Understanding Leaded and Lead-Free Solder
What is Leaded Solder?
Leaded solder is an alloy that traditionally consists of 63% tin (Sn) and 37% lead (Pb), known as Sn63/Pb37. This composition has been widely used in the electronics industry for decades due to its excellent wetting properties, low melting point, and reliable performance.
What is Lead-Free Solder?
Lead-free solder is an alloy that does not contain lead, typically consisting of tin (Sn), silver (Ag), and copper (Cu). The most common lead-free solder composition is Sn96.5/Ag3.0/Cu0.5, also known as SAC305. Lead-free solders were developed in response to environmental and health concerns associated with lead.
The Environmental and Health Impact
The Dangers of Lead
Lead is a toxic heavy metal that can cause serious health problems, including damage to the nervous system, kidneys, and reproductive system. When electronic devices containing leaded solder are improperly disposed of, lead can leach into the environment, contaminating soil and water sources.
Regulations Driving the Adoption of Lead-Free Solder
In response to the environmental and health risks posed by lead, many countries have implemented regulations restricting the use of leaded solder in electronics manufacturing. The most notable of these regulations include:
- The European Union’s Restriction of Hazardous Substances (RoHS) Directive
- China’s Administrative Measure on the Control of Pollution Caused by Electronic Information Products
- Japan’s J-MOSS (Japanese Industrial Standard for Marking of Specific Chemical Substances)
These regulations have driven the widespread adoption of lead-free solder in the electronics industry.
Comparing the Performance of Leaded and Lead-Free Solder
Reliability
Leaded solder has a proven track record of reliability in electronics manufacturing. Its lower melting point and superior wetting properties contribute to the formation of strong, reliable solder joints. In contrast, lead-free solders have higher melting points and can be more susceptible to common defects such as tin whiskers, which can cause short circuits and other reliability issues.
Solder Type | Melting Point | Wetting Properties | Reliability Concerns |
---|---|---|---|
Leaded (Sn63/Pb37) | 183°C | Excellent | None |
Lead-Free (SAC305) | 217°C | Good | Tin whiskers, higher stress |
Thermal Cycling Performance
Electronic devices often experience thermal cycling during operation, which can cause stress on solder joints. Leaded solder has a lower elastic modulus and higher ductility compared to lead-free solder, allowing it to better absorb stress during thermal cycling. This can result in improved long-term reliability for leaded solder joints.
Solder Type | Elastic Modulus | Ductility | Thermal Cycling Performance |
---|---|---|---|
Leaded (Sn63/Pb37) | Lower | Higher | Better stress absorption |
Lead-Free (SAC305) | Higher | Lower | More susceptible to stress |
Manufacturability
Lead-free solders have higher melting points than leaded solders, requiring higher processing temperatures during PCB assembly. This can lead to increased thermal stress on components and PCBs, potential damage to heat-sensitive components, and reduced energy efficiency in the manufacturing process.
Solder Type | Processing Temperature | Impact on Components and PCBs |
---|---|---|
Leaded (Sn63/Pb37) | Lower | Minimal thermal stress |
Lead-Free (SAC305) | Higher | Increased thermal stress, potential damage |
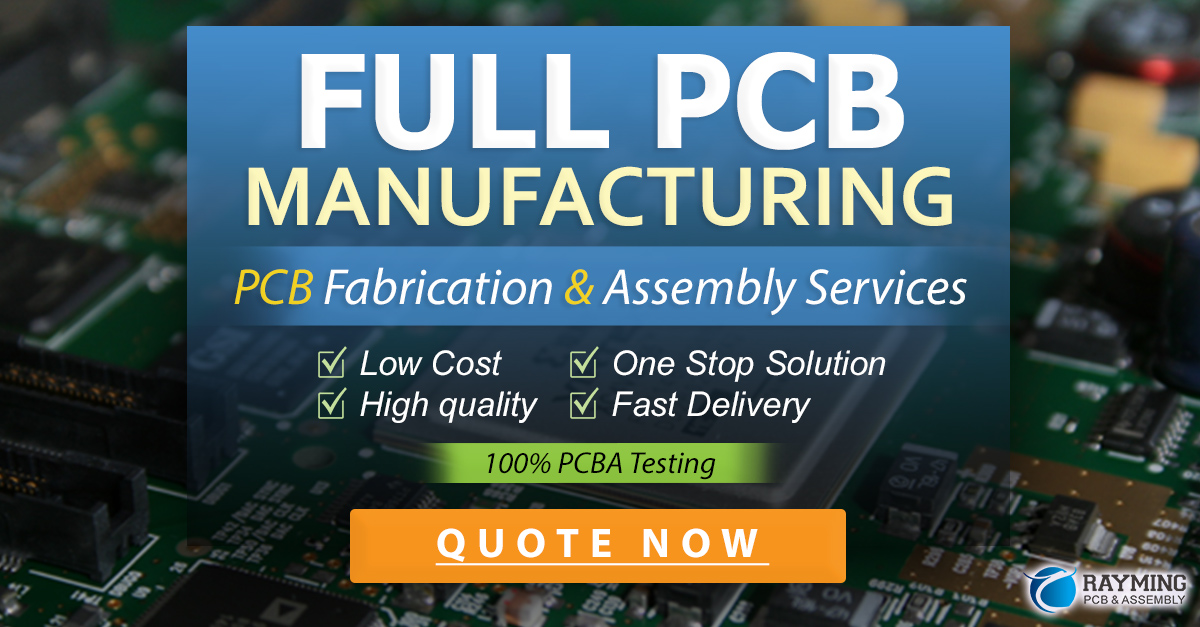
Cost Considerations
Raw Material Costs
Lead-free solders typically contain more expensive materials, such as silver, compared to leaded solders. This can result in higher raw material costs for lead-free solder.
Process Costs
The higher processing temperatures required for lead-free soldering can increase energy consumption and reduce the lifespan of manufacturing equipment. Additionally, the transition from leaded to lead-free solder may require investments in new equipment and training for personnel.
The Future of PCB Soldering
Advancements in Lead-Free Solder Technology
Researchers and manufacturers are continuously working to improve the performance and reliability of lead-free solders. Some recent advancements include:
- Development of new alloy compositions to enhance mechanical and thermal properties
- Optimization of PCB design and assembly processes for lead-free soldering
- Implementation of advanced quality control methods to detect and mitigate lead-free solder defects
Balancing Environmental Responsibility and Product Performance
As the electronics industry strives to reduce its environmental impact, the use of lead-free solder is likely to continue growing. However, it is crucial to balance environmental responsibility with product performance and reliability. Manufacturers must carefully consider the specific requirements of their products and select the most appropriate solder type for each application.
FAQ
- Is lead-free solder required by law?
-
In many countries, regulations such as the European Union’s RoHS Directive mandate the use of lead-free solder in most consumer electronics. However, some exemptions exist for certain applications, such as military and aerospace equipment.
-
Can leaded and lead-free solders be used together?
-
Mixing leaded and lead-free solders is generally not recommended, as it can lead to compatibility issues and reduced joint reliability. It is best to use either leaded or lead-free solder consistently throughout a PCB assembly.
-
How can manufacturers mitigate the reliability risks associated with lead-free solder?
-
Manufacturers can mitigate lead-free solder reliability risks by optimizing PCB design, implementing strict process controls, and conducting thorough testing and inspection. Additionally, using advanced lead-free solder alloys and surface finishes can improve joint reliability.
-
Are there any health risks associated with lead-free solder?
-
While lead-free solders eliminate the health risks associated with lead exposure, some studies have raised concerns about the potential toxicity of certain lead-free solder constituents, such as silver and copper. However, these risks are considered much lower than those posed by lead.
-
Will leaded solder be completely phased out in the future?
- It is unlikely that leaded solder will be completely phased out in the near future, as some applications, such as high-reliability military and aerospace electronics, may continue to rely on leaded solder for its proven performance. However, the use of lead-free solder will likely continue to grow in consumer electronics and other markets.
The lead-free solder debate in PCB manufacturing is a complex issue that requires careful consideration of environmental responsibility, product performance, and economic factors. As the electronics industry continues to evolve, it is essential for manufacturers to stay informed about the latest developments in solder technology and to make informed decisions that balance these competing priorities.
Leave a Reply