What is Electronics Environmental Testing?
Electronics environmental testing is a series of tests performed on electronic devices and components to evaluate their ability to function properly and reliably under different environmental conditions. These tests are designed to simulate real-world conditions that the electronics may encounter during their lifecycle, from manufacturing to end-use.
The primary goal of electronics environmental testing is to identify potential issues or failures that may occur due to exposure to various environmental factors. By detecting these issues early in the development process, manufacturers can make necessary modifications to improve the product’s durability and reliability.
Categories of Electronics Environmental Testing
Electronics environmental testing can be broadly categorized into two main types:
-
Climatic Testing: This category focuses on testing the effects of temperature, humidity, and other climatic conditions on electronic devices and components.
-
Dynamic Testing: This category involves testing the effects of mechanical stress, such as vibration and shock, on electronic devices and components.
Climatic Testing
Climatic testing evaluates the performance of electronic devices and components under various temperature and humidity conditions. Some common climatic tests include:
Temperature Testing
Temperature testing assesses the ability of electronic devices and components to function properly under different temperature conditions. This test can be further divided into two sub-categories:
-
High-Temperature Testing: This test evaluates the performance of electronics at elevated temperatures, typically ranging from 40°C to 85°C or higher, depending on the application.
-
Low-Temperature Testing: This test assesses the performance of electronics at low temperatures, typically ranging from -40°C to 0°C or lower, depending on the application.
Humidity Testing
Humidity testing evaluates the ability of electronic devices and components to function properly under different humidity levels. This test is often combined with temperature testing to create a more realistic environment. Common humidity tests include:
-
Steady-State Humidity Testing: This test exposes electronics to a constant humidity level for an extended period to assess their resistance to moisture.
-
Cyclic Humidity Testing: This test subjects electronics to alternating high and low humidity levels to evaluate their ability to withstand moisture-related stress.
Thermal Shock Testing
Thermal shock testing evaluates the ability of electronic devices and components to withstand rapid changes in temperature. This test involves exposing the electronics to alternating high and low-temperature extremes within a short period.
Salt Fog Testing
Salt fog testing assesses the resistance of electronic devices and components to corrosion caused by exposure to salt-laden atmospheres. This test is particularly relevant for electronics used in coastal or marine environments.
Dynamic Testing
Dynamic testing evaluates the performance of electronic devices and components under mechanical stress conditions. Some common dynamic tests include:
Vibration Testing
Vibration testing assesses the ability of electronic devices and components to function properly when subjected to vibrations of varying frequencies and amplitudes. This test is crucial for electronics used in applications such as automotive, aerospace, and industrial machinery.
Shock Testing
Shock testing evaluates the ability of electronic devices and components to withstand sudden, high-intensity mechanical shocks. This test simulates the impact of drops, collisions, or other sudden mechanical stresses that the electronics may encounter during their lifecycle.
Different Types of Electronics Environmental Tests
There are numerous specific tests within the categories of climatic and dynamic testing. Some of the most common types of electronics environmental tests include:
Temperature Cycling Test
The temperature cycling test exposes electronic devices and components to alternating high and low-temperature extremes for a specified number of cycles. This test evaluates the ability of the electronics to withstand thermal expansion and contraction stresses.
Parameter | Condition |
---|---|
Temperature Range | -40°C to 85°C |
Ramp Rate | 5°C/min |
Dwell Time | 30 min |
Number of Cycles | 100 |
Thermal Shock Test
The thermal shock test subjects electronic devices and components to rapid temperature changes by quickly transferring them between two temperature extremes. This test assesses the ability of the electronics to withstand sudden thermal stresses.
Parameter | Condition |
---|---|
Temperature Range | -55°C to 125°C |
Transfer Time | 10 sec |
Dwell Time | 30 min |
Number of Cycles | 50 |
Humidity Test
The humidity test exposes electronic devices and components to high humidity levels for an extended period. This test evaluates the ability of the electronics to resist moisture-related issues such as corrosion and electrical short circuits.
Parameter | Condition |
---|---|
Temperature | 85°C |
Relative Humidity | 85% |
Duration | 1000 hours |
Salt Fog Test
The salt fog test exposes electronic devices and components to a salt-laden atmosphere for an extended period. This test assesses the ability of the electronics to resist corrosion caused by exposure to salt.
Parameter | Condition |
---|---|
Temperature | 35°C |
Salt Concentration | 5% NaCl |
pH | 6.5 to 7.2 |
Duration | 96 hours |
Vibration Test
The vibration test subjects electronic devices and components to vibrations of varying frequencies and amplitudes. This test evaluates the ability of the electronics to function properly under vibratory stress.
Parameter | Condition |
---|---|
Frequency Range | 10 Hz to 2000 Hz |
Acceleration | 10 G |
Duration | 4 hours per axis |
Shock Test
The shock test exposes electronic devices and components to sudden, high-intensity mechanical shocks. This test assesses the ability of the electronics to withstand impact-related stresses.
Parameter | Condition |
---|---|
Peak Acceleration | 50 G |
Pulse Duration | 11 ms |
Number of Shocks | 3 per axis |
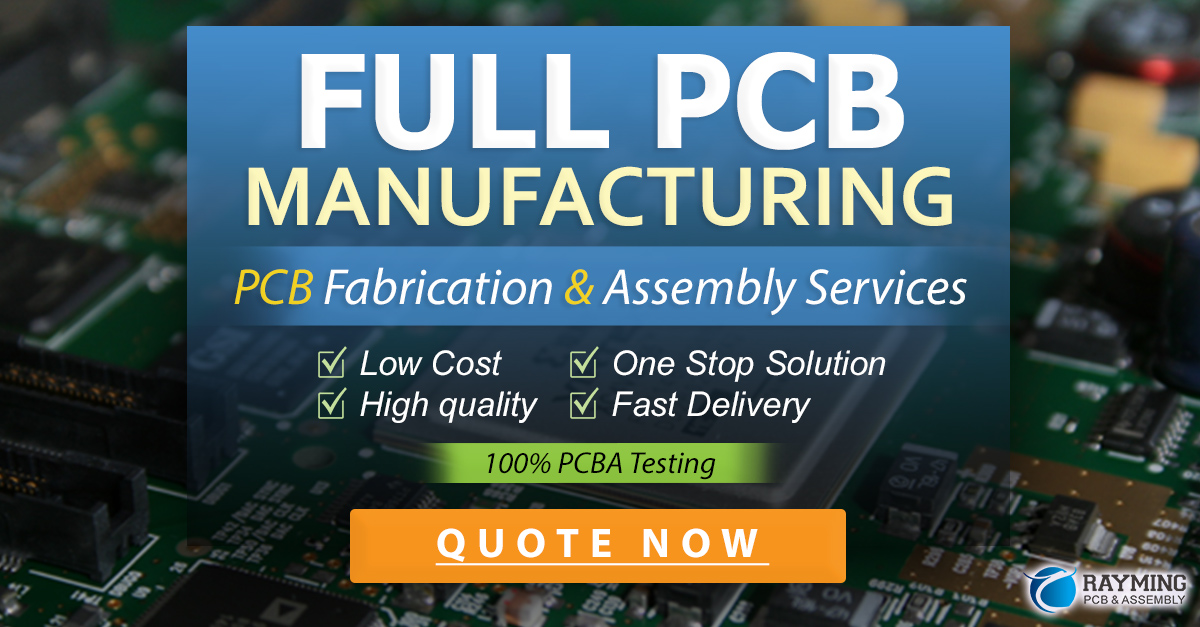
Frequently Asked Questions (FAQ)
-
Q: Why is electronics environmental testing important?
A: Electronics environmental testing is essential to ensure the reliability, durability, and performance of electronic devices and components under various environmental conditions. By identifying potential issues early in the development process, manufacturers can make necessary improvements to enhance the product’s quality and longevity. -
Q: What are the main categories of electronics environmental testing?
A: The two main categories of electronics environmental testing are climatic testing, which focuses on the effects of temperature, humidity, and other climatic conditions, and dynamic testing, which involves evaluating the effects of mechanical stress, such as vibration and shock. -
Q: What is the purpose of temperature cycling testing?
A: Temperature cycling testing evaluates the ability of electronic devices and components to withstand thermal expansion and contraction stresses caused by alternating exposure to high and low-temperature extremes. -
Q: How does salt fog testing assess the corrosion resistance of electronics?
A: Salt fog testing exposes electronic devices and components to a salt-laden atmosphere for an extended period to assess their ability to resist corrosion caused by exposure to salt. -
Q: What is the significance of vibration testing in electronics environmental testing?
A: Vibration testing is crucial for evaluating the performance of electronic devices and components under vibratory stress, particularly in applications such as automotive, aerospace, and industrial machinery, where the electronics may be subjected to constant vibrations during operation.
In conclusion, electronics environmental testing is a vital process in ensuring the reliability, durability, and performance of electronic devices and components under various environmental conditions. By conducting a wide range of climatic and dynamic tests, manufacturers can identify potential issues and make necessary improvements to enhance the quality and longevity of their products. As electronics continue to play an increasingly important role in our daily lives, the significance of environmental testing will only continue to grow, driving innovation and ensuring the development of more robust and reliable electronic devices and components.
Leave a Reply