PCB Substrate
The PCB substrate is the foundation of the printed circuit board. It is a thin, flat, and insulating material that provides mechanical support and electrical insulation for the components and conductors. The most common PCB substrate materials are:
Material | Description | Applications |
---|---|---|
FR-4 | A composite material made of fiberglass and epoxy resin. It has good mechanical and electrical properties. | Used in a wide range of applications, including consumer electronics, telecommunications, and industrial equipment. |
CEM-1 | A composite material made of cellulose paper and epoxy resin. It is less expensive than FR-4 but has lower performance. | Used in low-cost and low-performance applications, such as consumer electronics and toys. |
Polyimide | A high-performance polymer material with excellent thermal and chemical resistance. It is more expensive than FR-4. | Used in high-temperature and high-reliability applications, such as aerospace, military, and medical devices. |
Copper Foil
Copper foil is a thin layer of copper that is laminated onto the PCB substrate. It serves as the conductive material for the traces, pads, and vias on the PCB. The thickness of the copper foil is typically measured in ounces per square foot (oz/ft²). The most common copper foil thicknesses are:
- 0.5 oz/ft² (17.5 μm)
- 1 oz/ft² (35 μm)
- 2 oz/ft² (70 μm)
The choice of copper foil thickness depends on the current carrying capacity and the required impedance of the PCB traces.
PCB Components
PCB components are the electronic devices and parts that are mounted on the PCB substrate. They perform various functions, such as signal processing, power regulation, and data storage. The most common PCB components are:
Resistors
Resistors are passive components that resist the flow of electric current. They are used to control the voltage and current in a circuit, as well as to provide impedance matching and signal attenuation. Resistors are available in various types, such as:
- Carbon film resistors
- Metal film resistors
- Wire-wound resistors
- Surface mount resistors
The choice of resistor type depends on the required precision, power rating, and temperature coefficient.
Capacitors
Capacitors are passive components that store electric charge. They are used to filter, couple, and decouple signals, as well as to provide energy storage and power smoothing. Capacitors are available in various types, such as:
- Ceramic capacitors
- Tantalum capacitors
- Electrolytic capacitors
- Film capacitors
The choice of capacitor type depends on the required capacitance value, voltage rating, and frequency response.
Inductors
Inductors are passive components that store magnetic energy. They are used to filter, choke, and tune signals, as well as to provide impedance matching and energy storage. Inductors are available in various types, such as:
- Air core inductors
- Ferrite core inductors
- Iron powder core inductors
- Surface mount inductors
The choice of inductor type depends on the required inductance value, current rating, and frequency response.
Diodes
Diodes are semiconductor components that allow current to flow in one direction only. They are used for rectification, voltage regulation, and circuit protection. Diodes are available in various types, such as:
- Rectifier diodes
- Zener diodes
- Schottky diodes
- Light-emitting diodes (LEDs)
The choice of diode type depends on the required forward voltage drop, reverse breakdown voltage, and switching speed.
Transistors
Transistors are semiconductor components that amplify or switch electronic signals. They are used for signal processing, power control, and digital logic. Transistors are available in various types, such as:
- Bipolar junction transistors (BJTs)
- Field-effect transistors (FETs)
- Insulated-gate bipolar transistors (IGBTs)
- Surface mount transistors
The choice of transistor type depends on the required gain, power handling, and switching speed.
Integrated Circuits
Integrated circuits (ICs) are miniaturized electronic circuits that contain multiple components, such as transistors, diodes, resistors, and capacitors. They are used for complex functions, such as microprocessors, memory, and analog-to-digital converters. ICs are available in various packages, such as:
- Dual in-line package (DIP)
- Small outline integrated circuit (SOIC)
- Quad flat package (QFP)
- Ball grid array (BGA)
The choice of IC package depends on the required pin count, power dissipation, and mounting method.
PCB Assembly
PCB assembly is the process of mounting and soldering the components onto the PCB substrate. It involves several steps, such as:
-
Solder paste application: A thin layer of solder paste is applied to the pads on the PCB using a stencil or screen printing.
-
Component placement: The components are placed on the pads using a pick-and-place machine or by hand.
-
Reflow soldering: The PCB is heated in a reflow oven to melt the solder paste and form a permanent bond between the components and the pads.
-
Inspection: The assembled PCB is inspected for defects, such as shorts, opens, and misaligned components, using automated optical inspection (AOI) or X-ray inspection.
-
Testing: The assembled PCB is tested for functionality and performance using various methods, such as in-circuit testing (ICT), functional testing, and boundary scan testing.
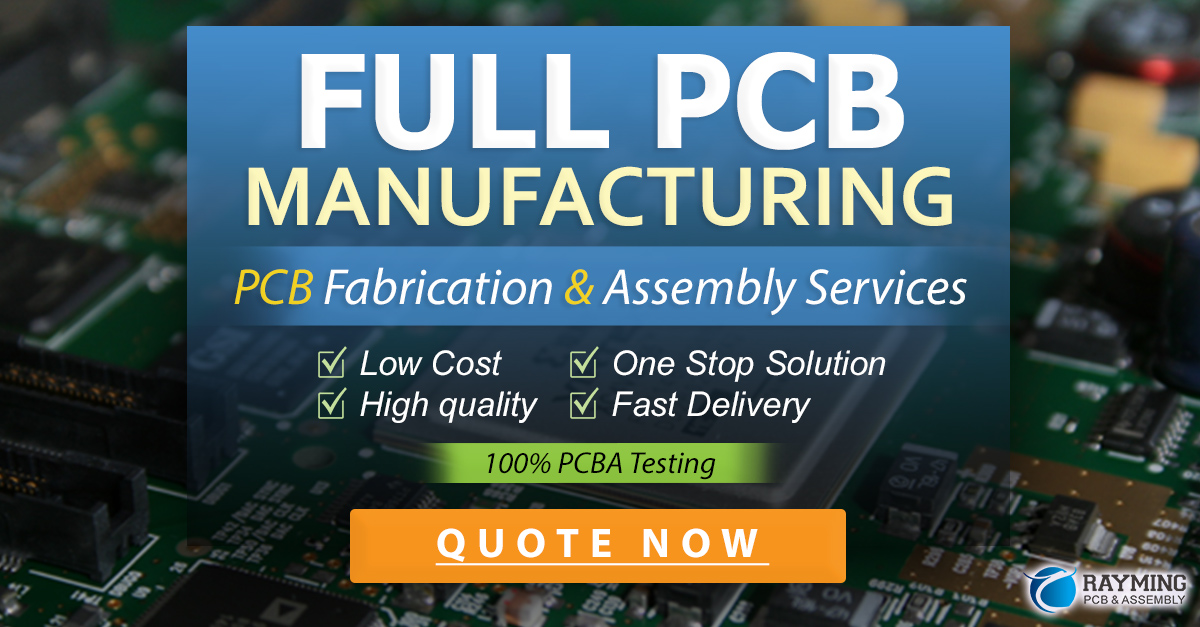
PCB Design Considerations
PCB design is a critical aspect of PCB manufacturing. It involves several considerations, such as:
Component Selection
The selection of components depends on the required functionality, performance, and cost of the PCB. It is important to choose components that are readily available, reliable, and compatible with the PCB manufacturing process.
Layout and Routing
The layout and routing of the PCB traces and components affect the signal integrity, electromagnetic compatibility (EMC), and manufacturability of the PCB. It is important to follow the design rules and guidelines, such as:
- Minimizing the trace length and impedance
- Avoiding sharp corners and acute angles
- Providing adequate clearance and creepage distances
- Using ground planes and shielding techniques
Thermal Management
The thermal management of the PCB is important to ensure the reliability and longevity of the components. It involves several techniques, such as:
- Using thermal vias and heat sinks
- Providing adequate copper area for heat dissipation
- Selecting components with low power dissipation
- Using thermal interface materials and potting compounds
Manufacturing Constraints
The PCB design must also consider the manufacturing constraints, such as:
- Minimum trace width and spacing
- Minimum hole size and pad size
- Maximum aspect ratio and copper thickness
- Panelization and depanelization methods
Frequently Asked Questions (FAQ)
1. What is the difference between a through-hole and a surface mount component?
A through-hole component has leads that are inserted into holes drilled in the PCB and soldered on the opposite side. A surface mount component has leads or pads that are soldered directly onto the surface of the PCB. Surface mount components are smaller, cheaper, and easier to assemble than through-hole components.
2. What is the purpose of a solder mask on a PCB?
A solder mask is a thin layer of polymer that covers the copper traces on the PCB, except for the pads and vias. It serves several purposes, such as:
- Protecting the copper from oxidation and corrosion
- Preventing solder bridges and shorts
- Providing electrical insulation and isolation
- Improving the aesthetics and readability of the PCB
3. What is the difference between a single-sided and a double-sided PCB?
A single-sided PCB has components and traces on one side of the substrate only. A double-sided PCB has components and traces on both sides of the substrate, with vias connecting the two sides. Double-sided PCBs offer higher component density and routing flexibility than single-sided PCBs, but are more expensive and complex to manufacture.
4. What is the purpose of a silkscreen on a PCB?
A silkscreen is a layer of ink that is printed on the surface of the PCB, usually on top of the solder mask. It serves several purposes, such as:
- Labeling the components and connectors
- Providing assembly and testing instructions
- Indicating the polarity and orientation of the components
- Improving the aesthetics and branding of the PCB
5. What is the difference between a rigid and a flexible PCB?
A rigid PCB is made of a solid substrate, such as FR-4, that does not bend or flex. A flexible PCB is made of a thin, flexible substrate, such as polyimide, that can bend and conform to various shapes. Flexible PCBs are used in applications that require movable or wearable electronics, such as mobile phones, medical devices, and automotive sensors.
Conclusion
PCB manufacturing is a complex and critical process that involves various components and considerations. The choice of components, substrate, and assembly methods depends on the required functionality, performance, and cost of the PCB. The PCB design must also consider the manufacturing constraints, thermal management, and signal integrity aspects.
By understanding the common components and their roles in PCB manufacturing, designers and engineers can create reliable, efficient, and cost-effective PCBs for various applications.
Leave a Reply