Understanding PCB Substrates
A PCB substrate is an insulating material that serves as the base for the conductive copper traces and components. It plays a critical role in determining the electrical, thermal, and mechanical characteristics of the PCB. The choice of substrate material depends on factors such as the operating frequency, temperature range, environmental conditions, and cost constraints of your project.
Key Properties of PCB Substrates
When evaluating PCB substrate materials, several key properties should be considered:
-
Dielectric Constant (Dk): The dielectric constant measures the substrate’s ability to store electrical energy. A lower Dk value indicates better signal integrity and higher speed capabilities.
-
Dissipation Factor (Df): The dissipation factor represents the amount of energy lost as heat in the substrate. A lower Df value means less signal loss and better performance at high frequencies.
-
Thermal Conductivity: This property determines how well the substrate conducts heat away from components. Higher thermal conductivity helps in preventing overheating and improves the PCB’s reliability.
-
Coefficient of Thermal Expansion (CTE): CTE measures the substrate’s expansion or contraction with changes in temperature. A substrate with a CTE close to that of copper minimizes stress and prevents warping or delamination.
-
Mechanical Strength: The substrate must possess sufficient mechanical strength to withstand handling, assembly, and operational stresses without cracking or breaking.
-
Flame Retardancy: Some applications require the substrate to be flame retardant to ensure safety and comply with industry standards.
Common PCB Substrate Materials
Now, let’s explore some of the most commonly used PCB substrate materials and their characteristics.
1. FR-4
FR-4 (Flame Retardant 4) is the most widely used PCB substrate material. It is a composite material made of woven fiberglass cloth impregnated with an epoxy resin. FR-4 offers a good balance of electrical, mechanical, and thermal properties at a relatively low cost.
Property | Value |
---|---|
Dielectric Constant (Dk) | 4.2 – 4.5 @ 1 MHz |
Dissipation Factor (Df) | 0.02 @ 1 MHz |
Thermal Conductivity | 0.3 W/mK |
CTE (Z-axis) | 50-70 ppm/°C |
Tg (Glass Transition Temp.) | 130°C – 140°C |
FR-4 is suitable for most general-purpose applications, including consumer electronics, industrial controls, and telecommunications equipment. However, it may not be the best choice for high-frequency or high-speed designs due to its relatively high Dk and Df values.
2. High Tg FR-4
High Tg FR-4 is a variant of the standard FR-4 material with improved thermal stability. It uses a modified epoxy resin that provides a higher glass transition temperature (Tg) compared to regular FR-4.
Property | Value |
---|---|
Dielectric Constant (Dk) | 4.2 – 4.5 @ 1 MHz |
Dissipation Factor (Df) | 0.02 @ 1 MHz |
Thermal Conductivity | 0.3 W/mK |
CTE (Z-axis) | 50-70 ppm/°C |
Tg (Glass Transition Temp.) | 170°C – 180°C |
The higher Tg of this material allows for better thermal stability during assembly processes, such as Lead-Free Soldering, and improved reliability in high-temperature environments. High Tg FR-4 is often used in automotive, aerospace, and military applications where thermal challenges are present.
3. Rogers 4003
Rogers 4003 is a high-performance laminate material designed for high-frequency and high-speed applications. It is composed of a ceramic-filled hydrocarbon resin with low dielectric loss and excellent thermal properties.
Property | Value |
---|---|
Dielectric Constant (Dk) | 3.38 @ 10 GHz |
Dissipation Factor (Df) | 0.0027 @ 10 GHz |
Thermal Conductivity | 0.71 W/mK |
CTE (Z-axis) | 46 ppm/°C |
Tg (Glass Transition Temp.) | >280°C |
Rogers 4003 is well-suited for RF and microwave applications, such as antennas, filters, and amplifiers. Its low Dk and Df values enable superior signal integrity and reduced signal loss at high frequencies. The material’s excellent thermal conductivity and high Tg also contribute to its reliability in demanding environments.
4. Polyimide
Polyimide is a high-performance polymer known for its exceptional thermal stability, mechanical strength, and chemical resistance. It is often used in flexible and Rigid-Flex PCBs.
Property | Value |
---|---|
Dielectric Constant (Dk) | 3.5 @ 1 MHz |
Dissipation Factor (Df) | 0.002 @ 1 MHz |
Thermal Conductivity | 0.2 W/mK |
CTE (Z-axis) | 30-60 ppm/°C |
Tg (Glass Transition Temp.) | >250°C |
Polyimide’s high thermal stability and flexibility make it ideal for applications that require bendable or foldable PCBs, such as wearable electronics, aerospace systems, and medical devices. Its low Dk and Df values also make it suitable for high-frequency applications.
5. Teflon (PTFE)
Teflon, or polytetrafluoroethylene (PTFE), is a fluoropolymer known for its extremely low dielectric loss and high thermal stability. It is often used in high-frequency and microwave applications.
Property | Value |
---|---|
Dielectric Constant (Dk) | 2.1 @ 10 GHz |
Dissipation Factor (Df) | 0.0002 @ 10 GHz |
Thermal Conductivity | 0.25 W/mK |
CTE (Z-axis) | 100-200 ppm/°C |
Tg (Glass Transition Temp.) | N/A (Melting Point >300°C) |
Teflon’s exceptionally low Dk and Df values make it an excellent choice for high-frequency and low-loss applications, such as radar systems, satellite communications, and high-speed digital circuits. However, its high CTE and relatively low thermal conductivity can pose challenges in manufacturing and reliability.
Choosing the Right PCB Substrate
Selecting the appropriate PCB substrate material depends on the specific requirements of your project. Consider the following factors when making your decision:
-
Frequency and Speed: For high-frequency or high-speed applications, choose materials with low Dk and Df values, such as Rogers 4003 or Teflon.
-
Temperature Range: If your PCB will be exposed to high temperatures, opt for materials with high Tg and good thermal stability, such as High Tg FR-4 or polyimide.
-
Flexibility: For applications requiring bendable or flexible PCBs, polyimide is an excellent choice.
-
Cost: FR-4 is the most cost-effective option for general-purpose applications, while high-performance materials like Rogers 4003 and Teflon come at a higher price point.
-
Manufacturing Complexity: Some materials, such as Teflon, may require specialized manufacturing processes and expertise, which can impact the overall cost and lead time of your project.
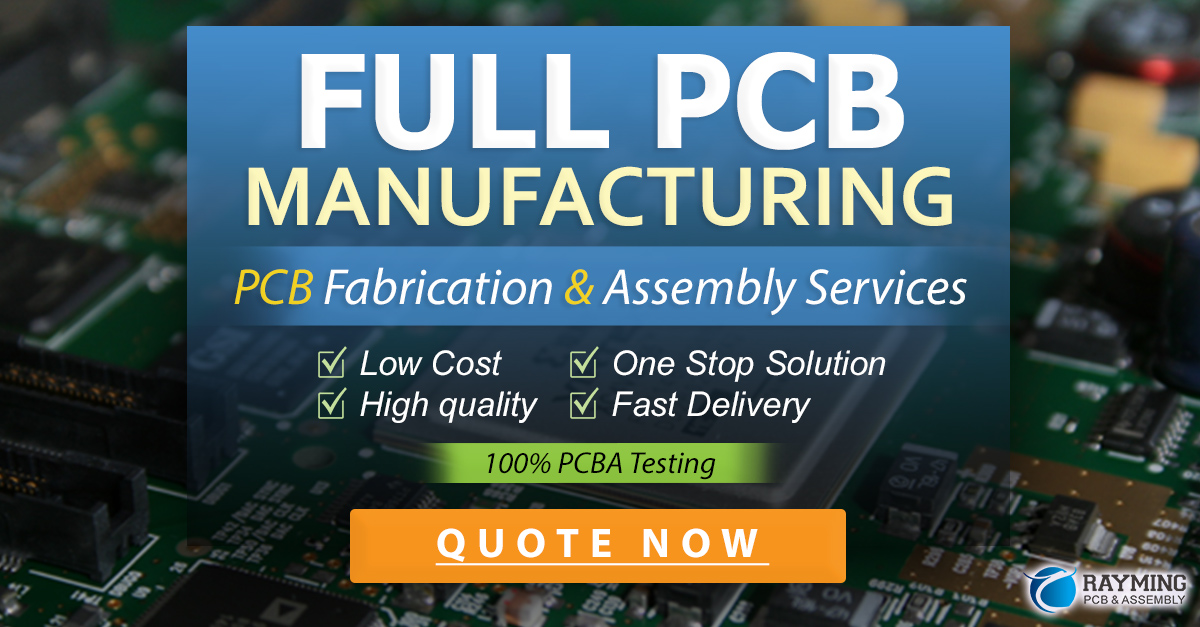
Frequently Asked Questions (FAQ)
-
Q: Can I mix different substrate materials in a single PCB?
A: Yes, it is possible to use different substrate materials in a single PCB, known as a hybrid or mixed-material PCB. This approach allows you to leverage the strengths of each material in specific areas of the board. However, it requires careful design considerations and may increase manufacturing complexity. -
Q: How does the substrate thickness affect PCB performance?
A: The substrate thickness can impact several aspects of PCB performance. Thinner substrates are more suitable for high-frequency applications as they minimize signal reflections and losses. However, thicker substrates provide better mechanical stability and thermal dissipation. The choice of thickness depends on the specific requirements of your project. -
Q: Can I use FR-4 for high-frequency applications?
A: While FR-4 is a versatile and cost-effective substrate material, it may not be the best choice for high-frequency applications above a few gigahertz. Its relatively high Dk and Df values can lead to signal integrity issues and increased losses at higher frequencies. For such applications, materials like Rogers 4003 or Teflon are more suitable. -
Q: What is the difference between rigid and flexible PCB substrates?
A: Rigid PCB substrates, such as FR-4, provide a stable and sturdy base for the circuit board. They are suitable for most general-purpose applications. Flexible PCB substrates, like polyimide, allow the board to bend or flex, making them ideal for applications requiring conformity to unique shapes or dynamic flexing. -
Q: How do I choose the right substrate material for my project?
A: Choosing the right substrate material involves considering various factors such as the operating frequency, temperature range, environmental conditions, flexibility requirements, and cost constraints of your project. Evaluate the key properties of each material and consult with PCB manufacturers or design experts to make an informed decision based on your specific needs.
Conclusion
Selecting the appropriate PCB substrate material is a critical step in designing and manufacturing reliable and high-performance electronic systems. By understanding the properties and characteristics of different substrate materials, such as FR-4, High Tg FR-4, Rogers 4003, polyimide, and Teflon, you can make an informed decision that meets the specific requirements of your project.
Consider factors such as frequency, speed, temperature range, flexibility, cost, and manufacturing complexity when choosing the right substrate material. Don’t hesitate to consult with PCB manufacturers or design experts to ensure the best possible outcome for your project.
By selecting the optimal PCB substrate material, you can enhance signal integrity, thermal management, and mechanical stability, ultimately leading to a more reliable and successful electronic product.
Leave a Reply