Introduction to Solder Paste Testing
Solder paste printing is a critical process in the manufacturing of printed circuit boards (PCBs). It involves the precise application of solder paste onto the PCB Pads, which will later be used to attach electronic components. The quality of the solder paste printing process directly impacts the reliability and functionality of the final product. Therefore, it is essential to test solder paste printing to ensure that it meets the required standards.
Why is Solder Paste Testing Important?
Solder paste testing is crucial for several reasons:
-
Ensures Consistent Quality: Regular testing helps maintain consistent quality of the solder paste printing process, reducing the risk of defects and failures in the final product.
-
Identifies Issues Early: Testing allows for early detection of any issues in the solder paste printing process, enabling timely corrective actions to be taken.
-
Reduces Costs: By identifying and addressing problems early, solder paste testing helps reduce the costs associated with rework, scrap, and customer returns.
-
Improves Reliability: Thorough testing ensures that the solder paste printing process is reliable, resulting in higher-quality PCBs and improved product performance.
Methods for Testing Solder Paste Printing
There are several methods used to test solder paste printing, each with its own advantages and limitations. The choice of method depends on factors such as the desired level of accuracy, speed, and cost. Some of the most common methods include:
1. Visual Inspection
Visual inspection is the most basic and widely used method for testing solder paste printing. It involves visually examining the printed solder paste under magnification to check for any defects or irregularities. This method is quick, simple, and cost-effective, making it suitable for high-volume production.
However, visual inspection has its limitations. It is subjective and relies on the operator’s experience and judgment, which can lead to inconsistencies. Additionally, it may not detect subtle defects that are not visible to the naked eye.
2. 2D Solder Paste Inspection (SPI)
2D SPI is an automated method that uses machine vision technology to inspect the solder paste printing process. It captures high-resolution images of the printed solder paste and analyzes them using advanced algorithms to detect defects and measure various parameters such as volume, height, and area.
Advantages of 2D SPI include:
- High-speed inspection: Can inspect thousands of pads per minute
- Objective and consistent: Eliminates human error and subjectivity
- Detailed analysis: Provides quantitative data on solder paste volume, height, and area
However, 2D SPI has limitations in detecting certain types of defects, such as bridging or insufficient solder paste in the z-axis (height).
3. 3D Solder Paste Inspection (SPI)
3D SPI is an advanced method that uses laser scanning or structured light technology to create a three-dimensional profile of the printed solder paste. This allows for a more comprehensive inspection, including the measurement of solder paste height and detection of defects in the z-axis.
Advantages of 3D SPI include:
- Comprehensive inspection: Detects defects in all three dimensions (x, y, and z)
- High accuracy: Provides precise measurements of solder paste volume, height, and area
- Improved process control: Enables better monitoring and optimization of the solder paste printing process
However, 3D SPI systems are generally more expensive than 2D systems and may require longer inspection times.
4. X-ray Inspection
X-ray inspection is a non-destructive method that uses X-rays to penetrate the solder paste and create images of the internal structure. This method is particularly useful for detecting defects that are not visible on the surface, such as voids or insufficient solder paste coverage.
Advantages of X-ray inspection include:
- Non-destructive: Does not damage the PCB or components
- Detects internal defects: Can identify voids, insufficient coverage, and other hidden defects
- Suitable for complex assemblies: Can inspect Multi-layer PCBs and dense component layouts
However, X-ray inspection systems are expensive and may require specialized training to operate effectively.
Solder Paste Testing Parameters
When testing solder paste printing, several key parameters are measured and analyzed to assess the quality of the process. These parameters include:
1. Volume
Solder paste volume refers to the amount of solder paste deposited on each PCB pad. It is typically measured in cubic millimeters (mm³) and is critical for ensuring a reliable solder joint. Insufficient solder paste volume can lead to weak or open connections, while excessive volume can cause bridging or short circuits.
Solder Paste Volume | Recommended Range |
---|---|
Small Pads | 0.2 – 0.5 mm³ |
Medium Pads | 0.5 – 1.0 mm³ |
Large Pads | 1.0 – 2.0 mm³ |
2. Height
Solder paste height refers to the thickness of the solder paste deposit on each pad. It is typically measured in micrometers (μm) and is important for ensuring proper component placement and reflow. Insufficient height can result in poor Wetting and weak solder joints, while excessive height can cause bridging or tombstoning.
Solder Paste Height | Recommended Range |
---|---|
Fine Pitch | 100 – 150 μm |
Standard Pitch | 150 – 200 μm |
Large Pitch | 200 – 250 μm |
3. Area
Solder paste area refers to the coverage of the solder paste on each pad. It is typically measured as a percentage of the pad area and is important for ensuring adequate wetting and strong solder joints. Insufficient area coverage can lead to weak or open connections, while excessive coverage can cause bridging or solder balling.
Solder Paste Area | Recommended Range |
---|---|
Fine Pitch | 60 – 80% |
Standard Pitch | 70 – 90% |
Large Pitch | 80 – 95% |
4. Alignment
Solder paste alignment refers to the position of the solder paste deposit relative to the PCB pad. It is typically measured in micrometers (μm) and is important for ensuring proper component placement and preventing defects such as bridging or tombstoning. Misaligned solder paste can cause component shifting or rotation during reflow.
Solder Paste Alignment | Recommended Tolerance |
---|---|
Fine Pitch | ± 25 μm |
Standard Pitch | ± 50 μm |
Large Pitch | ± 100 μm |
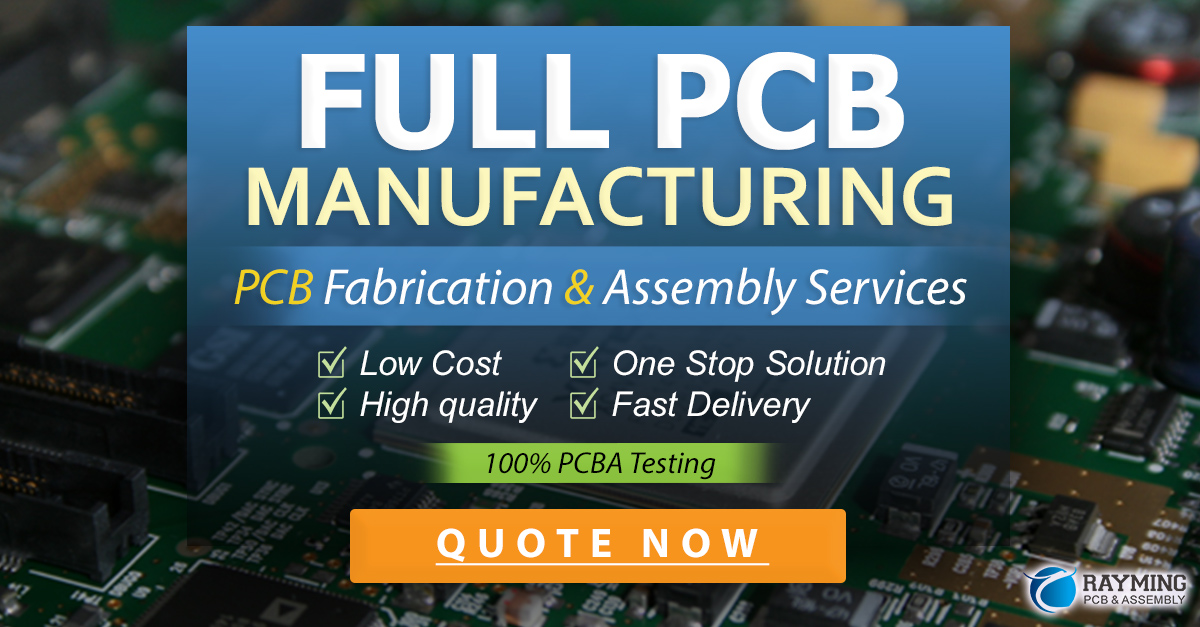
Solder Paste Testing Frequency
The frequency of solder paste testing depends on various factors, such as the complexity of the PCB, the production volume, and the quality requirements of the end product. In general, it is recommended to conduct solder paste testing at the following intervals:
-
Start of Production: Test the first few PCBs to ensure that the solder paste printing process is set up correctly and producing acceptable results.
-
Periodic Intervals: Test at regular intervals throughout the production run to monitor the consistency of the solder paste printing process. The frequency may vary from hourly to daily, depending on the production volume and process stability.
-
Changeovers: Test when changing solder paste, stencils, or other process parameters to ensure that the new setup is producing acceptable results.
-
Quality Issues: Test immediately if any quality issues are detected, such as an increase in defects or customer complaints, to identify and address the root cause.
Best Practices for Solder Paste Testing
To ensure the effectiveness and reliability of solder paste testing, follow these best practices:
-
Establish Acceptable Limits: Define clear and measurable acceptance criteria for each solder paste printing parameter, based on industry standards, customer requirements, and process capabilities.
-
Use Appropriate Equipment: Select testing equipment that is suitable for the desired level of accuracy, speed, and cost. Ensure that the equipment is properly calibrated and maintained.
-
Train Operators: Provide adequate training to operators involved in solder paste testing to ensure consistent and accurate results. Regularly assess their competence and provide refresher training as needed.
-
Document Results: Record and document all solder paste testing results, including the date, time, operator, equipment, and any corrective actions taken. Use this data for process analysis and continuous improvement.
-
Review and Optimize: Regularly review solder paste testing results and trends to identify opportunities for process optimization. Implement changes as needed to improve quality, efficiency, and cost-effectiveness.
Frequently Asked Questions (FAQ)
1. What is the most common method for testing solder paste printing?
The most common method for testing solder paste printing is visual inspection. This method is quick, simple, and cost-effective, making it suitable for high-volume production. However, it has limitations in terms of accuracy and consistency.
2. What are the advantages of 3D solder paste inspection (SPI)?
3D SPI provides a comprehensive inspection of the solder paste printing process, including the measurement of solder paste height and detection of defects in the z-axis. It offers high accuracy, improved process control, and the ability to detect defects that are not visible on the surface.
3. How often should solder paste testing be conducted?
The frequency of solder paste testing depends on various factors, such as the complexity of the PCB, the production volume, and the quality requirements of the end product. In general, it is recommended to conduct testing at the start of production, at periodic intervals throughout the production run, during changeovers, and when quality issues are detected.
4. What are the key parameters measured during solder paste testing?
The key parameters measured during solder paste testing include volume, height, area, and alignment. These parameters are critical for ensuring the quality and reliability of the solder joints and the overall PCB Assembly.
5. What are some best practices for solder paste testing?
Best practices for solder paste testing include establishing acceptable limits, using appropriate equipment, training operators, documenting results, and regularly reviewing and optimizing the process. By following these practices, manufacturers can ensure the effectiveness and reliability of their solder paste testing process.
Conclusion
Solder paste testing is a critical process in the manufacturing of printed circuit boards, ensuring the quality and reliability of the final product. There are various methods for testing solder paste printing, each with its own advantages and limitations. By understanding the key parameters, testing frequency, and best practices, manufacturers can effectively monitor and optimize their solder paste printing process, reducing defects, costs, and customer returns.
As the electronics industry continues to evolve, with increasing complexity and miniaturization of PCBs, the importance of solder paste testing will only grow. Manufacturers that invest in advanced testing technologies, such as 3D SPI and X-ray inspection, will be better positioned to meet the demanding quality requirements of their customers and stay competitive in the market.
Leave a Reply