Table of Contents
- Introduction to AOI Test
- How Does AOI Testing Work?
- Types of AOI Systems
- Advantages of AOI Testing
- Limitations of AOI Testing
- Applications of AOI Testing
- Implementing AOI in Electronics Manufacturing
- Best Practices for Effective AOI Testing
- Future Trends in AOI Technology
- Frequently Asked Questions (FAQ)
- Conclusion
Introduction to AOI Test
Automated Optical Inspection (AOI) is a non-contact, image-based inspection method used to detect defects and ensure the quality of printed circuit boards (PCBs), electronic assemblies, and other manufactured products. AOI systems use high-resolution cameras, advanced lighting techniques, and sophisticated image processing algorithms to capture and analyze images of the inspected objects.
The primary goal of AOI testing is to identify defects such as:
- Solder joint defects (bridging, insufficient solder, lifted leads)
- Component placement errors (missing, misaligned, or rotated components)
- Solder Paste Printing issues (insufficient or excessive paste, smearing)
- PCB defects (shorts, opens, contamination)
By detecting these defects early in the manufacturing process, AOI helps reduce rework costs, improve production yields, and ensure the reliability of the final product.
How Does AOI Testing Work?
AOI systems operate by capturing high-resolution images of the inspected object under various lighting conditions and comparing these images to a reference image or CAD data. The process typically involves the following steps:
-
Image Acquisition: High-resolution cameras capture images of the PCB or Electronic Assembly from multiple angles and under different lighting conditions (e.g., bright field, dark field, or color lighting).
-
Image Processing: The captured images are processed using advanced algorithms to enhance contrast, remove noise, and extract relevant features.
-
Defect Detection: The processed images are compared to a reference image or CAD data to identify any deviations or anomalies that may indicate a defect. This is done using techniques such as pattern matching, feature extraction, and machine learning.
-
Defect Classification: Detected defects are classified based on their type, severity, and location. This information is used to generate a report and provide feedback to the manufacturing process.
-
Reporting and Data Analysis: AOI systems generate detailed reports on the inspection results, including defect types, locations, and statistics. This data can be used for process optimization, quality control, and traceability purposes.
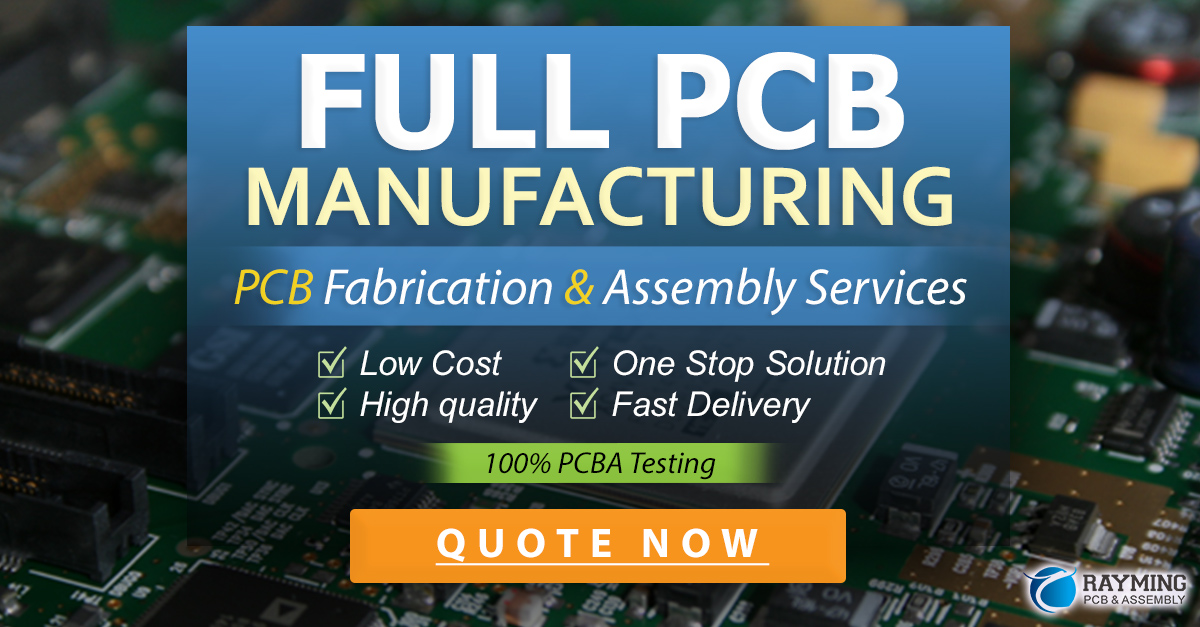
Types of AOI Systems
There are several types of AOI systems, each with its own strengths and applications:
-
2D AOI Systems: These systems use top-down cameras to capture 2D images of the inspected object. They are suitable for detecting defects on the surface of the PCB, such as component placement errors and solder paste printing issues.
-
3D AOI Systems: 3D AOI systems use multiple cameras or laser scanners to capture height and volume information of the inspected object. This allows them to detect defects that are difficult to identify using 2D imaging, such as lifted leads, insufficient solder, and coplanarity issues.
-
Inline AOI Systems: Inline AOI systems are integrated into the production line and perform inspections immediately after the solder paste printing, component placement, or reflow soldering processes. They provide real-time feedback, allowing for quick identification and correction of defects.
-
Offline AOI Systems: Offline AOI systems are stand-alone units that are used for batch inspections or as a complement to inline systems. They are often used for more detailed inspections, process validation, or failure analysis.
AOI System Type | Strengths | Applications |
---|---|---|
2D AOI | Surface defect detection, high-speed inspection | Solder paste printing, component placement |
3D AOI | Volumetric defect detection, lifted lead and coplanarity issues | Post-reflow soldering inspection |
Inline AOI | Real-time feedback, early defect detection and correction | High-volume production lines |
Offline AOI | Detailed inspection, process validation, failure analysis | Low-volume production, prototype validation |
Advantages of AOI Testing
AOI testing offers several advantages over manual inspection methods:
-
Consistency and Repeatability: AOI systems provide consistent and repeatable inspection results, eliminating the variability associated with human operators.
-
High Speed: AOI systems can inspect PCBs and electronic assemblies much faster than manual methods, enabling higher production throughput.
-
Early Defect Detection: By inspecting products at various stages of the manufacturing process, AOI helps identify defects early, reducing rework costs and improving overall quality.
-
Objective Results: AOI systems provide objective, quantitative results based on predefined criteria, reducing the subjectivity associated with manual inspections.
-
Traceability and Data Analysis: AOI systems generate detailed inspection data that can be used for process optimization, quality control, and traceability purposes.
Limitations of AOI Testing
Despite its many advantages, AOI testing also has some limitations:
-
Limited Depth Perception: 2D AOI systems may have difficulty detecting defects that require height or volume information, such as lifted leads or insufficient solder.
-
False Positives and False Negatives: AOI systems may generate false positives (identifying non-defects as defects) or false negatives (missing actual defects), requiring manual verification.
-
Programming and Setup: AOI systems require careful programming and setup to ensure accurate defect detection. This can be time-consuming and may require specialized expertise.
-
Cost: Implementing AOI systems can be costly, especially for high-end 3D systems or those with advanced features.
Applications of AOI Testing
AOI testing is widely used in various industries for quality control and defect detection:
-
Electronics Manufacturing: AOI is extensively used in the production of PCBs, electronic assemblies, and semiconductor packages to ensure product quality and reliability.
-
Automotive Industry: AOI systems are used to inspect electronic components, sensors, and other critical parts in automotive manufacturing to meet stringent quality and safety requirements.
-
Medical Devices: AOI testing is employed in the production of medical devices to ensure the highest levels of quality and compliance with regulatory standards.
-
Aerospace and Defense: AOI is used to inspect high-reliability electronic components and assemblies used in aerospace and defense applications.
-
Consumer Electronics: AOI systems are used in the production of smartphones, tablets, and other consumer electronic devices to ensure product quality and reduce returns.
Implementing AOI in Electronics Manufacturing
To successfully implement AOI in an electronics manufacturing process, consider the following steps:
-
Define Inspection Requirements: Identify the critical defects and quality parameters that need to be monitored, and establish acceptable defect thresholds.
-
Select the Appropriate AOI System: Choose an AOI system that meets your inspection requirements, production volume, and budget. Consider factors such as speed, resolution, defect detection capabilities, and ease of use.
-
Develop Inspection Programs: Create inspection programs that define the reference images, defect criteria, and inspection parameters for each product or assembly.
-
Integrate AOI into the Production Line: Determine the optimal placement of the AOI system within the production line, considering factors such as process flow, cycle time, and accessibility.
-
Train Operators and Maintenance Personnel: Provide training to operators and maintenance personnel on the proper use, programming, and maintenance of the AOI system.
-
Monitor and Optimize Performance: Regularly monitor the performance of the AOI system, analyzing defect data and making necessary adjustments to improve inspection accuracy and efficiency.
Best Practices for Effective AOI Testing
To ensure the effectiveness of AOI testing, consider the following best practices:
-
Establish Clear Defect Criteria: Define clear and measurable criteria for defect detection, including size, shape, and location tolerances.
-
Maintain Consistent Lighting and Imaging Conditions: Ensure consistent lighting and imaging conditions to minimize variations that may affect defect detection.
-
Regularly Calibrate and Maintain Equipment: Perform regular calibration and maintenance of AOI systems to ensure optimal performance and accuracy.
-
Use Appropriate Reference Images or CAD Data: Ensure that the reference images or CAD data used for comparison are accurate, up-to-date, and representative of the inspected products.
-
Implement Statistical Process Control (SPC): Use SPC techniques to monitor AOI performance, identify trends, and make data-driven decisions for process improvement.
Future Trends in AOI Technology
As electronics manufacturing continues to evolve, AOI technology is also advancing to meet new challenges and requirements:
-
Artificial Intelligence and Machine Learning: AI and machine learning techniques are being incorporated into AOI systems to improve defect detection accuracy, reduce false positives, and enable adaptive learning.
-
High-Resolution and Multi-Spectral Imaging: AOI systems are adopting higher resolution cameras and multi-spectral imaging techniques to detect smaller and more subtle defects.
-
Integration with Other Inspection Technologies: AOI is being combined with other inspection methods, such as X-ray inspection (AXI) and in-circuit testing (ICT), to provide a more comprehensive quality control solution.
-
Cloud-Based Data Management and Analytics: Cloud-based platforms are being used to store, analyze, and share AOI data across multiple production sites, enabling better collaboration and process optimization.
Frequently Asked Questions (FAQ)
-
What is the difference between AOI and visual inspection?
AOI is an automated, image-based inspection method that uses cameras and software to detect defects, while visual inspection is a manual process performed by human operators. AOI is faster, more consistent, and better suited for high-volume production, while visual inspection is more flexible and can detect some defects that may be missed by AOI. -
Can AOI detect all types of defects?
While AOI is effective at detecting a wide range of defects, it may have limitations in detecting certain types of defects, such as those that require cross-sectional or internal views of the product. In some cases, AOI may need to be combined with other inspection methods, such as X-ray inspection or electrical testing, to provide a more comprehensive defect detection solution. -
How much does an AOI system cost?
The cost of an AOI system can vary widely depending on factors such as the type of system (2D or 3D), resolution, speed, and additional features. Entry-level 2D systems can cost around $50,000 to $100,000, while high-end 3D systems can cost upwards of $500,000 or more. It is important to consider the total cost of ownership, including maintenance, programming, and operator training, when evaluating the cost of an AOI system. -
How long does it take to program an AOI system for a new product?
The time required to program an AOI system for a new product can vary depending on the complexity of the product, the number of defect types to be detected, and the experience of the programmer. Simple products may take a few hours to program, while complex products with many defect types may take several days or even weeks. Many AOI systems offer features such as CAD import and automated program generation to help reduce programming time. -
What training is required to operate and maintain an AOI system?
Operators of AOI systems typically require training on the basic operation of the system, including loading and unloading of products, starting and stopping inspection runs, and reviewing inspection results. Maintenance personnel may require additional training on calibration, troubleshooting, and repair procedures. Many AOI system vendors offer training courses and certifications to help ensure that users are properly trained on their systems.
Conclusion
Automated Optical Inspection (AOI) is a powerful and widely used test method in electronics manufacturing for detecting defects and ensuring product quality. By leveraging advanced imaging technologies, image processing algorithms, and automated defect detection, AOI systems provide fast, consistent, and objective inspection results.
While AOI offers many advantages over manual inspection methods, it is important to consider its limitations and to select the appropriate AOI system for your specific application and requirements. Effective implementation of AOI testing requires careful planning, programming, and integration into the production process, as well as ongoing monitoring and optimization.
As electronics manufacturing continues to advance, AOI technology is evolving to meet new challenges, with trends such as AI and machine learning, high-resolution imaging, and cloud-based data management promising to further enhance the capabilities and value of AOI testing in the future.
Leave a Reply