Introduction to PCBA Quality Criteria
Printed Circuit Board Assembly (PCBA) is a crucial process in the manufacturing of electronic devices. The quality of the PCBA directly affects the performance, reliability, and longevity of the final product. To ensure that the PCBA meets the required standards, it is essential to establish clear quality criteria and implement effective inspection processes.
In this article, we will discuss the various criteria used to assess the quality of PCBA and identify potential defects. We will also explore the common causes of these defects and provide guidelines for preventing them.
Types of PCBA Defects
PCBA defects can be broadly categorized into the following types:
- Solder defects
- Component defects
- Assembly defects
- Contamination defects
- Mechanical defects
Let’s explore each of these categories in more detail.
Solder Defects
Solder defects are among the most common issues encountered in PCBA. These defects can lead to poor electrical connections, reduced reliability, and premature failure of the assembly. The main types of solder defects include:
Insufficient Solder
Insufficient solder occurs when there is not enough solder to form a proper connection between the component lead and the pad. This can result in a weak or intermittent connection.
Excessive Solder
Excessive solder, also known as solder bridging, happens when too much solder is applied, causing it to flow between adjacent pads or leads. This can lead to short circuits and unintended connections.
Cold Solder Joints
Cold solder joints form when the solder does not melt completely or when there is inadequate heat transfer during the soldering process. These joints appear dull and grainy and are prone to cracking and failure.
Solder Balls
Solder balls are small spheres of solder that can form during the reflow process. They can cause short circuits if they come into contact with other components or traces.
Component Defects
Component defects relate to issues with the individual components used in the PCBA. These defects can arise due to manufacturing flaws, improper handling, or incompatibility with the assembly process. Common component defects include:
Missing Components
Missing components occur when a required component is not placed on the board during the assembly process. This can lead to incomplete circuits and non-functional assemblies.
Misaligned Components
Misaligned components are those that are not placed accurately on the pads or are rotated from their intended orientation. This can cause poor connections and mechanical stress on the component.
Damaged Components
Damaged components can result from improper handling, excessive heat, or mechanical stress during the assembly process. Damaged components may not function as intended and can compromise the overall reliability of the PCBA.
Incorrect Components
Incorrect components are those that do not match the specified part number or value in the bill of materials (BOM). Using incorrect components can lead to functional failures and non-compliance with design specifications.
Assembly Defects
Assembly defects relate to issues that arise during the physical assembly of the PCBA. These defects can impact the mechanical integrity and functionality of the final product. Common assembly defects include:
Poor Component Placement
Poor component placement occurs when components are not seated properly on the pads or are not aligned with the solder paste. This can result in weak connections and mechanical stress on the components.
Incorrect Component Orientation
Incorrect component orientation happens when polarized components, such as capacitors or diodes, are placed in the wrong direction. This can cause the component to malfunction or fail prematurely.
Lifted Pads
Lifted pads occur when the copper pad separates from the PCB substrate during the assembly process. This can be caused by excessive heat, mechanical stress, or poor adhesion between the pad and the substrate.
Damaged Traces
Damaged traces can result from mechanical stress, such as bending or twisting of the board, or from improper handling during the assembly process. Damaged traces can cause open circuits or high resistance connections.
Contamination Defects
Contamination defects are caused by the presence of foreign materials on the PCBA. These contaminants can interfere with the electrical and mechanical properties of the assembly. Common contamination defects include:
Flux Residue
Flux residue is a byproduct of the soldering process that can remain on the PCBA if not properly cleaned. Excessive flux residue can cause corrosion, electrical leakage, and poor adhesion of conformal coatings.
Foreign Objects
Foreign objects, such as dust, fibers, or metal shavings, can contaminate the PCBA during the assembly process. These objects can cause short circuits, mechanical interference, and reliability issues.
Electrostatic Discharge (ESD) Damage
ESD damage occurs when static electricity discharges through sensitive components on the PCBA. This can cause immediate or latent failures in the affected components.
Mechanical Defects
Mechanical defects relate to the physical integrity of the PCBA and its components. These defects can arise from improper handling, packaging, or environmental factors. Common mechanical defects include:
Bent Leads
Bent leads occur when the leads of through-hole components are deformed during the insertion process or when the PCBA is mishandled. Bent leads can cause poor connections and mechanical stress on the components.
Cracked Components
Cracked components can result from mechanical shock, thermal stress, or improper handling. Cracks in components can lead to electrical failures and reliability issues.
Damaged Solder Mask
Damaged solder mask can expose the underlying copper traces, leading to short circuits and corrosion. Solder Mask Damage can be caused by mechanical abrasion, chemical exposure, or improper handling.
PCBA Quality Inspection Methods
To identify and prevent PCBA defects, various inspection methods are employed throughout the manufacturing process. These methods include:
Visual Inspection
Visual inspection is the most basic form of quality control, where trained operators visually examine the PCBA for defects such as missing components, solder bridges, and mechanical damage.
Automated Optical Inspection (AOI)
AOI uses high-resolution cameras and image processing algorithms to automatically detect surface-level defects, such as component placement errors, solder defects, and missing components.
X-Ray Inspection
X-ray inspection is used to detect defects that are not visible on the surface, such as voids in solder joints, BGA (Ball Grid Array) defects, and internal component damage.
In-Circuit Testing (ICT)
ICT is a functional test that verifies the electrical connectivity and performance of individual components on the PCBA. ICT can identify defects such as open circuits, short circuits, and component failures.
Functional Testing
Functional testing involves powering up the PCBA and testing its functionality against the design specifications. This method can detect defects that may not be apparent during static testing.
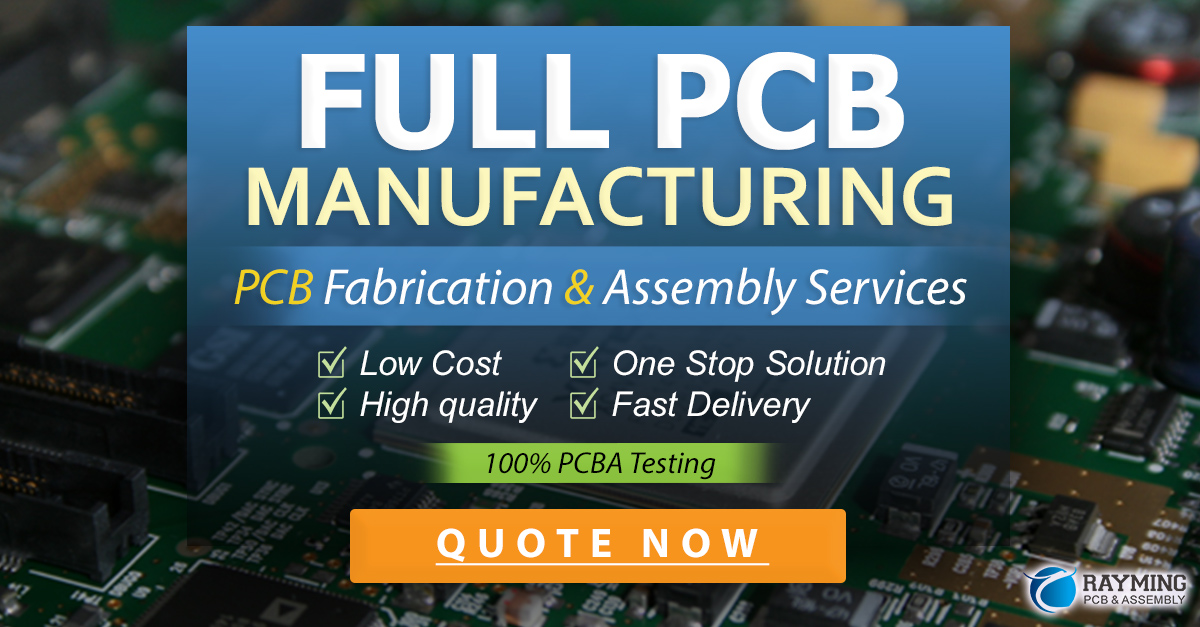
Preventing PCBA Defects
To minimize the occurrence of PCBA defects, several best practices should be implemented:
-
Robust Design for Manufacturing (DFM): Ensure that the PCBA design is optimized for manufacturability, considering factors such as component placement, solder pad design, and clearances.
-
Supplier Quality Management: Select reliable component suppliers and maintain strict incoming quality control to prevent defective components from entering the assembly process.
-
Process Control: Implement statistical process control (SPC) to monitor and maintain the stability of the manufacturing process, including solder paste printing, component placement, and reflow soldering.
-
Cleanliness and Contamination Control: Maintain a clean manufacturing environment and use appropriate cleaning processes to remove flux residue and other contaminants from the PCBA.
-
Training and Operator Certification: Provide comprehensive training to operators and technicians involved in the PCBA manufacturing process to ensure adherence to best practices and quality standards.
-
Traceability and Root Cause Analysis: Implement a robust traceability system to track components, processes, and operators throughout the manufacturing process. Use root cause analysis to identify and address the underlying causes of defects.
Frequently Asked Questions (FAQ)
1. What is the difference between a solder bridge and a solder ball?
A solder bridge is an unintended connection between two adjacent pads or leads caused by excessive solder. A solder ball, on the other hand, is a small sphere of solder that can form during the reflow process and may cause short circuits if it comes into contact with other components or traces.
2. How can ESD damage be prevented during PCBA manufacturing?
ESD damage can be prevented by implementing an ESD control program, which includes the use of grounded workstations, wrist straps, and ESD-safe packaging materials. Operators should also be trained in ESD-safe handling procedures.
3. What is the purpose of solder mask on a PCB?
Solder mask is a protective coating applied to the copper traces on a PCB. It serves to prevent solder bridging, protect the traces from corrosion, and provide electrical insulation between adjacent traces.
4. How can missing components be detected during the assembly process?
Missing components can be detected using automated optical inspection (AOI) systems, which compare the assembled PCBA to the expected layout and component placement specified in the design files.
5. What are the consequences of using incorrect components in a PCBA?
Using incorrect components can lead to functional failures, non-compliance with design specifications, and potential safety hazards. Incorrect components may have different electrical characteristics, ratings, or pinouts compared to the specified components, which can compromise the performance and reliability of the PCBA.
Conclusion
Ensuring the quality of PCBA is essential for the reliable performance and longevity of electronic devices. By understanding the various types of defects that can occur and implementing appropriate inspection and prevention methods, manufacturers can minimize the occurrence of these defects and maintain high quality standards.
Establishing clear quality criteria, such as those outlined in this article, provides a framework for assessing the quality of PCBA and identifying areas for improvement. By continuously monitoring and refining the manufacturing process, manufacturers can reduce defects, improve yield, and ultimately deliver high-quality products to their customers.
Key Takeaways
- PCBA quality is critical for the performance and reliability of electronic devices.
- Common PCBA defects include solder defects, component defects, assembly defects, contamination defects, and mechanical defects.
- Various inspection methods, such as visual inspection, AOI, X-ray inspection, ICT, and functional testing, are used to identify and prevent defects.
- Implementing best practices in design, supplier management, process control, cleanliness, training, and traceability can help minimize the occurrence of defects.
- Continuous monitoring and improvement of the PCBA manufacturing process are essential for maintaining high quality standards and customer satisfaction.
By adhering to these quality criteria and best practices, manufacturers can ensure that their PCBA products meet the highest standards of performance, reliability, and customer satisfaction.
Leave a Reply