED PCBs. Some key factors to consider include:
- Current and Voltage Requirements: LEDs have specific current and voltage requirements that must be met to ensure proper operation. Current-limiting resistors or constant-current drivers are often used to regulate the current flowing through the LEDs.
- Power Supply Selection: Choosing the appropriate power supply is essential for providing the necessary voltage and current to the LEDs. Factors such as efficiency, ripple, and transient response should be considered when selecting a power supply.
- Circuit Protection: Incorporating protection features, such as reverse polarity protection, overvoltage protection, and electrostatic discharge (ESD) protection, can help safeguard the LEDs and associated circuitry from damage.
Layout Considerations
The layout of an LED PCB plays a significant role in its performance and reliability. Some important layout considerations include:
- Minimizing Trace Length: Keeping the copper traces between the power source and the LEDs as short as possible can help reduce voltage drop and improve overall efficiency.
- Avoiding Electromagnetic Interference (EMI): Proper trace routing and the use of ground planes can help minimize EMI, which can cause flickering or other unwanted effects in LED lighting systems.
- Accommodating Mechanical Constraints: The PCB layout must consider the mechanical requirements of the application, such as mounting holes, connectors, and clearances for other components.
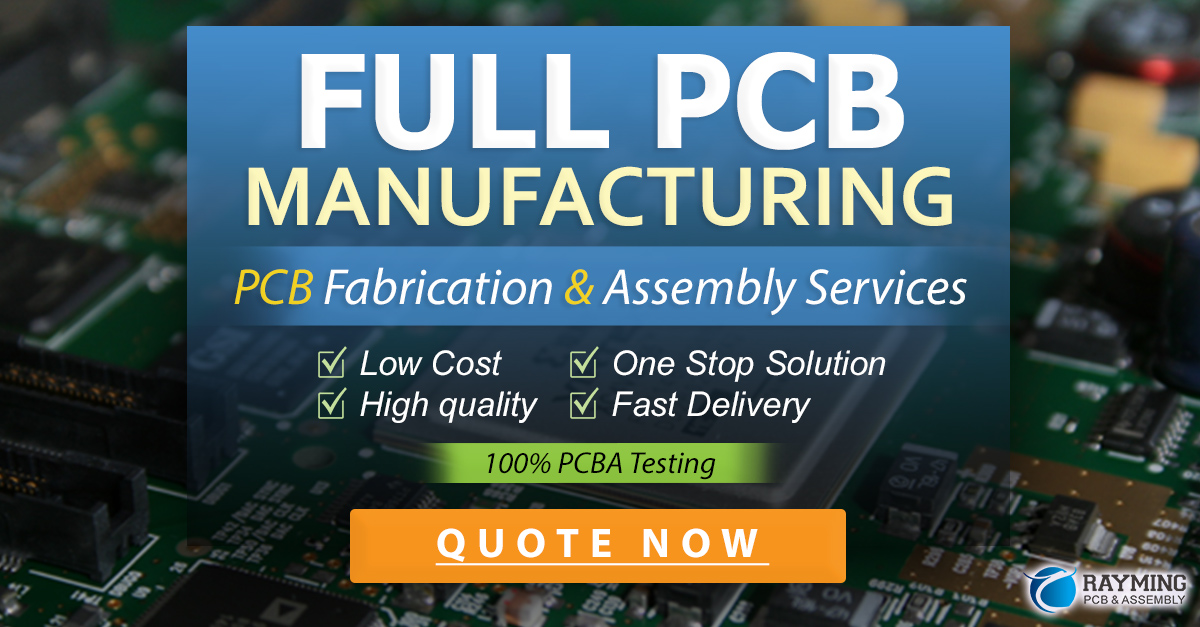
Manufacturing LED PCBs
PCB Fabrication
Once the LED PCB design is finalized, the next step is to manufacture the physical board. The fabrication process typically involves the following steps:
- Printing the Circuit Pattern: The PCB design files are used to create a photomask, which is then used to transfer the circuit pattern onto the copper-clad substrate.
- Etching: The unwanted copper is removed using a chemical etching process, leaving only the desired traces and pads.
- Applying Solder Mask and Silkscreen: A protective solder mask is applied to the PCB, and the silkscreen layer is printed for component identification and assembly guidance.
- Drilling and Cutting: Holes are drilled for through-hole components and vias, and the PCB is cut to its final shape and size.
LED Assembly
After the PCB is fabricated, the LEDs and other components are assembled onto the board. This process can be done manually for small-scale productions or using automated assembly lines for larger volumes.
Common LED assembly methods include:
- Through-Hole Assembly: LEDs with long leads are inserted through holes in the PCB and soldered in place.
- Surface Mount Assembly: Surface-mount LEDs are placed on pads on the PCB and soldered using reflow or wave soldering techniques.
- Chip-on-Board (COB) Assembly: Bare LED chips are directly bonded to the PCB substrate and then encapsulated for protection.
Applications of LED PCBs
LED PCBs find applications in a wide range of industries and products, including:
- Automotive Lighting: LED PCBs are used in headlights, taillights, interior lighting, and instrument panels in modern vehicles.
- Architectural Lighting: LED PCBs are used in various architectural lighting applications, such as wall sconces, downlights, and cove lighting.
- Signage and Displays: LED PCBs are used in digital signage, billboards, and information displays.
- Industrial and Machine Vision: LED PCBs provide illumination for machine vision systems, inspection equipment, and other industrial applications.
- Consumer Electronics: LED PCBs are found in a wide range of consumer products, from smartphones and laptops to home appliances and gaming devices.
Future Trends in LED PCB Technology
As LED technology continues to evolve, so too will LED PCBs. Some emerging trends in LED PCB technology include:
- Flexible and Stretchable PCBs: The development of flexible and stretchable substrates will enable new applications for LED lighting in wearable devices, automotive interiors, and architectural installations.
- Increased Integration: The integration of control circuitry, sensors, and communication interfaces directly onto LED PCBs will lead to more compact, intelligent, and connected lighting systems.
- Improved Thermal Management: Advancements in materials science and manufacturing techniques will enable more efficient thermal management solutions, such as embedded heat pipes and advanced substrates.
- Sustainable Manufacturing: There will be a growing emphasis on eco-friendly materials and manufacturing processes, such as the use of biodegradable substrates and low-impact fabrication methods.
Frequently Asked Questions (FAQ)
1. What is the difference between an LED and an LED PCB?
An LED, or Light Emitting Diode, is a semiconductor device that emits light when an electric current passes through it. An LED PCB, on the other hand, is a printed circuit board designed to support and control one or more LEDs. The PCB provides the necessary electrical connections, heat dissipation, and mechanical support for the LEDs to function properly.
2. Can LED PCBs be used in outdoor applications?
Yes, LED PCBs can be designed for outdoor use. However, special considerations must be made to ensure the PCB and its components are protected from environmental factors such as moisture, temperature extremes, and UV exposure. This may involve using weatherproof enclosures, conformal coatings, or specialized PCB materials.
3. How do I choose the right LED PCB for my application?
Choosing the right LED PCB depends on several factors, including the specific requirements of your application, such as the desired light output, color, and power consumption. Other considerations include the operating environment, budget, and any space or weight constraints. It’s essential to work with an experienced LED PCB manufacturer or designer to ensure the best solution for your needs.
4. What is the lifespan of an LED PCB?
The lifespan of an LED PCB depends on several factors, including the quality of the LEDs, the PCB design, and the operating environment. With proper thermal management and electrical design, LED PCBs can last for tens of thousands of hours, often surpassing the lifespan of traditional lighting solutions. However, it’s essential to follow the manufacturer’s guidelines for operation and maintenance to ensure optimal performance and longevity.
5. Are LED PCBs more expensive than traditional lighting solutions?
While LED PCBs may have a higher initial cost compared to traditional lighting solutions, they often provide a lower total cost of ownership due to their energy efficiency, long lifespan, and reduced maintenance requirements. Additionally, the price of LED technology has been steadily decreasing over the years, making LED PCBs an increasingly cost-effective solution for a wide range of applications.
Conclusion
LED PCBs have revolutionized the lighting industry, offering energy-efficient, versatile, and durable solutions for a wide range of applications. By understanding the key components, design considerations, and manufacturing processes involved in creating LED PCBs, engineers and designers can develop innovative lighting solutions that meet the ever-evolving needs of various industries.
As technology continues to advance, the future of LED PCBs looks bright, with new materials, manufacturing techniques, and integration possibilities on the horizon. By staying informed about these developments and working with experienced LED PCB Manufacturers and designers, businesses can harness the power of LED PCBs to create efficient, reliable, and sustainable lighting solutions for years to come.
Leave a Reply