Introduction to PCB Drilling
PCB (Printed Circuit Board) drilling is a crucial step in the PCB manufacturing process. It involves creating holes in the PCB to allow for the insertion of electronic components and the creation of vias for electrical connections between layers. Drilling is typically done using specialized machines called PCB drills or CNC (Computer Numerical Control) machines.
Types of PCB Drills
There are two main types of PCB drills:
-
Mechanical Drills: These drills use physical drill bits to create holes in the PCB. They are typically used for larger holes and are less precise than laser drills.
-
Laser Drills: These drills use high-powered lasers to create holes in the PCB. They are more precise than mechanical drills and can create smaller holes, but they are also more expensive.
PCB Drilling Process
The PCB drilling process typically involves the following steps:
-
Design: The first step is to design the PCB layout, including the placement of components and the location of holes and vias.
-
Drilling File Creation: Once the design is complete, a drilling file is created that specifies the location, size, and type of each hole to be drilled.
-
Drilling: The drilling file is loaded into the PCB drill or CNC machine, which then drills the holes according to the specifications in the file.
-
Deburring: After drilling, the holes may have rough edges or burrs that need to be removed. This is typically done using a deburring tool or by applying a chemical solution.
-
Cleaning: Finally, the PCB is cleaned to remove any debris or residue from the drilling process.
Drilling File Formats
There are several common drilling file formats used in PCB design:
Format | Description |
---|---|
Excellon | The most common format, uses ASCII text to specify drill locations and sizes |
Sieb & Meyer | Similar to Excellon, but uses a different format for specifying drill locations |
Gerber | A format used for specifying the overall PCB layout, including drill holes |
Types of PCB Drill Bits
There are several types of drill bits used in PCB drilling:
Carbide Drill Bits
Carbide drill bits are the most common type used in PCB drilling. They are made from a hard, wear-resistant material called tungsten carbide and can drill through a variety of materials, including fiberglass, copper, and aluminum.
High-Speed Steel (HSS) Drill Bits
HSS drill bits are made from a high-speed steel alloy and are less expensive than carbide bits. They are typically used for drilling softer materials like plastics and are not as durable as carbide bits.
Diamond-Coated Drill Bits
Diamond-coated drill bits have a layer of diamond particles on the cutting edges, which makes them very hard and wear-resistant. They are typically used for drilling hard materials like ceramics and glass-reinforced plastics.
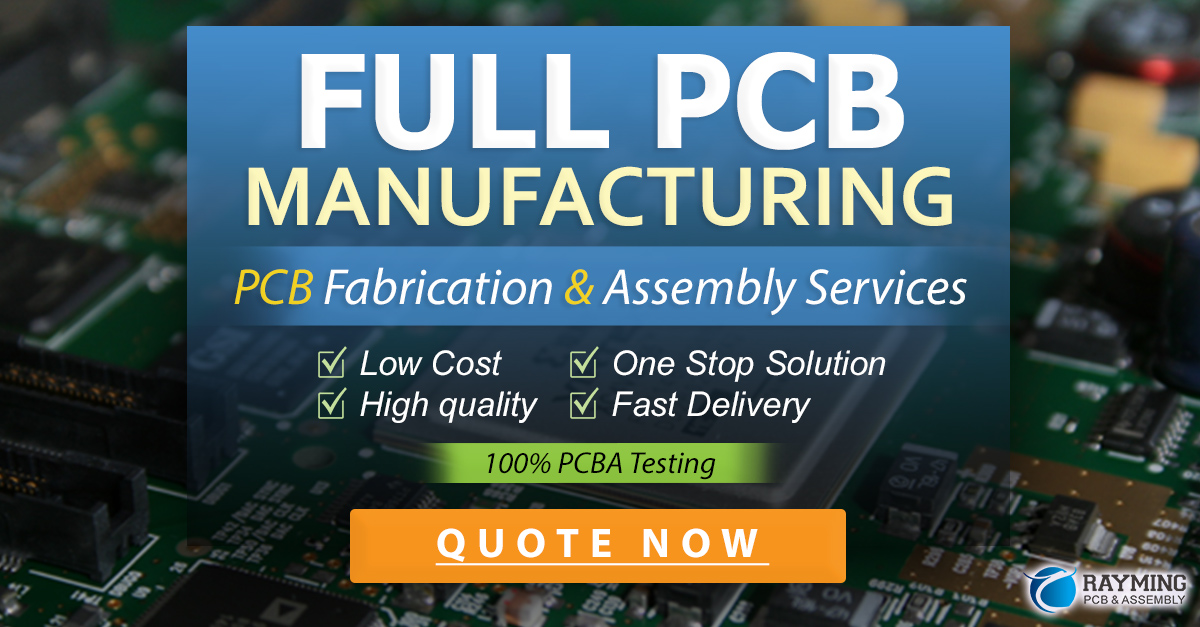
PCB Drilling Challenges
There are several challenges that can arise during the PCB drilling process:
Drill Wander
Drill wander occurs when the drill bit moves off course during drilling, resulting in misaligned or oversized holes. This can be caused by a variety of factors, including worn or damaged drill bits, incorrect feed rates, and improper drill alignment.
Drill Breakage
Drill breakage occurs when the drill bit breaks during drilling, often due to excessive wear or improper feed rates. This can cause damage to the PCB and may require rework or scrapping of the board.
Hole Wall Quality
The quality of the hole walls is important for ensuring proper electrical connections and preventing signal loss. Rough or uneven hole walls can be caused by worn or damaged drill bits, incorrect feed rates, or improper cleaning after drilling.
Best Practices for PCB Drilling
To ensure successful PCB drilling and minimize challenges, follow these best practices:
-
Use high-quality drill bits: Choose drill bits that are appropriate for the materials being drilled and replace them regularly to prevent wear and damage.
-
Use appropriate feed rates: Adjust the feed rate (the speed at which the drill bit moves through the material) based on the material being drilled and the size of the hole.
-
Regularly maintain and calibrate equipment: Regular maintenance and calibration of drilling equipment can help prevent issues like drill wander and breakage.
-
Use proper cleaning techniques: After drilling, use appropriate cleaning techniques to remove debris and ensure high-quality hole walls.
-
Follow manufacturer recommendations: Always follow the recommendations of the equipment and material manufacturers for best results.
FAQ
-
What is the most common type of drill bit used in PCB drilling?
Carbide drill bits are the most common type used in PCB drilling due to their hardness and wear resistance. -
What causes drill wander in PCB drilling?
Drill wander can be caused by worn or damaged drill bits, incorrect feed rates, and improper drill alignment. -
Why is hole wall quality important in PCB drilling?
The quality of the hole walls is important for ensuring proper electrical connections and preventing signal loss. -
How can I prevent drill breakage in PCB drilling?
To prevent drill breakage, use appropriate feed rates and replace drill bits regularly to prevent excessive wear. -
What are some best practices for successful PCB drilling?
Some best practices for successful PCB drilling include using high-quality drill bits, adjusting feed rates based on the material being drilled, regularly maintaining and calibrating equipment, using proper cleaning techniques, and following manufacturer recommendations.
Conclusion
PCB drilling is a critical step in the PCB manufacturing process that requires precision, skill, and attention to detail. By understanding the different types of drills and drill bits, the drilling process, and common challenges and best practices, PCB designers and manufacturers can ensure high-quality, reliable PCBs that meet the needs of their customers.
Leave a Reply