Introduction to Flex PCB Prototyping
Flexible printed circuit boards (Flex PCBs) have revolutionized the electronics industry by offering a versatile and reliable solution for designing and manufacturing compact, lightweight, and durable electronic devices. Flex PCB prototyping is an essential step in the development process, allowing engineers and designers to test and refine their designs before mass production. In this article, we will explore the world of flexible PCB Prototype manufacturing services, discussing the advantages, processes, and key considerations involved in creating high-quality flex PCB Prototypes.
What are Flexible PCBs?
Flexible PCBs, also known as flex circuits, are printed circuit boards made from flexible materials, such as polyimide or polyester. These materials allow the PCB to bend, twist, and fold without damaging the electrical components or connections. Flex PCBs are commonly used in applications that require compact, lightweight, and durable electronic assemblies, such as:
- Wearable devices
- Medical equipment
- Aerospace and defense systems
- Automotive electronics
- Consumer electronics
Advantages of Flex PCBs
Compared to traditional rigid PCBs, flex PCBs offer several advantages:
-
Flexibility and durability: Flex PCBs can withstand repeated bending and flexing without cracking or breaking, making them ideal for applications that require movement or are subjected to vibration and shock.
-
Reduced weight and size: By eliminating the need for bulky connectors and wires, flex PCBs enable the design of more compact and lightweight electronic devices.
-
Improved signal integrity: The shorter signal paths and reduced parasitic capacitance and inductance in flex PCBs result in improved signal integrity and higher-frequency performance.
-
Enhanced thermal management: Flex PCBs can be designed with built-in thermal management features, such as heat sinks and thermal vias, to dissipate heat more efficiently.
-
Cost-effective: In many cases, using flex PCBs can reduce the overall cost of an electronic assembly by simplifying the design, reducing the number of components, and streamlining the manufacturing process.
Flex PCB Prototyping Process
The flex PCB prototyping process involves several key steps to ensure the design is functional, reliable, and ready for mass production. These steps include:
1. Design and Layout
The first step in flex PCB prototyping is to create a detailed design and layout using specialized PCB design software. The design should take into account the specific requirements of the application, such as the desired flexibility, component placement, and signal integrity. Key considerations during the design phase include:
- Choosing the appropriate flexible substrate material
- Determining the number of layers and their arrangement
- Placing components and routing traces to optimize signal integrity and minimize electromagnetic interference (EMI)
- Incorporating any necessary shielding or grounding features
2. Material Selection
Selecting the right materials for your flex PCB prototype is crucial for ensuring its performance and reliability. The most common flexible substrate materials are:
- Polyimide (PI): A high-temperature, chemically resistant material with excellent mechanical and electrical properties.
- Polyester (PET): A lower-cost alternative to polyimide, suitable for less demanding applications.
Other materials to consider include the copper foil thickness, adhesives, and coverlay materials. Your flex PCB prototype manufacturing service provider can help you select the most appropriate materials based on your application’s requirements.
3. Fabrication
Once the design is finalized and the materials are selected, the flex PCB prototype is fabricated using specialized equipment and processes. The fabrication process typically includes:
- Printing the circuit pattern onto the flexible substrate using a photolithographic process
- Etching away the unwanted copper to create the desired traces and pads
- Laminating the layers together using adhesives and heat and pressure
- Drilling any necessary holes and vias
- Applying solder mask and silkscreen for protection and labeling
4. Assembly
After the flex PCB prototype is fabricated, the electronic components are assembled onto the board using various techniques, such as:
- Surface mount technology (SMT): Components are placed and soldered onto the surface of the PCB using automated pick-and-place machines and reflow ovens.
- Through-hole technology (THT): Components with leads are inserted through holes in the PCB and soldered in place.
- Chip-on-flex (COF): Bare die components are directly mounted onto the flexible substrate using adhesives and wire bonding.
5. Testing and Validation
Before the flex PCB prototype is considered complete, it must undergo rigorous testing and validation to ensure it meets the design specifications and performs as intended. Common testing methods include:
- Continuity testing: Verifying that all connections are intact and there are no short circuits or open circuits.
- Functional testing: Checking that the assembled PCB performs the desired functions and meets the performance requirements.
- Environmental testing: Subjecting the prototype to various environmental conditions, such as temperature, humidity, and vibration, to assess its durability and reliability.
6. Iteration and Refinement
Based on the results of the testing and validation phase, the flex PCB prototype design may need to be refined or optimized. This iterative process helps identify and address any issues or weaknesses in the design before proceeding to mass production. Collaboration between the design team and the flex PCB prototype manufacturing service provider is essential for efficiently iterating and refining the design.
Choosing a Flex PCB Prototype Manufacturing Service
When selecting a flex PCB prototype manufacturing service, there are several key factors to consider to ensure you receive high-quality prototypes that meet your requirements. These factors include:
1. Experience and Expertise
Look for a manufacturer with extensive experience in producing flex PCB prototypes for a variety of applications. They should have a deep understanding of the unique challenges and requirements associated with designing and fabricating flexible circuits. Additionally, they should be able to provide expert guidance and support throughout the prototyping process.
2. Technical Capabilities
Ensure that the manufacturer has the necessary equipment, processes, and expertise to handle your specific flex PCB prototype requirements. This includes:
- Ability to work with a wide range of flexible substrate materials
- High-precision fabrication capabilities, such as fine-pitch traces and small via sizes
- Advanced assembly techniques, such as chip-on-flex and micro-welding
- Comprehensive testing and validation services
3. Quality Control and Certifications
A reputable flex PCB prototype manufacturing service should have robust quality control processes in place to ensure consistent, high-quality results. Look for manufacturers with relevant certifications, such as:
- ISO 9001: Quality management systems
- IPC-6013: Qualification and performance specification for flexible printed boards
- UL 94: Standard for safety of flammability of plastic materials
4. Turnaround Time and Cost
Flex PCB prototyping often operates on tight deadlines, so it’s essential to choose a manufacturer that can deliver high-quality prototypes quickly and efficiently. Look for a provider with fast turnaround times and transparent pricing. Keep in mind that while cost is an important consideration, the lowest price may not always result in the best value, especially if it compromises quality or reliability.
5. Communication and Support
Effective communication and support are crucial for a successful flex PCB prototyping project. Choose a manufacturer that is responsive, communicative, and willing to work closely with your team to understand your requirements and provide regular updates on the project’s progress. They should also offer comprehensive technical support and be available to address any issues or concerns that may arise during the prototyping process.
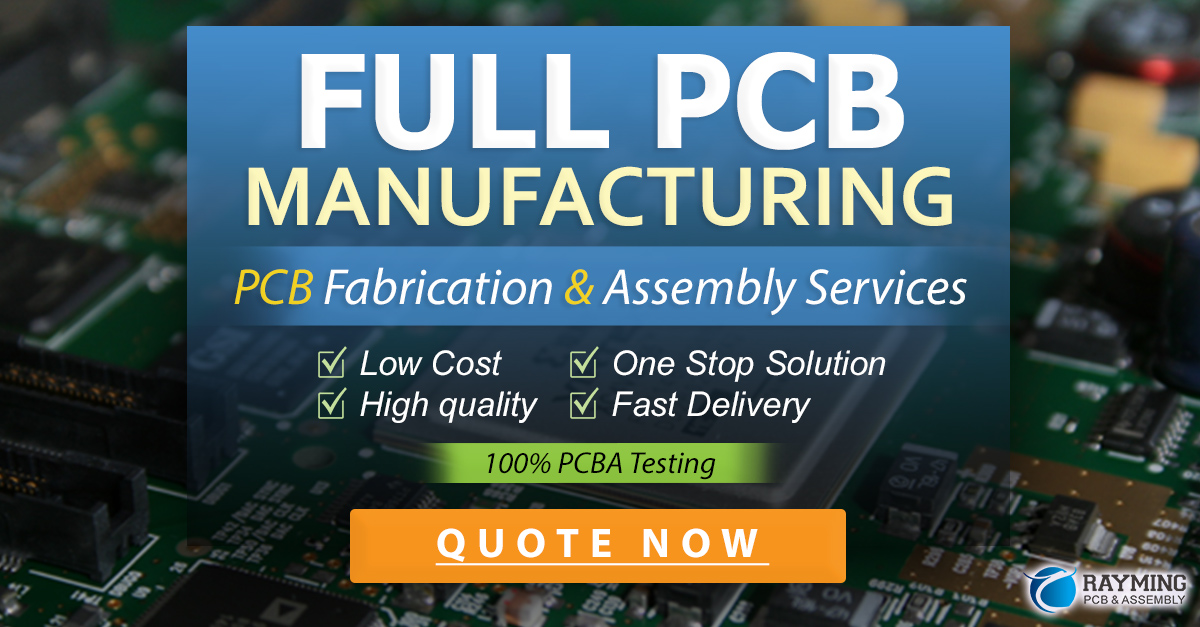
Flex PCB Prototyping Design Considerations
To ensure a successful flex PCB prototyping project, designers must take into account several key considerations specific to flexible circuits. These include:
1. Bend Radius and Flexibility Requirements
One of the most critical aspects of flex PCB design is determining the required bend radius and flexibility. The bend radius is the minimum radius that the PCB can be bent without damaging the traces or components. It is influenced by factors such as the substrate material, copper thickness, and the size and location of components. Designers must carefully consider the intended application and the expected range of motion to specify the appropriate bend radius and flexibility requirements.
2. Trace Width and Spacing
Flex PCBs often require finer trace widths and spacing compared to rigid PCBs to maintain flexibility and minimize stress on the traces during bending. However, narrower traces can also increase resistance and limit current-carrying capacity. Designers must strike a balance between trace width, spacing, and electrical performance based on the specific requirements of the application.
3. Stiffener Placement
In some cases, it may be necessary to add stiffeners to certain areas of the flex PCB to provide support for components or connectors. Stiffeners are typically made from rigid materials, such as FR-4 or polyimide, and are laminated to the flexible substrate. Designers must carefully consider the placement and size of stiffeners to ensure they do not interfere with the desired flexibility of the PCB.
4. Strain Relief
Strain relief features are essential for protecting the flex PCB and its components from stress and damage caused by repeated bending or flexing. Common strain relief techniques include:
- Incorporating service loops or meanders in the traces to allow for expansion and contraction during bending
- Using flexible adhesives or encapsulants to support and protect components
- Adding reinforced areas or strain relief cut-outs in the substrate material
5. Shielding and Grounding
Flex PCBs are often used in applications that are sensitive to electromagnetic interference (EMI) or require a high degree of signal integrity. In these cases, designers must incorporate appropriate shielding and grounding features into the flex PCB design. This may include:
- Adding conductive layers or traces to provide shielding against EMI
- Using ground planes or grids to improve signal integrity and reduce crosstalk
- Incorporating shield termination features, such as vias or conductive adhesives, to ensure proper grounding
Flex PCB Prototype Manufacturing Processes
There are several key manufacturing processes involved in producing high-quality flex PCB prototypes. These processes must be carefully controlled and optimized to ensure the desired performance, reliability, and durability of the final product.
1. Imaging and Etching
The first step in flex PCB fabrication is to transfer the circuit pattern onto the flexible substrate using a photolithographic process. This involves:
- Applying a photosensitive resist to the copper-clad substrate
- Exposing the resist to UV light through a photomask containing the circuit pattern
- Developing the resist to remove the unexposed areas
- Etching away the unwanted copper using a chemical solution
- Stripping the remaining resist to reveal the final circuit pattern
Advances in imaging and etching processes, such as direct imaging and plasma etching, have enabled the production of finer traces and more complex circuit patterns on flex PCBs.
2. Lamination
After the circuit pattern is etched, the flexible layers are laminated together using a combination of heat, pressure, and adhesives. The lamination process typically involves:
- Aligning the layers in the proper sequence and orientation
- Applying adhesive between the layers
- Placing the stack-up in a lamination press
- Applying heat and pressure for a specified duration to bond the layers together
Lamination parameters, such as temperature, pressure, and time, must be carefully controlled to ensure proper bonding and to avoid damaging the circuits or components.
3. Drilling and Routing
Once the layers are laminated, any necessary holes and vias are drilled through the flex PCB using mechanical drilling or laser drilling processes. The holes are then cleaned and plated with copper to provide electrical connectivity between layers.
Routing is the process of cutting the flex PCB to its final shape and size. This is typically done using a computer-controlled routing machine or Laser Cutter. The routing process must be carefully controlled to avoid damaging the circuits or components and to ensure the desired flexibility of the final product.
4. Solder Mask and Silkscreen
A solder mask is a protective coating applied to the flex PCB to prevent solder bridging and to protect the copper traces from oxidation and damage. The solder mask is typically applied using a screen printing or photoimaging process and then cured using UV light or heat.
Silkscreen is a process used to add text, logos, or other markings to the flex PCB for identification and assembly purposes. The silkscreen ink is applied using a screen printing process and then cured using UV light or heat.
5. Surface Finishing
The final step in flex PCB fabrication is to apply a surface finish to the exposed copper areas to prevent oxidation and to facilitate soldering. Common surface finishes for flex PCBs include:
- Hot air solder leveling (HASL): A thin layer of solder is applied to the copper surfaces using a hot air leveling machine.
- Electroless nickel immersion gold (ENIG): A layer of nickel is deposited onto the copper surfaces, followed by a thin layer of gold to protect the nickel from oxidation.
- Immersion silver: A thin layer of silver is deposited onto the copper surfaces through a chemical immersion process.
The choice of surface finish depends on the specific requirements of the application, such as the desired solderability, durability, and cost.
Flex PCB Prototype Testing and Validation
To ensure the quality, reliability, and functionality of flex PCB prototypes, a comprehensive testing and validation process is essential. This process typically involves several key steps:
1. Visual Inspection
The first step in testing and validation is to perform a thorough visual inspection of the flex PCB prototype. This includes checking for any obvious defects or damage, such as:
- Cracks, tears, or delamination in the flexible substrate
- Broken or damaged traces or pads
- Misaligned or missing components
- Solder bridging or poor solder joints
- Incorrect labeling or markings
Any identified defects should be documented and addressed before proceeding with further testing.
2. Electrical Testing
Electrical testing is performed to verify the continuity, insulation resistance, and electrical performance of the flex PCB prototype. Common electrical tests include:
- Continuity testing: Verifying that all intended connections are intact and have acceptably low resistance.
- Insulation resistance testing: Measuring the resistance between adjacent traces or layers to ensure adequate insulation.
- Impedance testing: Measuring the impedance of traces and ensuring they meet the desired specifications for signal integrity.
- Functional testing: Verifying that the flex PCB performs the intended functions and meets the required performance specifications.
Electrical testing may be performed using automated test equipment (ATE) or manual test methods, depending on the complexity and volume of the prototypes.
3. Mechanical Testing
Mechanical testing is essential for evaluating the flexibility, durability, and reliability of flex PCB prototypes under various stress conditions. Common mechanical tests include:
- Bend testing: Subjecting the flex PCB to repeated bending cycles to assess its ability to withstand the intended range of motion without damage.
- Twist testing: Applying torsional stress to the flex PCB to evaluate its resistance to twisting and warping.
- Tear testing: Measuring the force required to tear the flexible substrate and assessing its tear resistance.
- Peel testing: Evaluating the adhesion strength between layers of the flex PCB by measuring the force required to peel them apart.
Mechanical testing helps identify any weaknesses or vulnerabilities in the flex PCB design that could lead to premature failure or reduced reliability.
4. Environmental Testing
Flex PCBs are often used in applications that expose them to various environmental stresses, such as temperature extremes, humidity, and vibration. Environmental testing is performed to assess the flex PCB’s ability to withstand these stresses and maintain its performance and reliability. Common environmental tests include:
- Temperature cycling: Subjecting the flex PCB to alternating high and low-temperature extremes to evaluate its ability to withstand thermal stress.
- Humidity testing: Exposing the flex PCB to high humidity levels to assess its resistance to moisture absorption and corrosion.
- Vibration testing: Subjecting the flex PCB to various vibration frequencies and amplitudes to evaluate its resistance to mechanical stress and fatigue.
- Thermal shock testing: Exposing the flex PCB to rapid temperature changes to assess its ability to withstand thermal expansion and contraction.
Environmental testing helps ensure that the flex PCB prototype can withstand the intended operating conditions and maintain its performance and reliability over its expected lifetime.
5. Accelerated Life Testing
Accelerated life testing (ALT) is a method used to predict the long-term reliability and durability of flex PCB prototypes by subjecting them to elevated stress levels for a shorter duration. By applying higher-than-normal stress levels, such as increased temperature, humidity, or vibration, ALT can simulate the effects of long-term use in a compressed time frame.
ALT helps identify potential failure modes and mechanisms that may not be apparent during normal testing, allowing designers to make necessary improvements to enhance the flex PCB’s reliability and durability.
Flex PCB Prototype Manufacturing Case Studies
To illustrate the benefits and challenges of flex PCB prototype manufacturing, let’s explore some real-world case studies:
Case Study 1: Wearable Medical Device
A medical device company was developing a new wearable sensor for continuous patient monitoring. The device required a compact, lightweight, and flexible design to ensure patient comfort and ease of use. The company partnered with a flex PCB prototype manufacturing service to develop a custom flex PCB solution.
The key challenges included:
- Achieving a high degree of flexibility and durability to withstand repeated bending and stretching
- Incorporating multiple sensor types and wireless connectivity in a small form factor
- Ensuring biocompatibility and safety for long-term skin contact
The flex PCB prototype manufacturing service worked closely
Leave a Reply