What is a Layer Stack-Up in PCB Design?
A layer stack-up in printed circuit board (PCB) design refers to the arrangement of copper layers and insulating materials that make up the PCB. It is a crucial aspect of PCB design as it determines the electrical, mechanical, and thermal properties of the board. The layer stack-up defines the number of layers, their order, and the thickness of each layer and insulating material.
Importance of Layer Stack-Up in PCB Design
The layer stack-up is important in PCB design for several reasons:
-
Signal Integrity: The arrangement of layers and the choice of materials affect the signal integrity of the PCB. Proper layer stack-up helps minimize crosstalk, electromagnetic interference (EMI), and signal reflections.
-
Impedance Control: The layer stack-up influences the characteristic impedance of the traces on the PCB. Maintaining consistent impedance is essential for high-speed designs to ensure proper signal transmission and reduce signal distortion.
-
Manufacturing Feasibility: The layer stack-up must be designed considering the manufacturing capabilities and limitations. Factors such as the minimum trace width, spacing, and hole sizes are dependent on the manufacturing process and should be taken into account during the layer stack-up design.
-
Cost: The number of layers and the choice of materials in the layer stack-up directly impact the cost of the PCB. Increasing the number of layers or using specialized materials can significantly increase the manufacturing cost.
Factors to Consider in Layer Stack-Up Design
When designing the layer stack-up for a PCB, several factors need to be considered:
1. Number of Layers
The number of layers in a PCB is determined by the complexity of the design, the routing requirements, and the available space. PCBs can have anywhere from one to multiple layers. Some common layer configurations include:
- Single-layer PCB: Consists of a single conductive layer on one side of the substrate.
- Double-layer PCB: Has two conductive layers, one on each side of the substrate.
- Multi-layer PCB: Includes three or more conductive layers, with insulating layers in between.
The choice of the number of layers depends on factors such as the component density, signal routing complexity, power requirements, and cost constraints.
2. Material Selection
The selection of materials for the conductive layers and insulating substrates is crucial in the layer stack-up design. The most common materials used in PCBs are:
- Copper: Used for the conductive layers due to its excellent electrical conductivity and thermal properties.
- FR-4: A popular choice for the insulating substrate, FR-4 is a glass-reinforced epoxy laminate material with good mechanical and electrical properties.
- High-frequency laminates: For high-speed designs, specialized laminate materials like Rogers or Isola are used to achieve better signal integrity and controlled impedance.
The choice of materials depends on the electrical, mechanical, and thermal requirements of the PCB, as well as the operating environment and cost constraints.
3. Layer Thickness
The thickness of the conductive layers and insulating substrates affects the electrical and mechanical properties of the PCB. Thicker copper layers provide lower resistance and better current carrying capacity but may increase the overall thickness of the board. Thinner copper layers are suitable for fine-pitch components and high-density designs but may have limitations in terms of current handling.
The thickness of the insulating substrates determines the spacing between layers and affects the dielectric constant and impedance of the traces. Thicker substrates provide better isolation between layers but increase the overall thickness of the board.
4. Signal Integrity Considerations
Signal integrity is a critical aspect of PCB design, especially for high-speed and high-frequency applications. The layer stack-up plays a significant role in maintaining signal integrity. Some key considerations include:
- Controlled Impedance: Designing the layer stack-up to achieve a specific characteristic impedance for the traces, typically 50 ohms for single-ended signals and 100 ohms for differential pairs.
- Shielding: Using ground planes or power planes to shield sensitive signals from electromagnetic interference (EMI) and crosstalk.
- Trace Geometry: Optimizing the trace width, spacing, and routing to minimize signal reflections, crosstalk, and electromagnetic compatibility (EMC) issues.
- Via Placement: Careful placement and design of vias to minimize signal integrity issues such as impedance discontinuities and signal reflections.
5. Manufacturing Considerations
The layer stack-up design must take into account the manufacturing capabilities and limitations to ensure the PCB can be reliably manufactured. Some manufacturing considerations include:
- Minimum Trace Width and Spacing: The minimum trace width and spacing that can be reliably manufactured depends on the PCB fabrication process and the chosen copper thickness.
- Hole Sizes: The minimum hole size for vias and through-holes is determined by the drilling capabilities of the manufacturer.
- Copper Balancing: Balancing the copper distribution across layers to minimize warpage and ensure proper plating during the manufacturing process.
- Solder Mask and Silkscreen: Considering the placement and design of solder mask and silkscreen layers for component identification and protection.
Common Layer Stack-Up Configurations
There are several common layer stack-up configurations used in PCB design, depending on the number of layers and the specific requirements of the design. Some examples include:
1. Four-Layer Stack-Up
A typical four-layer PCB stack-up consists of the following layers:
Layer | Material | Thickness |
---|---|---|
Top Layer | Copper | 1 oz (35 µm) |
Prepreg | FR-4 | 0.2 mm |
Inner Layer 1 (Ground) | Copper | 0.5 oz (18 µm) |
Core | FR-4 | 0.5 mm |
Inner Layer 2 (Power) | Copper | 0.5 oz (18 µm) |
Prepreg | FR-4 | 0.2 mm |
Bottom Layer | Copper | 1 oz (35 µm) |
This stack-up provides a good balance between signal integrity, power distribution, and EMI shielding.
2. Six-Layer Stack-Up
A six-layer PCB stack-up offers more routing flexibility and better signal integrity compared to a four-layer stack-up. A typical six-layer stack-up might look like this:
Layer | Material | Thickness |
---|---|---|
Top Layer | Copper | 1 oz (35 µm) |
Prepreg | FR-4 | 0.2 mm |
Inner Layer 1 (Signal) | Copper | 0.5 oz (18 µm) |
Core | FR-4 | 0.5 mm |
Inner Layer 2 (Ground) | Copper | 0.5 oz (18 µm) |
Prepreg | FR-4 | 0.2 mm |
Inner Layer 3 (Power) | Copper | 0.5 oz (18 µm) |
Core | FR-4 | 0.5 mm |
Inner Layer 4 (Signal) | Copper | 0.5 oz (18 µm) |
Prepreg | FR-4 | 0.2 mm |
Bottom Layer | Copper | 1 oz (35 µm) |
This stack-up provides additional signal layers for routing, as well as dedicated ground and power planes for improved signal integrity and power distribution.
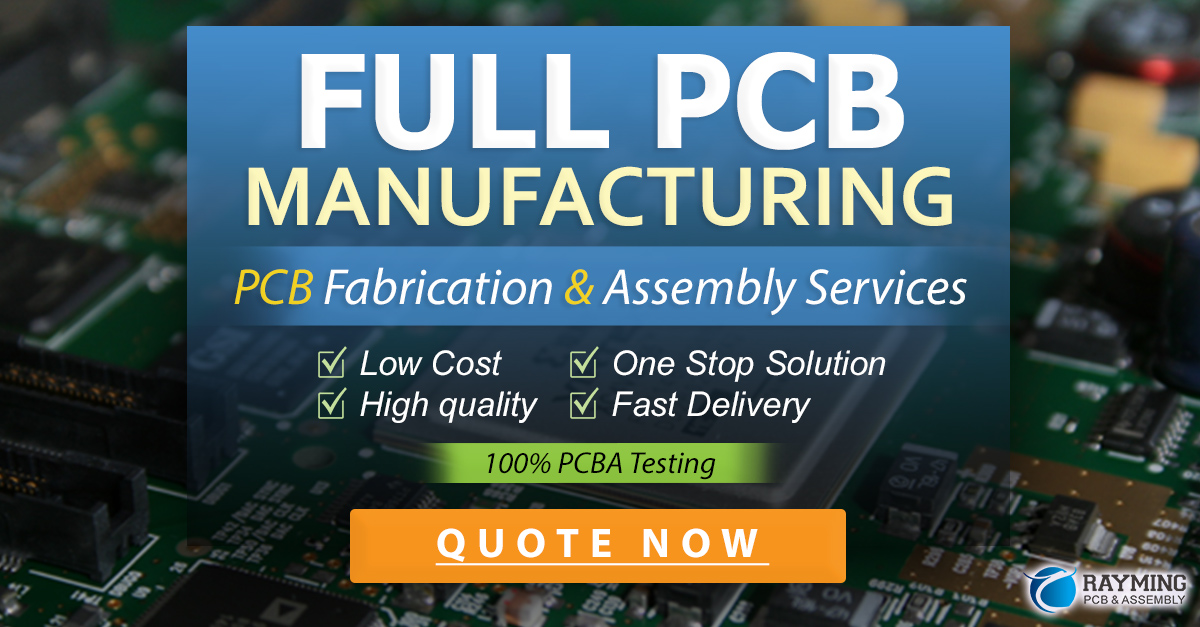
High-Speed Design Considerations
When designing PCBs for high-speed applications, additional considerations come into play to ensure signal integrity and minimize EMI. Some key aspects to consider in high-speed layer stack-up design include:
1. Controlled Impedance
Maintaining a consistent characteristic impedance for the traces is crucial in high-speed designs to minimize signal reflections and ensure proper signal transmission. The layer stack-up, trace geometry, and dielectric materials must be carefully selected to achieve the desired impedance.
2. Differential Signaling
Differential signaling is commonly used in high-speed designs to reduce EMI and improve signal integrity. Differential pairs require careful routing and spacing to maintain signal balance and minimize crosstalk. The layer stack-up should provide dedicated layers for differential pairs, with appropriate spacing and shielding.
3. Ground and Power Planes
In high-speed designs, solid ground and power planes are essential for providing low-impedance return paths, minimizing EMI, and reducing ground bounce. The layer stack-up should include dedicated ground and power planes, strategically placed to provide effective shielding and minimize the loop area of high-speed signals.
4. Via Optimization
Vias can introduce impedance discontinuities and signal reflections in high-speed designs. Proper via design and placement are critical to minimize these effects. Techniques such as via shielding, back-drilling, and optimized via geometry can help mitigate signal integrity issues related to vias.
Advanced Layer Stack-Up Techniques
In addition to the basic layer stack-up configurations, there are several advanced techniques that can be employed to enhance the performance and reliability of PCBs:
1. Blind and Buried Vias
Blind vias are used to connect the outer layers to inner layers, while buried vias connect inner layers without reaching the outer layers. These types of vias can help reduce the overall PCB size, improve signal integrity, and provide more routing flexibility.
2. Hybrid Stack-Up
A hybrid stack-up combines different materials within the same PCB to achieve specific electrical or mechanical properties. For example, using a high-frequency laminate material for critical high-speed layers while using standard FR-4 for other layers can provide a cost-effective solution for mixed-signal designs.
3. Asymmetric Stack-Up
An asymmetric stack-up refers to a layer arrangement where the copper and dielectric thicknesses vary across the layers. This technique can be used to optimize the impedance and signal integrity of specific layers while maintaining manufacturability and cost-effectiveness.
4. HDI (High Density Interconnect)
HDI PCBs employ advanced manufacturing techniques, such as microvias and fine-pitch traces, to achieve higher component density and routing complexity. HDI stack-ups typically involve multiple layers of thin dielectrics and copper, enabling the integration of more components in a smaller footprint.
Conclusion
The layer stack-up is a fundamental aspect of PCB design that significantly impacts the electrical, mechanical, and thermal performance of the board. Careful consideration of factors such as the number of layers, material selection, layer thickness, signal integrity, and manufacturing constraints is essential for designing an optimal layer stack-up.
By understanding the principles of layer stack-up design and applying appropriate techniques based on the specific requirements of the application, PCB designers can ensure reliable and high-performance boards that meet the demands of modern electronic systems.
Frequently Asked Questions (FAQ)
-
What is the purpose of a layer stack-up in PCB design?
A: The layer stack-up defines the arrangement of conductive layers and insulating materials in a PCB. It determines the electrical, mechanical, and thermal properties of the board, and plays a crucial role in ensuring signal integrity, impedance control, and manufacturability. -
How does the number of layers affect the PCB design?
A: The number of layers in a PCB depends on the complexity of the design, routing requirements, and available space. Increasing the number of layers provides more routing flexibility and can improve signal integrity, but it also increases the manufacturing cost and overall thickness of the board. -
What materials are commonly used in PCB layer stack-ups?
A: Copper is the most common material used for the conductive layers in PCBs due to its excellent electrical conductivity and thermal properties. FR-4, a glass-reinforced epoxy laminate, is a popular choice for the insulating substrate. For high-speed designs, specialized materials like Rogers or Isola laminates are used to achieve better signal integrity and controlled impedance. -
How does the layer stack-up affect signal integrity in PCBs?
A: The layer stack-up plays a significant role in maintaining signal integrity, especially in high-speed designs. Factors such as controlled impedance, shielding, trace geometry, and via placement are influenced by the layer stack-up. Proper design of the stack-up helps minimize crosstalk, EMI, and signal reflections, ensuring reliable signal transmission. -
What are some advanced layer stack-up techniques used in PCB design?
A: Advanced layer stack-up techniques include the use of blind and buried vias to connect specific layers, hybrid stack-ups that combine different materials, asymmetric stack-ups with varying copper and dielectric thicknesses, and HDI (High Density Interconnect) stack-ups that employ microvias and fine-pitch traces for higher component density and routing complexity.
Leave a Reply