Introduction to Castellated PCBs
Castellated PCBs, also known as castellated hole PCBs or castellations, have become increasingly popular in the electronics industry due to their versatility and ease of assembly. These PCBs feature small, semi-circular holes or slots along the edges, resembling the battlements of a castle, hence the name “castellated.” This unique design allows for a secure and reliable connection between multiple PCBs or modules, making them ideal for a wide range of applications.
What is a Castellated PCB?
A castellated PCB is a printed circuit board that has small, Plated-through Holes drilled along its edges. These holes, called castellations, are typically half-drilled, meaning they extend from the edge of the board to about halfway through the thickness of the PCB. The castellations are plated with a conductive material, such as copper, to ensure electrical connectivity between the PCB and any mating components or boards.
Advantages of Castellated PCBs
Castellated PCBs offer several advantages over traditional PCB Assembly Methods:
-
Ease of Assembly: Castellated PCBs allow for simple and quick assembly, as they can be easily soldered to other boards or components without the need for additional connectors or wires.
-
Space Savings: By eliminating the need for bulky connectors, castellated PCBs help to reduce the overall size of the assembled board, making them ideal for space-constrained applications.
-
Cost-Effective: Castellated PCBs are often more cost-effective than other assembly methods, as they require fewer components and less assembly time.
-
Reliability: The plated-through castellations provide a secure and reliable electrical connection, reducing the risk of connection failures or signal integrity issues.
Applications of Castellated PCBs
Castellated PCBs find use in a wide range of industries and applications, including:
Consumer Electronics
In the consumer electronics industry, castellated PCBs are commonly used in the assembly of compact devices such as smartphones, tablets, and wearables. The space-saving design of castellated PCBs allows for the creation of smaller, more portable devices without compromising on functionality or reliability.
Industrial Automation
Castellated PCBs are also used in industrial automation systems, where they are often employed in the assembly of sensors, actuators, and control modules. The robust and reliable connections provided by castellations ensure that these critical components remain securely connected, even in harsh industrial environments.
Medical Devices
In the medical device industry, castellated PCBs are used in the assembly of various diagnostic and therapeutic equipment, such as patient monitors, imaging systems, and drug delivery devices. The compact and reliable nature of castellated PCBs makes them well-suited for these applications, where space is often limited and reliability is paramount.
Automotive Electronics
Castellated PCBs are increasingly being used in the automotive industry, particularly in the development of advanced driver assistance systems (ADAS) and in-vehicle infotainment (IVI) systems. The secure connections provided by castellations help to ensure the reliable operation of these safety-critical systems, even in the challenging environment of a moving vehicle.
Designing Castellated PCBs
When designing a castellated PCB, several key factors must be considered to ensure optimal performance and reliability:
Castellation Dimensions
The size and spacing of the castellations should be carefully selected based on the requirements of the application. Factors to consider include:
-
Hole Diameter: The diameter of the castellations should be large enough to allow for easy soldering and inspection, but not so large as to compromise the structural integrity of the PCB.
-
Hole Spacing: The spacing between castellations should be sufficient to prevent solder bridging, while still allowing for a compact design.
-
Edge Clearance: Adequate clearance should be maintained between the castellations and the edge of the PCB to prevent damage during handling and assembly.
Parameter | Recommended Value |
---|---|
Hole Diameter | 0.8 mm – 1.2 mm |
Hole Spacing | 1.0 mm – 2.0 mm |
Edge Clearance | 0.5 mm – 1.0 mm |
Material Selection
The choice of PCB material is critical to the performance and reliability of the castellated board. Factors to consider include:
-
Dielectric Constant: The dielectric constant of the PCB material should be low to minimize signal loss and distortion.
-
Thermal Conductivity: The PCB material should have good thermal conductivity to facilitate heat dissipation and prevent thermal stress on the components.
-
Mechanical Strength: The PCB material should have sufficient mechanical strength to withstand the stresses of handling and assembly.
Some commonly used PCB materials for castellated boards include:
Material | Dielectric Constant | Thermal Conductivity (W/mK) | Mechanical Strength (MPa) |
---|---|---|---|
FR-4 | 4.3 – 4.9 | 0.3 – 0.4 | 310 – 380 |
Rogers 4003C | 3.38 | 0.71 | 280 – 400 |
Isola IS410 | 4.1 – 4.3 | 0.6 – 0.8 | 450 – 550 |
Signal Integrity
To ensure optimal signal integrity, the PCB layout should be carefully designed to minimize noise, crosstalk, and reflections. Some key considerations include:
-
Trace Width: The width of the PCB traces should be selected based on the required current carrying capacity and the desired impedance.
-
Trace Spacing: Adequate spacing should be maintained between traces to minimize crosstalk and interference.
-
Ground Planes: The use of ground planes can help to minimize noise and improve signal integrity by providing a low-impedance return path for the signals.
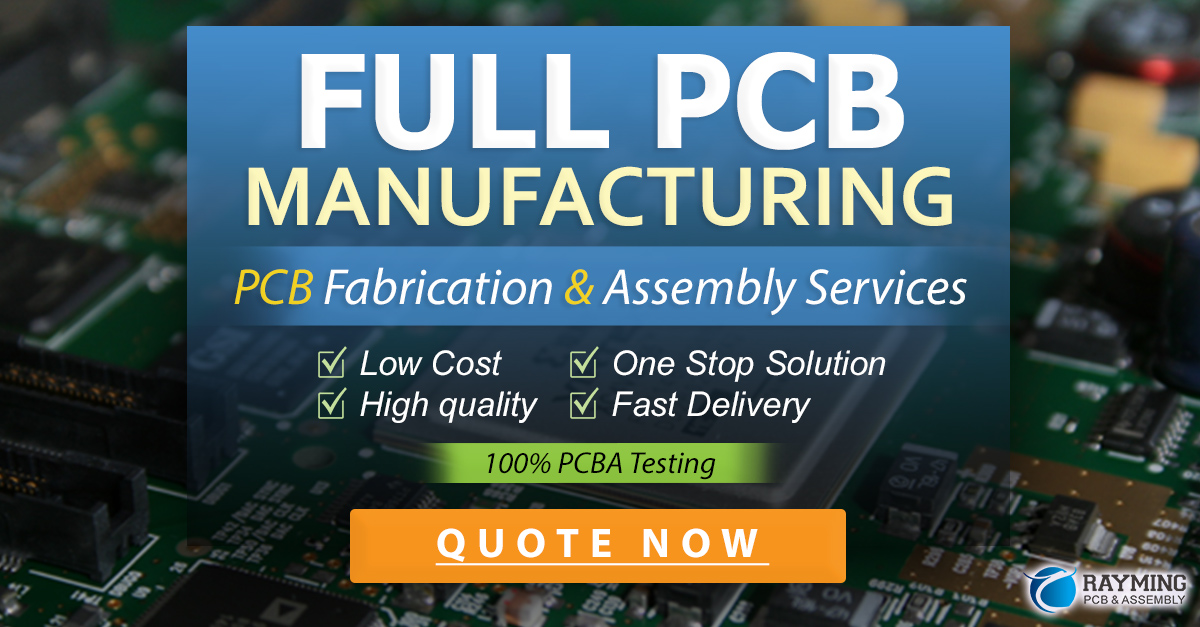
Assembly of Castellated PCBs
The assembly process for castellated PCBs is relatively simple and can be accomplished using standard soldering techniques.
Solder Paste Application
Solder paste is applied to the castellations using a stencil or syringe. The amount of solder paste should be carefully controlled to prevent bridging or insufficient fillets.
Component Placement
The mating PCB or component is aligned with the castellations and placed on top of the solder paste. Proper alignment is critical to ensure a reliable connection.
Reflow Soldering
The assembled board is then subjected to a reflow soldering process, where the solder paste is melted and flows around the castellations, creating a secure electrical and mechanical connection.
Inspection and Testing
After soldering, the assembled board should be visually inspected for any defects, such as bridging, insufficient fillets, or misalignment. Electrical testing should also be performed to verify the functionality and reliability of the connections.
Frequently Asked Questions (FAQ)
-
Q: What is the difference between a castellated PCB and a regular PCB?
A: A castellated PCB has small, plated-through holes or slots along its edges, which allow for easy and secure connection to other PCBs or components. Regular PCBs do not have these features and require additional connectors or wires for assembly. -
Q: Can castellated PCBs be used for high-frequency applications?
A: Yes, castellated PCBs can be used for high-frequency applications, provided that the PCB material and layout are properly designed to minimize signal loss and distortion. Materials with low dielectric constants, such as Rogers 4003C, are often used for high-frequency castellated PCBs. -
Q: What are the advantages of using castellated PCBs over other assembly methods?
A: Castellated PCBs offer several advantages, including ease of assembly, space savings, cost-effectiveness, and reliability. They eliminate the need for additional connectors or wires, reducing the overall size and cost of the assembled board, while providing secure and reliable electrical connections. -
Q: How small can the castellations be on a castellated PCB?
A: The size of the castellations depends on the specific application and the capabilities of the PCB manufacturer. Typically, castellations can range from 0.5 mm to 1.2 mm in diameter, with a minimum spacing of around 1.0 mm between holes. However, smaller castellations may be possible with advanced manufacturing techniques. -
Q: Are there any special considerations when designing a castellated PCB?
A: When designing a castellated PCB, it is important to carefully consider the dimensions of the castellations, the choice of PCB material, and the signal integrity of the layout. Proper hole size, spacing, and edge clearance should be maintained to ensure reliable connections and prevent damage during handling and assembly. The PCB material should be selected based on the desired electrical, thermal, and mechanical properties, and the layout should be optimized to minimize noise, crosstalk, and reflections.
Conclusion
Castellated PCBs offer a versatile and reliable solution for assembling multiple PCBs or modules in a compact and cost-effective manner. By featuring small, plated-through holes along the edges of the board, castellated PCBs allow for easy and secure connections without the need for additional connectors or wires. This makes them ideal for a wide range of applications, from consumer electronics and industrial automation to medical devices and automotive electronics.
When designing a castellated PCB, careful consideration must be given to the dimensions of the castellations, the choice of PCB material, and the signal integrity of the layout. Proper assembly techniques, including solder paste application, component placement, and reflow soldering, are also critical to ensuring a reliable and robust final product.
As the demand for compact, high-performance electronic devices continues to grow, castellated PCBs are likely to play an increasingly important role in the electronics industry. By offering a simple, reliable, and cost-effective assembly solution, castellated PCBs are poised to enable the next generation of innovative electronic products and systems.
Leave a Reply