What is Rogers Material PCB?
Rogers Material PCB refers to printed circuit boards that use specialized dielectric materials manufactured by Rogers Corporation. These high-performance materials are engineered to provide superior electrical properties compared to standard FR-4 PCB Substrates. Rogers materials are commonly used in demanding applications such as high-frequency RF and microwave circuits, radar systems, aerospace and defense electronics, and advanced telecommunications equipment.
RAYPCB is a leading PCB manufacturer that offers expertise in fabricating boards using Rogers materials. By leveraging the advanced properties of Rogers substrates and RAYPCB’s state-of-the-art manufacturing capabilities, designers can create PCBs optimized for high-speed, low-loss performance.
Key Properties of Rogers Materials
Rogers materials exhibit several distinct properties that make them ideal for high-frequency and high-speed applications:
-
Low Dielectric Constant (Dk): Rogers materials have a lower dielectric constant compared to FR-4, which reduces the amount of signal loss and allows for faster signal propagation.
-
Low Dissipation Factor (Df): The dissipation factor measures the amount of energy lost as heat in the dielectric material. Rogers materials have a low Df, minimizing signal attenuation and improving overall efficiency.
-
Tight Dk and Df Control: Rogers materials are manufactured with strict control over the dielectric constant and dissipation factor, ensuring consistent performance across the entire PCB.
-
High Thermal Conductivity: Many Rogers materials offer high thermal conductivity, which helps dissipate heat more effectively and improves the PCB’s thermal stability.
-
Dimensional Stability: Rogers materials maintain their dimensions and electrical properties over a wide temperature range, making them suitable for applications with demanding environmental conditions.
Common Rogers Material Grades
Rogers Corporation offers several grades of dielectric materials, each with unique properties tailored for specific applications. Some of the most popular Rogers material grades include:
Grade | Dk | Df | Key Features |
---|---|---|---|
RO3003 | 3.00 | 0.0010 | Low loss, excellent thermal stability |
RO4003C | 3.38 | 0.0027 | Low loss, CAF resistant, cost-effective |
RO4350B | 3.48 | 0.0037 | Low loss, high thermal conductivity |
RT/duroid 5880 | 2.20 | 0.0009 | Ultra-low loss, lightweight, high Dk stability |
RT/duroid 6002 | 2.94 | 0.0012 | Low loss, high power handling, low CTE |
Each Rogers material grade has its own set of electrical and mechanical properties, allowing designers to select the most suitable material for their specific application requirements.
RAYPCB’s Capabilities for Rogers Material PCB Manufacturing
RAYPCB has extensive experience in manufacturing PCBs using Rogers materials. The company invests in advanced equipment and processes to ensure the highest quality and reliability of the finished boards.
Multilayer Rogers PCB Fabrication
RAYPCB can fabricate multilayer PCBs using Rogers materials, allowing for complex designs with multiple signal layers. The company employs precise registration techniques to align the layers accurately and maintain the tight tolerances required for high-frequency applications.
Controlled Impedance
Controlling the impedance of transmission lines is crucial for maintaining signal integrity in high-speed circuits. RAYPCB has the expertise to design and fabricate controlled impedance PCBs using Rogers materials, ensuring that the impedance remains within the specified tolerance across the entire board.
High-Density Interconnect (HDI)
HDI technology enables the miniaturization of PCBs by using microvias and fine pitch features. RAYPCB can combine HDI techniques with Rogers materials to create compact, high-performance boards for applications where space is limited.
Hybrid Stackups
In some cases, it may be beneficial to use a combination of Rogers materials and standard FR-4 in a single PCB Stackup. RAYPCB can design and fabricate hybrid stackups that leverage the strengths of each material, optimizing performance while managing costs.
Precision Drilling and Routing
Manufacturing PCBs with Rogers materials requires precise drilling and routing to maintain the integrity of the material and ensure accurate feature sizes. RAYPCB uses high-speed CNC machines with specialized tooling to achieve clean, burr-free holes and tight tolerance routing.
Design Considerations for Rogers Material PCBs
Designing PCBs with Rogers materials requires careful consideration of several factors to ensure optimal performance and manufacturability.
Material Selection
Choosing the appropriate Rogers material grade is crucial for meeting the specific requirements of the application. Designers should consider factors such as the dielectric constant, dissipation factor, thermal conductivity, and cost when selecting a material.
Trace Width and Spacing
The trace width and spacing on a Rogers PCB can significantly impact the impedance and signal integrity. Designers must calculate the appropriate trace dimensions based on the material properties and the desired impedance. RAYPCB can provide guidance and assistance in determining the optimal trace geometry.
Via Design
Vias play a critical role in Multilayer PCBs, providing electrical connections between layers. When designing vias for Rogers PCBs, designers must consider the via size, pad size, and anti-pad size to minimize signal reflections and maintain impedance control.
Thermal Management
High-frequency circuits generate significant amounts of heat, which can affect the performance and reliability of the PCB. Designers should incorporate thermal management techniques, such as using high-thermal-conductivity Rogers materials, adding thermal vias, and designing proper heatsinking, to dissipate heat effectively.
Assembly Considerations
Assembling components on Rogers PCBs requires special considerations due to the unique properties of the materials. Designers should work closely with RAYPCB and the assembly team to ensure that the PCB design is compatible with the chosen assembly process, such as reflow soldering or wire bonding.
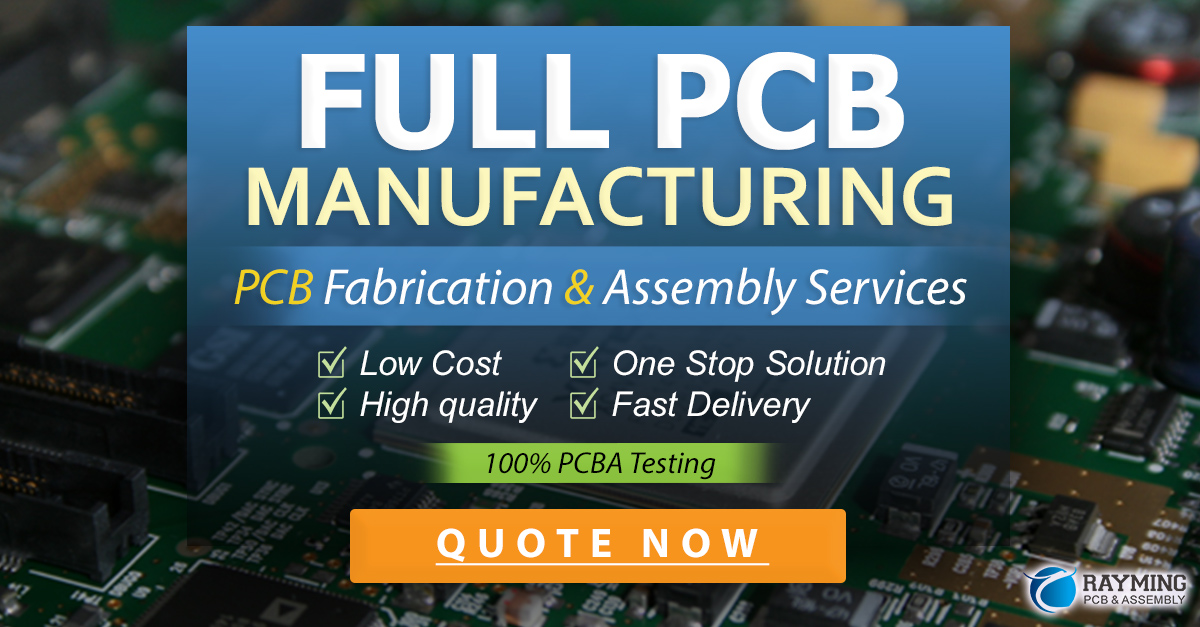
Applications of Rogers Material PCBs
Rogers material PCBs find applications in various industries where high-frequency, high-speed, and high-reliability performance is critical. Some common applications include:
Wireless Communications
Rogers materials are extensively used in wireless communication systems, such as 5G networks, cellular base stations, and satellite communications. The low-loss properties of Rogers materials enable efficient signal transmission and reception at high frequencies.
Aerospace and Defense
In aerospace and defense applications, Rogers PCBs are used in radar systems, avionics, and military communications equipment. The materials’ ability to maintain stable performance over wide temperature ranges and withstand harsh environments makes them ideal for these demanding applications.
Automotive Radar
Advanced driver assistance systems (ADAS) and autonomous vehicles rely on high-frequency radar systems for object detection and collision avoidance. Rogers materials are used to fabricate the PCBs for these radar modules, ensuring reliable performance and enabling the development of safer automotive technologies.
Internet of Things (IoT)
As the IoT continues to grow, there is an increasing demand for high-performance wireless connectivity solutions. Rogers material PCBs are used in IoT devices and gateways to enable fast, reliable data transmission and reception.
Medical Electronics
In medical electronics, Rogers PCBs are used in applications such as MRI systems, ultrasound imaging, and patient monitoring devices. The materials’ low-loss properties and high reliability ensure accurate data acquisition and transmission, supporting the development of advanced medical technologies.
Frequently Asked Questions (FAQ)
-
Q: What are the advantages of using Rogers materials over standard FR-4 for high-frequency applications?
A: Rogers materials offer several advantages over FR-4, including lower dielectric constant, lower dissipation factor, tighter Dk and Df control, higher thermal conductivity, and better dimensional stability. These properties enable faster signal propagation, lower signal loss, and improved thermal management, making Rogers materials ideal for high-frequency applications. -
Q: Can RAYPCB fabricate multilayer PCBs using Rogers materials?
A: Yes, RAYPCB has the capability to fabricate Multilayer PCBs using Rogers materials. The company employs precise registration techniques to align the layers accurately and maintain the tight tolerances required for high-frequency applications. -
Q: What is controlled impedance, and why is it important for Rogers PCBs?
A: Controlled impedance refers to the precise control of the impedance of transmission lines on a PCB. It is important for Rogers PCBs because maintaining a consistent impedance is critical for ensuring signal integrity in high-speed circuits. RAYPCB has the expertise to design and fabricate controlled impedance PCBs using Rogers materials. -
Q: Can RAYPCB assist with the design of Rogers material PCBs?
A: Yes, RAYPCB can provide guidance and assistance in designing PCBs using Rogers materials. The company’s experienced engineers can help with material selection, trace width and spacing calculations, via design, and thermal management considerations to ensure optimal performance and manufacturability. -
Q: What industries commonly use Rogers material PCBs?
A: Rogers material PCBs are commonly used in industries such as wireless communications, aerospace and defense, automotive radar, Internet of Things (IoT), and medical electronics. These industries require high-frequency, high-speed, and high-reliability performance, which Rogers materials can provide.
Conclusion
Rogers material PCBs offer superior performance and reliability for high-frequency and high-speed applications. By leveraging the advanced properties of Rogers materials and RAYPCB’s manufacturing expertise, designers can create PCBs that meet the demanding requirements of various industries.
RAYPCB’s capabilities in fabricating Rogers material PCBs, including multilayer fabrication, controlled impedance, HDI, hybrid stackups, and precision drilling and routing, enable the production of high-quality boards for a wide range of applications.
When designing Rogers material PCBs, careful consideration of material selection, trace geometry, via design, thermal management, and assembly compatibility is essential for achieving optimal performance and manufacturability.
As technology continues to advance, the demand for high-performance PCBs using Rogers materials will continue to grow. RAYPCB is well-positioned to support designers and industries in meeting this demand, providing state-of-the-art manufacturing solutions for Rogers material PCBs.
Leave a Reply