The Role of Conformal Coatings in Automotive Electronics
Conformal coatings are thin, protective layers applied to PCBs to shield them from environmental hazards such as moisture, dust, chemicals, and extreme temperatures. In the automotive industry, where electronics are subjected to harsh conditions, conformal coatings play a vital role in ensuring the reliability and durability of PCBs.
Benefits of Conformal Coatings
- Protection against moisture and corrosion
- Insulation against electrical shorts and arcing
- Resistance to chemicals and solvents
- Improved mechanical strength and vibration dampening
- Enhanced thermal stability and heat dissipation
Types of Conformal Coatings
There are several types of conformal coatings used in the automotive industry, each with its unique properties and advantages.
Acrylic Conformal Coatings
Acrylic coatings are known for their excellent moisture resistance, easy application, and fast drying times. They provide good electrical insulation and are ideal for general-purpose applications.
Silicone Conformal Coatings
Silicone coatings offer superior temperature resistance, making them suitable for high-temperature environments. They also provide excellent flexibility and dampening properties, making them ideal for applications subject to vibration and thermal cycling.
Polyurethane Conformal Coatings
Polyurethane coatings provide excellent chemical resistance and mechanical strength. They are ideal for applications exposed to harsh chemicals or abrasive environments.
Epoxy Conformal Coatings
Epoxy coatings offer the highest level of protection against moisture, chemicals, and abrasion. They are often used in critical applications where maximum reliability is required.
Coating Type | Moisture Resistance | Temperature Resistance | Chemical Resistance | Mechanical Strength |
---|---|---|---|---|
Acrylic | Excellent | Good | Good | Good |
Silicone | Good | Excellent | Good | Excellent |
Polyurethane | Good | Good | Excellent | Excellent |
Epoxy | Excellent | Good | Excellent | Excellent |
Application Methods for Conformal Coatings
There are several methods for applying conformal coatings to PCBs, each with its advantages and limitations.
Spray Coating
Spray coating is a quick and efficient method for applying conformal coatings to large areas. It is ideal for high-volume production and can achieve a uniform coating thickness.
Brush Coating
Brush coating is a manual application method suitable for small-scale production or touch-up work. It allows for precise control over the coating application but can be time-consuming and may result in uneven coating thicknesses.
Dip Coating
Dip coating involves immersing the PCB in a tank of liquid coating material. It is an efficient method for coating complex geometries and can achieve a uniform coating thickness. However, it may require additional masking to prevent coating of unwanted areas.
Selective Coating
Selective coating uses automated dispensing systems to apply conformal coatings to specific areas of the PCB. It is ideal for applications requiring precise coating placement and can reduce material waste.
Application Method | Suitable for | Advantages | Limitations |
---|---|---|---|
Spray Coating | High-volume production | Fast, uniform coating | Overspray, masking required |
Brush Coating | Small-scale, touch-up work | Precise control | Time-consuming, uneven coating |
Dip Coating | Complex geometries | Uniform coating, efficient | Masking required |
Selective Coating | Precise coating placement | Reduced waste, targeted application | Higher equipment costs |
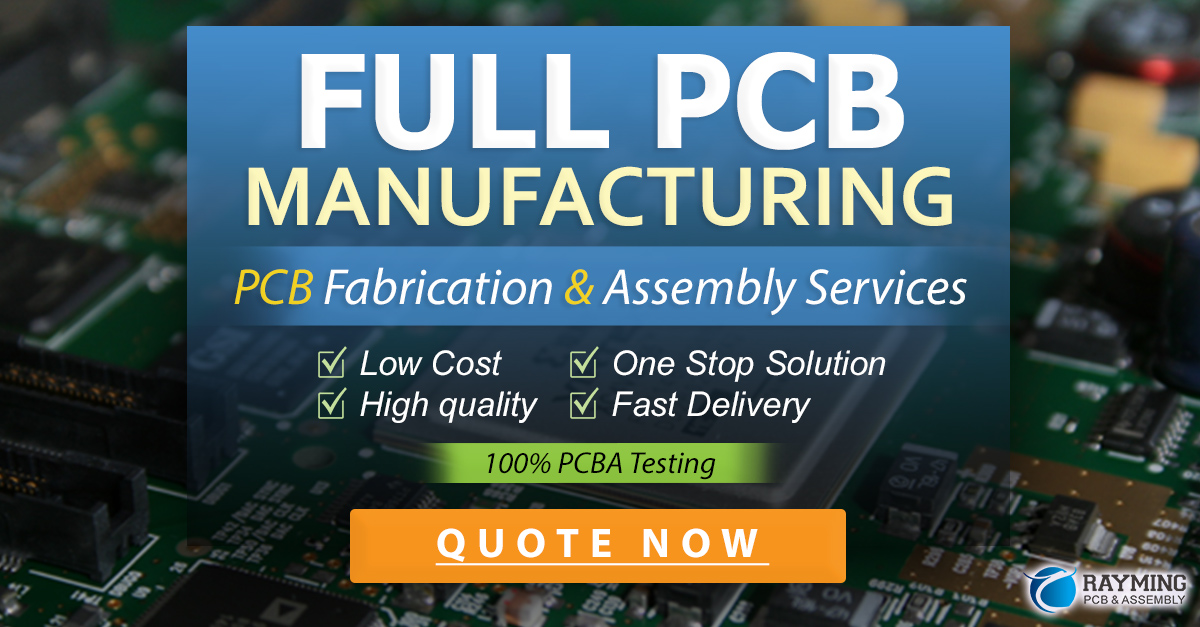
Future Trends in Conformal Coatings for Automotive Electronics
As automotive electronics continue to advance, the demand for innovative conformal coating solutions is expected to grow. Some of the future trends in this field include:
- Development of high-performance, eco-friendly coating materials
- Increased adoption of automated coating processes for improved efficiency and consistency
- Integration of smart sensors and self-healing coatings for enhanced protection and monitoring
- Advancements in nanotechnology for ultra-thin, multi-functional coatings
Frequently Asked Questions (FAQ)
1. What is the primary purpose of conformal coatings in automotive electronics?
Conformal coatings are applied to PCBs in automotive electronics to protect them from environmental hazards such as moisture, chemicals, and extreme temperatures, ensuring their reliability and longevity.
2. Which conformal coating is best suited for high-temperature environments?
Silicone conformal coatings offer superior temperature resistance, making them the best choice for high-temperature environments in automotive electronics.
3. Can conformal coatings be removed for PCB repair or rework?
Yes, conformal coatings can be removed using various methods such as solvent stripping, thermal removal, or mechanical abrasion. However, the removal process should be carefully controlled to avoid damaging the underlying PCB.
4. How do I choose the right conformal coating for my automotive electronics application?
Choosing the right conformal coating depends on factors such as the specific environmental challenges, required level of protection, and compatibility with the PCB materials and components. It is recommended to consult with a coating specialist or refer to industry guidelines and standards.
5. Are there any potential drawbacks to using conformal coatings on Automotive PCBs?
While conformal coatings offer numerous benefits, some potential drawbacks include increased production time and costs, the need for additional masking and cleaning steps, and the possibility of coating defects if not applied properly. However, these drawbacks are generally outweighed by the long-term protection and reliability provided by conformal coatings.
In conclusion, conformal coatings have become a critical aspect of PCB fabrication for automotive electronics, providing essential protection against the harsh environments encountered in modern vehicles. As the complexity and performance demands of automotive electronics continue to rise, the role of conformal coatings in ensuring the reliability and longevity of these systems will only become more significant. By understanding the types, benefits, and application methods of conformal coatings, manufacturers can make informed decisions to optimize the protection of their automotive PCBs, ultimately contributing to the development of safer, more reliable, and innovative vehicles.
Leave a Reply