Introduction to Copper PCB
Copper is a vital component in the manufacturing of printed circuit boards (PCBs). It is the primary conductive material used in PCB Fabrication due to its excellent electrical conductivity, thermal conductivity, and mechanical properties. The use of copper in PCBs has a significant impact on the overall performance, reliability, and cost of the final product. In this article, we will explore the various aspects of copper PCB and how it influences PCB Manufacturing.
Properties of Copper
Copper is a chemical element with the symbol Cu and atomic number 29. It is a soft, malleable, and ductile metal with a distinctive reddish-orange color. Some of the key properties of copper that make it an ideal choice for PCB manufacturing include:
- High electrical conductivity
- Good thermal conductivity
- Excellent ductility and malleability
- Corrosion resistance
- Easy to solder
Role of Copper in PCB Manufacturing
Copper plays a crucial role in the manufacturing of PCBs. It is used to create the conductive traces, pads, and vias that allow electrical signals to flow between components on the board. The thickness and width of the copper traces determine the current-carrying capacity and the impedance of the circuit.
Types of Copper Used in PCB Manufacturing
There are two main types of copper used in PCB manufacturing: electrodeposited copper (ED copper) and rolled copper.
Electrodeposited Copper (ED Copper)
ED copper is the most commonly used type of copper in PCB manufacturing. It is produced by electroplating a thin layer of copper onto a substrate material, such as fiberglass or epoxy. The thickness of the ED copper layer can range from 0.5 oz to 2 oz per square foot (17 to 68 µm).
Advantages of ED Copper:
– Cost-effective
– Uniform thickness
– Good adhesion to the substrate
– Suitable for fine-pitch designs
Disadvantages of ED Copper:
– Limited current-carrying capacity
– Higher resistance compared to rolled copper
Rolled Copper
Rolled copper, also known as wrought copper, is produced by mechanically rolling copper foil to the desired thickness. The thickness of rolled copper can range from 0.5 oz to 5 oz per square foot (17 to 170 µm).
Advantages of Rolled Copper:
– Higher current-carrying capacity
– Lower resistance compared to ED copper
– Better thermal conductivity
– Suitable for high-power applications
Disadvantages of Rolled Copper:
– More expensive than ED copper
– Difficulty in achieving uniform thickness
– Limited availability in thinner gauges
Copper Thickness and Weight
The thickness and weight of the copper layer in a PCB are critical factors that influence the performance and cost of the board. Copper thickness is typically measured in ounces per square foot (oz/ft²) or micrometers (µm).
Standard Copper Weights
Copper Weight (oz/ft²) | Thickness (µm) |
---|---|
0.5 | 17 |
1.0 | 34 |
2.0 | 68 |
3.0 | 102 |
4.0 | 136 |
5.0 | 170 |
Choosing the Right Copper Thickness
The choice of copper thickness depends on several factors, including:
- Current-carrying requirements
- Signal integrity
- Thermal management
- Manufacturing constraints
- Cost considerations
Thicker copper layers offer better current-carrying capacity and thermal management but increase the overall cost and weight of the PCB. Thinner copper layers are more cost-effective and suitable for fine-pitch designs but have limited current-carrying capacity and higher resistance.
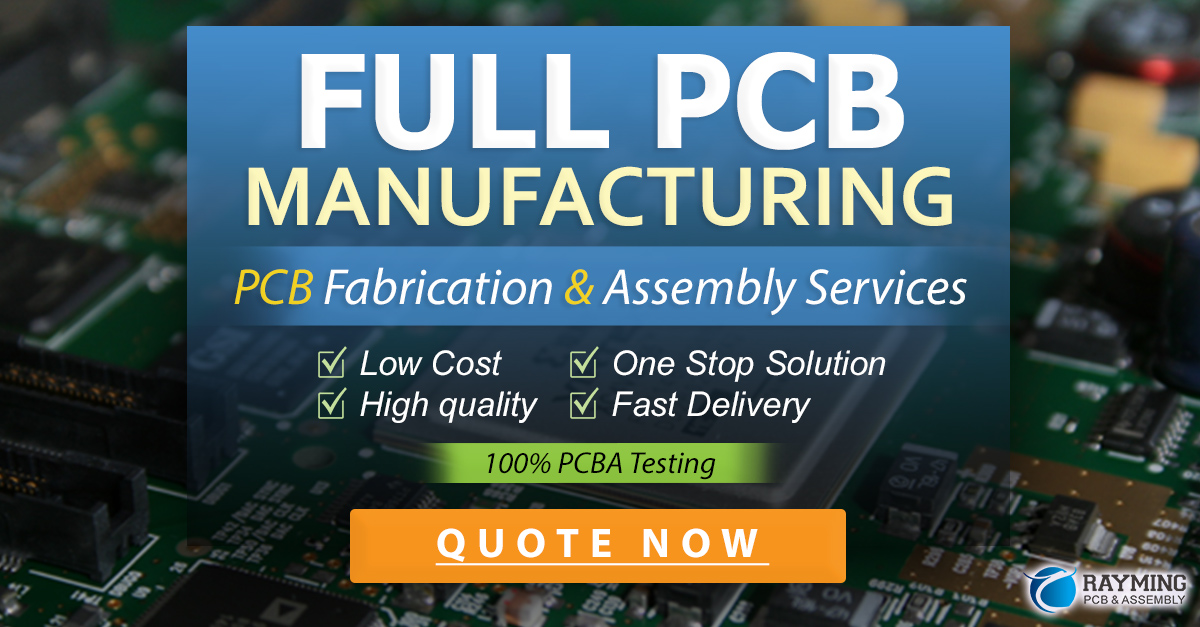
Copper Foil Surface Treatments
Copper foil used in PCB manufacturing can undergo various surface treatments to enhance its properties and improve the adhesion between the copper and the substrate. Some common surface treatments include:
Electrodeposited Copper Surface Treatments
- Micro-etching: A chemical process that roughens the surface of the copper to improve adhesion.
- Brass coating: A thin layer of brass is electroplated onto the copper surface to prevent oxidation and enhance solderability.
- Zinc coating: A thin layer of zinc is electroplated onto the copper surface to improve shelf life and prevent oxidation.
Rolled Copper Surface Treatments
- Passivation: A chemical process that forms a thin, protective layer on the copper surface to prevent oxidation.
- Roughening: Mechanical or chemical processes that increase the surface roughness of the copper to improve adhesion.
- Bonding treatments: Various treatments, such as black oxide or brown oxide, that enhance the bonding between the copper and the substrate.
Copper Trace Design Considerations
The design of copper traces in a PCB is critical for ensuring proper signal integrity, current-carrying capacity, and thermal management. Some key considerations when designing copper traces include:
Trace Width and Thickness
The width and thickness of copper traces determine their current-carrying capacity and impedance. Wider and thicker traces can carry more current and have lower resistance but occupy more space on the PCB. Narrower and thinner traces are more space-efficient but have limited current-carrying capacity and higher resistance.
Trace Spacing
The spacing between copper traces, also known as the trace pitch, is important for preventing signal interference and ensuring proper insulation. The minimum trace spacing depends on the manufacturing capabilities and the voltage requirements of the circuit.
Copper Pour and Ground Planes
Copper pour and ground planes are large areas of copper that provide a low-impedance return path for electrical currents and help in shielding sensitive signals. They also contribute to the thermal management of the PCB by dissipating heat more efficiently.
PCB Manufacturing Process with Copper
The manufacturing process of a PCB involves several steps that utilize copper foil. A simplified overview of the process is as follows:
- Substrate preparation: The base substrate material, such as fiberglass or epoxy, is cut to the desired size and shape.
- Copper foil lamination: Copper foil is laminated onto the substrate using heat and pressure.
- Drilling: Holes are drilled through the copper-clad substrate for component leads and vias.
- Patterning: The desired circuit pattern is transferred onto the copper layer using photolithography or screen printing techniques.
- Etching: The unwanted copper is etched away, leaving behind the desired circuit pattern.
- Plating: Additional copper, and sometimes other metals like gold or silver, may be plated onto the circuit pattern to improve conductivity and solderability.
- Solder mask application: A protective solder mask layer is applied over the copper traces, leaving exposed areas for component soldering.
- Surface finish application: A surface finish, such as HASL, ENIG, or OSP, is applied to the exposed copper areas to prevent oxidation and enhance solderability.
- Silkscreen printing: Text and symbols are printed onto the PCB for component identification and assembly guidance.
- Final inspection and testing: The completed PCB undergoes visual inspection and electrical testing to ensure proper functionality.
Challenges and Innovations in Copper PCB Manufacturing
As the demand for smaller, faster, and more complex PCBs continues to grow, copper PCB manufacturing faces several challenges and opportunities for innovation.
Challenges
- Miniaturization: As components and feature sizes shrink, the manufacturing of fine-pitch copper traces becomes more challenging.
- Signal integrity: Higher frequencies and faster data rates require careful design and control of copper traces to maintain signal integrity.
- Thermal management: Increased power densities and smaller form factors make thermal management more difficult, requiring innovative copper trace designs and materials.
- Cost pressures: The competitive nature of the electronics industry demands cost-effective PCB manufacturing solutions while maintaining high quality and reliability.
Innovations
- High-Density Interconnect (HDI): HDI technology enables the creation of finer pitch copper traces and smaller vias, allowing for higher component density and improved signal integrity.
- Embedded copper: Embedding copper traces within the substrate material can help reduce PCB Thickness, improve signal integrity, and enhance thermal management.
- Advanced surface finishes: The development of new surface finishes, such as immersion silver and electroless palladium, offers improved solderability and reliability compared to traditional finishes like HASL and ENIG.
- 3D printing: The emergence of 3D printing technologies for PCB manufacturing, such as selective laser sintering (SLS) and inkjet printing, could enable the rapid prototyping and production of complex copper trace designs.
Frequently Asked Questions (FAQ)
- What is the difference between ED copper and rolled copper in PCB manufacturing?
-
ED copper is electrodeposited onto the substrate and has a uniform thickness, while rolled copper is mechanically rolled to the desired thickness. Rolled copper has a higher current-carrying capacity and lower resistance compared to ED copper.
-
How does copper thickness affect PCB performance?
-
Thicker copper layers offer better current-carrying capacity and thermal management but increase the overall cost and weight of the PCB. Thinner copper layers are more cost-effective and suitable for fine-pitch designs but have limited current-carrying capacity and higher resistance.
-
What are some common surface treatments for copper foil in PCB manufacturing?
-
Common surface treatments for copper foil include micro-etching, brass coating, zinc coating, passivation, roughening, and bonding treatments like black oxide or brown oxide. These treatments enhance the properties of the copper and improve adhesion between the copper and the substrate.
-
Why are copper pour and ground planes important in PCB design?
-
Copper pour and ground planes provide a low-impedance return path for electrical currents and help in shielding sensitive signals. They also contribute to the thermal management of the PCB by dissipating heat more efficiently.
-
What are some innovations in copper PCB manufacturing?
- Some innovations in copper PCB manufacturing include High-Density Interconnect (HDI) technology, embedded copper, advanced surface finishes, and 3D printing technologies like selective laser sintering (SLS) and inkjet printing.
Conclusion
Copper is an essential material in PCB manufacturing, playing a vital role in the performance, reliability, and cost of the final product. Understanding the properties of copper, the different types of copper used in PCB manufacturing, and the design considerations for copper traces is crucial for creating high-quality and cost-effective PCBs.
As the electronics industry continues to evolve, copper PCB manufacturing faces challenges in miniaturization, signal integrity, thermal management, and cost pressures. However, innovations such as HDI technology, embedded copper, advanced surface finishes, and 3D printing offer exciting opportunities for the future of copper PCB manufacturing.
By staying informed about the latest developments and best practices in copper PCB manufacturing, PCB designers and manufacturers can create innovative, high-performance products that meet the ever-growing demands of the electronics industry.
Leave a Reply