Introduction to DFM-aided PCB Fabrication
Design for Manufacturability (DFM) is a methodology that optimizes the design of printed circuit boards (PCBs) to ensure they can be efficiently and reliably manufactured. By incorporating DFM principles early in the design process, PCB designers can create boards that are easier to fabricate, assemble, test, and repair. This leads to a range of benefits, including reduced costs, improved quality, faster time-to-market, and increased product reliability.
In this article, we will explore nine key advantages of DFM-aided PCB fabrication, highlighting how this approach can streamline the manufacturing process and deliver superior results.
Advantage 1: Reduced Manufacturing Costs
One of the primary benefits of DFM-aided PCB fabrication is the potential for significant cost savings. By designing boards with manufacturability in mind, designers can minimize the need for expensive materials, complex processes, and specialized equipment. Some key cost-saving strategies include:
- Choosing standard component sizes and packages
- Minimizing the number of layers in the PCB Stack-up
- Optimizing trace widths and spacings for ease of fabrication
- Avoiding unnecessary features such as blind or buried vias
By simplifying the design and aligning it with the capabilities of the manufacturing process, DFM can help reduce both material and labor costs, resulting in a more cost-effective end product.
Advantage 2: Improved PCB Quality and Reliability
DFM-aided PCB fabrication also contributes to higher quality and more reliable boards. By following DFM guidelines, designers can ensure that their PCBs are well-suited to the manufacturing process, minimizing the risk of defects and failures. Some key quality and reliability benefits include:
- Reduced risk of short circuits and open connections
- Improved signal integrity and power distribution
- Enhanced mechanical stability and durability
- Better thermal management and heat dissipation
By creating PCBs that are more robust and reliable, DFM can help reduce the incidence of field failures and warranty claims, ultimately improving customer satisfaction and brand reputation.
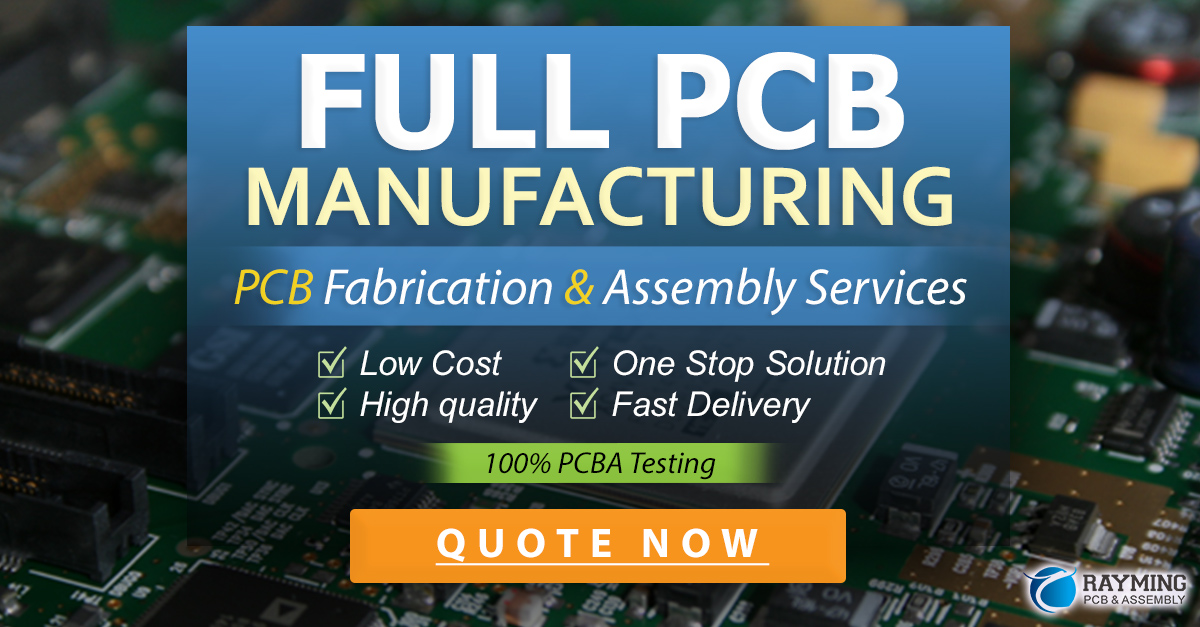
Advantage 3: Faster Time-to-Market
In today’s fast-paced business environment, getting products to market quickly is essential for staying ahead of the competition. DFM-aided PCB fabrication can help accelerate the development process by streamlining the transition from design to manufacturing. Some key time-saving benefits include:
- Reduced need for design revisions and rework
- Faster prototype development and testing
- Smoother handoff between design and manufacturing teams
- More efficient production ramp-up and volume scaling
By minimizing delays and interruptions in the manufacturing process, DFM can help companies bring their products to market faster, capitalizing on new opportunities and maximizing revenue potential.
Advantage 4: Enhanced Design Flexibility and Innovation
While DFM emphasizes adherence to manufacturing constraints, it can also foster greater design flexibility and innovation. By understanding the capabilities and limitations of the fabrication process, designers can make informed decisions about how to implement new features and functionalities. Some key benefits of DFM for design innovation include:
- Ability to incorporate advanced technologies such as HDI and embedded components
- Opportunities to explore alternative materials and processes
- Improved collaboration between design and manufacturing teams
- Greater freedom to experiment with novel form factors and packaging solutions
By providing a framework for pushing the boundaries of what is possible in PCB design, DFM can help companies develop more innovative and differentiated products that stand out in the marketplace.
Advantage 5: Reduced Environmental Impact
DFM-aided PCB fabrication can also contribute to more sustainable and eco-friendly manufacturing practices. By optimizing designs for manufacturability, companies can reduce waste, conserve resources, and minimize their environmental footprint. Some key environmental benefits of DFM include:
- Reduced material consumption and waste generation
- Lower energy and water usage in the manufacturing process
- Fewer toxic chemicals and hazardous substances
- Easier recycling and disposal of end-of-life products
By aligning PCB design with environmental best practices, DFM can help companies meet their sustainability goals and comply with increasingly stringent regulations.
Advantage 6: Improved Supply Chain Management
DFM-aided PCB fabrication can also streamline supply chain management by fostering greater collaboration and communication between designers, manufacturers, and suppliers. By involving all stakeholders early in the design process, companies can ensure that everyone is working towards the same goals and using compatible processes and materials. Some key supply chain benefits of DFM include:
- Better alignment between design specifications and supplier capabilities
- Reduced risk of component obsolescence and supply disruptions
- Improved inventory management and just-in-time delivery
- Greater flexibility to adapt to changing market conditions and customer requirements
By creating a more transparent and collaborative supply chain, DFM can help companies optimize their operations, reduce costs, and improve overall efficiency.
Advantage 7: Enhanced Testing and Inspection
DFM-aided PCB fabrication can also facilitate more effective testing and inspection processes, ensuring that boards meet all quality and performance requirements before they leave the factory. By designing PCBs with testability in mind, companies can reduce the time and cost associated with identifying and correcting defects. Some key testing and inspection benefits of DFM include:
- Improved access to test points and probe pads
- Reduced need for specialized testing equipment and fixtures
- Faster and more accurate automated optical inspection (AOI)
- Easier in-circuit testing (ICT) and boundary scan testing
By catching defects early in the manufacturing process, DFM can help companies avoid costly rework and delays, ultimately improving overall quality and customer satisfaction.
Advantage 8: Better Documentation and Traceability
DFM-aided PCB fabrication also promotes better documentation and traceability throughout the manufacturing process. By creating comprehensive design files and specifications that adhere to industry standards, companies can ensure that all stakeholders have access to the information they need to do their jobs effectively. Some key documentation and traceability benefits of DFM include:
- Clear and concise design files that are easy to interpret and share
- Detailed bill of materials (BOM) and assembly instructions
- Consistent naming conventions and revision control
- Complete traceability from design to finished product
By maintaining accurate and up-to-date documentation, DFM can help companies streamline communication, reduce errors, and demonstrate compliance with regulatory requirements.
Advantage 9: Improved Product Lifecycle Management
Finally, DFM-aided PCB fabrication can contribute to more effective product lifecycle management, from initial design through end-of-life disposal. By considering the entire lifecycle of the product during the design phase, companies can make informed decisions about materials, components, and processes that will impact its long-term performance and sustainability. Some key lifecycle management benefits of DFM include:
- Easier upgrades and modifications to existing designs
- Reduced obsolescence risk and longer product lifespan
- Lower maintenance and repair costs
- Improved end-of-life disassembly and recycling
By taking a holistic view of the product lifecycle, DFM can help companies create PCBs that are more durable, adaptable, and environmentally friendly, ultimately delivering greater value to customers and society as a whole.
Frequently Asked Questions (FAQ)
- What is Design for Manufacturability (DFM) in PCB fabrication?
-
DFM is a methodology that optimizes PCB designs to ensure they can be efficiently and reliably manufactured, taking into account the capabilities and constraints of the fabrication process.
-
How does DFM impact the cost of PCB fabrication?
-
DFM can help reduce the cost of PCB fabrication by minimizing the need for expensive materials, complex processes, and specialized equipment, as well as reducing the risk of defects and rework.
-
What are some key strategies for improving PCB quality and reliability through DFM?
-
Some key strategies include choosing standard component sizes and packages, minimizing the number of layers in the PCB stack-up, optimizing trace widths and spacings, and avoiding unnecessary features such as blind or buried vias.
-
How can DFM contribute to faster time-to-market for new products?
-
DFM can help accelerate the development process by reducing the need for design revisions and rework, enabling faster prototype development and testing, and facilitating smoother handoffs between design and manufacturing teams.
-
What are some environmental benefits of DFM-aided PCB fabrication?
- DFM can help reduce material consumption and waste generation, lower energy and water usage in the manufacturing process, minimize the use of toxic chemicals and hazardous substances, and facilitate easier recycling and disposal of end-of-life products.
Conclusion
In conclusion, DFM-aided PCB fabrication offers a wide range of benefits for companies looking to optimize their manufacturing processes and deliver high-quality, reliable products to market. By considering manufacturability early in the design process, companies can reduce costs, improve quality, accelerate development, and enhance overall competitiveness.
As the electronics industry continues to evolve and new technologies emerge, the importance of DFM will only continue to grow. By embracing this methodology and collaborating closely with manufacturing partners, companies can position themselves for success in an increasingly complex and dynamic marketplace.
Advantage | Key Benefits |
---|---|
Reduced Manufacturing Costs | – Lower material and labor costs – Fewer design revisions and rework – Simplified processes and equipment |
Improved PCB Quality and Reliability | – Reduced defects and failures – Better signal integrity and power distribution – Enhanced mechanical stability and durability |
Faster Time-to-Market | – Streamlined design-to-manufacturing transition – Faster prototype development and testing – Efficient production ramp-up and volume scaling |
Enhanced Design Flexibility and Innovation | – Ability to incorporate advanced technologies – Opportunities to explore alternative materials and processes – Improved collaboration between teams |
Reduced Environmental Impact | – Lower material consumption and waste – Reduced energy and water usage – Minimized use of toxic chemicals and hazardous substances |
Improved Supply Chain Management | – Better alignment between design and supplier capabilities – Reduced risk of component obsolescence and supply disruptions – Optimized inventory management |
Enhanced Testing and Inspection | – Improved access to test points and probe pads – Faster and more accurate automated optical inspection – Easier in-circuit and boundary scan testing |
Better Documentation and Traceability | – Clear and concise design files – Detailed BOM and assembly instructions – Consistent naming conventions and revision control |
Improved Product Lifecycle Management | – Easier upgrades and modifications – Reduced obsolescence risk and longer product lifespan – Lower maintenance and repair costs |
By leveraging these advantages and continuously refining their DFM practices, companies can drive innovation, quality, and competitiveness in the fast-paced world of electronics manufacturing.
Leave a Reply