Introduction to Breadboard-to-PCB Transition
When developing electronic projects, it’s common to start with a breadboard prototype to quickly test and validate your circuit design. However, once you’ve proven your concept and are ready to move forward with a more permanent solution, transitioning from a breadboard to a printed circuit board (PCB) becomes essential. This guide will walk you through the process of moving from a breadboard prototype to a full product, covering key aspects such as circuit design, PCB layout, component selection, and manufacturing considerations.
Understanding the Differences Between Breadboards and PCBs
Before diving into the transition process, it’s important to understand the fundamental differences between breadboards and PCBs:
Aspect | Breadboard | PCB |
---|---|---|
Purpose | Rapid prototyping and testing | Permanent and reliable circuit implementation |
Reusability | Highly reusable, components can be easily inserted/removed | Components are soldered, not meant for frequent changes |
Durability | Less durable, prone to loose connections and physical damage | Robust and durable, suitable for long-term use |
Size | Larger footprint due to spacing between holes | Compact and space-efficient |
Signal Integrity | Prone to noise and crosstalk due to long jumper wires | Improved signal integrity with proper routing and layout |
Cost | Low cost for prototyping | Higher initial cost but cost-effective for mass production |
Understanding these differences will help you make informed decisions throughout the transition process.
Step 1: Finalize and Optimize Your Circuit Design
1.1 Review and Validate Your Breadboard Circuit
Before transitioning to a PCB, thoroughly review your breadboard circuit to ensure it functions as intended. Test the circuit under various conditions and make any necessary adjustments to improve its performance, reliability, and efficiency.
1.2 Create a Schematic Diagram
Translate your breadboard circuit into a schematic diagram using electronic design automation (EDA) software. A schematic diagram represents the logical connections between components and serves as a blueprint for your PCB layout. Popular EDA tools include:
- KiCad
- Eagle
- Altium Designer
- OrCAD
1.3 Optimize Component Selection
Review the components used in your breadboard circuit and consider optimizing them for your PCB design. Factors to consider include:
- Size and package type (through-hole vs. surface-mount)
- Availability and sourcing
- Cost
- Performance and specifications
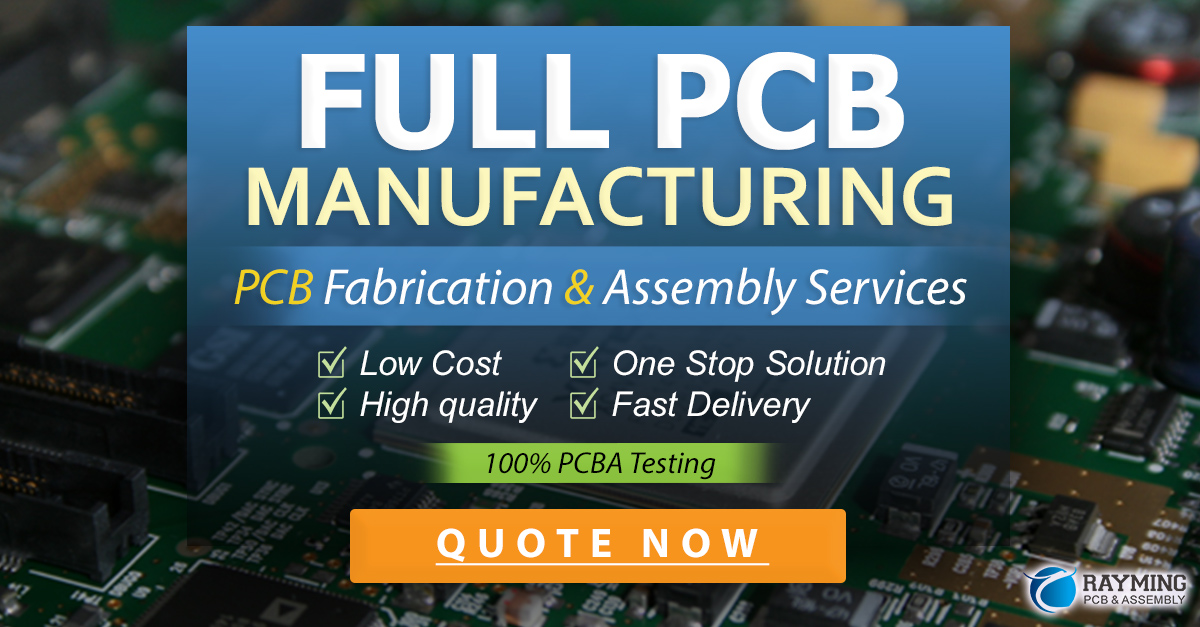
Step 2: Design Your PCB Layout
2.1 Choose the Appropriate PCB Size and Shape
Determine the size and shape of your PCB based on the space constraints of your final product enclosure. Consider factors such as component placement, mounting holes, and connectors.
2.2 Define PCB Layers and Stack-up
Decide on the number of layers your PCB will have and define the stack-up, which specifies the arrangement of copper layers, insulation, and any special materials. The number of layers depends on the complexity of your circuit and routing requirements.
2.3 Place Components and Route Traces
Using your EDA software, place the components on the PCB layout according to your schematic. Consider factors such as component orientation, spacing, and thermal management. Once the components are placed, route the traces to establish electrical connections. Follow best practices for PCB layout, including:
- Minimizing trace lengths and avoiding sharp angles
- Providing adequate clearance between traces and components
- Using ground planes for improved signal integrity and EMI reduction
- Considering high-current traces and power distribution
2.4 Add Silkscreen and Solder Mask
Include silkscreen labels to identify components, connectors, and important information on your PCB. Apply solder mask to protect the copper traces from oxidation and prevent accidental short circuits during soldering.
Step 3: Prototyping and Testing
3.1 Generate Manufacturing Files
Once your PCB layout is complete, generate the necessary manufacturing files, such as Gerber files and drill files. These files contain the information needed by PCB Manufacturers to fabricate your board.
3.2 Order PCB Prototypes
Submit your manufacturing files to a PCB fabrication service or manufacturer. Many online PCB Prototyping services offer fast turnaround times and affordable prices for small quantities. Some popular options include:
- JLCPCB
- PCBWay
- OSH Park
- Seeed Studio
3.3 Assemble and Test Prototypes
Upon receiving your PCB Prototypes, assemble the components onto the board using soldering techniques appropriate for your component types (e.g., through-hole or surface-mount). Test the assembled prototype to verify its functionality and performance. If any issues arise, make necessary revisions to your design and repeat the prototyping process.
Step 4: Preparing for Production
4.1 Design for Manufacturing (DFM)
Before moving to full-scale production, review your PCB design for manufacturability. Consider factors such as:
- Component placement and orientation for automated assembly
- Solder pad sizes and spacing
- Testability and accessibility for quality control
- Panelization for efficient fabrication
Consult with your PCB manufacturer for specific DFM guidelines and recommendations.
4.2 Create a Bill of Materials (BOM)
Prepare a detailed bill of materials that lists all the components required for your PCB Assembly. Include information such as part numbers, quantities, and supplier details. A well-organized BOM facilitates the procurement process and ensures consistent component sourcing.
4.3 Choose a Manufacturing Partner
Select a reliable manufacturing partner for PCB fabrication and assembly. Consider factors such as:
- Experience and expertise in your product type
- Quality control processes and certifications
- Lead times and production capacity
- Cost and minimum order quantities
- Communication and support
Establish clear communication channels with your manufacturing partner to ensure a smooth production process.
Step 5: Mass Production and Quality Control
5.1 Place Production Orders
Once your design is finalized and you’ve chosen a manufacturing partner, place your production orders for PCB fabrication and assembly. Provide your manufacturing partner with the necessary files, including Gerber files, drill files, and the bill of materials.
5.2 Implement Quality Control Measures
Establish quality control measures to ensure the consistency and reliability of your manufactured PCBs. This may include:
- Incoming inspection of PCBs and components
- In-circuit testing (ICT) or functional testing
- Visual inspection for soldering quality and workmanship
- Burn-in testing to identify early failures
Work with your manufacturing partner to implement appropriate quality control processes.
5.3 Packaging and Shipping
Determine the packaging requirements for your PCBs to ensure they are protected during shipping and storage. Consider factors such as electrostatic discharge (ESD) protection, moisture barriers, and physical protection. Label your packages clearly with relevant information, such as part numbers, quantities, and handling instructions.
Conclusion
Transitioning from a breadboard prototype to a full PCB product requires careful planning and execution. By following the steps outlined in this guide, you can successfully navigate the process of circuit design, PCB layout, prototyping, and mass production. Remember to prioritize key aspects such as component selection, design for manufacturability, and quality control to ensure the success of your final product.
Frequently Asked Questions (FAQ)
1. How do I choose the right PCB manufacturer for my project?
When selecting a PCB manufacturer, consider factors such as their experience, quality control processes, lead times, pricing, and customer support. Read reviews and ask for recommendations from other designers or engineers in your network. Request quotes from multiple manufacturers and compare their offerings to find the best fit for your project.
2. What are the benefits of using surface-mount components over through-hole components?
Surface-mount components offer several advantages over through-hole components, including:
- Smaller size and lower profile, enabling more compact PCB designs
- Improved high-frequency performance due to shorter lead lengths
- Faster and more efficient automated assembly processes
- Lower cost for high-volume production
However, through-hole components may be preferred for certain applications, such as high-power circuits or designs requiring greater mechanical strength.
3. How can I ensure good signal integrity in my PCB design?
To maintain good signal integrity in your PCB design, follow these best practices:
- Minimize trace lengths and avoid sharp angles or sudden changes in direction
- Use appropriate trace widths and spacing based on the signal frequency and current requirements
- Implement proper grounding techniques, such as ground planes and star grounding
- Consider the use of differential signaling for high-speed or noise-sensitive signals
- Use appropriate termination and impedance matching techniques
- Separate analog and digital circuits to minimize crosstalk and interference
4. What are some common pitfalls to avoid when transitioning from breadboard to PCB?
Some common pitfalls to avoid during the breadboard-to-PCB transition include:
- Not thoroughly testing and validating the breadboard circuit before moving to PCB design
- Failing to consider component availability, cost, and lead times during the design phase
- Neglecting design for manufacturability (DFM) principles, leading to production issues
- Inadequate documentation, such as incomplete or inaccurate schematics and bills of materials
- Skipping the prototyping stage and moving directly to mass production without proper testing
- Not establishing clear communication and expectations with the PCB manufacturer
By being aware of these potential pitfalls and taking proactive steps to address them, you can minimize risks and ensure a smoother transition process.
5. How can I reduce the cost of my PCB production?
To reduce the cost of your PCB production, consider the following strategies:
- Optimize your PCB design for manufacturability, minimizing complexity and using standard processes where possible
- Choose cost-effective components and consider using surface-mount components for automated assembly
- Minimize the PCB size and number of layers while still meeting your design requirements
- Order larger quantities to take advantage of volume discounts
- Consider panelizing your PCB design to maximize fabrication efficiency
- Explore alternative PCB materials, such as lower-cost substrates or finishes, that meet your performance requirements
- Negotiate with your PCB manufacturer for better pricing based on your specific needs and order volume
By implementing these cost-saving measures, you can reduce the overall expense of your PCB production without compromising quality or functionality.
Leave a Reply