What is PCB Soldermask and Why Remove It?
Soldermask, also known as solder resist or solder mask, is a thin layer of polymer applied to the copper traces of a printed circuit board (PCB) to protect them from oxidation, prevent solder bridges, and provide electrical insulation. While soldermask is essential for the proper functioning and longevity of a PCB, there are situations where it needs to be removed, such as:
- Repairing or modifying a PCB
- Exposing copper traces for testing or troubleshooting
- Preparing a PCB for custom surface finishes or coatings
- Salvaging components from a damaged or obsolete PCB
Types of Soldermask
There are two main types of soldermask used in PCB manufacturing:
-
Liquid Photoimageable Soldermask (LPI): This type of soldermask is applied as a liquid and then cured using UV light. LPI soldermask is the most common type used in the industry due to its ease of application, high resolution, and durability.
-
Dry Film Soldermask (DFSM): This type of soldermask comes in the form of a pre-made film that is laminated onto the PCB surface and then cured using heat and pressure. DFSM is less common than LPI but offers better chemical resistance and is suitable for high-temperature applications.
Soldermask Type | Application Method | Curing Method | Advantages | Disadvantages |
---|---|---|---|---|
Liquid Photoimageable Soldermask (LPI) | Liquid | UV light | Easy application, high resolution, durable | Requires specialized equipment |
Dry Film Soldermask (DFSM) | Pre-made film | Heat and pressure | Better chemical resistance, suitable for high-temp applications | More expensive, lower resolution |
Methods for PCB Soldermask Removal
There are several methods for removing soldermask from a PCB, each with its own advantages and disadvantages. The choice of method depends on factors such as the type of soldermask, the size of the area to be removed, and the available tools and materials.
1. Chemical Stripping
Chemical stripping involves using a specialized soldermask stripper solution to dissolve the soldermask layer. This method is relatively quick and easy but requires careful handling of the chemicals and proper ventilation.
Steps for Chemical Stripping
- Wear protective gloves and eyewear.
- Apply the soldermask stripper solution to the desired area using a brush or cotton swab.
- Allow the solution to sit for the recommended time (usually 5-15 minutes).
- Use a soft brush or scraper to remove the softened soldermask.
- Rinse the PCB with water and dry it thoroughly.
2. Mechanical Abrasion
Mechanical abrasion involves using abrasive tools such as sandpaper, steel wool, or a rotary tool with a grinding attachment to physically remove the soldermask layer. This method is suitable for small areas but can be time-consuming and may damage the copper traces if not done carefully.
Steps for Mechanical Abrasion
- Secure the PCB to a stable work surface.
- Select the appropriate abrasive tool based on the size of the area and the desired level of precision.
- Gently sand or grind away the soldermask, being careful not to damage the copper traces.
- Use compressed air or a soft brush to remove any debris.
- Inspect the PCB for any remaining soldermask and repeat the process if necessary.
3. Laser Ablation
Laser ablation involves using a high-power laser to vaporize the soldermask layer. This method is fast, precise, and does not require any chemicals or abrasives. However, it requires specialized equipment and may not be cost-effective for small-scale or one-time projects.
Steps for Laser Ablation
- Set up the laser ablation system according to the manufacturer’s instructions.
- Adjust the laser parameters (power, speed, and focus) based on the type and thickness of the soldermask.
- Position the PCB in the laser chamber and align the laser with the desired area.
- Initiate the laser ablation process and wait for it to complete.
- Remove the PCB from the laser chamber and inspect it for any remaining soldermask.
Comparison of PCB Soldermask Removal Methods
Method | Advantages | Disadvantages |
---|---|---|
Chemical Stripping | Quick, easy, suitable for large areas | Requires chemicals, proper ventilation |
Mechanical Abrasion | Suitable for small areas, no chemicals needed | Time-consuming, may damage copper traces |
Laser Ablation | Fast, precise, no chemicals or abrasives | Requires specialized equipment, may not be cost-effective |
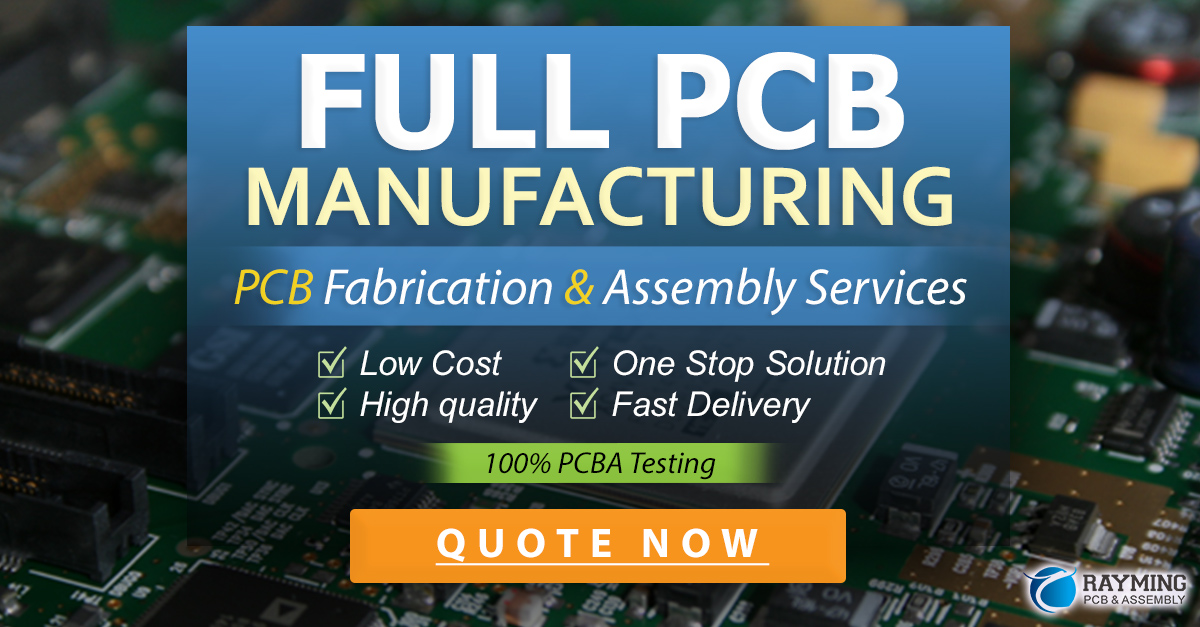
Safety Precautions and Best Practices
When removing soldermask from a PCB, it is important to follow safety precautions and best practices to avoid injury and ensure the best possible results.
Safety Precautions
- Always wear protective gloves and eyewear when handling chemicals or abrasive tools.
- Work in a well-ventilated area when using chemical strippers or laser ablation systems.
- Follow the manufacturer’s instructions and safety guidelines for any tools or chemicals used.
- Dispose of any waste materials properly and in accordance with local regulations.
Best Practices
- Test the chosen method on a small, non-critical area of the PCB before proceeding with the entire board.
- Work slowly and carefully to avoid damaging the copper traces or other components.
- Clean the PCB thoroughly after removing the soldermask to ensure optimal performance and longevity.
- Consider using a professional PCB rework service for complex or high-value boards.
Frequently Asked Questions (FAQ)
-
Q: Can I use household chemicals like acetone or nail polish remover to strip soldermask?
A: No, household chemicals are not recommended for removing soldermask as they may damage the PCB or leave residues that can affect its performance. Always use a specialized soldermask stripper solution designed for this purpose. -
Q: How long does it take to remove soldermask using chemical stripping?
A: The time required for chemical stripping depends on the type and thickness of the soldermask, as well as the specific stripper solution used. In general, the process takes between 5 and 15 minutes, but always follow the manufacturer’s recommended time for best results. -
Q: Can I remove soldermask using a regular laser pointer?
A: No, a regular laser pointer does not have sufficient power or precision to remove soldermask safely and effectively. Laser ablation requires a specialized high-power laser system designed for this purpose. -
Q: Will removing the soldermask affect the functionality of my PCB?
A: Removing the soldermask will expose the copper traces, making them more susceptible to oxidation and environmental factors. This can affect the long-term reliability and performance of the PCB. If the exposed areas are not critical for the board’s functionality, the impact may be minimal. -
Q: Can I reapply soldermask after removing it from a PCB?
A: Yes, it is possible to reapply soldermask after removing it, but the process can be challenging and may not result in the same level of protection and appearance as the original soldermask. If you need to reapply soldermask, it is recommended to use a professional PCB rework service or consult with a PCB manufacturer for guidance.
Conclusion
Removing soldermask from a PCB can be necessary for various reasons, such as repairing, modifying, or salvaging the board. There are several methods for PCB soldermask removal, including chemical stripping, mechanical abrasion, and laser ablation, each with its own advantages and disadvantages. When choosing a method, consider factors such as the type of soldermask, the size of the area to be removed, and the available tools and materials.
Regardless of the method chosen, always follow safety precautions and best practices to avoid injury and ensure the best possible results. If you are unsure about your ability to remove soldermask safely and effectively, consider using a professional PCB rework service or consulting with a PCB manufacturer for guidance.
By understanding the different methods and considerations involved in PCB soldermask removal, you can make informed decisions and achieve the desired results for your PCB projects.
Leave a Reply