What is Solder Escape?
Solder escape, also known as Solder Wicking, is a common problem that occurs during the soldering process. It happens when molten solder flows or “wicks” up the component lead or wire, away from the intended solder joint. This can lead to a weak or incomplete solder connection, compromising the integrity and reliability of the Electronic Assembly.
Solder escape is particularly problematic with stranded wires, where the solder can wick up the individual strands, making the wire stiff and brittle. It can also occur with component leads, especially those with long exposed lengths or inadequate lead-to-hole ratios in through-hole assemblies.
Causes of Solder Escape
Several factors can contribute to the occurrence of solder escape:
Excessive Heat
Applying too much heat during soldering can cause the solder to become excessively fluid, increasing the likelihood of it wicking up the component lead or wire. Overheating can also damage components and board materials.
Prolonged Soldering Time
Holding the soldering iron on the joint for too long can lead to solder escape. The longer the heat is applied, the more time the molten solder has to flow away from the intended joint.
Inappropriate Soldering Iron Tip
Using a soldering iron tip that is too large or has the wrong shape for the specific job can result in poor heat transfer and increase the risk of solder escape. The tip should be appropriately sized and shaped to efficiently deliver heat to the joint.
Insufficient Flux
Flux is essential for promoting proper solder flow and preventing oxidation during the soldering process. If there is not enough flux or if the flux is of poor quality, it can lead to suboptimal solder flow and increase the chances of solder escape.
Improper Lead Preparation
Failing to properly prepare component leads or wires before soldering can contribute to solder escape. Leads should be clean, free of oxidation, and properly tinned to promote good solder wetting and adhesion.
Preventing Solder Escape
To prevent solder escape and ensure reliable solder joints, consider the following techniques and best practices:
Use the Right Soldering Iron Tip
Select a soldering iron tip that is appropriately sized and shaped for the specific soldering task. A tip that is too large can overheat the joint, while a tip that is too small may not provide sufficient heat transfer. Conical or chisel tips are suitable for most general-purpose soldering applications.
Control Soldering Temperature
Set the soldering iron temperature to the appropriate level for the solder alloy being used. Typical temperatures range from 600°F to 800°F (315°C to 425°C) for lead-based solders and 700°F to 900°F (370°C to 480°C) for lead-free solders. Avoid excessive temperatures that can cause overheating and solder escape.
Limit Soldering Time
Apply heat to the solder joint only for the time necessary to achieve a proper connection. Prolonged heating can lead to solder escape and damage components. A general guideline is to apply heat for no more than 2-3 seconds per joint.
Use Adequate Flux
Ensure that there is sufficient flux present during the soldering process. Flux helps to remove oxides, promotes solder flow, and prevents re-oxidation. Use a good quality flux that is compatible with the solder alloy and the components being soldered. Apply flux to the joint before soldering and add more if needed during the process.
Proper Lead Preparation
Prepare component leads and wires before soldering to promote good solder wetting and adhesion. Trim leads to the appropriate length, typically no more than 2-3mm beyond the solder joint. If necessary, strip wire insulation and twist stranded wires tightly. Pre-tin leads by applying a thin layer of solder before assembly.
Adjust Lead-to-Hole Ratio
In through-hole assemblies, ensure that the component lead diameter is appropriate for the hole size on the printed circuit board (PCB). A good lead-to-hole ratio allows for proper solder fill and reduces the risk of solder escape. Typical lead-to-hole ratios range from 1:1.5 to 1:2.5, depending on the component and PCB design.
Use Heat Sinks
When soldering temperature-sensitive components or those with long leads, consider using heat sinks to control heat transfer. Heat sinks, such as alligator clips or specialized tools, can be attached to component leads to dissipate excess heat and prevent solder escape.
Implement Proper Ventilation
Solder fumes can be harmful to health and may also contribute to solder escape by creating air currents that disrupt the soldering process. Ensure that the work area has adequate ventilation, such as fume extraction systems or fans, to remove solder fumes and maintain a stable environment.
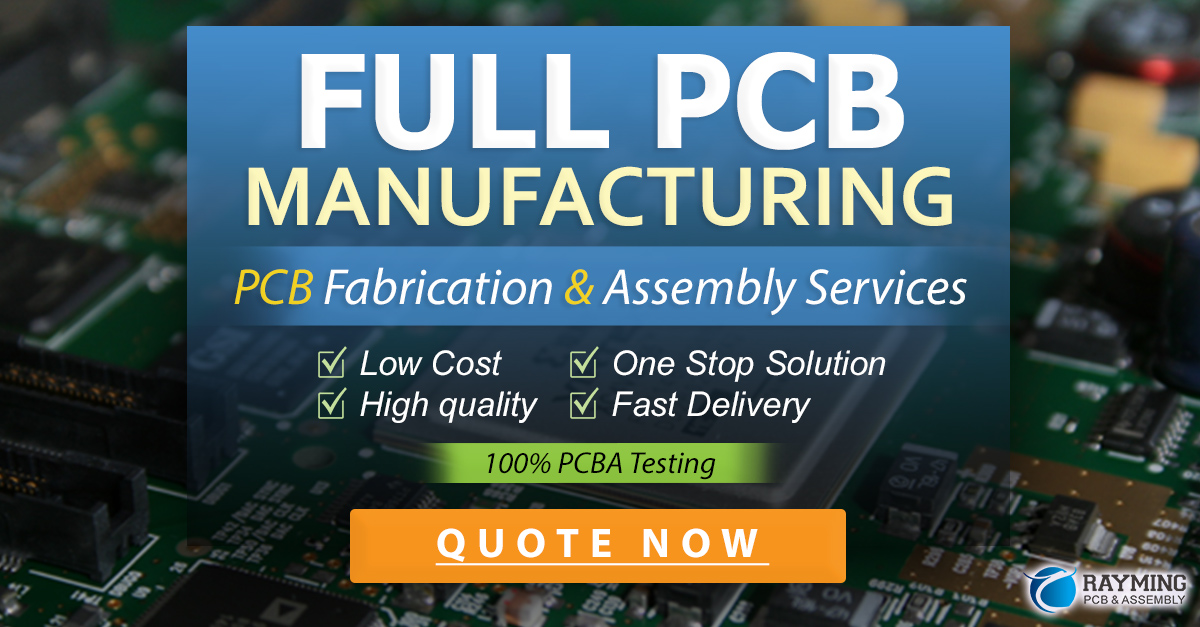
Correcting Solder Escape
If solder escape does occur, it can often be corrected using the following methods:
Solder Wick
Solder wick, also known as Desoldering Braid, is a copper braid infused with flux that can be used to remove excess solder from a joint. To use solder wick, place it on the affected area and apply the soldering iron tip to the wick. The heat will cause the excess solder to flow into the wick, removing it from the joint. Trim off the used section of the wick and repeat as needed.
Desoldering Pump
A desoldering pump, or solder sucker, is a manual tool that uses suction to remove molten solder from a joint. To use a desoldering pump, melt the solder on the joint with the soldering iron and quickly place the tip of the pump over the molten solder. Activate the pump to suck up the excess solder. Repeat as necessary to remove solder escape.
Rework and Resoldering
In some cases, it may be necessary to completely remove the affected component, clean the leads and pads, and resolder the component. This process involves using desoldering tools to remove the component, cleaning the area with solder wick or a desoldering pump, and then resoldering the component using the proper techniques to prevent solder escape.
FAQ
Q1: What is the main cause of solder escape?
A1: The main cause of solder escape is excessive heat applied during the soldering process. This can be due to a soldering iron temperature that is too high, prolonged soldering time, or an inappropriate soldering iron tip size or shape.
Q2: How can I tell if my soldering iron tip is the right size for the job?
A2: The soldering iron tip should be sized and shaped to efficiently transfer heat to the solder joint. A tip that is too large may overheat the joint and cause solder escape, while a tip that is too small may not provide enough heat. Conical or chisel tips are suitable for most general soldering applications.
Q3: What is the purpose of flux in soldering?
A3: Flux serves several important functions in the soldering process. It helps to remove oxide layers from the metals being soldered, promotes solder flow and wetting, and prevents re-oxidation of the joint during soldering. Adequate flux is essential for achieving reliable solder connections and preventing solder escape.
Q4: Can solder escape be fixed?
A4: Yes, solder escape can often be corrected using tools such as solder wick (desoldering braid) or a desoldering pump (solder sucker). These tools are designed to remove excess solder from the joint. In some cases, complete rework and resoldering of the affected component may be necessary.
Q5: Is ventilation important when soldering?
A5: Yes, proper ventilation is crucial when soldering. Solder fumes can be harmful to health if inhaled, and they can also contribute to solder escape by creating air currents that disrupt the soldering process. Use fume extraction systems or fans to remove solder fumes and maintain a stable soldering environment.
Factor | Recommendation |
---|---|
Soldering Iron Tip | Use an appropriately sized and shaped tip for efficient heat transfer |
Soldering Temperature | Set temperature based on solder alloy: 600-800°F for lead-based, 700-900°F for lead-free |
Soldering Time | Limit heat application to 2-3 seconds per joint |
Flux | Use adequate flux compatible with solder and components |
Lead Preparation | Trim leads to 2-3mm, strip and tin wires before soldering |
Lead-to-Hole Ratio | Maintain a ratio of 1:1.5 to 1:2.5 for proper solder fill |
Heat Sinks | Use heat sinks on temperature-sensitive components or long leads |
Ventilation | Implement fume extraction or fans for a stable soldering environment |
By understanding the causes of solder escape and implementing the prevention techniques and best practices outlined in this article, you can significantly reduce the occurrence of this problem and achieve more reliable solder joints in your electronic assemblies. Remember to select the right tools, control soldering parameters, use adequate flux, prepare components properly, and maintain a safe and stable soldering environment. If solder escape does occur, tools like solder wick and desoldering pumps can help in correcting the issue. With practice and attention to detail, you can master the art of soldering and produce high-quality, reliable electronic connections.
Leave a Reply