Introduction to PCB repair and Testing
Printed circuit boards (PCBs) are the foundation of modern electronics. They provide the electrical connections and mechanical support for electronic components in devices ranging from smartphones and laptops to industrial control systems and medical equipment. However, like any complex system, PCBs can fail due to manufacturing defects, environmental factors, or normal wear and tear.
PCB repair is the process of identifying and fixing these issues to restore the functionality of the circuit board. This can involve a range of techniques, from simple visual inspections to advanced diagnostic tools and specialized repair equipment. One key aspect of PCB repair is testing – using specialized equipment to identify faults and verify that repairs have been successful.
In this article, we’ll explore the world of PCB repair and testing, with a particular focus on circuit board testers and methods that are conducive to efficient and effective repairs. We’ll cover the basics of PCB Construction and common failure modes, the types of testers and diagnostic tools available, and best practices for PCB repair and maintenance.
Understanding PCB Construction and Common Failure Modes
PCB Construction Basics
Before diving into PCB repair and testing, it’s important to understand the basics of how PCBs are constructed. A typical PCB consists of several layers:
- Substrate: The base material, usually made of fiberglass or other insulating material
- Copper layers: Thin sheets of copper foil that are etched to create the electrical connections between components
- Solder mask: A protective coating that covers the copper layers, leaving only the pads and other connection points exposed
- Silkscreen: Text and graphics printed on the surface of the board to identify components and provide other information
The copper layers are the most critical part of the PCB, as they provide the electrical pathways that allow signals and power to flow between components. These layers are typically arranged in a stack, with insulating material between them to prevent short circuits.
Common PCB Failure Modes
PCBs can fail in a variety of ways, depending on the specific design, manufacturing process, and operating environment. Some of the most common failure modes include:
- Open circuits: A break in a copper trace or connection point, preventing current from flowing
- Short circuits: An unintended connection between two or more traces or components, often caused by solder bridges or conductive debris
- Component failures: Malfunctions in individual components, such as resistors, capacitors, or integrated circuits
- Delamination: Separation of the layers of the PCB, often due to thermal stress or moisture ingress
- Corrosion: Degradation of the copper traces or other metal parts due to exposure to moisture, chemicals, or other corrosive agents
Identifying the specific failure mode is a critical first step in PCB repair, as it guides the selection of diagnostic tools and repair techniques.
Types of Circuit Board Testers and Diagnostic Tools
To identify faults and verify repairs, PCB technicians rely on a range of specialized testers and diagnostic tools. These can be broadly categorized into several types:
Multimeters
Multimeters are basic but essential tools for measuring voltage, current, and resistance. They can be used to check for open or short circuits, verify power supply voltages, and test individual components.
Oscilloscopes
Oscilloscopes display waveforms of electrical signals over time, allowing technicians to analyze the timing and shape of signals. They are particularly useful for debugging digital circuits and identifying issues with signal integrity.
Logic Analyzers
Logic analyzers capture and display digital signals from multiple channels simultaneously. They are used to debug complex digital systems, such as microprocessors and field-programmable gate arrays (FPGAs).
In-Circuit Testers (ICTs)
ICTs are automated testing systems that use a bed-of-nails fixture to make electrical contact with test points on the PCB. They can rapidly test for open and short circuits, component values, and other basic functionality.
Tester Type | Key Features | Typical Applications |
---|---|---|
Multimeter | Measures voltage, current, and resistance | Basic continuity and component testing |
Oscilloscope | Displays waveforms of electrical signals over time | Debugging digital circuits and signal integrity issues |
Logic Analyzer | Captures and displays digital signals from multiple channels | Debugging complex digital systems, such as microprocessors and FPGAs |
In-Circuit Tester (ICT) | Automated testing using bed-of-nails fixture | Rapid testing for opens, shorts, and component values |
Boundary Scan Testers
Boundary scan is a testing methodology that uses dedicated test circuitry built into integrated circuits to test the interconnections between them. Boundary scan testers can identify faults that are difficult or impossible to detect with other methods, such as shorts between pins on a ball grid array (BGA) package.
X-Ray Inspection Systems
X-ray inspection systems use high-energy radiation to create images of the internal structure of PCBs. They are particularly useful for inspecting solder joints and other hidden features that are not visible to the naked eye.
Thermal Imaging Cameras
Thermal imaging cameras detect infrared radiation to create images that show the temperature distribution across a PCB. They can be used to identify hot spots caused by short circuits, overloaded components, or other thermal issues.
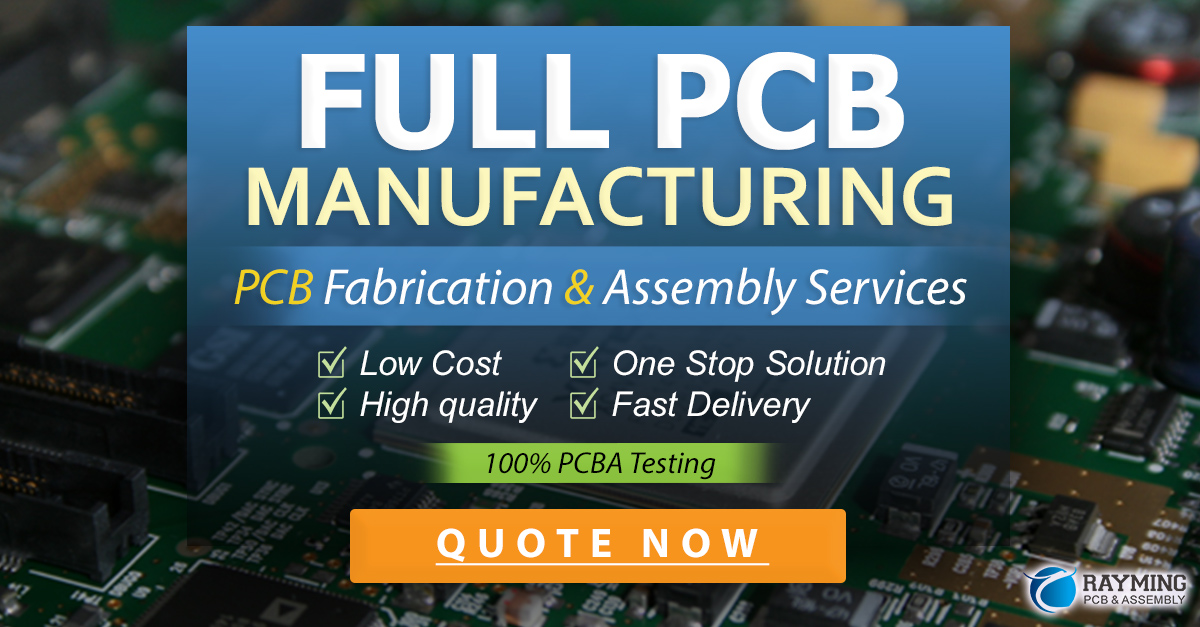
Best Practices for PCB Repair and Maintenance
Proper Handling and Storage
PCBs are delicate and sensitive to environmental factors such as moisture, static electricity, and physical damage. To minimize the risk of damage during handling and storage:
- Use anti-static bags, containers, and work surfaces to prevent electrostatic discharge (ESD) damage
- Store PCBs in a cool, dry place away from direct sunlight and sources of moisture
- Handle PCBs by the edges to avoid touching sensitive components or connectors
Regular Inspection and Cleaning
Regular visual inspection and cleaning can help identify potential issues before they lead to failures. Some key steps include:
- Visually inspecting PCBs for signs of damage, corrosion, or contamination
- Using compressed air or specialized cleaning solutions to remove dust, dirt, and other debris
- Checking for loose or damaged connectors, components, or mounting hardware
Proper Repair Techniques
When a fault is identified, it’s important to use the appropriate repair techniques to ensure a reliable and long-lasting fix. Some key considerations include:
- Using the correct tools and materials for the specific repair, such as soldering irons, solder, and flux
- Following industry standards and manufacturer guidelines for repair procedures
- Verifying repairs with appropriate testing methods to ensure functionality and reliability
Documentation and Traceability
Proper documentation is essential for tracking repairs, identifying recurring issues, and maintaining traceability for quality control and regulatory compliance. Key elements of documentation include:
- Detailed repair logs that include the date, technician, fault description, and repair actions taken
- Photographs or other visual records of the PCB before and after repair
- Unique identifiers, such as serial numbers or barcodes, to link the physical PCB to its documentation
FAQ
What are the most common causes of PCB failures?
The most common causes of PCB failures include:
- Manufacturing defects, such as incorrect component placement or solder bridges
- Environmental factors, such as moisture, temperature extremes, and vibration
- User-induced damage, such as physical impact or electrostatic discharge (ESD)
- Component failures due to aging, overheating, or electrical overstress
What safety precautions should be taken when repairing PCBs?
When repairing PCBs, it’s important to take safety precautions to protect yourself and the equipment:
- Use appropriate personal protective equipment (PPE), such as safety glasses and ESD-safe gloves
- Ensure proper ventilation when using solvents or other chemicals
- Follow manufacturer guidelines and industry standards for safe handling and repair procedures
- Disconnect power sources and discharge capacitors before beginning repairs
Can all PCB faults be repaired, or are some boards beyond repair?
While many PCB faults can be repaired, there are some cases where the board may be beyond repair:
- Severe physical damage, such as broken substrates or extensively corroded copper traces
- Widespread delamination or other structural failures
- Obsolete or discontinued components that cannot be sourced for replacement
In these cases, it may be more cost-effective to replace the entire PCB rather than attempting a repair.
How can I choose the right circuit board tester for my needs?
Choosing the right circuit board tester depends on several factors:
- The type of PCBs you will be testing (analog, digital, mixed-signal, etc.)
- The specific faults you need to detect (opens, shorts, component failures, etc.)
- The level of automation and throughput required for your testing process
- Your budget and available workspace
It’s often helpful to consult with experienced technicians or equipment manufacturers to determine the best tester for your specific application.
What role does testing play in the overall PCB repair process?
Testing is a critical component of the PCB repair process, serving several key functions:
- Identifying the specific fault or failure mode to guide repair actions
- Verifying that repairs have been successful and the PCB is functioning correctly
- Ensuring the reliability and longevity of the repaired PCB
- Providing documentation and traceability for quality control and regulatory compliance
Effective testing requires a combination of the right equipment, procedures, and expertise to ensure accurate and reliable results.
Conclusion
PCB repair and testing are essential skills for anyone working with electronic systems. By understanding the basics of PCB construction, common failure modes, and the tools and techniques used for diagnosis and repair, technicians can efficiently and effectively maintain and restore the functionality of these critical components.
From basic multimeters to advanced boundary scan testers and X-ray inspection systems, there is a wide range of equipment available to suit different applications and budgets. By following best practices for handling, inspection, repair, and documentation, technicians can ensure the reliability and longevity of repaired PCBs.
As electronic systems continue to become more complex and integrated, the importance of effective PCB repair and testing will only continue to grow. By staying up-to-date with the latest tools, techniques, and standards, technicians can position themselves to meet the evolving challenges of this dynamic field.
Leave a Reply