What are Aluminum PCBs?
Aluminum PCBs, also known as Metal Core PCBs (MCPCBs), are printed circuit boards that utilize an aluminum substrate instead of the traditional FR-4 material. The aluminum substrate serves as a heat sink, efficiently dissipating heat generated by the components mounted on the PCB. This unique property makes aluminum PCBs ideal for applications that require high thermal management, such as high-power LED lighting, automotive electronics, and power electronics.
Composition of Aluminum PCBs
Aluminum PCBs typically consist of three layers:
- Dielectric layer
- Aluminum substrate
- Copper layer
The dielectric layer is an electrically insulating material that separates the copper layer from the aluminum substrate. The most common dielectric materials used in aluminum PCBs are:
- Polyimide
- Epoxy
- Ceramic
The aluminum substrate is the core of the PCB, providing mechanical support and thermal dissipation. The copper layer is laminated on top of the dielectric layer and is used for creating the desired circuit pattern.
Advantages of Aluminum PCBs
Aluminum PCBs offer several advantages over traditional FR-4 PCBs:
- Excellent thermal management
- Aluminum’s high thermal conductivity allows for efficient heat dissipation
-
Reduces the need for additional heat sinks or cooling systems
-
Improved reliability
- Better thermal management leads to increased component lifespan
-
Reduced thermal stress on components
-
Lightweight and durable
- Aluminum is lighter than copper, resulting in a lighter overall PCB
-
Aluminum’s strength and rigidity provide enhanced durability
-
Cost-effective
- Eliminates the need for additional heat sinks, reducing overall system cost
- Simplified assembly process
Applications of Aluminum PCBs
Aluminum PCBs are used in various industries and applications that require efficient thermal management. Some common applications include:
High-Power LED Lighting
- LED spotlights and floodlights
- Automotive LED headlights
- LED street lighting
Automotive Electronics
- Engine control units (ECUs)
- Power inverters
- Battery management systems
Power Electronics
- Switching mode power supplies (SMPS)
- Motor drives
- Solar inverters
Industrial Controls
- Programmable logic controllers (PLCs)
- Human-machine interfaces (HMIs)
- Industrial sensors
Designing Aluminum PCBs
When designing aluminum PCBs, several factors need to be considered to ensure optimal performance and reliability.
Thermal Management
The primary purpose of using an aluminum substrate is to efficiently dissipate heat. To maximize thermal management, consider the following:
- Aluminum substrate thickness
- Thicker substrates provide better heat spreading
-
Typical thicknesses range from 0.8mm to 3.2mm
-
Dielectric layer thickness and material
- Thinner dielectric layers offer better thermal conductivity
-
Choose materials with high thermal conductivity, such as ceramic or high-performance epoxy
-
Copper layer thickness
- Thicker copper layers improve current carrying capacity and heat spreading
- Typical thicknesses range from 0.5oz to 4oz
Circuit Layout
When designing the circuit layout for an aluminum PCB, keep the following guidelines in mind:
- Component placement
- Place high-power components directly over the aluminum substrate for optimal heat dissipation
-
Avoid placing temperature-sensitive components near high-power components
-
Trace width and spacing
- Use wider traces for high-current paths to minimize resistance and improve heat dissipation
-
Maintain adequate spacing between traces to prevent electrical shorts and minimize crosstalk
-
Thermal vias
- Use thermal vias to transfer heat from the copper layer to the aluminum substrate
- Place thermal vias strategically around high-power components
Manufacturing Considerations
Aluminum PCBs require specialized manufacturing processes compared to traditional FR-4 PCBs. Some key considerations include:
- Dielectric layer application
- The dielectric layer must be applied uniformly to ensure proper insulation and thermal conductivity
-
Common application methods include lamination, screen printing, and anodizing
-
Copper layer bonding
- The copper layer must be securely bonded to the dielectric layer to prevent delamination
-
Bonding methods include direct bonding, adhesive bonding, and plating
-
Aluminum substrate preparation
- The aluminum substrate must be cleaned and treated to ensure proper adhesion and prevent oxidation
- Surface treatments include degreasing, etching, and anodizing
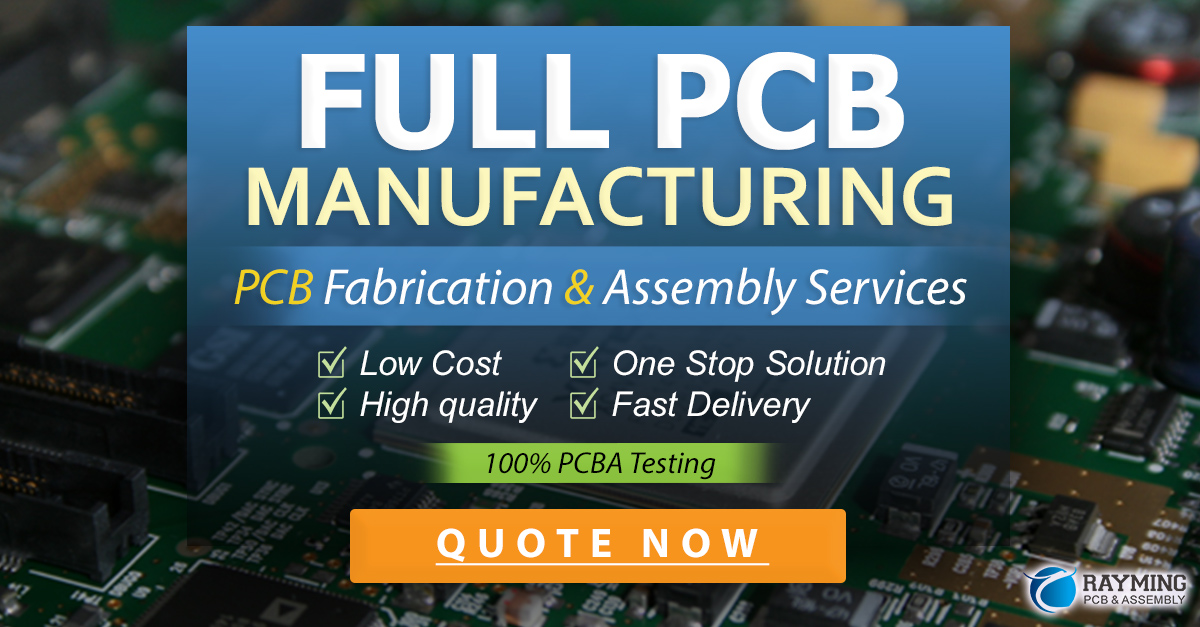
Comparing Aluminum PCBs to Traditional FR-4 PCBs
When deciding between aluminum PCBs and traditional FR-4 PCBs, it’s essential to understand their differences and suitability for specific applications.
Feature | Aluminum PCBs | FR-4 PCBs |
---|---|---|
Thermal conductivity | High (150-200 W/mK) | Low (0.3-0.4 W/mK) |
Dielectric constant | 4.5-10 | 4.2-4.5 |
Mechanical strength | High | Moderate |
Weight | Lightweight | Heavier |
Cost | Higher | Lower |
Aluminum PCBs are the preferred choice when:
- Efficient thermal management is critical
- High reliability is required in harsh environments
- Weight reduction is a priority
FR-4 PCBs are suitable when:
- Thermal management is not a primary concern
- Cost is a limiting factor
- Dielectric properties are essential
Frequently Asked Questions (FAQ)
-
Q: Can aluminum PCBs be used for high-frequency applications?
A: Yes, aluminum PCBs can be used for high-frequency applications. However, the dielectric layer material must be carefully selected to minimize signal loss and maintain the desired dielectric properties. -
Q: Are aluminum PCBs more expensive than FR-4 PCBs?
A: Yes, aluminum PCBs are generally more expensive than FR-4 PCBs due to the specialized manufacturing processes and materials required. However, the added cost can be justified by the improved thermal management and reliability in applications that demand these features. -
Q: Can aluminum PCBs be soldered using standard methods?
A: Yes, aluminum PCBs can be soldered using standard methods such as reflow soldering or wave soldering. However, it’s essential to use solder alloys with a higher melting point to prevent damage to the aluminum substrate. -
Q: How do I select the appropriate aluminum substrate thickness for my application?
A: The aluminum substrate thickness should be selected based on the thermal management requirements of your application. Thicker substrates provide better heat spreading but may increase the overall PCB Thickness. Consult with your PCB manufacturer to determine the optimal thickness for your specific application. -
Q: Are there any limitations on the minimum trace width and spacing for aluminum PCBs?
A: The minimum trace width and spacing for aluminum PCBs are generally similar to those of FR-4 PCBs. However, it’s essential to consider the specific capabilities of your chosen PCB manufacturer and the dielectric layer material being used. Always consult with your manufacturer to ensure your design meets their manufacturing guidelines.
Conclusion
Aluminum PCBs offer a unique solution for applications that require efficient thermal management and high reliability. By utilizing an aluminum substrate as a heat sink, these PCBs can effectively dissipate heat generated by components, leading to improved performance and extended component lifespan. While aluminum PCBs may have a higher initial cost compared to traditional FR-4 PCBs, the benefits they provide can outweigh the added expense in applications where thermal management is critical.
When designing aluminum PCBs, it’s crucial to consider factors such as thermal management, circuit layout, and manufacturing processes to ensure optimal performance and reliability. By carefully selecting the appropriate substrate thickness, dielectric material, and copper layer thickness, designers can create aluminum PCBs that meet the specific requirements of their applications.
As technology continues to advance and the demand for high-performance electronics grows, aluminum PCBs will likely play an increasingly important role in various industries. From high-power LED lighting to automotive electronics and beyond, aluminum PCBs offer a reliable and efficient solution for managing heat and ensuring the long-term reliability of electronic systems.
Leave a Reply