The Role of PCBs in Automotive Innovation
PCBs are the backbone of modern automotive electronics, providing the foundation for a wide range of systems and applications. From engine management and powertrain control to infotainment and advanced driver assistance systems (ADAS), PCBs enable the integration of complex electronic components into a compact and reliable package.
Engine Management and Powertrain Control
One of the primary applications of PCBs in the automotive industry is in engine management and powertrain control systems. These systems rely on a network of sensors, actuators, and electronic control units (ECUs) to optimize engine performance, fuel efficiency, and emissions control. PCBs provide the necessary interconnections between these components, enabling the rapid transmission and processing of data.
Component | Function |
---|---|
Sensors | Collect data on engine parameters such as temperature, pressure, and speed |
Actuators | Control various engine functions such as fuel injection, valve timing, and turbocharging |
ECUs | Process sensor data and control actuators to optimize engine performance |
Infotainment and Connectivity
Another area where PCBs have had a significant impact on automotive innovation is in the development of advanced infotainment and connectivity systems. Modern vehicles are equipped with a wide range of features, including touchscreen displays, audio systems, navigation, and wireless connectivity. PCBs provide the necessary infrastructure for these systems, enabling the integration of multiple functions into a single, user-friendly interface.
Feature | Description |
---|---|
Touchscreen Displays | Provide a intuitive interface for accessing various vehicle functions and settings |
Audio Systems | Deliver high-quality sound for music, podcasts, and hands-free calling |
Navigation | Offers real-time guidance and traffic updates to help drivers reach their destinations efficiently |
Wireless Connectivity | Enables the integration of smartphones and other devices for streaming media and accessing remote services |
Advanced Driver Assistance Systems (ADAS)
ADAS is a rapidly growing area of automotive innovation that relies heavily on PCB technology. These systems use a combination of sensors, cameras, and radar to provide drivers with enhanced safety features such as lane departure warning, adaptive cruise control, and automatic emergency braking. PCBs play a critical role in the development of these systems, providing the necessary interconnections between the various components and enabling the rapid processing of sensor data.
ADAS Feature | Description |
---|---|
Lane Departure Warning | Alerts drivers when the vehicle begins to drift out of its lane |
Adaptive Cruise Control | Automatically adjusts the vehicle’s speed to maintain a safe distance from other vehicles |
Automatic Emergency Braking | Applies the brakes automatically to avoid or mitigate collisions |
Challenges and Opportunities in Automotive PCB Manufacturing
While PCBs have enabled significant advancements in automotive technology, their integration into vehicles also presents a number of challenges and opportunities for manufacturers.
Reliability and Durability
One of the primary challenges in automotive PCB manufacturing is ensuring the reliability and durability of the boards in the harsh operating conditions of a vehicle. PCBs must be able to withstand extreme temperatures, vibrations, and exposure to moisture and chemicals. To address these challenges, manufacturers have developed specialized materials and manufacturing processes that enhance the robustness of automotive PCBs.
Conformal Coatings
Conformal coatings are thin, protective layers applied to PCBs to shield them from environmental factors such as moisture, dust, and chemicals. These coatings help to improve the reliability and longevity of automotive PCBs, reducing the risk of failure in harsh operating conditions.
High-Temperature Materials
Automotive PCBs are often exposed to extreme temperatures, both from the operating environment and from the heat generated by electronic components. To withstand these conditions, manufacturers use high-temperature materials such as polyimide and ceramic substrates, which offer superior thermal stability compared to traditional FR-4 materials.
Miniaturization and Integration
Another challenge in automotive PCB manufacturing is the need for miniaturization and integration of multiple functions onto a single board. As vehicles become more complex and feature-rich, there is a growing demand for smaller, more compact PCBs that can accommodate a greater number of components and functions.
High-Density Interconnect (HDI) PCBs
HDI PCBs are a type of PCB that feature fine pitch traces and micro vias, enabling a higher density of interconnections on a smaller board area. These PCBs are increasingly being used in automotive applications to enable the integration of more functions into a smaller package.
Flexible and Rigid-Flex PCBs
Flexible and rigid-flex PCBs are another solution for miniaturization and integration in automotive applications. These PCBs combine flexible and rigid substrates, allowing for greater design flexibility and the ability to conform to irregular shapes and spaces within the vehicle.
Cost and Volume Production
Finally, automotive PCB manufacturing must also address the challenges of cost and volume production. With the increasing demand for advanced electronics in vehicles, manufacturers must find ways to produce high-quality PCBs at a low cost and in large volumes.
Automation and Lean Manufacturing
To achieve cost-effective volume production, many automotive PCB manufacturers are turning to automation and lean manufacturing techniques. By automating key processes such as assembly, inspection, and testing, manufacturers can reduce labor costs and improve efficiency. Lean manufacturing principles, such as just-in-time inventory management and continuous improvement, also help to streamline operations and reduce waste.
Standardization and Modular Design
Another approach to reducing costs and improving volume production is through standardization and modular design. By using standardized components and designs across multiple vehicle platforms, manufacturers can reduce the complexity and cost of PCB production. Modular designs also allow for greater flexibility and easier updates as new technologies and features are developed.
The Future of Automotive PCB Innovation
As the automotive industry continues to evolve, the role of PCBs in enabling innovation will only become more critical. Some of the key trends and developments that are likely to shape the future of automotive PCB manufacturing include:
Electrification and Hybrid Powertrains
The growing demand for electric and hybrid vehicles is driving the development of new PCB solutions for power management and distribution. These PCBs must be able to handle high voltages and currents while also being lightweight and compact to maximize vehicle range and performance.
Autonomous Driving and Connected Vehicles
The development of autonomous driving technology and connected vehicle systems will require even more advanced PCBs to enable the rapid processing of sensor data and the reliable communication between vehicles and infrastructure. These PCBs will need to be highly reliable and secure to ensure the safety and integrity of the autonomous driving system.
5G and Beyond
The rollout of 5G wireless networks will enable new possibilities for connected vehicle services and applications. PCBs will play a critical role in enabling the high-speed, low-latency communication required for these services, as well as the integration of 5G modules into vehicle systems.
Sustainability and Circular Economy
As concerns about environmental sustainability continue to grow, there will be increasing pressure on automotive PCB manufacturers to adopt more sustainable practices and materials. This may include the use of recycled and recyclable materials, as well as the development of more energy-efficient manufacturing processes.
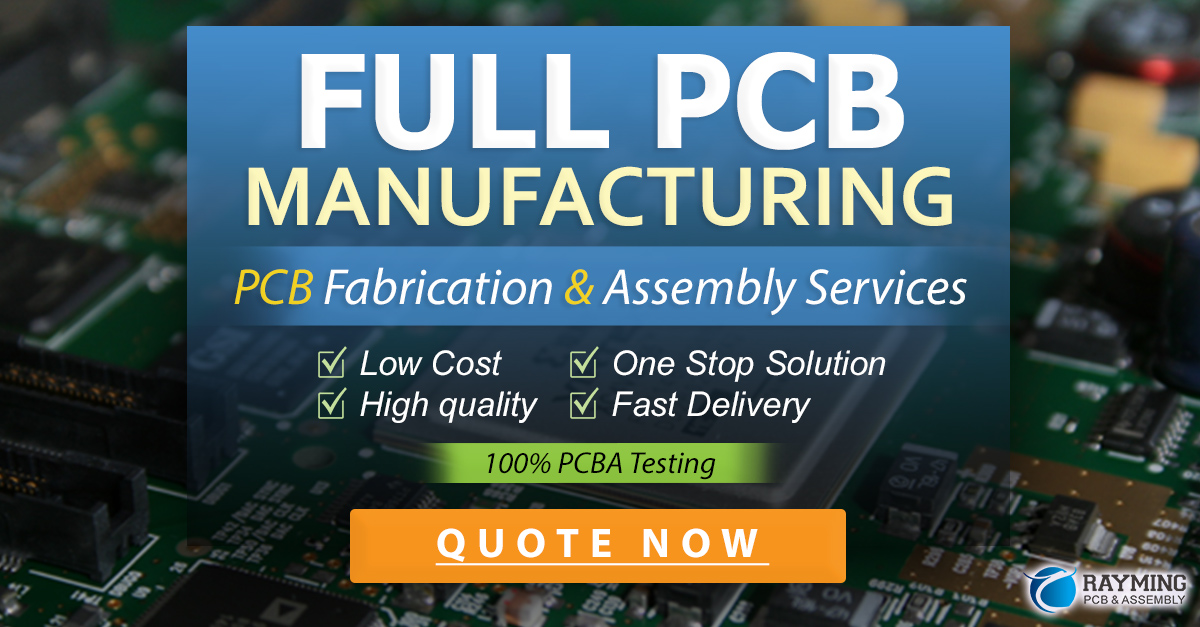
Frequently Asked Questions (FAQ)
- What are the key benefits of using PCBs in automotive applications?
PCBs offer several key benefits for automotive applications, including: - Enabling the integration of complex electronic systems into a compact and reliable package
- Providing the necessary interconnections for rapid data transmission and processing
- Enhancing the reliability and durability of electronic components in harsh operating conditions
-
Enabling the miniaturization and integration of multiple functions onto a single board
-
What are some of the specialized materials used in automotive PCBs?
Some of the specialized materials used in automotive PCBs include: - Polyimide substrates for high-temperature applications
- Ceramic substrates for superior thermal stability
-
Conformal coatings for protection against moisture, dust, and chemicals
-
How are manufacturers addressing the challenges of cost and volume production in automotive PCBs?
Manufacturers are addressing the challenges of cost and volume production through: - Automation and lean manufacturing techniques to reduce labor costs and improve efficiency
- Standardization and modular design to reduce complexity and enable greater flexibility
-
The use of cost-effective materials and manufacturing processes
-
What are some of the future trends in automotive PCB innovation?
Some of the key trends shaping the future of automotive PCB innovation include: - The development of new solutions for electrification and hybrid powertrains
- The integration of autonomous driving technology and connected vehicle systems
- The rollout of 5G wireless networks and the enabling of new connected vehicle services
-
The adoption of more sustainable practices and materials in PCB manufacturing
-
How are automotive PCBs different from PCBs used in other industries?
Automotive PCBs are designed to withstand the unique challenges of the vehicle operating environment, including: - Extreme temperatures and temperature fluctuations
- Vibrations and mechanical stress
- Exposure to moisture, chemicals, and other environmental factors
As a result, automotive PCBs often require specialized materials, manufacturing processes, and testing procedures to ensure their reliability and durability in these harsh conditions.
Conclusion
PCB manufacturing has become a critical enabler of innovation in the automotive industry, providing the necessary foundation for the development of advanced electronic systems and features. From engine management and infotainment to ADAS and autonomous driving, PCBs are at the heart of the technological revolution that is transforming the way we drive.
However, the integration of PCBs into vehicles also presents a number of challenges and opportunities for manufacturers, including the need for increased reliability and durability, miniaturization and integration, and cost-effective volume production. By addressing these challenges through the use of specialized materials, manufacturing processes, and design techniques, automotive PCB manufacturers are helping to pave the way for a new era of innovation in the industry.
As the automotive landscape continues to evolve, the role of PCBs in enabling new technologies and features will only become more important. From the development of new solutions for electrification and autonomous driving to the integration of 5G connectivity and sustainable manufacturing practices, the future of automotive PCB innovation is bright and full of exciting possibilities.
Leave a Reply