Introduction to Flip chip Technology
Flip chip technology, also known as controlled collapse chip connection (C4), is a method for interconnecting semiconductor devices, such as integrated circuit (IC) chips and microelectromechanical systems (MEMS), to external circuitry with solder bumps that have been deposited onto the chip pads. The solder bumps are used to connect the chip to the external circuitry, and can provide both electrical and mechanical connections.
Flip chip technology was developed in the 1960s by IBM as an alternative to PCB.com/?p=6195″>Wire Bonding and tape automated bonding (TAB) in order to allow for a higher density of interconnects and improved electrical performance. In flip chip packaging, the IC chips are “flipped” over so that the active side faces down and can be connected directly to the external circuitry.
Advantages of Flip Chip Technology
Flip chip technology offers several advantages over traditional wire bonding and TAB techniques:
-
Higher interconnect density: Flip chip allows for a much higher density of interconnects compared to wire bonding, enabling smaller and more compact packages.
-
Improved electrical performance: The short interconnect lengths in flip chip packaging reduce inductance and resistance, leading to improved electrical performance, especially at high frequencies.
-
Better thermal management: Flip chip allows for better Heat Dissipation from the active side of the chip, which is directly connected to the substrate or heat spreader.
-
Enhanced reliability: Flip chip interconnects are less susceptible to mechanical stress and strain compared to wire bonds, resulting in improved reliability.
-
Lower manufacturing costs: Flip chip technology enables simpler and more automated manufacturing processes, leading to lower production costs for high-volume applications.
Applications of Flip Chip Technology
Flip chip technology is widely used in various applications, including:
- High-performance computing (HPC) and data centers
- Telecommunications and networking equipment
- Consumer electronics, such as smartphones, tablets, and wearables
- Automotive electronics, including infotainment systems and advanced driver assistance systems (ADAS)
- Medical devices and healthcare electronics
- Aerospace and defense systems
Flip Chip Resistors
Resistors are essential components in electronic circuits, used to control current flow, divide voltages, and provide impedance matching. In flip chip packaging, resistors can be integrated directly onto the chip or the substrate using various techniques, such as thin-film deposition or printed resistive materials.
Types of Flip Chip Resistors
There are several types of flip chip resistors, each with its own characteristics and manufacturing methods:
-
Thin-film resistors: These resistors are fabricated by depositing a thin layer of resistive material, such as nickel-chromium (NiCr) or tantalum nitride (TaN), onto the chip or substrate using physical vapor deposition (PVD) or chemical vapor deposition (CVD) techniques. Thin-film resistors offer high precision, low temperature coefficients, and good stability.
-
Thick-film resistors: Thick-film resistors are created by screen printing or stenciling a paste containing resistive materials, such as ruthenium oxide (RuO2) or bismuth ruthenate (Bi2Ru2O7), onto the substrate and firing it at high temperatures. Thick-film resistors are less precise than thin-film resistors but offer higher power handling capabilities and lower costs.
-
Printed resistors: Printed resistors are fabricated using additive manufacturing techniques, such as inkjet printing or aerosol jet printing, to deposit resistive materials directly onto the chip or substrate. Printed resistors enable the creation of complex geometries and can be integrated with other printed components, such as capacitors and inductors.
Flip Chip Resistor Performance Characteristics
The performance of flip chip resistors depends on several factors, including the resistive material, geometry, and manufacturing process. Some key performance characteristics include:
-
Resistance value: The nominal resistance value of the resistor, typically expressed in ohms (Ω).
-
Tolerance: The allowable variation in resistance value from the nominal value, usually expressed as a percentage (e.g., ±1%, ±5%).
-
Temperature coefficient of resistance (TCR): The change in resistance value with respect to temperature, expressed in parts per million per degree Celsius (ppm/°C). A low TCR indicates good stability over temperature variations.
-
Power rating: The maximum power that the resistor can dissipate without damage or performance degradation, expressed in watts (W).
-
Voltage rating: The maximum voltage that can be applied across the resistor without causing breakdown or insulation failure.
-
Noise: The unwanted electrical fluctuations generated by the resistor, which can affect circuit performance. Noise is often quantified by the noise index or noise voltage ratio.
-
Stability: The ability of the resistor to maintain its resistance value over time and under various environmental conditions, such as humidity, vibration, and shock.
Improving Flip Chip Resistor Performance
Researchers and engineers have been working on various strategies to improve the performance of flip chip resistors, addressing challenges such as precision, stability, and power handling. Some of the key approaches include:
Advanced Resistive Materials
One avenue for improving flip chip resistor performance is the development and adoption of advanced resistive materials with superior properties, such as:
-
High-temperature superconductors (HTS): HTS materials, such as yttrium barium copper oxide (YBCO) and bismuth strontium calcium copper oxide (BSCCO), offer extremely low resistance and high current carrying capabilities at cryogenic temperatures. While the need for cooling limits their practical applications, HTS resistors can be used in specialized high-performance systems.
-
Graphene: Graphene, a two-dimensional carbon nanomaterial, has been explored as a potential resistive material due to its high electrical conductivity, thermal stability, and mechanical strength. Graphene-based resistors have demonstrated good temperature stability and low noise, making them promising for high-frequency applications.
-
Conductive polymers: Intrinsically conductive polymers, such as polyaniline (PANI) and polypyrrole (PPy), have been investigated as alternatives to traditional resistive materials. These polymers offer the advantages of flexibility, low cost, and easy processing, although their stability and precision are generally lower than inorganic materials.
Optimized Geometries and Layouts
Another approach to improving flip chip resistor performance is through the optimization of resistor geometries and layouts. By carefully designing the shape, size, and placement of resistors on the chip or substrate, engineers can achieve better precision, higher power handling, and improved thermal management.
Some examples of optimized resistor geometries include:
-
Serpentine resistors: These resistors feature a winding, snake-like pattern that increases the effective length of the resistive element within a given area. Serpentine resistors offer higher resistance values and better power dissipation compared to straight resistors.
-
Interdigitated resistors: Interdigitated resistors consist of interlocking comb-like structures that increase the effective surface area and improve heat dissipation. This geometry is particularly useful for high-power applications.
-
Distributed resistor networks: By using multiple resistors connected in series, parallel, or a combination of both, designers can achieve more precise resistance values and better current handling capabilities. Distributed resistor networks also help to minimize the impact of local defects or variations in the resistive material.
Enhanced Manufacturing Processes
Improvements in manufacturing processes can also contribute to better flip chip resistor performance. Some key areas of focus include:
-
Precision deposition techniques: Advances in thin-film deposition methods, such as atomic layer deposition (ALD) and pulsed laser deposition (PLD), enable the creation of ultra-thin and highly uniform resistive layers with tight tolerances.
-
Laser trimming: Laser trimming is a post-processing technique used to adjust the resistance value of flip chip resistors by selectively removing portions of the resistive material. By using high-precision laser systems and optimized trimming patterns, manufacturers can achieve very tight tolerances (e.g., ±0.1%) and improve the overall accuracy of the resistors.
-
Improved packaging and encapsulation: The packaging and encapsulation of flip chip resistors play a crucial role in their performance and reliability. By using advanced materials, such as low-stress epoxies and high-temperature polymers, and optimizing the packaging design, engineers can minimize the impact of mechanical stress, moisture, and other environmental factors on resistor performance.
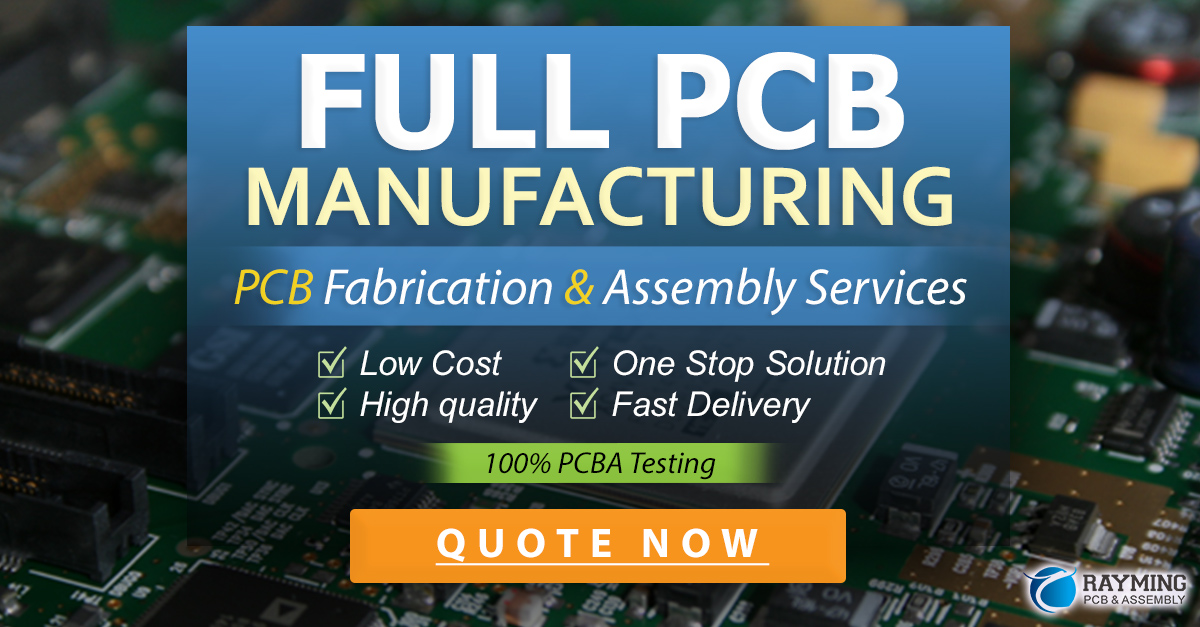
Case Studies and Research Examples
Several research groups and companies have reported significant improvements in flip chip resistor performance through the application of the aforementioned strategies. Some notable examples include:
-
Panasonic’s high-precision flip chip resistors: Panasonic developed a line of high-precision flip chip resistors using a proprietary thin-film process and optimized resistor geometries. These resistors achieved a tolerance of ±0.1%, a TCR of ±25 ppm/°C, and a power rating of up to 1 W in a compact 0603 package.
-
IBM’s graphene-based resistors: Researchers at IBM demonstrated graphene-based flip chip resistors with a TCR of less than 1 ppm/°C and a noise index of -40 dB. These resistors showed excellent stability and low noise, making them suitable for high-frequency analog circuits and precision instrumentation.
-
University of California, Berkeley’s 3D printed resistors: A team at UC Berkeley developed a novel 3D printing process for fabricating high-performance flip chip resistors. By using a conductive polymer composite and a multi-material 3D printer, they created resistors with a tolerance of ±5%, a TCR of ±100 ppm/°C, and a power rating of up to 0.5 W. This approach enables the rapid prototyping and customization of flip chip resistors for various applications.
Frequently Asked Questions (FAQ)
-
Q: What is the main advantage of using flip chip resistors compared to discrete surface-mount resistors?
A: Flip chip resistors offer several advantages, including smaller size, better thermal management, and improved high-frequency performance due to reduced parasitic inductance and capacitance. -
Q: Can flip chip resistors be used in high-power applications?
A: Yes, flip chip resistors can be designed for high-power applications by using optimized geometries, such as serpentine or interdigitated patterns, and advanced resistive materials with high thermal stability and power handling capabilities. -
Q: How do thin-film and thick-film flip chip resistors differ in terms of performance?
A: Thin-film flip chip resistors generally offer higher precision, lower TCR, and better stability compared to thick-film resistors. However, thick-film resistors typically have higher power handling capabilities and lower manufacturing costs. -
Q: Are flip chip resistors more expensive than traditional surface-mount resistors?
A: The cost of flip chip resistors depends on factors such as the resistive material, manufacturing process, and volume. While they may have higher initial costs compared to surface-mount resistors, flip chip resistors can offer cost savings in terms of board space, assembly, and overall system performance. -
Q: What are some of the emerging materials being explored for flip chip resistors?
A: Researchers are investigating various advanced materials for flip chip resistors, including high-temperature superconductors (HTS), graphene, and conductive polymers. These materials offer unique properties, such as extremely low resistance, high thermal stability, and flexibility, which can enable new applications and improved performance.
Conclusion
Flip chip resistors are essential components in modern electronic systems, offering advantages such as compact size, improved electrical performance, and better thermal management compared to traditional surface-mount resistors. As the demand for higher performance, precision, and reliability continues to grow, researchers and engineers are developing innovative strategies to improve flip chip resistor performance.
These strategies include the adoption of advanced resistive materials, optimization of resistor geometries and layouts, and enhancements in manufacturing processes. By leveraging these approaches, manufacturers can create flip chip resistors with tighter tolerances, lower temperature coefficients, higher power handling capabilities, and improved stability.
As new materials, technologies, and applications emerge, the field of flip chip resistors will continue to evolve, driving further advancements in electronic systems across various industries, from consumer electronics and telecommunications to aerospace and healthcare.
Leave a Reply