Introduction
The rapid growth of the electric vehicle (EV) market has led to an increased demand for efficient and reliable charging infrastructure. As a result, the design and manufacturing of printed circuit boards (PCBs) for EV charging stations have become crucial in meeting this demand. PCB layout and PCB assembly play a vital role in ensuring the optimal performance, safety, and durability of EV charging stations. In this article, we will explore how PCB trends are shaping the future of EV charging infrastructure.
The Importance of PCB Layout in EV Charging Stations
Optimizing Power Delivery
One of the primary challenges in designing PCBs for EV charging stations is ensuring efficient power delivery. The layout of the PCB must be optimized to minimize power losses and ensure stable voltage regulation. This is achieved by carefully placing components, such as power MOSFETs and capacitors, to minimize the distance between them and reduce parasitic inductance. Additionally, using thicker copper traces and multiple layers can help distribute the current evenly and prevent hotspots.
Thermal Management
EV charging stations generate a significant amount of heat during operation, which can negatively impact the performance and lifespan of the PCB. Effective thermal management is crucial to dissipate heat and maintain optimal operating temperatures. PCB layout techniques, such as the use of thermal vias, heat spreaders, and adequate spacing between components, can help improve heat dissipation. Furthermore, the selection of appropriate materials, such as high thermal conductivity substrates and thermal interface materials, can enhance thermal performance.
Electromagnetic Compatibility (EMC)
EV charging stations must comply with stringent EMC regulations to ensure they do not interfere with other electronic devices or be affected by external electromagnetic noise. PCB layout plays a critical role in achieving EMC compliance. Proper grounding, shielding, and the use of filters can help minimize electromagnetic interference (EMI) and improve the overall system’s immunity to external disturbances. Additionally, the placement of sensitive components, such as communication modules and sensors, must be carefully considered to avoid interference from high-power components.
PCB Assembly Trends in EV Charging Stations
Surface Mount Technology (SMT)
SMT has become the preferred method for PCB assembly in EV charging stations due to its numerous advantages over through-hole technology. SMT allows for the use of smaller components, which results in more compact and lightweight PCBs. This is particularly important for wall-mounted and portable charging stations, where space is limited. Additionally, SMT enables faster assembly processes, higher component density, and improved reliability, making it an ideal choice for high-volume production.
Automated Optical Inspection (AOI)
To ensure the quality and reliability of PCBs used in EV charging stations, manufacturers are increasingly adopting automated optical inspection (AOI) systems. AOI uses high-resolution cameras and advanced image processing algorithms to detect defects, such as missing components, solder bridges, and incorrect component placement. This technology enables faster and more accurate inspection compared to manual methods, reducing the risk of defective PCBs entering the market. Moreover, AOI can provide valuable data for process improvement and traceability.
Conformal Coating
EV charging stations are often exposed to harsh environmental conditions, such as moisture, dust, and temperature fluctuations. To protect the PCBs from these elements, conformal coating is applied during the assembly process. Conformal coating is a thin, protective layer that covers the PCB surface, preventing corrosion, short circuits, and other damage caused by environmental factors. Various coating materials, such as acrylic, silicone, and polyurethane, are used depending on the specific requirements of the application.
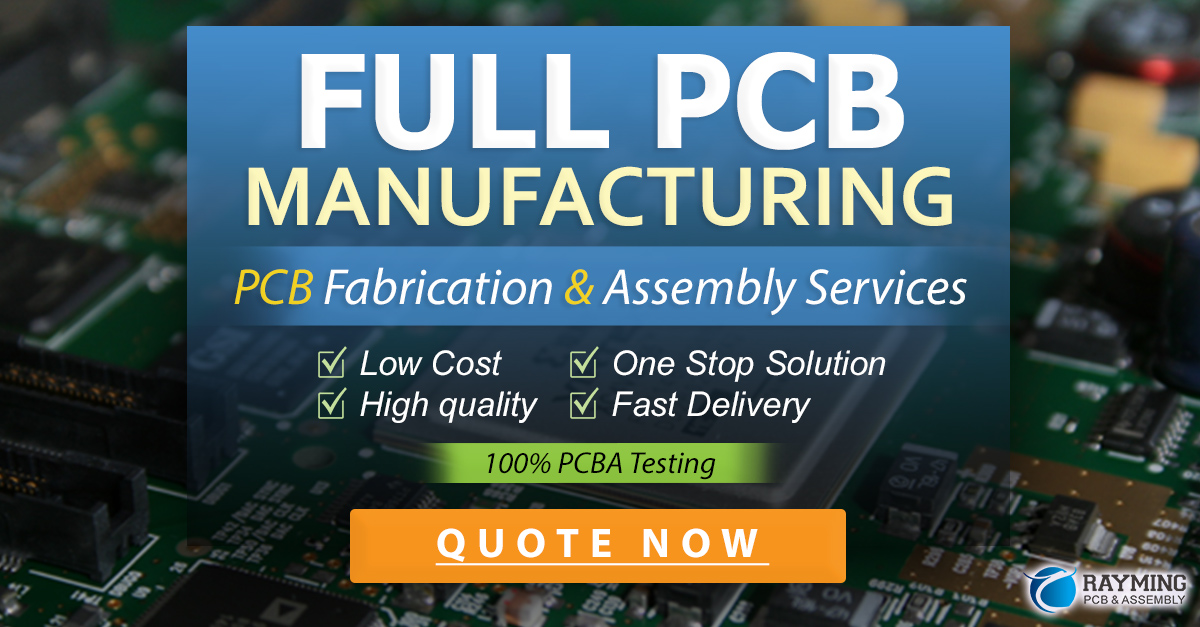
The Future of PCB Design and Assembly in EV Charging Stations
Modular Design
As the demand for EV charging infrastructure grows, there is a need for more flexible and scalable solutions. Modular PCB design is emerging as a trend to address this challenge. By designing PCBs as modular units, manufacturers can easily customize charging stations to meet specific requirements, such as power output, communication protocols, and user interfaces. This approach also simplifies maintenance and repairs, as faulty modules can be easily replaced without the need to replace the entire PCB.
Integration of Advanced Features
The increasing sophistication of EV charging stations is driving the integration of advanced features into PCBs. These features include:
- Smart charging algorithms to optimize charging speed and efficiency
- Vehicle-to-grid (V2G) functionality for bidirectional power flow
- Wireless communication for remote monitoring and control
- User authentication and payment systems
To accommodate these features, PCB designers must incorporate advanced components, such as microcontrollers, communication modules, and security chips. The layout and assembly of these components require careful consideration to ensure optimal performance and security.
Sustainable Materials and Processes
As environmental concerns continue to grow, there is a push towards the use of sustainable materials and processes in PCB manufacturing. This includes the use of halogen-free and lead-free materials, as well as the adoption of green manufacturing practices, such as energy-efficient equipment and waste reduction. Additionally, the development of biodegradable and recyclable PCB substrates is gaining traction, which could significantly reduce the environmental impact of EV charging stations at the end of their life cycle.
Frequently Asked Questions (FAQ)
1. What are the key challenges in designing PCBs for EV charging stations?
The key challenges in designing PCBs for EV charging stations include optimizing power delivery, ensuring effective thermal management, and achieving electromagnetic compatibility (EMC) compliance. PCB designers must carefully consider component placement, material selection, and layout techniques to address these challenges.
2. Why is surface mount technology (SMT) preferred for PCB assembly in EV charging stations?
SMT is preferred for PCB assembly in EV charging stations due to its numerous advantages, such as the ability to use smaller components, faster assembly processes, higher component density, and improved reliability. These benefits make SMT an ideal choice for high-volume production and compact charging station designs.
3. How does automated optical inspection (AOI) improve the quality and reliability of PCBs in EV charging stations?
AOI uses high-resolution cameras and advanced image processing algorithms to detect defects in PCBs, such as missing components, solder bridges, and incorrect component placement. This technology enables faster and more accurate inspection compared to manual methods, reducing the risk of defective PCBs entering the market.
4. What is the purpose of conformal coating in PCB assembly for EV charging stations?
Conformal coating is a thin, protective layer applied to the PCB surface during the assembly process. It protects the PCB from harsh environmental conditions, such as moisture, dust, and temperature fluctuations, preventing corrosion, short circuits, and other damage caused by these factors.
5. How can modular PCB design benefit EV charging station manufacturers?
Modular PCB design allows manufacturers to easily customize charging stations to meet specific requirements, such as power output, communication protocols, and user interfaces. This approach also simplifies maintenance and repairs, as faulty modules can be easily replaced without the need to replace the entire PCB, making it a more flexible and scalable solution.
Conclusion
PCB layout and PCB assembly are critical aspects of EV charging station design and manufacturing. As the demand for efficient and reliable charging infrastructure grows, PCB Trends are evolving to meet these challenges. From optimizing power delivery and thermal management to adopting advanced assembly techniques and integrating cutting-edge features, PCB designers and manufacturers are setting a new trend in the EV charging industry.
By embracing these trends, EV charging station manufacturers can create more compact, efficient, and reliable products that meet the growing needs of the market. As the world moves towards a more sustainable future, the role of PCBs in enabling the widespread adoption of electric vehicles cannot be overstated. With continued innovation and collaboration between PCB designers, manufacturers, and EV charging station providers, we can expect to see even more exciting developments in this field in the years to come.
Leave a Reply