What is an MCPCB?
A Metal Core Printed Circuit Board (MCPCB) is a specialized type of PCB that has a metal core or base, usually made of aluminum, instead of the traditional FR-4 material. The metal core serves as a heat spreader, efficiently dissipating heat generated by the components mounted on the PCB. This makes MCPCBs ideal for applications that require high power density or generate significant amounts of heat, such as LED lighting, power electronics, and automotive systems.
Advantages of MCPCBs
- Excellent thermal management
- Improved reliability and longevity of components
- Reduced size and weight compared to traditional PCBs with separate heat sinks
- Enhanced mechanical stability and rigidity
- Suitable for high-power applications
Structure of an MCPCB
An MCPCB typically consists of three layers:
- Dielectric layer: An electrically insulating layer that is thermally conductive, usually made of a ceramic-filled polymer or epoxy material.
- Circuit layer: A thin layer of copper foil that is etched to form the desired circuit pattern.
- Metal core: A thick layer of metal, usually aluminum, that serves as a heat spreader and provides mechanical support.
Layer | Material | Thickness |
---|---|---|
Dielectric | Ceramic-filled polymer/epoxy | 0.1-0.3 mm |
Circuit | Copper foil | 0.035-0.07 mm |
Metal Core | Aluminum | 1.0-3.0 mm |
Dielectric Layer Materials
The dielectric layer is a critical component of an MCPCB, as it must provide electrical insulation while allowing efficient heat transfer from the circuit layer to the metal core. Some common dielectric materials used in MCPCBs include:
Material | Thermal Conductivity (W/mK) | Dielectric Constant | Dielectric Strength (kV/mm) |
---|---|---|---|
Al2O3 | 20-30 | 9.0-10.0 | 10-20 |
BN | 50-60 | 4.0-4.5 | 50-80 |
AlN | 150-200 | 8.0-9.0 | 15-20 |
Si3N4 | 60-90 | 7.0-8.0 | 20-30 |
Manufacturing Process
The manufacturing process for MCPCBs involves several steps:
- Preparing the metal core: The aluminum core is cleaned, degreased, and roughened to improve adhesion.
- Applying the dielectric layer: The dielectric material is applied to the metal core using techniques such as screen printing, lamination, or vapor deposition.
- Laminating the copper foil: A thin layer of copper foil is laminated onto the dielectric layer using heat and pressure.
- Patterning the circuit: The desired circuit pattern is etched onto the copper foil using photolithography and chemical etching processes.
- Applying solder mask and silkscreen: A solder mask is applied to protect the circuit, and a silkscreen layer is added for component labeling and identification.
- Mounting components: Electronic components are soldered onto the MCPCB using standard SMT or through-hole techniques.
MCPCB Design Considerations
When designing an MCPCB, several factors must be considered to ensure optimal performance and reliability:
- Thermal management: The layout and placement of components should be optimized to maximize heat dissipation and minimize thermal stress.
- Mechanical stress: The differences in thermal expansion between the metal core, dielectric layer, and copper foil can lead to mechanical stress and warping. Proper material selection and design techniques can help mitigate these issues.
- Electrical isolation: The dielectric layer must provide sufficient electrical isolation between the metal core and the circuit layer to prevent short circuits and leakage currents.
- Manufacturing constraints: The choice of materials, layer thicknesses, and minimum feature sizes should be compatible with the selected manufacturing process and equipment.
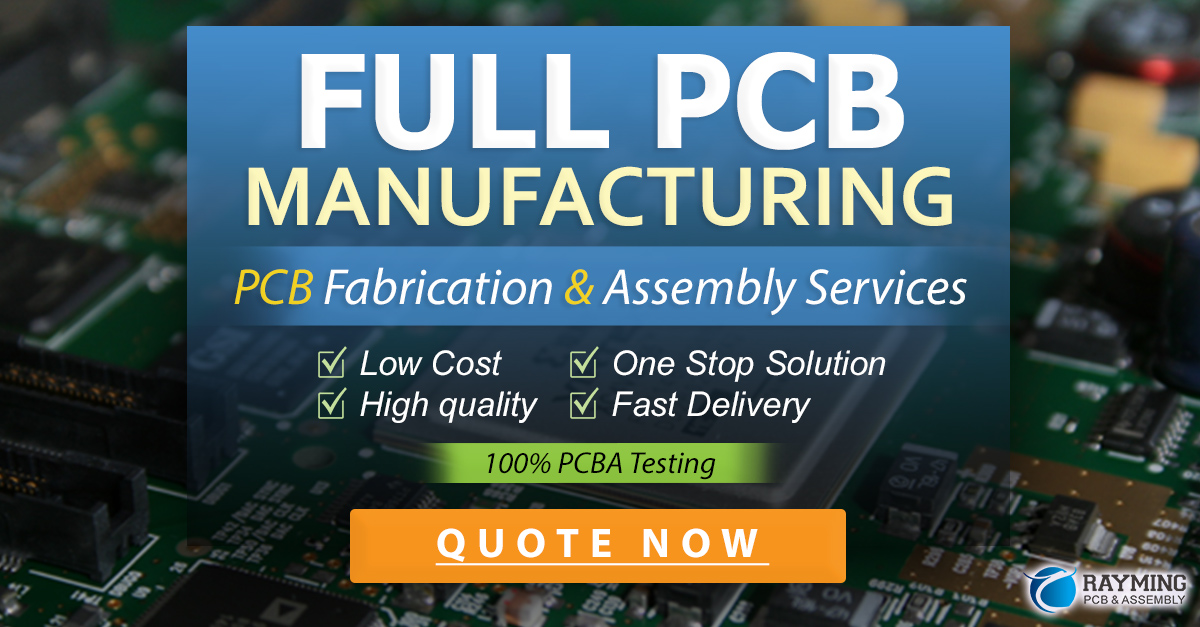
Applications of MCPCBs
MCPCBs are used in a wide range of applications that require efficient heat dissipation and high power density, such as:
- LED lighting: MCPCBs are widely used in LED lighting applications, as they help to dissipate the heat generated by the LEDs and improve their efficiency, brightness, and longevity.
- Power electronics: High-power electronic components such as MOSFETs, IGBTs, and rectifiers can be mounted on MCPCBs to improve their thermal performance and reliability.
- Automotive electronics: MCPCBs are used in various automotive applications, such as headlights, brake lights, engine control units, and power inverters for electric vehicles.
- Telecommunications: High-power RF and microwave components used in telecommunications equipment can benefit from the improved thermal management provided by MCPCBs.
- Industrial controls: MCPCBs are used in industrial control systems, such as motor drives, power supplies, and HVAC controls, where reliable operation in harsh environments is essential.
LED Lighting Applications
One of the most common applications for MCPCBs is LED lighting. LEDs generate significant amounts of heat, which must be efficiently dissipated to maintain their performance and longevity. By using MCPCBs, LED manufacturers can:
- Increase the power density of LED arrays
- Improve the efficiency and brightness of LEDs
- Extend the lifespan of LED components
- Reduce the size and weight of LED fixtures
- Simplify the design and manufacturing process
Application | Power Density (W/cm²) | Operating Temperature (°C) | Typical MCPCB Thickness (mm) |
---|---|---|---|
General Lighting | 0.5-1.0 | 60-80 | 1.0-1.6 |
Automotive Lighting | 1.0-2.0 | 80-100 | 1.6-2.0 |
High-Power Lighting | 2.0-5.0 | 100-120 | 2.0-3.0 |
Advantages of MCPCBs over Traditional PCBs
MCPCBs offer several advantages over traditional PCBs with separate heat sinks:
- Improved thermal performance: The metal core provides a direct thermal path for heat dissipation, reducing thermal resistance and improving overall thermal performance.
- Reduced size and weight: By integrating the heat sink into the PCB, MCPCBs eliminate the need for separate heat sinks, reducing the overall size and weight of the assembly.
- Simplified assembly process: MCPCBs simplify the assembly process by reducing the number of components and eliminating the need for thermal interface materials between the PCB and heat sink.
- Enhanced mechanical stability: The metal core provides additional mechanical support and rigidity to the PCB, reducing warping and improving overall stability.
- Cost-effective for high-volume production: While MCPCBs may have higher initial costs compared to traditional PCBs, they can be more cost-effective for high-volume production due to simplified assembly and reduced material costs.
Challenges and Limitations of MCPCBs
Despite their many advantages, MCPCBs also present some challenges and limitations:
- Limited design flexibility: The presence of the metal core can limit the routing and placement options for components, as well as the number of layers that can be incorporated into the PCB.
- Higher initial costs: The specialized materials and manufacturing processes used for MCPCBs can result in higher initial costs compared to traditional PCBs, particularly for low-volume production.
- Thermal expansion mismatch: The different thermal expansion coefficients of the metal core, dielectric layer, and copper foil can lead to mechanical stress and warping, which must be addressed through proper design and material selection.
- Limited dielectric material options: The choice of dielectric materials for MCPCBs is limited compared to traditional PCBs, as they must provide both electrical insulation and thermal conductivity.
- Manufacturing complexity: The manufacturing process for MCPCBs is more complex than traditional PCBs, requiring specialized equipment and expertise.
Future Trends and Developments
As the demand for high-power, miniaturized electronics continues to grow, MCPCBs are expected to play an increasingly important role in various industries. Some future trends and developments in MCPCB technology include:
- Advanced dielectric materials: Researchers are developing new dielectric materials with higher thermal conductivity and lower dielectric constants to improve the performance of MCPCBs.
- 3D printing techniques: Additive manufacturing techniques, such as 3D printing, are being explored for the fabrication of MCPCBs, enabling more complex geometries and customized designs.
- Integration with other technologies: MCPCBs are being integrated with other technologies, such as flexible electronics and embedded components, to create multifunctional, high-performance systems.
- Expanded applications: As MCPCB technology advances, it is expected to find new applications in areas such as renewable energy, aerospace, and medical devices.
- Sustainable materials and processes: There is a growing focus on developing sustainable materials and manufacturing processes for MCPCBs, such as using recycled aluminum and environmentally friendly dielectric materials.
FAQ
1. What is the main difference between MCPCBs and traditional PCBs?
The main difference between MCPCBs and traditional PCBs is the presence of a metal core, usually made of aluminum, which serves as a heat spreader. Traditional PCBs use a dielectric material, such as FR-4, as the base material and rely on separate heat sinks for thermal management.
2. Can MCPCBs be used for all types of electronic applications?
While MCPCBs offer excellent thermal management and are suitable for many high-power applications, they may not be the best choice for all electronic applications. MCPCBs have limitations in terms of design flexibility, layer count, and initial costs, which should be considered when selecting the appropriate PCB technology for a given application.
3. What are the most common dielectric materials used in MCPCBs?
Some of the most common dielectric materials used in MCPCBs include aluminum oxide (Al2O3), boron nitride (BN), aluminum nitride (AlN), and silicon nitride (Si3N4). These materials provide electrical insulation and thermal conductivity, allowing efficient heat transfer from the circuit layer to the metal core.
4. How do MCPCBs compare to traditional PCBs in terms of cost?
MCPCBs generally have higher initial costs compared to traditional PCBs due to the specialized materials and manufacturing processes involved. However, for high-volume production, MCPCBs can be more cost-effective due to simplified assembly and reduced material costs, as they eliminate the need for separate heat sinks and thermal interface materials.
5. What are some future trends and developments in MCPCB technology?
Future trends and developments in MCPCB technology include the development of advanced dielectric materials with higher thermal conductivity and lower dielectric constants, the use of 3D printing techniques for fabrication, integration with other technologies such as flexible electronics and embedded components, expansion into new application areas, and a focus on sustainable materials and manufacturing processes.
Leave a Reply