Introduction to PCB Solder Mask Opening (SMO)
Printed Circuit Boards (PCBs) are essential components in modern electronics, providing a platform for mounting and interconnecting electronic components. One critical aspect of PCB manufacturing is the application of a solder mask, which serves as a protective layer and helps to prevent short circuits during the soldering process. Solder Mask Opening (SMO) is a crucial step in the PCB fabrication process that involves creating openings in the solder mask layer to expose the copper pads and traces where components will be soldered.
In this comprehensive guide, we will delve into the intricacies of PCB Solder Mask Opening, covering its importance, techniques, design considerations, and best practices. Whether you are a PCB designer, manufacturer, or electronics enthusiast, understanding SMO is essential for creating high-quality and reliable PCBs.
What is PCB Solder Mask Opening?
PCB Solder Mask Opening refers to the process of creating openings or apertures in the solder mask layer of a PCB. The solder mask is a thin, protective layer applied over the copper traces and pads on a PCB, leaving only the areas where components will be soldered exposed. The primary purpose of SMO is to ensure proper solderability and prevent solder bridges or short circuits during the assembly process.
Functions of Solder Mask Opening
-
Exposing Solder Pads: SMO allows the copper pads, where components will be soldered, to be exposed and accessible for soldering.
-
Preventing Solder Bridging: By selectively exposing only the desired areas, SMO helps to prevent solder from inadvertently bridging between adjacent pads or traces.
-
Protecting Copper Traces: The solder mask layer covers and protects the copper traces on the PCB, preventing oxidation and providing insulation.
-
Improving Aesthetics: SMO contributes to the overall appearance of the PCB by creating a clean and professional look.
Solder Mask Opening Techniques
There are several techniques used to create solder mask openings on PCBs. Each method has its advantages and considerations. Let’s explore the most common SMO techniques:
Liquid Photo Imageable (LPI) Solder Mask
LPI solder mask is a photosensitive liquid material that is applied to the PCB surface and then exposed to UV light through a photomask. The exposed areas harden, while the unexposed areas remain soluble and can be washed away, creating the desired openings.
Advantages:
– High precision and resolution
– Suitable for fine-pitch components
– Excellent adhesion to the PCB surface
Considerations:
– Requires specialized equipment and materials
– Longer processing time compared to other methods
Direct Imaging (DI) Solder Mask
Direct Imaging involves using a high-resolution digital printer to directly apply the solder mask pattern onto the PCB surface. This method eliminates the need for a physical photomask, as the pattern is digitally controlled.
Advantages:
– Quick and efficient process
– Eliminates the need for photomasks
– Allows for rapid design changes
Considerations:
– Higher initial equipment costs
– May have limitations in achieving very fine resolutions
Screen Printing Solder Mask
Screen printing is a traditional method where the solder mask is applied through a fine mesh screen with the desired pattern. The solder mask is forced through the openings in the screen onto the PCB surface.
Advantages:
– Cost-effective for large-volume production
– Simple and straightforward process
Considerations:
– Lower resolution compared to LPI and DI methods
– Suitable for larger SMO sizes
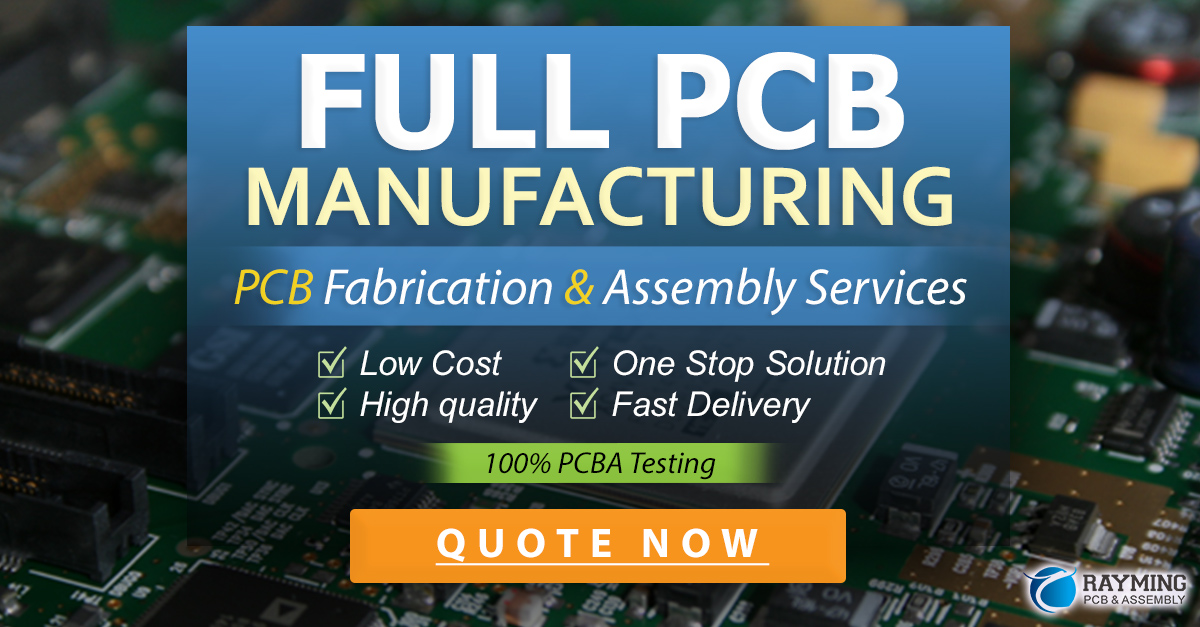
SMO Design Considerations
When designing solder mask openings for your PCB, there are several key factors to consider to ensure optimal results and manufacturability. Let’s discuss some essential SMO design considerations:
SMO Size and Clearance
The size of the solder mask opening should be carefully determined based on the component and pad sizes. It is crucial to provide sufficient clearance around the pads to accommodate the solder mask registration tolerances and ensure proper solderability.
Recommended SMO sizes:
| Component Type | SMO Size (mm) |
|—————-|—————|
| Chip Resistors | 0.1 – 0.2 |
| Chip Capacitors| 0.1 – 0.2 |
| SOT Packages | 0.2 – 0.3 |
| QFP Packages | 0.3 – 0.5 |
Solder Mask Expansion
Solder mask expansion refers to the amount of solder mask that extends beyond the copper pad. It is essential to provide adequate solder mask expansion to ensure proper adhesion and prevent solder bridging.
Recommended solder mask expansion:
| Copper Thickness | Solder Mask Expansion (mm) |
|——————|—————————-|
| 1 oz (35 μm) | 0.05 – 0.075 |
| 2 oz (70 μm) | 0.075 – 0.1 |
Solder Mask Slivers
Solder mask slivers refer to thin strips of solder mask between closely spaced pads or traces. It is important to avoid creating solder mask slivers that are too narrow, as they can be prone to peeling or damage during the manufacturing process.
Minimum recommended solder mask sliver width: 0.1 mm
Solder Mask Dams
Solder mask dams are small areas of solder mask placed between adjacent pads or traces to prevent solder bridging. They are particularly useful in high-density designs or when working with fine-pitch components.
Recommended solder mask dam width: 0.1 – 0.15 mm
SMO Best Practices
To ensure the best results and reliability of your PCBs, consider the following best practices when designing and manufacturing solder mask openings:
-
Consult with your PCB Manufacturer: Engage with your PCB manufacturer early in the design process to discuss their specific SMO capabilities, guidelines, and recommendations.
-
Use Appropriate SMO Sizes: Follow the recommended SMO sizes based on the component type and package to ensure proper solderability and prevent issues like solder bridging or insufficient solder joint formation.
-
Maintain Consistent Solder Mask Expansion: Ensure consistent solder mask expansion around pads and traces to promote uniform adhesion and prevent solder mask lifting or peeling.
-
Avoid Narrow Solder Mask Slivers: Minimize the occurrence of narrow solder mask slivers, as they can be fragile and prone to damage during manufacturing or assembly.
-
Implement Solder Mask Dams: Utilize solder mask dams where necessary to prevent solder bridging between closely spaced pads or traces.
-
Conduct Design Rule Checks (DRC): Perform thorough DRC to identify any SMO design violations or potential issues before finalizing your PCB layout.
-
Verify SMO Quality: Inspect the solder mask openings on the manufactured PCBs to ensure they meet the specified dimensions, alignment, and quality standards.
Frequently Asked Questions (FAQ)
-
What is the purpose of solder mask opening on PCBs?
The purpose of solder mask opening is to expose the copper pads and areas where components will be soldered while protecting the rest of the PCB surface from solder bridging and short circuits. -
What are the most common solder mask opening techniques?
The most common solder mask opening techniques include Liquid Photo Imageable (LPI) solder mask, Direct Imaging (DI) solder mask, and screen printing solder mask. -
How do I determine the appropriate solder mask opening size for my components?
The appropriate solder mask opening size depends on the component type and package. Consult the component manufacturer’s datasheet and follow the recommended SMO sizes based on the component size and pitch. -
What is solder mask expansion, and why is it important?
Solder mask expansion refers to the amount of solder mask that extends beyond the copper pad. It is important to provide adequate solder mask expansion to ensure proper adhesion and prevent solder mask lifting or peeling. -
Can I use solder mask dams to prevent solder bridging?
Yes, solder mask dams are an effective way to prevent solder bridging between closely spaced pads or traces. By placing small areas of solder mask between adjacent pads, you can minimize the risk of solder bridging during the assembly process.
Conclusion
PCB Solder Mask Opening is a critical aspect of PCB manufacturing that plays a vital role in ensuring the quality, reliability, and functionality of electronic assemblies. By understanding the techniques, design considerations, and best practices associated with SMO, you can create PCBs that meet the highest standards of solderability and performance.
Remember to collaborate closely with your PCB manufacturer, follow recommended guidelines, and conduct thorough design reviews to optimize your SMO design. With the knowledge gained from this comprehensive guide, you are well-equipped to navigate the intricacies of PCB Solder Mask Opening and create successful PCB designs.
Leave a Reply