What is Black Pad and Why is Preventing it Important?
Black pad, also known as “black pad syndrome” or “weak solder joint”, is a defect that can occur during the PCB Assembly process which results in poor solder joints and unreliable connections between components and the printed circuit board. It is characterized by a dark, oxidized appearance of the solder pad and solder mask.
Black pad can lead to a variety of issues including:
- Intermittent electrical connections
- Decreased reliability and lifespan of the PCB
- Increased scrap rates and rework costs
- Potential safety hazards if the PCB is used in a critical application
Preventing black pad is crucial for ensuring the quality, reliability, and longevity of PCBs. By taking proactive steps during the design, fabrication, and assembly stages, the risk of black pad can be significantly reduced.
Causes of Black Pad
There are several potential causes of black pad, including:
Improper Surface Finish
One of the most common causes of black pad is an improper surface finish on the PCB pads. Some finishes, such as Electroless Nickel Immersion Gold (ENIG), are more prone to black pad than others. This is because the nickel layer can become oxidized or contaminated, preventing proper solder wetting.
Excessive Soldering Temperatures
Applying excessive heat during the soldering process can also lead to black pad. If the temperature is too high or applied for too long, it can cause the solder mask and pad to degrade, resulting in oxidation and poor solder wetting.
Contamination
Contamination of the PCB pads or solder can also contribute to black pad. This can include:
- Oils and residues from handling the PCB
- Flux residue that is not properly cleaned
- Oxidation due to exposure to air or moisture
Insufficient Solder Volume
Using an insufficient amount of solder can result in weak, unreliable solder joints that are prone to black pad. It’s important to use the appropriate solder volume for the size and type of component being soldered.
Preventing Black Pad in PCB Design
Preventing black pad starts with proper PCB design. Here are some design considerations to reduce the risk of black pad:
Choose the Right Surface Finish
Selecting an appropriate surface finish is critical for preventing black pad. Some recommended finishes include:
Finish | Pros | Cons |
---|---|---|
Immersion Silver (IAg) | – Lower cost – Good solderability – Suitable for most applications |
– Limited shelf life – Can tarnish over time |
Immersion Tin (ISn) | – Excellent solderability – RoHS compliant – Suitable for most applications |
– Limited shelf life – Can form whiskers |
Organic Solderability Preservative (OSP) | – Low cost – Excellent solderability – Suitable for most applications |
– Limited shelf life – Can be difficult to inspect |
Avoid using ENIG if possible, as it is more prone to black pad than other finishes.
Design for Manufacturability
When designing the PCB, it’s important to follow best practices for manufacturability, such as:
- Providing adequate pad size and spacing for the components being used
- Avoiding overly small or tightly spaced pads that can be difficult to solder
- Using Solder Mask Dams between pads to prevent solder bridging
- Specifying the appropriate solder mask type and thickness
Specify Appropriate Solder Paste
Choosing the right solder paste is also important for preventing black pad. Consider the following factors:
- Alloy composition (e.g. SAC305, SN100C)
- Particle size and shape
- Flux type and activity level
- Rheology and printability
Work with your solder paste supplier to select a paste that is compatible with your PCB design and assembly process.
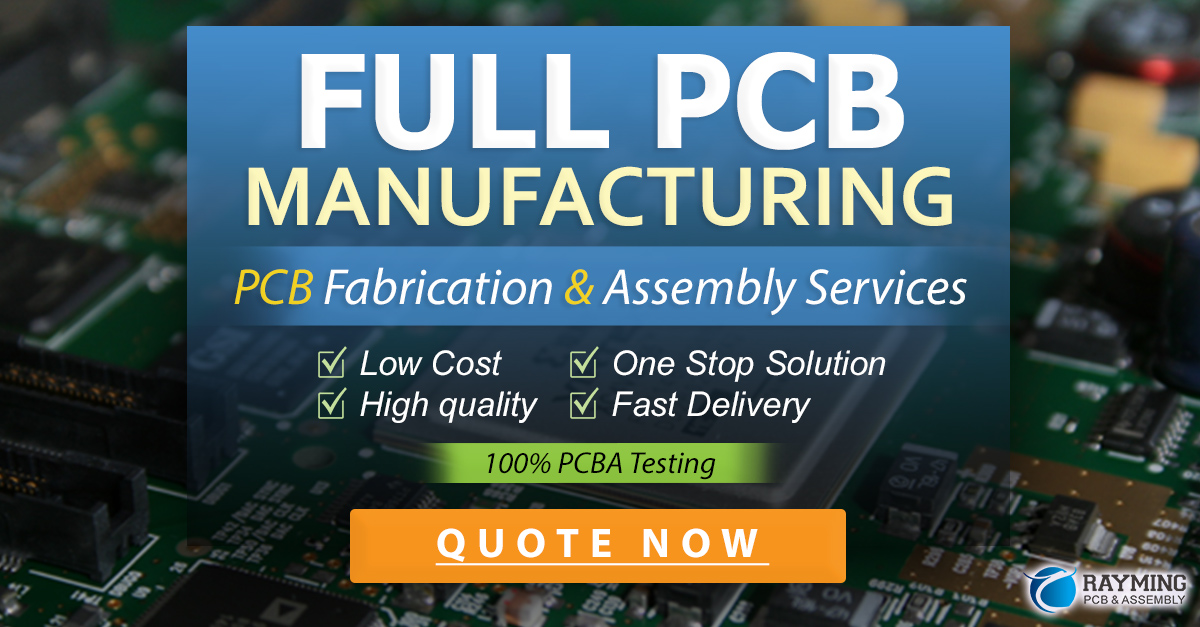
Preventing Black Pad in PCB Fabrication
The PCB fabrication process also plays a role in preventing black pad. Here are some key considerations:
Proper Handling and Storage
PCBs should be handled and stored properly to avoid contamination and oxidation. This includes:
- Wearing gloves when handling PCBs
- Storing PCBs in moisture-barrier bags with desiccant
- Avoiding exposure to extreme temperatures and humidity
Quality Control and Inspection
Implementing thorough quality control and inspection procedures can help identify and address potential issues before they lead to black pad. This may include:
- Visual inspection of the PCB pads and surface finish
- Solderability testing using Wetting Balance or dip and look methods
- Cross-sectioning and analysis of solder joints
Process Control and Monitoring
Monitoring and controlling the key parameters in the fabrication process can help ensure consistency and reduce the risk of black pad. This includes:
- Plating bath composition and temperature
- Exposure and development of the solder mask
- Etching and cleaning processes
Preventing Black Pad in PCB Assembly
Finally, the assembly process is critical for preventing black pad. Here are some best practices:
Soldering Profile Optimization
Developing and optimizing the soldering profile is essential for achieving reliable solder joints and preventing black pad. Key considerations include:
- Ramp rate and peak temperature
- Time above liquidus (TAL)
- Cooling rate
The soldering profile should be tailored to the specific PCB design, components, and solder paste being used.
Proper Cleaning and Maintenance
Regularly cleaning and maintaining the soldering equipment can help prevent contamination and ensure consistent performance. This includes:
- Cleaning the stencil and screen after each use
- Replacing worn or damaged squeegees and blades
- Monitoring and replacing the solder paste as needed
Inspection and Rework
Post-soldering inspection and rework procedures can help identify and correct any instances of black pad. This may include:
- Visual inspection under magnification
- X-ray inspection for hidden solder joints
- Reworking or replacing affected components
FAQ
Q: Can black pad be repaired?
A: In some cases, black pad can be repaired by reworking the affected solder joint. This may involve removing the component, cleaning the pad, and resoldering. However, prevention is always the best approach.
Q: How can I tell if my PCB has black pad?
A: Black pad can often be identified visually by the dark, oxidized appearance of the solder pad and mask. However, more thorough inspection methods such as cross-sectioning or X-ray may be needed to confirm the presence of black pad.
Q: Can black pad be caused by the component itself?
A: While black pad is primarily related to the PCB and soldering process, certain component finishes or materials can be more prone to oxidation and may contribute to the problem. It’s important to consider the compatibility of the component finish with the PCB finish and solder paste.
Q: How does the choice of solder paste affect black pad?
A: The solder paste plays a significant role in preventing black pad. Factors such as the alloy composition, flux type, and rheology can impact the solderability and reliability of the joint. It’s important to choose a solder paste that is compatible with the PCB design and assembly process.
Q: Can black pad be prevented through testing and inspection?
A: While testing and inspection can help identify instances of black pad, prevention is always the best approach. By following best practices in PCB design, fabrication, and assembly, the risk of black pad can be significantly reduced from the outset. However, thorough quality control and inspection procedures are still important for catching any issues that may arise.
Conclusion
Black pad is a serious issue that can impact the reliability and longevity of PCBs. By understanding the causes of black pad and implementing best practices in PCB design, fabrication, and assembly, the risk of this defect can be significantly reduced. This includes selecting appropriate surface finishes and solder pastes, designing for manufacturability, implementing proper handling and storage procedures, optimizing the soldering profile, and conducting thorough inspection and rework.
By taking a proactive approach to preventing black pad, PCB manufacturers and assemblers can improve the quality and reliability of their products, reduce scrap and rework costs, and enhance customer satisfaction. While there is no one-size-fits-all solution to preventing black pad, by considering the factors discussed in this article and working closely with suppliers and partners, the risk of this defect can be effectively managed and minimized.
Leave a Reply