Understanding Flex PCB Materials
The choice of materials for a flex PCB is critical, as they directly impact the board’s electrical, mechanical, and thermal properties. Some of the most commonly used materials in flex PCB manufacturing include:
Polyimide (PI)
Polyimide is the most widely used substrate material for flex PCBs due to its excellent thermal stability, chemical resistance, and mechanical strength. It can withstand high temperatures up to 300°C, making it suitable for various applications, including aerospace, automotive, and medical devices.
Polyethylene Terephthalate (PET)
PET is a cost-effective alternative to polyimide for less demanding applications. It offers good electrical properties and flexibility but has a lower temperature resistance compared to polyimide.
Liquid Crystal Polymer (LCP)
LCP is a high-performance material known for its low dielectric constant, low moisture absorption, and excellent high-frequency performance. It is commonly used in RF and microwave applications.
Adhesives
Adhesives are used to bond the copper layers to the substrate material. The most common adhesives used in flex PCBs are acrylic and epoxy-based. The choice of adhesive depends on the specific requirements of the application, such as temperature resistance, flexibility, and chemical resistance.
Flex PCB Layer Stackup
The layer stackup of a flex PCB refers to the arrangement of conductive and dielectric layers that make up the board. The number of layers and their configuration can vary depending on the complexity and requirements of the application. Let’s explore some common Flex PCB Stackups:
Single-Layer Flex PCB
A single-layer flex PCB consists of a single conductive layer (usually copper) bonded to a flexible substrate. This simple construction is suitable for low-complexity designs and is often used in applications that require minimal wiring, such as LED lighting strips or simple sensors.
Layer | Material | Thickness |
---|---|---|
Cover Layer | Polyimide | 25 µm |
Copper Layer | Copper | 18 µm |
Base Layer | Polyimide | 25 µm |
Double-Layer Flex PCB
A double-layer flex PCB has two conductive layers separated by a flexible dielectric substrate. This configuration allows for more complex routing and interconnections compared to a single-layer design. Double-layer flex PCBs are commonly used in applications such as displays, cameras, and wearable devices.
Layer | Material | Thickness |
---|---|---|
Cover Layer | Polyimide | 25 µm |
Top Copper Layer | Copper | 18 µm |
Dielectric Layer | Polyimide | 50 µm |
Bottom Copper Layer | Copper | 18 µm |
Base Layer | Polyimide | 25 µm |
Multi-Layer Flex PCB
Multi-layer flex PCBs consist of three or more conductive layers separated by flexible dielectric substrates. This stackup offers the highest level of design complexity and allows for dense routing and interconnections. Multi-layer flex PCBs are used in advanced applications, such as aerospace, military, and high-end consumer electronics.
Layer | Material | Thickness |
---|---|---|
Cover Layer | Polyimide | 25 µm |
Top Copper Layer | Copper | 18 µm |
Dielectric Layer 1 | Polyimide | 50 µm |
Inner Copper Layer 1 | Copper | 18 µm |
Dielectric Layer 2 | Polyimide | 50 µm |
Inner Copper Layer 2 | Copper | 18 µm |
Dielectric Layer 3 | Polyimide | 50 µm |
Bottom Copper Layer | Copper | 18 µm |
Base Layer | Polyimide | 25 µm |
Rigid-Flex PCB
A rigid-flex PCB combines both rigid and flexible sections in a single board. The rigid sections provide mechanical support and allow for the mounting of components, while the flexible sections enable the board to bend and fold as required. Rigid-flex PCBs offer the advantages of both rigid and flex PCBs, making them suitable for applications that require complex 3D packaging and reliable interconnections between rigid sections.
Layer | Material | Thickness |
---|---|---|
Cover Layer (Flex) | Polyimide | 25 µm |
Top Copper Layer (Flex) | Copper | 18 µm |
Dielectric Layer (Flex) | Polyimide | 50 µm |
Bottom Copper Layer (Flex) | Copper | 18 µm |
Adhesive Layer | Acrylic | 50 µm |
Rigid Layer 1 | FR-4 | 100 µm |
Copper Layer (Rigid) | Copper | 35 µm |
Dielectric Layer (Rigid) | FR-4 | 200 µm |
Copper Layer (Rigid) | Copper | 35 µm |
Rigid Layer 2 | FR-4 | 100 µm |
Design Considerations for Flex PCB Stackup
When designing a flex PCB stackup, several factors must be considered to ensure optimal performance and manufacturability:
-
Bend Radius: The minimum bend radius of a flex PCB is determined by the thickness and material properties of the substrate and copper layers. It is essential to ensure that the bend radius is within the allowable range to prevent damage to the board during flexing.
-
Copper Thickness: The thickness of the copper layers affects the electrical performance and mechanical stability of the flex PCB. Thinner copper layers (18 µm or less) are generally preferred for increased flexibility, while thicker layers (35 µm or more) offer better current carrying capacity and mechanical strength.
-
Adhesive Selection: The choice of adhesive should take into account the operating temperature range, chemical resistance, and flexibility requirements of the application. Acrylic adhesives are commonly used for their good flexibility and ease of processing, while epoxy adhesives offer better temperature and chemical resistance.
-
Coverlay and Stiffener: Coverlay is an insulating layer applied over the outer copper layers to protect the circuitry and provide electrical insulation. Stiffeners are used to reinforce specific areas of the flex PCB, such as connector locations or component mounting areas, to improve mechanical stability.
-
Shielding: In applications sensitive to electromagnetic interference (EMI), shielding layers may be incorporated into the flex PCB stackup. These layers, typically made of copper or conductive materials, help to reduce EMI and improve signal integrity.
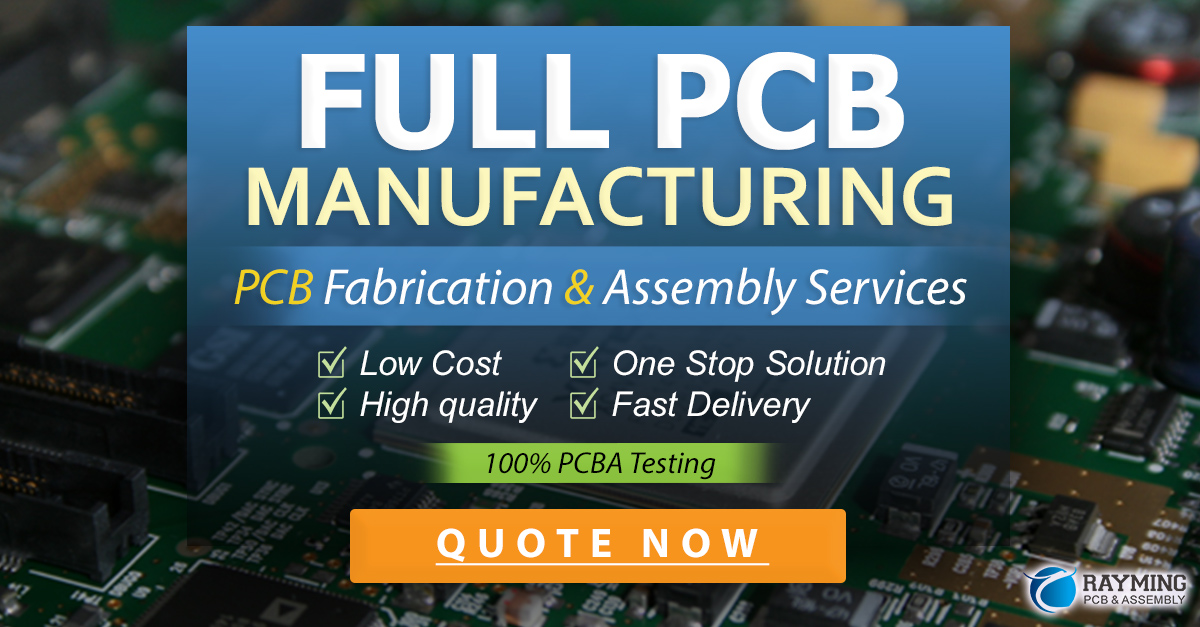
Frequently Asked Questions (FAQ)
-
What is the difference between a flex PCB and a rigid PCB?
A flex PCB is made of flexible materials, such as polyimide, that allow the board to bend and conform to various shapes. In contrast, a rigid PCB is made of a rigid substrate material, typically FR-4, and cannot be bent or flexed. -
Can flex PCBs be used in high-temperature applications?
Yes, flex PCBs made with polyimide substrates can withstand high temperatures up to 300°C, making them suitable for various high-temperature applications, such as aerospace and automotive electronics. -
What are the advantages of using a rigid-flex PCB?
Rigid-flex PCBs combine the benefits of both rigid and flexible PCBs in a single board. They offer improved mechanical stability, reduced assembly costs, and enhanced reliability by eliminating the need for connectors between rigid and flexible sections. -
How does the copper thickness affect the flexibility of a flex PCB?
Thinner copper layers (18 µm or less) are generally preferred for increased flexibility, as they allow the board to bend more easily without causing damage to the copper traces. Thicker copper layers (35 µm or more) offer better current carrying capacity and mechanical strength but may reduce the overall flexibility of the board. -
What is the purpose of a coverlay in a flex PCB?
A coverlay is an insulating layer applied over the outer copper layers of a flex PCB. Its primary purpose is to protect the circuitry from damage and provide electrical insulation. Coverlays also help to improve the durability and reliability of the flex PCB by protecting the copper traces from environmental factors, such as moisture and abrasion.
Conclusion
Flex PCB material selection and layer stackup are critical aspects of designing and manufacturing reliable and high-performance flexible electronic assemblies. By understanding the properties of various substrate materials, adhesives, and layer configurations, designers can create flex PCBs that meet the specific requirements of their applications. Careful consideration of factors such as bend radius, copper thickness, and shielding ensures that the flex PCB will perform optimally in its intended environment. As technology advances and the demand for compact, lightweight, and flexible electronics grows, the importance of optimizing flex PCB stackups will only continue to increase.
Leave a Reply