The Rise of High-Density Interconnect (HDI) PCBs
High-Density Interconnect (HDI) PCBs are becoming increasingly popular due to their ability to accommodate a large number of components in a small form factor. HDI PCBs feature smaller vias, thinner traces, and reduced spacing between components, enabling the creation of highly compact and efficient electronic devices.
Benefits of HDI PCBs
- Miniaturization: HDI PCBs allow for the development of smaller, more portable electronic devices.
- Improved signal integrity: The reduced trace lengths and smaller vias in HDI PCBs minimize signal loss and improve overall signal integrity.
- Enhanced thermal management: HDI PCBs offer better thermal management due to their ability to dissipate heat more efficiently.
Parameter | Traditional PCB | HDI PCB |
---|---|---|
Via Size | 0.3-0.5 mm | 0.1-0.2 mm |
Trace Width | 0.1-0.2 mm | 0.05-0.1 mm |
Layer Count | 2-8 layers | 8-16 layers |
The Adoption of Flexible and Rigid-Flex PCBs
Flexible and rigid-flex PCBs are gaining traction in the industry due to their ability to conform to various shapes and sizes, making them ideal for applications that require flexibility and durability.
Advantages of Flexible and Rigid-Flex PCBs
- Improved reliability: Flexible and rigid-flex PCBs are more resilient to vibrations and mechanical stress, increasing the overall reliability of the device.
- Space-saving design: These PCBs can be folded and bent to fit into tight spaces, reducing the overall size of the device.
- Reduced assembly costs: Flexible and rigid-flex PCBs eliminate the need for additional connectors and cables, simplifying the assembly process and reducing costs.
The Growth of Embedded Components
Embedded components, such as resistors, capacitors, and inductors, are increasingly being integrated directly into the PCB substrate. This trend is driven by the need for smaller, more efficient, and cost-effective electronic devices.
Benefits of Embedded Components
- Reduced board size: Embedding components within the PCB substrate frees up valuable board space, allowing for smaller and more compact designs.
- Improved signal integrity: Embedded components minimize the distance between components, reducing signal loss and improving overall signal integrity.
- Enhanced reliability: By integrating components directly into the PCB, the number of solder joints is reduced, increasing the reliability of the device.
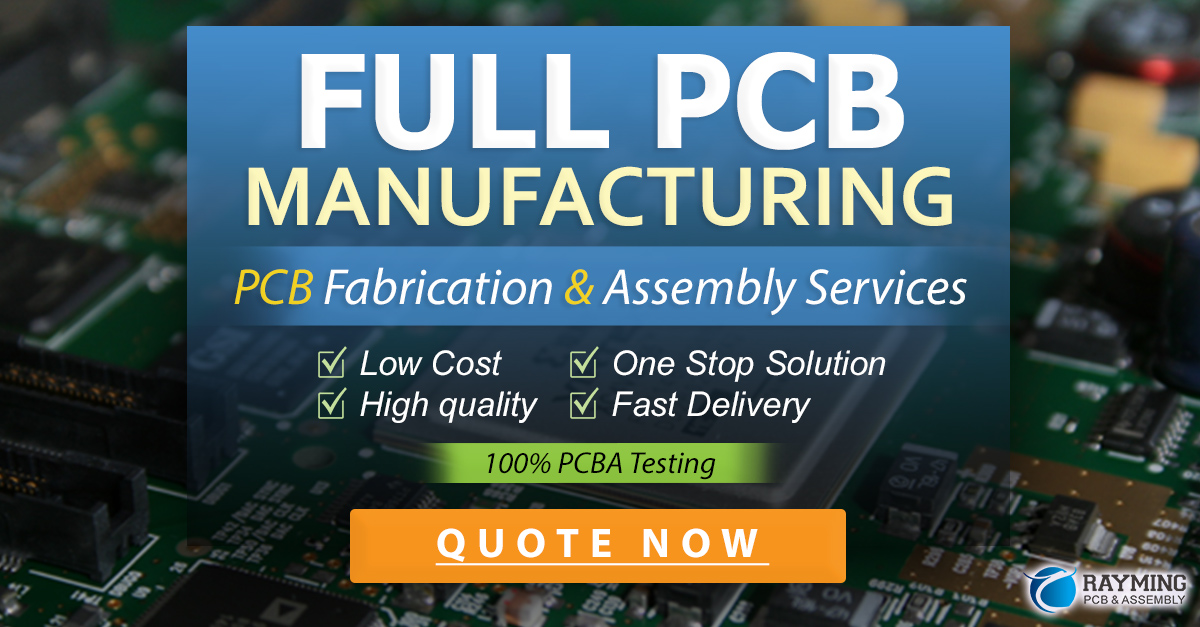
The Shift Towards Eco-Friendly Materials
As environmental concerns continue to grow, the PCB industry is shifting towards the use of eco-friendly materials. This includes the adoption of halogen-free and lead-free materials, as well as the use of biodegradable and recyclable substrates.
Eco-Friendly PCB Materials
- Halogen-free laminates: These materials reduce the environmental impact of PCBs by eliminating the release of harmful chemicals during disposal.
- Lead-free solders: Lead-free solders, such as tin-silver-copper (SAC) alloys, are becoming the standard in PCB assembly, minimizing the use of toxic lead.
- Biodegradable substrates: Researchers are exploring the use of biodegradable materials, such as paper and bioplastics, as PCB substrates to reduce electronic waste.
The Emergence of 3D Printing in PCB Fabrication
3D printing technology is making its way into the PCB industry, offering a new approach to PCB fabrication. This technology enables the creation of complex, three-dimensional PCB structures that are difficult or impossible to achieve with traditional manufacturing methods.
Advantages of 3D Printing in PCB Fabrication
- Rapid prototyping: 3D printing allows for the quick and cost-effective creation of PCB prototypes, reducing the time and resources required for product development.
- Customization: 3D printing enables the fabrication of PCBs with unique shapes and structures, tailored to specific applications.
- Reduced waste: 3D printing is an additive manufacturing process, which means that it only uses the material needed for the PCB, reducing waste compared to traditional subtractive manufacturing methods.
Frequently Asked Questions (FAQ)
-
Q: What are the main drivers behind the constant changes in the PCB industry?
A: The main drivers behind the constant changes in the PCB industry are the increasing demand for smaller, faster, and more efficient electronic devices, as well as the need for eco-friendly solutions and cost-effective manufacturing processes. -
Q: How do HDI PCBs differ from traditional PCBs?
A: HDI PCBs feature smaller vias, thinner traces, and reduced spacing between components compared to traditional PCBs. This allows for the creation of highly compact and efficient electronic devices with improved signal integrity and thermal management. -
Q: What are the benefits of using flexible and rigid-flex PCBs?
A: Flexible and rigid-flex PCBs offer improved reliability, space-saving design, and reduced assembly costs. They can conform to various shapes and sizes, making them ideal for applications that require flexibility and durability. -
Q: How do embedded components contribute to the development of smaller and more efficient electronic devices?
A: Embedded components, such as resistors, capacitors, and inductors, are integrated directly into the PCB substrate, reducing board size, improving signal integrity, and enhancing reliability by minimizing the number of solder joints. -
Q: What role does 3D printing play in the future of PCB fabrication?
A: 3D printing technology offers a new approach to PCB fabrication, enabling rapid prototyping, customization, and reduced waste. It allows for the creation of complex, three-dimensional PCB structures that are difficult or impossible to achieve with traditional manufacturing methods.
The PCB industry is constantly evolving, driven by the demand for smaller, faster, and more efficient electronic devices. The top PCB technology trends, such as HDI PCBs, flexible and rigid-flex PCBs, embedded components, eco-friendly materials, and 3D printing, are bringing about significant changes in the way PCBs are designed and manufactured. As these trends continue to shape the industry, we can expect to see even more innovative and sustainable solutions in the future.
Leave a Reply