HDI vs PCB: Understanding the Key Differences
In the world of printed circuit boards (PCBs), there are various types and manufacturing techniques to suit different applications and requirements. Two common terms you might come across are HDI (High-Density Interconnect) and regular PCB. Understanding the differences between HDI and regular PCB is crucial for determining which type of board is best suited for your product.
What is a Regular PCB?
A regular PCB, also known as a conventional PCB, is a printed circuit board that consists of conductive copper traces, pads, and other features etched onto a non-conductive substrate. These boards are used to mechanically support and electrically connect electronic components using conductive pathways, tracks, or signal traces.
Regular PCBs can be categorized based on the number of layers:
- Single-layer PCB: Has conductive copper traces on one side of the substrate.
- Double-layer PCB: Has conductive copper traces on both sides of the substrate.
- Multi-layer PCB: Has three or more conductive copper layers, with insulating layers separating them.
What is an HDI PCB?
HDI (High-Density Interconnect) PCBs are advanced printed circuit boards that offer higher wiring density than regular PCBs. They feature finer lines and spaces, smaller vias, and capture pads, enabling the placement of more components in a smaller area.
The main characteristics of HDI PCBs include:
- Fine pitch: HDI boards have a smaller distance between the leads of components, allowing for denser component placement.
- Microvias: These are small vias (holes) that are drilled using laser technology, enabling more efficient use of space and better electrical performance.
- Buried and blind vias: HDI boards often utilize buried vias (which connect inner layers) and blind vias (which connect an outer layer to an inner layer), further increasing the density of interconnects.
Differences between HDI and Regular PCB
Here’s a table summarizing the key differences between HDI and regular PCB:
Feature | HDI PCB | Regular PCB |
---|---|---|
Wiring Density | Higher, with finer lines and spaces | Lower, with wider lines and spaces |
Via Size | Smaller, typically using microvias | Larger, using conventional through-holes |
Component Density | Higher, allowing for more compact designs | Lower, requiring more space |
Manufacturing Process | Advanced techniques like laser drilling | Conventional drilling and etching |
Cost | Generally more expensive | Generally less expensive |
Applications | High-performance, miniaturized devices | General-purpose, larger-scale applications |
Factors to Consider When Choosing Between HDI and Regular PCB
When deciding whether your product requires an HDI or a regular PCB, there are several factors to consider:
1. Size and Component Density
If your product requires a compact design with a high component density, an HDI PCB might be the better choice. HDI technology allows for the placement of more components in a smaller area, making it ideal for miniaturized devices such as smartphones, wearables, and IoT devices.
2. Electrical Performance
HDI PCBs offer better electrical performance compared to regular PCBs. The smaller via sizes and shorter signal paths in HDI boards result in reduced signal loss, crosstalk, and electromagnetic interference (EMI). If your product requires high-speed signals or operates at high frequencies, an HDI PCB can provide superior performance.
3. Cost Considerations
HDI PCBs generally come with a higher price tag compared to regular PCBs due to the advanced manufacturing techniques and materials involved. However, the cost difference has been decreasing over time as HDI technology becomes more prevalent. It’s essential to weigh the cost against the benefits and requirements of your product.
4. Manufacturing Complexity
The manufacturing process for HDI PCBs is more complex than that of regular PCBs. It involves advanced techniques like laser drilling, sequential lamination, and precise alignment. If your product requires quick turnaround times or has simpler design requirements, a regular PCB might be sufficient.
5. Application and Industry Standards
Different industries and applications may have specific requirements or standards that dictate the use of HDI or regular PCBs. For example, the aerospace and defense industries often require HDI boards for their high-reliability and space-saving needs. It’s crucial to consider the specific requirements of your industry and target market when making the decision.
How to Determine if Your Product Needs an HDI or Regular PCB
To determine whether your product requires an HDI or a regular PCB, follow these steps:
-
Assess the size and component density: Evaluate the physical dimensions and component count of your product. If you need to fit a large number of components in a small space, an HDI PCB might be necessary.
-
Consider the electrical performance requirements: Analyze the signal speeds, frequencies, and integrity requirements of your product. If you need high-speed signals or low signal loss, an HDI PCB can offer better performance.
-
Evaluate the cost implications: Obtain quotes for both HDI and regular PCB Options from manufacturers. Compare the costs against your budget and the expected benefits of using an HDI board.
-
Review the manufacturing complexity: Assess the design complexity and turnaround time requirements of your product. If you have a simpler design or need faster production, a regular PCB might suffice.
-
Check industry standards and regulations: Research the specific requirements and standards of your industry and target market. Ensure that your chosen PCB type complies with any necessary regulations.
-
Consult with PCB experts: Engage with experienced PCB designers or manufacturers to get their insights and recommendations based on your product’s specific requirements.
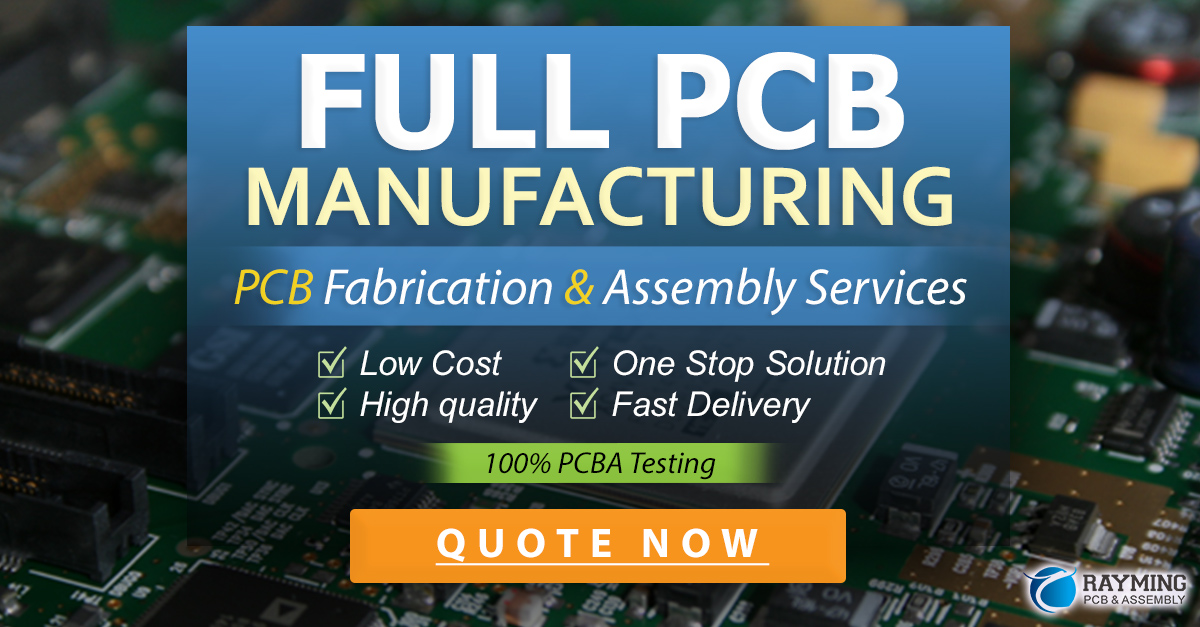
FAQ
1. Can I use both HDI and regular PCB in the same product?
Yes, it’s possible to use both HDI and regular PCB sections in the same product, depending on the specific requirements of different parts of the circuit. This hybrid approach can help optimize cost and performance.
2. Are HDI PCBs always more expensive than regular PCBs?
While HDI PCBs are generally more expensive than regular PCBs due to the advanced manufacturing techniques and materials used, the cost difference has been decreasing as HDI technology becomes more widespread and accessible.
3. What are the main applications for HDI PCBs?
HDI PCBs are commonly used in applications that require high component density, compact size, and superior electrical performance. Examples include smartphones, wearable devices, IoT devices, medical equipment, and aerospace and defense systems.
4. Can I convert my existing regular PCB design to an HDI PCB?
Converting a regular PCB design to an HDI PCB is possible, but it requires a redesign process to incorporate the unique features and manufacturing techniques of HDI technology. It’s essential to work with experienced PCB designers to ensure a smooth transition.
5. How do I find a reliable HDI PCB Manufacturer?
To find a reliable HDI PCB manufacturer, research and compare different companies based on their experience, capabilities, quality certifications, and customer reviews. Look for manufacturers that specialize in HDI technology and have a proven track record of delivering high-quality boards. Requesting quotes and samples from multiple manufacturers can also help you make an informed decision.
Conclusion
Determining whether your product requires an HDI or a regular PCB involves evaluating various factors such as size, component density, electrical performance, cost, manufacturing complexity, and industry standards. HDI PCBs offer higher wiring density, better electrical performance, and compact designs, making them suitable for applications that require miniaturization and high-speed signals. On the other hand, regular PCBs are less expensive and sufficient for general-purpose applications with lower density requirements.
By assessing your product’s specific needs, consulting with experts, and weighing the benefits against the costs, you can make an informed decision on whether an HDI or regular PCB is the best fit for your project. Remember, the choice between HDI and regular PCB is not always clear-cut, and a hybrid approach combining both types can sometimes provide the optimal solution.
As technology continues to advance and the demand for smaller, high-performance devices grows, the use of HDI PCBs is likely to increase across various industries. Staying informed about the latest developments in PCB manufacturing and working closely with experienced professionals can help you navigate the decision-making process and ensure the success of your product.
Leave a Reply