Understanding Solder wicking
What is Solder Wick?
Solder wick is a specially designed braided wire made from fine copper strands. The copper strands are typically coated with a layer of flux, which helps to facilitate the removal of solder from electronic components and printed circuit boards (PCBs). The braided structure of the solder wick allows it to absorb molten solder through capillary action, making it an effective tool for desoldering.
How Does Solder Wicking Work?
The process of solder wicking relies on the principles of heat transfer and capillary action. When the solder wick is placed on top of a solder joint and heated with a soldering iron, the flux coating on the wick activates and helps to break down the surface tension of the molten solder. As a result, the molten solder is drawn into the fine spaces between the copper strands of the wick through capillary action. This process effectively removes the solder from the joint, leaving the component or PCB ready for further work.
Applications of Solder Wicking
Solder wicking finds its application in various aspects of electronics work, including:
-
Desoldering components: When replacing or removing electronic components from a PCB, solder wicking is an efficient method to remove the solder from the component leads, allowing for easy removal.
-
Cleaning up excess solder: During the soldering process, it is common to accidentally apply too much solder to a joint. Solder wicking can be used to remove the excess solder, ensuring a clean and precise solder joint.
-
Repairing solder bridges: Solder bridges occur when solder inadvertently connects two or more pins or pads that should remain separate. Solder wicking can be used to remove the excess solder and eliminate the short circuit caused by the bridge.
-
Reworking and modifying circuits: When modifying or repairing electronic circuits, solder wicking is an essential tool for removing solder from specific areas, allowing for the repositioning of components or the addition of new connections.
Solder Wicking Techniques
To effectively use solder wick for desoldering, it is important to follow proper techniques and best practices. Here are some key steps to keep in mind:
Preparation
-
Choose the appropriate size of solder wick based on the size of the solder joint you are working on. Solder wick comes in various widths, typically ranging from 0.5mm to 2.5mm.
-
Cut a suitable length of solder wick from the roll. A length of about 10-15cm is usually sufficient for most desoldering tasks.
-
Ensure that your soldering iron is clean and properly tinned. A clean and well-maintained soldering iron tip will ensure efficient heat transfer to the solder wick.
Desoldering Process
-
Place the end of the solder wick on top of the solder joint you wish to desolder. Ensure that the wick is in direct contact with the solder.
-
Position the soldering iron tip on top of the solder wick, applying gentle pressure to ensure good contact between the wick, solder, and iron tip.
-
Apply heat to the solder wick using the soldering iron. The flux will activate, and the molten solder will begin to wick up into the braided structure of the wick.
-
Slowly move the soldering iron and solder wick along the length of the solder joint, allowing the wick to absorb the molten solder as you progress.
-
Once the solder has been successfully removed from the joint, lift the soldering iron and solder wick away from the work area.
-
Inspect the desoldered joint to ensure that all solder has been removed. If necessary, repeat the process with a fresh piece of solder wick until the joint is clean.
Cleaning and Maintenance
-
After desoldering, trim off the used portion of the solder wick using wire cutters. This will prevent the contaminated and solder-filled section of the wick from coming into contact with your next desoldering job.
-
Clean the soldering iron tip with a damp sponge or brass wool to remove any residual solder or flux.
-
Store the solder wick in a cool, dry place to prevent the flux from degrading over time.
Solder Wick Size | Typical Application |
---|---|
0.5mm – 1.0mm | Small SMD components, fine-pitch leads |
1.5mm – 2.0mm | Through-hole components, larger SMD components |
2.5mm and above | Heavy-duty desoldering, large solder joints |
Table 1: Solder wick sizes and their typical applications
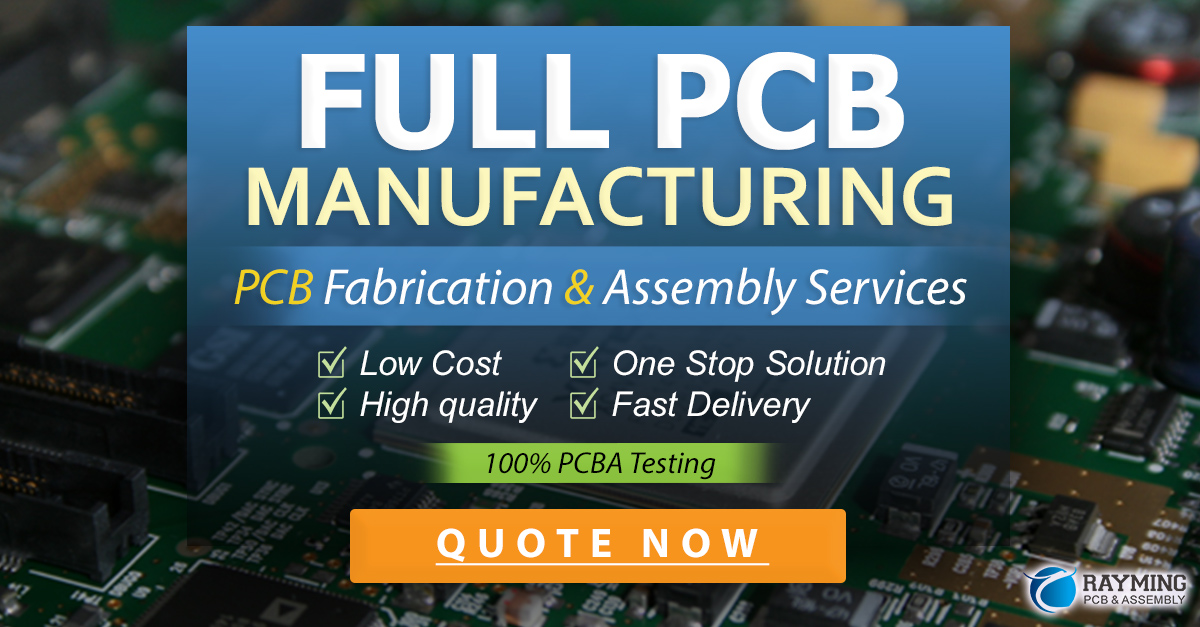
Best Practices for Solder Wicking
To achieve the best results when using solder wick, consider the following tips and best practices:
-
Use flux-coated solder wick: Always choose solder wick that is coated with flux. The flux helps to break down the surface tension of the molten solder, making it easier for the wick to absorb the solder.
-
Match the solder wick size to the job: Select the appropriate width of solder wick based on the size of the solder joint you are working on. Using a wick that is too small may result in inefficient solder removal, while using a wick that is too large can make it difficult to control and may damage nearby components.
-
Apply the right amount of heat: Ensure that your soldering iron is set to the appropriate temperature for the solder you are using. Applying too little heat will result in slow and ineffective solder removal, while too much heat can damage the PCB or components.
-
Work quickly and efficiently: Once the solder wick is heated and starts absorbing solder, work quickly to remove the solder from the joint. Prolonged heat exposure can cause damage to the PCB or components.
-
Keep the solder wick and soldering iron tip clean: Regularly trim off used sections of the solder wick and clean your soldering iron tip to ensure optimal heat transfer and prevent contamination of the desoldered joint.
Frequently Asked Questions (FAQ)
- What is the difference between solder wick and desoldering pump?
-
Solder wick and desoldering pump are both tools used for removing solder, but they work differently. Solder wick absorbs molten solder through capillary action, while a desoldering pump uses suction to remove molten solder from a joint.
-
Can I reuse solder wick?
-
It is not recommended to reuse solder wick, as the used section of the wick becomes saturated with solder and flux residue. Reusing contaminated solder wick can lead to poor desoldering performance and may introduce impurities to the solder joint.
-
What should I do if the solder wick is not absorbing the solder?
-
If the solder wick is not absorbing the solder effectively, ensure that you are applying sufficient heat to the wick and the solder joint. Also, check that the solder wick is making good contact with the solder. If the issue persists, try using a fresh piece of solder wick or a different brand.
-
Can I use solder wick on surface mount components?
-
Yes, solder wick can be used on surface mount components. However, it is essential to choose a solder wick size that is appropriate for the size of the component and its leads. Fine-pitch surface mount components may require a smaller solder wick size to avoid damaging the component or adjacent components.
-
How do I prevent the PCB from lifting when using solder wick?
- To prevent the PCB from lifting when using solder wick, avoid applying excessive heat or pressure to the PCB. Use a soldering iron with an appropriate temperature setting and apply gentle pressure when heating the solder wick. If the PCB starts to lift, remove the heat immediately and allow the area to cool before attempting to desolder again.
Conclusion
Solder wicking is an essential technique for anyone involved in electronics soldering and desoldering processes. By understanding the principles behind solder wicking, mastering the proper techniques, and following best practices, you can effectively remove solder from components and PCBs, enabling efficient repairs, modifications, and prototyping.
Remember to choose the appropriate solder wick size, use flux-coated wick, apply the right amount of heat, and work quickly and efficiently to achieve the best results. With practice and patience, you will develop the skills necessary to tackle a wide range of desoldering tasks with confidence and precision.
Leave a Reply