What is PCB Insulation?
PCB insulation refers to the protective layers and materials used in printed circuit boards (PCBs) to electrically isolate conductive traces and components from one another. Proper insulation is crucial for the reliable operation and longevity of PCBs, as it prevents short circuits, signal interference, and damage to sensitive electronic components.
Types of PCB Insulation Materials
There are several types of materials commonly used for PCB insulation, each with its own unique properties and advantages:
Insulation Material | Dielectric Constant | Breakdown Voltage | Thermal Conductivity (W/mK) | Applications |
---|---|---|---|---|
FR-4 | 4.2-4.9 | 50-60 kV/mm | 0.3 | General-purpose, high-volume PCBs |
Polyimide | 3.4 | 200 kV/mm | 0.1 | High-temperature, flexible PCBs |
PTFE (Teflon) | 2.1 | 60-173 kV/mm | 0.25 | High-frequency, low-loss PCBs |
Alumina (Ceramic) | 9.0-10.0 | 15-28 kV/mm | 20-30 | High-power, high-thermal-conductivity PCBs |
-
FR-4: A glass-reinforced epoxy laminate, FR-4 is the most widely used PCB insulation material due to its excellent mechanical strength, flame resistance, and electrical properties. It is suitable for most general-purpose PCB applications.
-
Polyimide: Polyimide films, such as Kapton, offer high thermal stability, flexibility, and excellent dielectric properties. They are ideal for high-temperature applications and flexible PCBs.
-
PTFE (Teflon): Polytetrafluoroethylene (PTFE) is a low-loss dielectric material with exceptional high-frequency performance. It is used in High-Frequency PCBs for applications like RF and microwave circuits.
-
Alumina (Ceramic): Alumina is a PCB-Material/”>ceramic material with high thermal conductivity and excellent electrical insulation properties. It is used in high-power PCBs and applications that require efficient heat dissipation.
The Importance of Proper PCB Insulation
Proper PCB insulation is essential for several reasons:
-
Preventing Short Circuits: Insulation materials provide a barrier between conductive traces and components, preventing unintended electrical contact and short circuits that can damage the PCB or connected devices.
-
Ensuring Signal Integrity: Insulation helps maintain the quality of electrical signals by minimizing crosstalk, electromagnetic interference (EMI), and signal attenuation. This is particularly important in high-frequency and high-speed applications.
-
Enhancing Durability: Insulation materials protect PCBs from environmental factors such as moisture, chemicals, and physical stress, extending the lifespan of the board and ensuring reliable operation in harsh conditions.
-
Meeting Safety Standards: Proper insulation is necessary to comply with various safety standards and regulations, such as UL and IEC, which ensure the safety of users and prevent potential hazards like electrical fires.
PCB Insulation Techniques
There are several techniques used to apply insulation to PCBs during the manufacturing process:
Solder Mask
Solder mask is a thin, protective layer applied to the surface of a PCB to insulate the copper traces and pads from accidental contact with solder during the assembly process. It also provides protection against oxidation and environmental damage.
Solder mask is typically applied using screen printing or photoimaging techniques:
-
Screen Printing: A thin, stencil-like screen is used to apply the solder mask ink to the PCB surface. The screen has openings that correspond to the areas where the solder mask should be applied.
-
Photoimaging: A photosensitive solder mask is applied to the entire PCB surface and then exposed to UV light through a photomask. The exposed areas harden, while the unexposed areas are removed during development, leaving the desired solder mask pattern.
Conformal Coating
Conformal coating is a protective layer applied to the assembled PCB to provide additional insulation and protection against environmental factors such as moisture, dust, and chemicals. Common conformal coating materials include:
-
Acrylic: Acrylic coatings offer good moisture resistance and are easy to apply and repair. However, they have limited chemical resistance and may not be suitable for high-temperature applications.
-
Silicone: Silicone coatings provide excellent moisture and temperature resistance, as well as flexibility. They are suitable for high-temperature applications but can be difficult to apply and repair.
-
Polyurethane: Polyurethane coatings offer good moisture, chemical, and abrasion resistance. They are widely used in automotive and aerospace applications.
Conformal Coatings are typically applied using spraying, dipping, or brushing methods, depending on the specific requirements of the PCB and the coating material used.
Insulating Substrates
The choice of PCB substrate material itself can provide insulation between layers in multi-layer PCBs. Some common insulating substrates include:
-
FR-4: As mentioned earlier, FR-4 is the most widely used PCB substrate material and provides good insulation between layers in multi-layer boards.
-
Polyimide: Polyimide substrates are used in flexible and Rigid-flex PCBs, offering excellent insulation properties and high-temperature performance.
-
PTFE: PTFE substrates are used in high-frequency PCBs due to their low dielectric constant and low dissipation factor, which help maintain signal integrity.
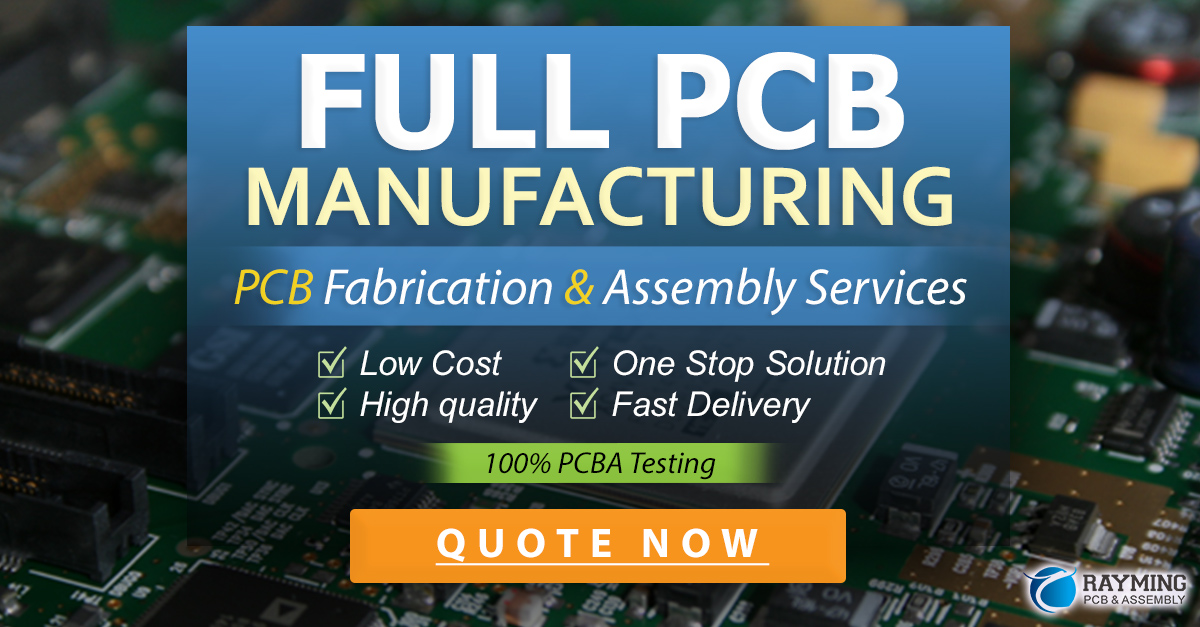
Design Considerations for PCB Insulation
When designing PCBs, several factors should be considered to ensure proper insulation and optimal performance:
-
Clearance and Creepage Distances: Clearance refers to the shortest distance through air between two conductive parts, while creepage is the shortest distance along the surface of the insulating material between two conductive parts. Adequate clearance and creepage distances must be maintained to prevent arcing and ensure proper insulation.
-
Dielectric Constant: The dielectric constant of the insulating material affects the signal propagation speed and impedance of the PCB traces. It is essential to choose an insulating material with a suitable dielectric constant for the specific application and frequency range.
-
Thermal Management: Insulating materials with high thermal conductivity, such as alumina, can help dissipate heat from high-power components and prevent thermal damage to the PCB.
-
Flexibility: In applications that require flexible or bendable PCBs, insulating materials like polyimide offer the necessary flexibility without compromising insulation properties.
-
Compatibility: The insulating material must be compatible with the PCB fabrication process, assembly methods, and operating environment. Factors such as temperature range, chemical exposure, and mechanical stress should be considered when selecting an insulating material.
FAQ
1. What is the most common PCB insulation material?
A: FR-4, a glass-reinforced epoxy laminate, is the most widely used PCB insulation material due to its excellent mechanical, thermal, and electrical properties.
2. How does PCB insulation prevent short circuits?
A: PCB insulation materials provide a physical barrier between conductive traces and components, preventing unintended electrical contact and short circuits that can damage the PCB or connected devices.
3. What is the difference between clearance and creepage in PCB design?
A: Clearance refers to the shortest distance through air between two conductive parts, while creepage is the shortest distance along the surface of the insulating material between two conductive parts. Both are important considerations for ensuring proper insulation in PCB design.
4. What are the advantages of using conformal coating on a PCB?
A: Conformal coating provides additional insulation and protection against environmental factors such as moisture, dust, and chemicals. It helps improve the reliability and longevity of the assembled PCB.
5. How does the choice of insulating substrate affect PCB performance?
A: The insulating substrate material influences the PCB’s electrical properties, such as signal propagation speed and impedance, as well as its thermal management capabilities and mechanical properties like flexibility. Choosing the appropriate insulating substrate is essential for optimizing PCB performance in specific applications.
In conclusion, PCB insulation is a critical aspect of PCB production that ensures the reliable operation, signal integrity, and longevity of printed circuit boards. By understanding the various insulation materials, techniques, and design considerations, PCB designers and manufacturers can create high-quality, dependable PCBs for a wide range of applications.
Leave a Reply