What is Electronic Assembly?
Electronic assembly is the process of assembling electronic components onto a PCB to create a functional electronic device. This process involves several steps, including:
-
PCB fabrication: The PCB is designed and manufactured according to the specific requirements of the electronic device.
-
Component procurement: The necessary electronic components, such as resistors, capacitors, and integrated circuits, are sourced and purchased.
-
PCB Assembly: The electronic components are soldered onto the PCB using various techniques, such as through-hole assembly or surface mount technology (SMT).
-
Testing and quality control: The assembled PCB is tested to ensure it functions as intended and meets the required quality standards.
Electronic assembly is a complex process that requires specialized knowledge, skills, and equipment. As such, many companies choose to outsource their electronic assembly needs to specialized service providers.
Benefits of Outsourcing Electronic Assembly
Outsourcing electronic assembly to a specialized service provider offers several benefits, including:
-
Cost savings: Outsourcing electronic assembly can be more cost-effective than setting up an in-house assembly line, especially for small to medium-sized businesses.
-
Expertise and experience: Electronic assembly service providers have the necessary expertise and experience to handle complex assembly projects efficiently and effectively.
-
Access to advanced technology: Service providers invest in the latest assembly technology and equipment, ensuring that your electronic devices are assembled using state-of-the-art techniques.
-
Scalability and flexibility: Outsourcing allows you to scale your production up or down as needed, without having to worry about the capacity of your in-house assembly line.
-
Focus on core competencies: By outsourcing electronic assembly, you can focus on your core competencies, such as product design and marketing, while leaving the assembly process to the experts.
Key Factors to Consider When Choosing an Electronic Assembly Service
When selecting an electronic assembly service provider, there are several key factors to consider to ensure you choose the best partner for your needs. These factors include:
1. Technical Capabilities
The first factor to consider is the technical capabilities of the service provider. You should look for a provider that has experience in assembling the type of electronic devices you require and has the necessary equipment and expertise to handle your project. Some key technical capabilities to look for include:
- Experience with various assembly techniques, such as through-hole and surface mount technology (SMT)
- Capability to handle high-mix, low-volume production runs
- Expertise in assembling complex, multi-layer PCBs
- Access to advanced assembly equipment, such as automated optical inspection (AOI) machines and X-ray inspection systems
2. Quality Control and Testing
Quality control and testing are critical aspects of electronic assembly. You should choose a service provider that has a robust quality control process in place to ensure that your electronic devices meet the required quality standards. Some key quality control and testing capabilities to look for include:
- In-process quality control checks
- Automated optical inspection (AOI) to detect assembly defects
- X-ray inspection for hidden defects
- Functional testing to ensure the device performs as intended
- Compliance with industry standards, such as IPC-A-610 and ISO 9001
3. Certifications and Standards Compliance
Industry certifications and standards compliance are important indicators of a service provider’s commitment to quality and reliability. You should look for a provider that holds relevant certifications and complies with industry standards, such as:
- ISO 9001: Quality management system certification
- ISO 14001: Environmental management system certification
- IPC-A-610: Acceptability of Electronic Assemblies standard
- RoHS (Restriction of Hazardous Substances) compliance
- UL (Underwriters Laboratories) certification for safety
4. Manufacturing Capabilities and Capacity
The manufacturing capabilities and capacity of the service provider are important factors to consider, especially if you have high-volume production requirements. You should choose a provider that has the necessary manufacturing capabilities and capacity to handle your project, such as:
- Automated assembly lines for high-volume production
- Flexible manufacturing systems for high-mix, low-volume production
- Rapid prototyping capabilities for quick turnaround times
- Scalable production capacity to accommodate changes in demand
5. Supply Chain Management
Effective supply chain management is critical for ensuring the timely delivery of your electronic devices. You should choose a service provider that has a robust supply chain management process in place, including:
- Strong relationships with component suppliers
- Effective inventory management to ensure the availability of components
- Ability to handle component obsolescence and find suitable replacements
- Effective logistics and shipping management to ensure timely delivery
6. Communication and Customer Service
Good communication and customer service are essential for a successful partnership with your electronic assembly service provider. You should choose a provider that maintains open and transparent communication throughout the project, and provides responsive customer service. Some key communication and customer service factors to consider include:
- Clear and timely project updates
- Easy access to project managers and technical support
- Flexibility to accommodate changes in project requirements
- Responsive and helpful customer service
- Ability to provide after-sales support and warranty services
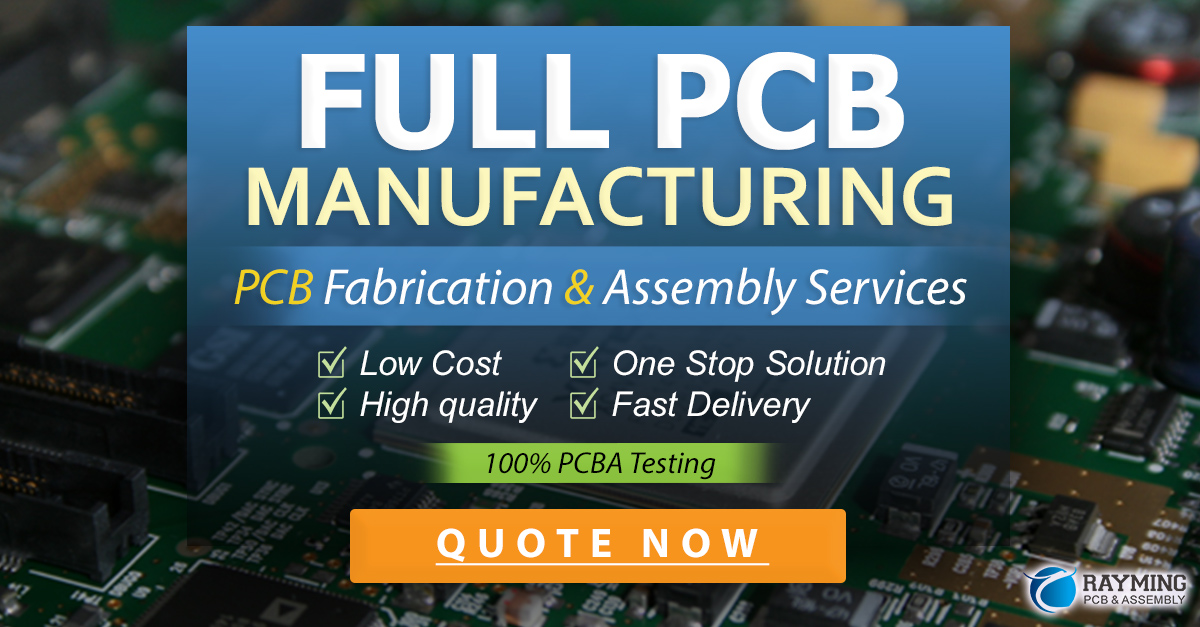
Steps to Choosing the Best Electronic Assembly Service
Now that we have discussed the key factors to consider when choosing an electronic assembly service provider, let’s look at the steps you can take to select the best partner for your needs.
Step 1: Define Your Requirements
The first step in choosing an electronic assembly service provider is to clearly define your project requirements. This includes specifying the type of electronic device you need to assemble, the required production volume, the target delivery date, and any special requirements or constraints.
Step 2: Research Potential Service Providers
Once you have defined your requirements, the next step is to research potential service providers. You can start by searching online for electronic assembly service providers in your area or those that specialize in your type of electronic device. You can also ask for referrals from colleagues or industry associations.
Step 3: Evaluate Technical Capabilities
After identifying potential service providers, you should evaluate their technical capabilities to ensure they have the necessary expertise and equipment to handle your project. This includes reviewing their experience with different assembly techniques, their capability to handle your production volume, and their access to advanced assembly equipment.
Step 4: Assess Quality Control and Testing Processes
Quality control and testing are critical aspects of electronic assembly. You should assess the quality control and testing processes of potential service providers to ensure they have a robust system in place to detect and prevent defects. This includes reviewing their in-process quality control checks, automated inspection capabilities, and compliance with industry standards.
Step 5: Review Certifications and Standards Compliance
Industry certifications and standards compliance are important indicators of a service provider’s commitment to quality and reliability. You should review the certifications and standards compliance of potential service providers to ensure they meet the necessary requirements for your project.
Step 6: Evaluate Manufacturing Capabilities and Capacity
If you have high-volume production requirements, you should evaluate the manufacturing capabilities and capacity of potential service providers to ensure they can handle your project. This includes reviewing their automated assembly lines, flexible manufacturing systems, and scalable production capacity.
Step 7: Assess Supply Chain Management
Effective supply chain management is critical for ensuring the timely delivery of your electronic devices. You should assess the supply chain management processes of potential service providers to ensure they have strong relationships with component suppliers, effective inventory management, and the ability to handle component obsolescence.
Step 8: Evaluate Communication and Customer Service
Good communication and customer service are essential for a successful partnership with your electronic assembly service provider. You should evaluate the communication and customer service of potential service providers to ensure they maintain open and transparent communication, provide responsive customer service, and have the flexibility to accommodate changes in project requirements.
Step 9: Request Quotes and Compare Pricing
Once you have evaluated potential service providers based on the above factors, you should request quotes and compare pricing. However, it is important to remember that price should not be the only factor in your decision. You should also consider the value-added services and support provided by the service provider.
Step 10: Make Your Selection and Establish a Partnership
After evaluating all the factors and comparing quotes, you can make your selection and establish a partnership with your chosen electronic assembly service provider. It is important to establish clear communication channels, agree on project milestones and deliverables, and maintain open and transparent communication throughout the project.
Frequently Asked Questions (FAQ)
- What is the difference between through-hole and surface mount technology (SMT) assembly?
-
Through-hole assembly involves inserting component leads through holes in the PCB and soldering them on the opposite side. SMT assembly involves placing components directly onto the surface of the PCB and soldering them in place. SMT assembly is generally faster and more efficient than through-hole assembly.
-
What is the importance of industry certifications and standards compliance?
-
Industry certifications and standards compliance are important indicators of a service provider’s commitment to quality and reliability. They ensure that the service provider has the necessary processes and controls in place to meet industry requirements and deliver high-quality electronic devices.
-
How can I ensure the timely delivery of my electronic devices?
-
To ensure the timely delivery of your electronic devices, you should choose a service provider with effective supply chain management processes, including strong relationships with component suppliers, effective inventory management, and the ability to handle component obsolescence. You should also establish clear communication channels and agree on project milestones and deliverables.
-
What should I do if I encounter quality issues with my assembled electronic devices?
-
If you encounter quality issues with your assembled electronic devices, you should first contact your electronic assembly service provider and provide them with detailed information about the issue. They should have a process in place to investigate and resolve quality issues in a timely manner. If the issue persists, you may need to escalate the matter to senior management or consider switching to a different service provider.
-
Can I visit the electronic assembly service provider’s facility before making a selection?
- Yes, most electronic assembly service providers welcome visits from potential clients to their facility. This can give you an opportunity to see their assembly lines, equipment, and processes firsthand, and to meet with their team members. It can also help you assess their communication and customer service capabilities and ensure that they are a good fit for your project.
Conclusion
Choosing the best electronic assembly service provider is a critical decision that can impact the success of your project. By considering the key factors discussed in this article, including technical capabilities, quality control and testing, certifications and standards compliance, manufacturing capabilities and capacity, supply chain management, and communication and customer service, you can select a partner that meets your specific needs and delivers high-quality electronic devices.
Remember to define your requirements clearly, research potential service providers, evaluate their capabilities and processes, and compare quotes and pricing before making your selection. And once you have established a partnership, maintain open and transparent communication and work together to ensure the success of your project.
By following these steps and selecting the right electronic assembly service provider, you can ensure that your electronic devices are assembled to the highest quality standards, delivered on time, and meet the needs of your customers and end-users.
Factor | Description | Importance |
---|---|---|
Technical Capabilities | Experience with various assembly techniques, equipment, and expertise to handle complex projects | High |
Quality Control and Testing | Robust quality control process, automated inspection capabilities, and compliance with industry standards | High |
Certifications and Standards Compliance | Holds relevant certifications (e.g., ISO 9001, ISO 14001) and complies with industry standards (e.g., IPC-A-610, RoHS) | High |
Manufacturing Capabilities and Capacity | Automated assembly lines, flexible manufacturing systems, and scalable production capacity | Medium to High |
Supply Chain Management | Strong relationships with component suppliers, effective inventory management, and ability to handle component obsolescence | High |
Communication and Customer Service | Open and transparent communication, responsive customer service, and flexibility to accommodate changes | High |
Leave a Reply