What is Solder?
Solder is a fusible metal alloy used to create a permanent bond between metal surfaces. It typically has a lower melting point than the metals being joined, allowing it to be melted and flowed into the joint without damaging the components. The most common types of solder are composed of tin (Sn) and lead (Pb) in varying proportions, although lead-free alternatives have gained popularity due to environmental and health concerns.
Importance of Choosing the Right Solder Type
Selecting the appropriate solder type is crucial for ensuring the quality, reliability, and longevity of the soldered connection. Different solder alloys have varying melting points, wetting abilities, mechanical strength, and electrical conductivity. Factors to consider when choosing a solder type include:
- The materials being joined
- The desired melting temperature
- Environmental conditions (e.g., temperature, humidity)
- Electrical and mechanical requirements
- Regulatory compliance (e.g., RoHS, REACH)
Tin-Lead (Sn-Pb) Solder
Tin-lead solder has been the most widely used type of solder for decades due to its excellent wetting properties, low melting point, and good electrical conductivity. The most common tin-lead solder alloys are:
63/37 Solder (Sn63Pb37)
- Composition: 63% tin, 37% lead
- Melting Point: 183°C (361°F)
- Applications: General-purpose electronic soldering, through-hole and surface mount assembly
60/40 Solder (Sn60Pb40)
- Composition: 60% tin, 40% lead
- Melting Point: 188°C (370°F)
- Applications: General-purpose electronic soldering, hand soldering, rework
Despite their popularity, tin-lead solders have faced increasing restrictions due to the toxicity of lead and its harmful effects on human health and the environment. As a result, lead-free alternatives have been developed to comply with regulations such as the Restriction of Hazardous Substances (RoHS) directive.
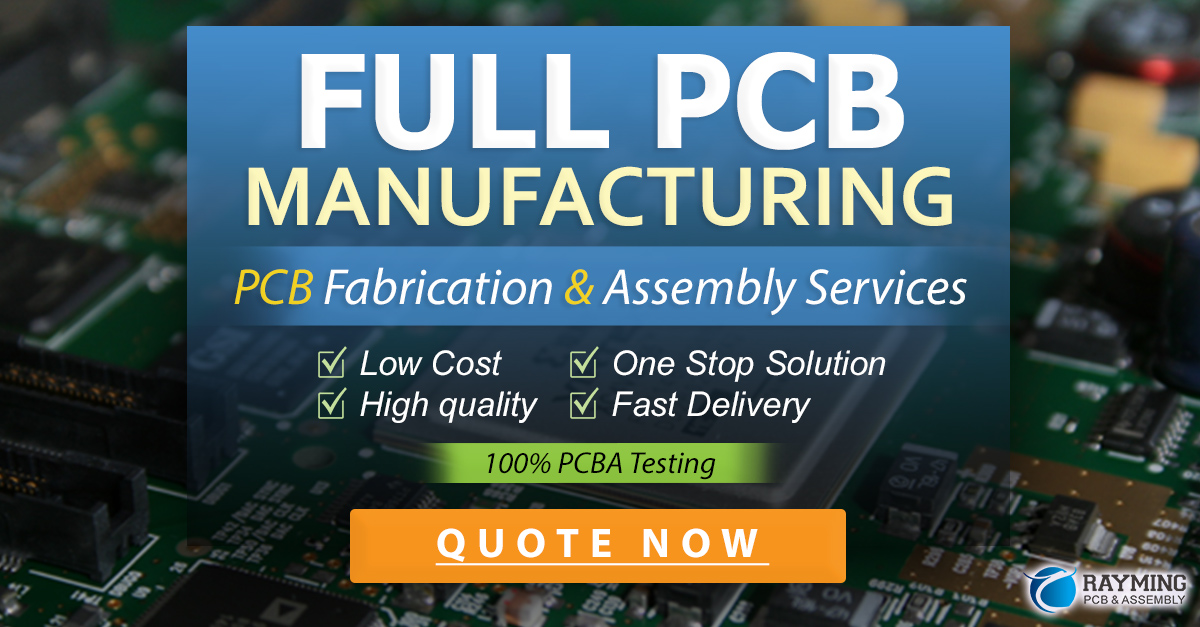
Lead-Free Solder
Lead-free solder alloys have been developed to replace tin-lead solders while maintaining similar performance characteristics. The most common lead-free solder alloys include:
Tin-Silver-Copper (SAC) Solder
- Composition: Tin (Sn), Silver (Ag), Copper (Cu) in various proportions
- Common Alloys: SAC305 (Sn96.5Ag3.0Cu0.5), SAC387 (Sn95.5Ag3.8Cu0.7)
- Melting Point: 217-220°C (423-428°F)
- Applications: Electronics assembly, surface mount technology (SMT), wave soldering
Tin-Copper (Sn-Cu) Solder
- Composition: Tin (Sn), Copper (Cu) in various proportions
- Common Alloy: Sn99.3Cu0.7
- Melting Point: 227°C (441°F)
- Applications: Wave soldering, selective soldering, hand soldering
Tin-Silver (Sn-Ag) Solder
- Composition: Tin (Sn), Silver (Ag) in various proportions
- Common Alloy: Sn96.5Ag3.5
- Melting Point: 221°C (430°F)
- Applications: Electronics assembly, high-temperature applications
Lead-free solders generally have higher melting points and may require adjustments to soldering processes and equipment. They also tend to have slightly inferior wetting properties compared to tin-lead solders, which can be mitigated through the use of appropriate fluxes and soldering techniques.
Specialty Solder Alloys
In addition to the standard tin-lead and lead-free solders, several specialty solder alloys have been developed for specific applications:
High-Temperature Solder
- Composition: Various alloys, e.g., Gold-Tin (Au-Sn), Gold-Germanium (Au-Ge)
- Melting Point: 280°C (536°F) and above
- Applications: Aerospace, automotive, high-temperature electronics
Low-Temperature Solder
- Composition: Bismuth (Bi) or Indium (In) based alloys
- Melting Point: Below 183°C (361°F)
- Applications: Temperature-sensitive components, step soldering, rework
Fusible Alloys
- Composition: Bismuth (Bi), Lead (Pb), Tin (Sn), Cadmium (Cd), Indium (In) in various proportions
- Melting Point: Ranging from 47°C (117°F) to 138°C (280°F)
- Applications: Low-temperature soldering, thermal fuses, heat-sensitive components
Solder Forms
Solder is available in various forms to accommodate different Soldering Methods and applications:
Solder Wire
- Description: A long, thin strand of solder, often with a flux core
- Diameters: Typically ranging from 0.25mm to 3.5mm
- Applications: Hand soldering, rework, repair
Solder Paste
- Description: A mixture of tiny solder spheres suspended in a flux matrix
- Applications: Surface mount assembly, stencil printing, reflow soldering
Solder Bar
- Description: A solid bar of solder, often used for melting and replenishing solder baths
- Applications: Wave soldering, dip soldering, solder pot maintenance
Solder Preforms
- Description: Pre-shaped solder pieces in various geometries (e.g., rings, discs, washers)
- Applications: Automated assembly, high-volume production, consistent Solder Volume
Flux Types
Flux is a chemical compound that aids in the soldering process by removing oxides from metal surfaces, promoting wetting, and preventing re-oxidation during soldering. The three main types of flux are:
Rosin Flux
- Description: A natural or synthetic resin-based flux
- Activity Levels: Ranging from R (Rosin) to RA (Rosin Activated)
- Residue: Non-conductive, may require cleaning for some applications
Water-Soluble Flux
- Description: A flux that produces water-soluble residues
- Activity Levels: Typically more active than rosin fluxes
- Residue: Conductive, requires cleaning after soldering
No-Clean Flux
- Description: A low-residue flux that does not require post-soldering cleaning
- Activity Levels: Varying, depending on the specific formulation
- Residue: Minimal, non-conductive, safe to leave on the assembly
The choice of flux depends on the solder type, substrate materials, environmental conditions, and the desired level of post-soldering cleanliness.
Soldering Standards and Regulations
Several international standards and regulations govern the use of solder in various industries:
RoHS (Restriction of Hazardous Substances)
- Description: A European Union directive restricting the use of certain hazardous substances, including lead, in electrical and electronic equipment
- Impact: Requires the use of lead-free solder for most consumer electronics
REACH (Registration, Evaluation, Authorization, and Restriction of Chemicals)
- Description: A European Union regulation addressing the production and use of chemical substances, including those found in solder alloys
- Impact: Requires registration and potential restriction of certain chemicals used in soldering
J-STD-001 (Requirements for Soldered Electrical and Electronic Assemblies)
- Description: A joint standard developed by IPC and EIA, providing guidelines for materials, methods, and verification criteria for producing high-quality soldered interconnections
- Impact: Establishes industry-wide requirements for soldering processes and quality control
IPC-A-610 (Acceptability of Electronic Assemblies)
- Description: A standard published by IPC, defining acceptability criteria for electronic assemblies, including soldered connections
- Impact: Sets visual and mechanical standards for evaluating the quality of soldered joints
Adhering to these standards and regulations ensures the production of reliable, safe, and compliant soldered assemblies.
Frequently Asked Questions
1. What is the difference between tin-lead and lead-free solder?
Tin-lead solder contains a mixture of tin and lead, typically in a 63/37 or 60/40 ratio. Lead-free solder, on the other hand, is composed of tin and other metals such as silver, copper, or bismuth, without the inclusion of lead. Lead-free solders have been developed to comply with environmental and health regulations, such as the RoHS directive.
2. Can lead-free solder be used as a direct replacement for tin-lead solder?
In most cases, lead-free solder can be used as a replacement for tin-lead solder. However, lead-free solders generally have higher melting points and may require adjustments to soldering processes, such as higher temperatures and longer dwell times. It is essential to consider the specific requirements of the application and consult with solder manufacturers for guidance on transitioning to lead-free solder.
3. What is flux, and why is it important in soldering?
Flux is a chemical compound that is used in conjunction with solder to improve the soldering process. It serves several purposes, including removing oxides from metal surfaces, promoting wetting of the solder, and preventing re-oxidation during soldering. Flux helps to ensure the formation of strong, reliable solder joints and is available in various formulations to suit different applications and cleaning requirements.
4. How do I choose the right solder type for my application?
Choosing the right solder type depends on several factors, such as the materials being joined, the desired melting temperature, environmental conditions, electrical and mechanical requirements, and regulatory compliance. Consider the specific needs of your application and consult with solder manufacturers or industry guidelines to select the most appropriate solder alloy and form factor.
5. What are the most common lead-free solder alloys?
The most common lead-free solder alloys include Tin-Silver-Copper (SAC) solders, such as SAC305 and SAC387, Tin-Copper (Sn-Cu) solders, and Tin-Silver (Sn-Ag) solders. These alloys have been developed to provide similar performance characteristics to tin-lead solders while complying with environmental and health regulations. The specific composition of these alloys may vary depending on the manufacturer and the intended application.
Conclusion
Selecting the appropriate solder type is crucial for ensuring the quality, reliability, and longevity of soldered connections in various applications. This article has provided a comprehensive overview of the different types of solder available, including tin-lead solder, lead-free alternatives, and specialty solder alloys. We have also discussed the importance of flux, solder forms, and relevant standards and regulations.
By understanding the unique properties and applications of each solder type, engineers, technicians, and hobbyists can make informed decisions when choosing solder for their projects. It is essential to stay updated on industry trends, regulatory requirements, and best practices to ensure the production of high-quality, reliable, and compliant soldered assemblies.
As technology advances and environmental concerns continue to shape the manufacturing landscape, the development and adoption of new solder alloys and soldering techniques will remain an ongoing process. By staying informed and adaptable, the soldering community can continue to innovate and meet the evolving demands of the electronics and metalworking industries.
Leave a Reply