What are Copper Defined Pads?
With copper defined pads (also known as non-solder mask defined or NSMD pads), the copper features on the outer layer of the PCB determine the size and shape of the exposed pads. The soldermask layer is then applied on top, with openings that are typically larger than the copper pads underneath.
The key characteristics of copper defined pads include:
- Copper features are larger than soldermask openings
- Soldermask overlaps the edges of the copper pads
- Copper etching process solely defines the pad edges
Copper defined pads are the traditional pad type and are still widely used today, especially for through-hole components and large SMT pads. However, they have some limitations for fine-pitch surface mount designs.
Advantages of Copper Defined Pads
Looser Soldermask Alignment Tolerances
One main advantage of copper defined pads is that the soldermask layer does not define the critical pad edges. This allows for looser registration tolerances between the copper and soldermask layers. If the soldermask opening is slightly misaligned, it will not affect the copper pad size or shape. Soldermask alignment is typically held to ±3 mil, while copper etching is controlled to ±1 mil or better.
Larger Solderable Area
With copper defined pads, the soldermask opening is larger than the copper pad. This exposes more of the copper area for soldering, which can improve solder joint strength. The extra solderable area is especially beneficial for large components or high-stress applications.
Easier Visual Inspection
Copper defined pads are often preferred for through-hole component pads and test point pads. The exposed copper annular ring around the drilled hole provides a visual reference for checking hole registration and plating quality. The oversized soldermask opening also makes it easier to inspect the solder fillet around leads after assembly.
Disadvantages of Copper Defined Pads
Potential for Solder Bridging
The main disadvantage of copper defined pads is the increased risk of solder bridges forming between adjacent pads. With excess exposed copper between pads, it is easier for solder to wick along the surface and short neighboring joints, especially for fine-pitch components. Proper soldermask dam sizing is critical to prevent bridging.
Reduced Pad Spacing
To allow adequate space for soldermask webbing between pads, the copper features must be pulled back from the pad edges. This reduces the usable pad area and limits how close pads can be placed. Copper defined pads are not suitable for ultra-fine pitch components below 0.5 mm.
Soldermask Coverage Variations
If the soldermask openings are too small or misregistered, they may overlap onto the pad surface and reduce the solderable area. Inconsistent soldermask coverage can lead to variations in solder joint shape and volume. The “solder steal” effect is another issue, where solder wicks under the soldermask at the pad edges and robs volume from the main joint.
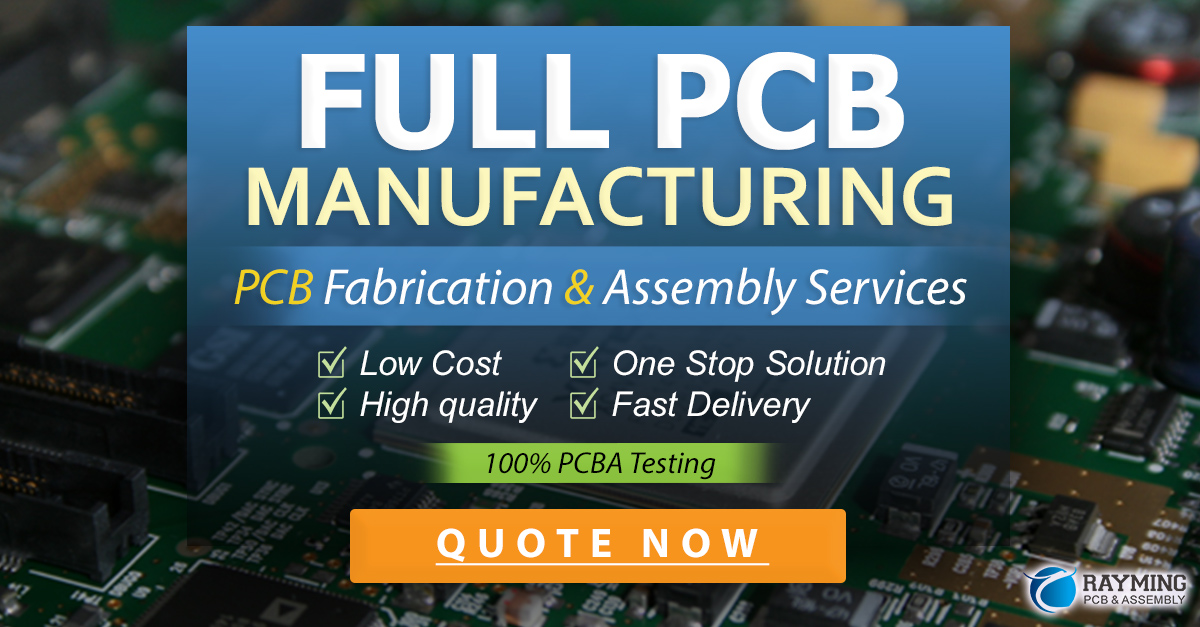
What are Soldermask Defined Pads?
Soldermask defined (SMD) pads, also referred to as solder mask defined or mask defined pads, use the openings in the solder resist layer to determine the final size and shape of the solderable pad surface. The underlying copper pad is etched larger, extending out beneath the soldermask. So the edges of the exposed copper area are defined solely by the soldermask opening.
The key attributes of soldermask defined pads are:
- Soldermask openings are smaller than copper pads
- Copper extends under soldermask at pad edges
- Soldermask etching process defines the solderable area
Soldermask defined pads have become increasingly popular in recent years, especially for fine-pitch surface mount designs. Most PCB design tools now include options for defining solder mask openings separately from copper pad shapes.
Advantages of Soldermask Defined Pads
Increased Pad Density
The main advantage of soldermask defined pads is the ability to achieve higher pad density. Because the pad edges are defined by the soldermask, there is no need for pullback between copper features. The space between pads is limited only by the soldermask web size and alignment tolerance, which is typically around 3-4 mils. This allows for finer pitch components and more compact PCB layouts.
More Consistent Solderable Area
With soldermask defined pads, the size and shape of the exposed copper is more consistent, as it is not affected by variations in the copper etching process. The Soldermask Thickness is also more uniform than copper thickness, so there is less variation in the solderable surface from pad to pad. This consistency can improve the reliability of solder joints, especially for small components.
Reduced Risk of Solder Bridging
Because the copper pads extend under the soldermask, there is less exposed copper between adjacent pads. This reduces the risk of solder bridging, as the solder is less likely to wick along the surface and short neighboring joints. The soldermask provides an effective barrier to prevent bridging, even at fine pitches.
Disadvantages of Soldermask Defined Pads
Tighter Soldermask Registration
The main disadvantage of soldermask defined pads is the need for tighter alignment between the copper and soldermask layers. If the soldermask openings are misregistered, they can overlap the pad edges and reduce the solderable area. In extreme cases, a misaligned opening can even create an open circuit if it falls off the pad entirely. Soldermask registration typically needs to be held to ±2 mil or better for fine-pitch designs.
Reduced Pad Strength
Because the copper pads are etched larger than the soldermask openings, there is less copper supporting the pad structure. This can reduce the mechanical strength of the pads, especially for larger components or high-stress applications. The unsupported copper at the pad edges is also more susceptible to lifting or peeling during rework.
Limited Annular Ring
For through-hole pads and vias, soldermask defined pads provide less annular ring around the drilled hole. The copper annular ring is the difference between the copper pad size and the hole size, and provides a margin for drill registration errors. With soldermask defined pads, the effective annular ring is limited by the soldermask opening size, not the copper pad size.
Choosing Between Copper and Soldermask Defined Pads
The choice between copper and soldermask defined pads depends on the specific requirements of your PCB design. Here are some guidelines to help you decide:
Factor | Copper Defined | Soldermask Defined |
---|---|---|
Pitch | >0.5 mm | <0.5 mm |
Density | Lower | Higher |
Soldermask Registration | ±3 mil | ±2 mil |
Solder Joint Consistency | Lower | Higher |
Solder Bridging Risk | Higher | Lower |
Pad Strength | Higher | Lower |
Annular Ring | Larger | Smaller |
In general, copper defined pads are better for larger components, through-hole designs, and high-reliability applications. Soldermask defined pads are preferred for fine-pitch surface mount designs, high-density layouts, and consistent solder joints.
It’s also possible to use a mix of copper and soldermask defined pads on the same PCB. For example, you could use soldermask defined for fine-pitch SMDs and copper defined for through-hole and test point pads. Most PCB design tools allow you to specify the pad type on a per-component or per-pad basis.
Frequently Asked Questions
What is the difference between copper and soldermask defined pads?
Copper defined pads use the copper features to determine the pad size and shape, while soldermask defined pads use the openings in the soldermask layer to define the exposed copper area. With copper defined pads, the soldermask opening is larger than the copper pad. With soldermask defined pads, the copper extends under the soldermask at the pad edges.
Which type of pad is better for fine-pitch components?
Soldermask defined pads are generally better for fine-pitch surface mount components, as they allow for higher pad density and more consistent solder joints. Copper defined pads require more space between pads for the soldermask webbing, which limits how close pads can be placed.
How do copper and soldermask defined pads affect solder bridging?
Copper defined pads have a higher risk of solder bridging, because there is more exposed copper between adjacent pads for solder to wick along. Soldermask defined pads reduce the risk of bridging, as the soldermask provides a barrier between pads to prevent solder wicking.
What are the soldermask registration requirements for each pad type?
Copper defined pads allow for looser soldermask registration, typically around ±3 mil, because the soldermask does not define the critical pad edges. Soldermask defined pads require tighter registration, usually ±2 mil or better, to ensure the openings are correctly aligned with the copper pads.
Can you mix copper and soldermask defined pads on the same PCB?
Yes, it is possible to use a mix of copper and soldermask defined pads on the same PCB, depending on the requirements of each component. For example, you could use soldermask defined pads for fine-pitch SMDs and copper defined pads for through-hole components and test points. Most PCB design tools support defining pad types individually.
Conclusion
Copper defined and soldermask defined pads are the two main methods for defining the exposed copper area on PCB pads. Copper defined pads offer advantages in terms of soldermask registration tolerances, solderable area, and visual inspection, but have limitations for fine-pitch designs and risk of solder bridging. Soldermask defined pads enable higher pad density, more consistent solder joints, and reduced bridging risk, but require tighter soldermask registration and have reduced pad strength.
When deciding between copper and soldermask defined pads, consider factors such as component pitch, pad density, soldermask registration capability, solder joint consistency requirements, and pad strength needs. A mix of both pad types can also be used to optimize the PCB design for different types of components and interconnects. By understanding the advantages and disadvantages of each approach, you can choose the best pad definition strategy to ensure the manufacturability, reliability, and performance of your PCB designs.
Leave a Reply