Introduction to Copper PCBs
Printed circuit boards (PCBs) are the backbone of modern electronics, providing a stable and efficient platform for mounting and connecting electronic components. At the heart of every PCB lies a thin layer of copper foil, which plays a crucial role in the board’s functionality, reliability, and performance. This article explores the importance of copper foil in PCBs, its properties, manufacturing processes, and applications.
What is Copper Foil?
Copper foil is a thin sheet of copper, typically ranging from 9 to 180 micrometers (μm) in thickness. It is produced by electrodeposition or rolling processes and is characterized by its high electrical conductivity, thermal conductivity, and malleability. These properties make copper foil an ideal material for use in PCBs, where it serves as the conductive layer for electrical connections.
Properties of Copper Foil
Property | Value |
---|---|
Electrical Conductivity | 58.7 × 10⁶ S/m |
Thermal Conductivity | 401 W/(m·K) |
Density | 8.96 g/cm³ |
Melting Point | 1083.4°C |
Yield Strength | 70-300 MPa |
Manufacturing Process of Copper Foil for PCBs
The production of copper foil for PCBs involves several steps, each contributing to the final product’s quality and performance.
Electrodeposition
Electrodeposition is the most common method for producing copper foil for PCBs. In this process, a thin layer of copper is deposited onto a rotating stainless steel drum immersed in an electrolyte solution containing copper ions. By applying an electric current, the copper ions are reduced and deposited onto the drum’s surface, forming a continuous sheet of copper foil.
Rolling
An alternative method for producing copper foil is rolling, where a thick copper sheet is passed through a series of rolls to reduce its thickness gradually. This process is less common in PCB manufacturing due to the higher cost and lower flexibility compared to electrodeposited foil.
Foil Treatments
After the copper foil is produced, it undergoes various treatments to enhance its properties and compatibility with the PCB manufacturing process. These treatments include:
- Surface roughening: A micro-roughening treatment is applied to one side of the foil to improve its adhesion to the dielectric substrate.
- Anti-tarnish coating: A thin layer of organic compounds is applied to the foil’s surface to prevent oxidation and maintain its solderability.
- Passivation: A chromate or zinc-based coating is applied to the foil to enhance its corrosion resistance and shelf life.
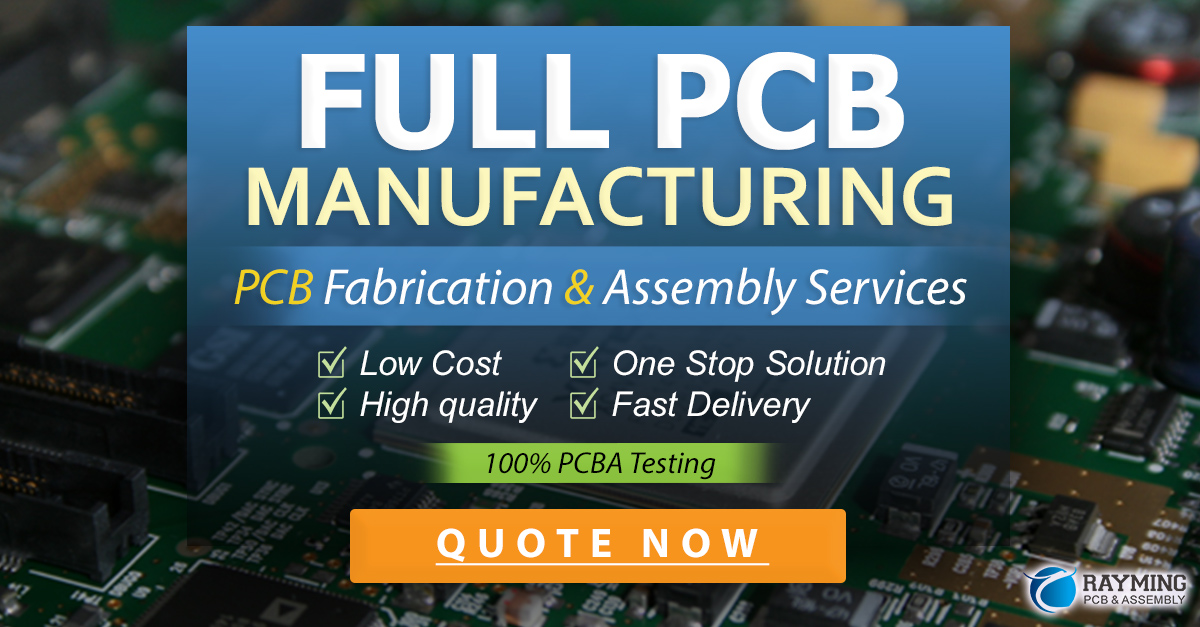
Role of Copper Foil in PCBs
Copper foil serves several essential functions in a printed circuit board:
Conductive Pathways
The primary role of copper foil in PCBs is to provide conductive pathways for electrical signals and power distribution. The copper traces etched onto the PCB’s surface allow for the interconnection of electronic components, enabling the device’s functionality.
Heat Dissipation
Copper’s high thermal conductivity helps dissipate heat generated by electronic components, preventing overheating and ensuring the device’s reliable operation.
Mechanical Support
The copper foil layer also provides mechanical support to the PCB, contributing to its overall strength and rigidity.
PCB Copper Thickness and Weight
The thickness and weight of the copper foil used in PCBs are crucial factors in determining the board’s electrical and thermal performance, as well as its manufacturability and cost.
Copper Thickness
PCB copper thickness is typically measured in ounces per square foot (oz/ft²), with 1 oz/ft² corresponding to a thickness of approximately 35 μm. Common copper thicknesses used in PCBs include:
Copper Thickness (oz/ft²) | Thickness (μm) |
---|---|
0.5 | 17.5 |
1 | 35 |
2 | 70 |
3 | 105 |
4 | 140 |
The choice of copper thickness depends on the specific application and design requirements, such as current carrying capacity, trace width, and manufacturing constraints.
Copper Weight
Copper weight is another way to express the amount of copper used in a PCB, and it is directly related to the copper thickness. The weight is measured in grams per square meter (g/m²), with the following relationship:
Copper Thickness (oz/ft²) | Copper Weight (g/m²) |
---|---|
0.5 | 152 |
1 | 305 |
2 | 610 |
3 | 915 |
4 | 1220 |
Types of Copper Foil for PCBs
There are two main types of copper foil used in PCB manufacturing: electrodeposited (ED) and rolled-annealed (RA) foil.
Electrodeposited (ED) Copper Foil
ED copper foil is the most common type used in PCBs. It is produced by the electrodeposition process described earlier and is characterized by its high purity, uniform thickness, and excellent adhesion to the dielectric substrate. ED foil is available in various thicknesses and surface treatments to suit different applications.
Rolled-Annealed (RA) Copper Foil
RA copper foil is produced by rolling a thick copper sheet and then annealing it to improve its ductility and conductivity. RA foil is less common in PCB manufacturing due to its higher cost and lower adhesion to the substrate compared to ED foil. However, it is sometimes used in high-frequency applications or when a smoother surface finish is required.
Copper Foil Selection Considerations
When selecting the appropriate copper foil for a PCB, several factors must be considered:
- Electrical requirements: The copper thickness and weight should be chosen based on the desired current carrying capacity, trace width, and impedance control.
- Thermal management: Thicker copper foil can improve heat dissipation, which is crucial for high-power applications.
- Manufacturing constraints: The choice of copper foil should be compatible with the PCB manufacturing process, including etching, drilling, and lamination.
- Cost: Thicker copper foil and specialized treatments can increase the overall cost of the PCB.
PCB Copper Foil Lamination Process
The lamination process is a critical step in PCB manufacturing, where the copper foil is bonded to the dielectric substrate. The process involves the following steps:
- Cleaning: The copper foil and dielectric substrate are cleaned to remove any contaminants that could affect the bonding process.
- Layup: The copper foil and dielectric substrate are stacked together, along with other layers such as prepreg and solder mask, to form the PCB stackup.
- Pressing: The stackup is placed in a heated press, where high temperature and pressure are applied to melt the prepreg and bond the layers together.
- Cooling: The laminated board is cooled to room temperature, allowing the bonding to solidify.
The lamination process parameters, such as temperature, pressure, and duration, must be carefully controlled to ensure a strong and reliable bond between the copper foil and the dielectric substrate.
Copper Foil Etching in PCB Manufacturing
After lamination, the copper foil on the PCB must be selectively etched to create the desired conductive patterns. The etching process involves the following steps:
- Photoresist application: A light-sensitive polymer called photoresist is applied to the copper foil surface.
- Exposure: The photoresist is exposed to UV light through a photomask, which contains the desired circuit pattern.
- Development: The exposed photoresist is developed, removing the soluble areas and leaving behind a protective pattern on the copper foil.
- Etching: The PCB is immersed in an etchant solution, typically containing cupric chloride or ferric chloride, which removes the unprotected copper foil while leaving the desired conductive patterns intact.
- Stripping: The remaining photoresist is stripped from the copper surface, revealing the final etched circuit pattern.
The etching process is a critical step in PCB manufacturing, as it determines the accuracy and reliability of the final circuit. Factors such as etchant concentration, temperature, and duration must be carefully controlled to ensure a high-quality result.
Applications of Copper PCBs
Copper PCBs are used in a wide range of electronic applications, from consumer devices to industrial equipment and aerospace systems. Some common applications include:
- Consumer electronics: Smartphones, tablets, laptops, televisions, and home appliances.
- Automotive: Engine control units, infotainment systems, sensors, and power electronics.
- Industrial: Process control systems, automation equipment, and power distribution.
- Medical: Diagnostic devices, imaging equipment, and patient monitoring systems.
- Aerospace and defense: Avionics, radar systems, and satellite communication equipment.
The specific requirements for copper foil in PCBs vary depending on the application, with factors such as operating environment, power levels, and signal frequencies influencing the choice of copper thickness, weight, and surface treatment.
Frequently Asked Questions (FAQ)
1. What is the most common copper thickness used in PCBs?
The most common copper thickness used in PCBs is 1 oz/ft², which corresponds to a thickness of approximately 35 μm. This thickness provides a good balance between electrical performance, manufacturability, and cost for many applications.
2. Can copper foil be recycled from old PCBs?
Yes, copper foil can be recycled from old PCBs through various processes, such as mechanical separation, pyrometallurgy, and hydrometallurgy. Recycling copper from PCBs helps reduce electronic waste and conserve natural resources.
3. What is the difference between low-profile and standard-profile copper foil?
Low-profile copper foil has a smoother surface finish compared to standard-profile foil, which has a slightly rougher surface. Low-profile foil is often used in high-frequency applications or when a finer trace resolution is required. Standard-profile foil is more common in general-purpose PCBs.
4. How does copper thickness affect PCB performance?
Thicker copper foil in PCBs can improve electrical performance by reducing resistance and increasing current carrying capacity. It can also enhance thermal management by dissipating heat more efficiently. However, thicker copper can also make the PCB more challenging to manufacture and increase the overall cost.
5. What are the environmental concerns associated with copper foil production and PCB manufacturing?
Copper foil production and PCB manufacturing can have environmental impacts, such as energy consumption, water usage, and the generation of hazardous waste. Proper waste management, recycling, and adherence to environmental regulations are essential to minimize these concerns. Many PCB manufacturers are adopting greener technologies and practices to reduce their environmental footprint.
Conclusion
Copper foil is a critical component in the production of printed circuit boards, providing the essential conductive pathways that enable the functionality of modern electronic devices. Its unique properties, including high electrical and thermal conductivity, make it an ideal material for PCB manufacturing. Understanding the different types of copper foil, their manufacturing processes, and selection considerations is crucial for designing and producing high-quality, reliable PCBs.
As electronic devices continue to advance and become more complex, the demand for copper PCBs is expected to grow. Innovations in copper foil production and PCB manufacturing processes will be essential to meet the evolving requirements of various industries, from consumer electronics to aerospace and beyond. By staying informed about the latest developments in copper foil technology and PCB manufacturing, engineers and designers can create cutting-edge electronic products that push the boundaries of performance and reliability.
Leave a Reply