What is PCB Registration?
PCB registration refers to the process of aligning layers, components, and features on a printed circuit board (PCB) during manufacturing. Proper registration is critical to ensure that all elements of the PCB line up correctly, allowing for proper electrical connections and functionality.
Registration is important at several stages of PCB manufacturing:
- Aligning multiple copper layers
- Positioning solder paste on pads via a stencil
- Placing components on the board
- Aligning drilled holes and vias
Misregistration at any of these stages can lead to defects and PCB failure. For example, if copper layers are misaligned, traces may not connect properly. If solder paste is not deposited accurately on pads, components may not attach correctly. Misplaced components can cause short circuits. Misaligned drill holes may not line up with component leads.
PCB Layer Registration
Most PCBs have multiple copper layers that must be aligned precisely. The most common registration method is to use fiducial marks, which are small copper features placed in specific locations on the outer edges of the panel. Fiducial marks allow the various machines involved in PCB Fabrication to optically recognize the panel’s position and align the layers accurately.
Here are some common types of fiducial marks used for layer registration:
Fiducial Type | Description |
---|---|
Global fiducials | Used to align the entire PCB panel |
Local fiducials | Used to align specific areas or features |
Copper crosses | Copper lines in a cross shape |
Copper circles | Small round copper dots |
The registration process typically involves the following steps:
- Capture an image of the fiducial marks using a camera
- Analyze the image to determine the position of the marks
- Adjust the panel position to align with a reference point
- Verify alignment and proceed with next manufacturing step
Automating registration with machine vision systems is crucial for maintaining high accuracy and preventing misalignment issues.
Solder Paste Stencil Printing Registration
Solder paste is applied to component pads on a PCB using a stencil, which is a thin sheet of metal with cutouts that match the pad shapes. The stencil is aligned with the PCB, solder paste is wiped over the stencil to fill the openings, and then the stencil is lifted away leaving paste deposits on the pads.
Proper registration between the stencil and PCB is essential to ensure that solder paste is deposited accurately on the pads. Misregistration can cause several issues:
- Insufficient solder paste on pads, leading to poor component connections
- Excess solder paste bridging between adjacent pads, causing short circuits
- Solder paste deposited in the wrong locations
The stencil printing process uses fiducial marks to align the stencil with the PCB. The PCB and stencil each have matching fiducial marks. A machine vision system locates the fiducials and adjusts the position of the PCB and stencil to align them properly before printing.
Some key factors for successful solder paste registration include:
- Choosing appropriate fiducial mark locations and shapes
- Keeping fiducials free of solder mask or other coverings
- Ensuring fiducials have good contrast for easy optical recognition
- Proper stencil tension and gasketing to prevent paste bleed-out
- Consistent PCB positioning in the printer
Advances in 3D machine vision systems and additional up-looking vision cameras provide improved registration accuracy for Solder Paste Printing.
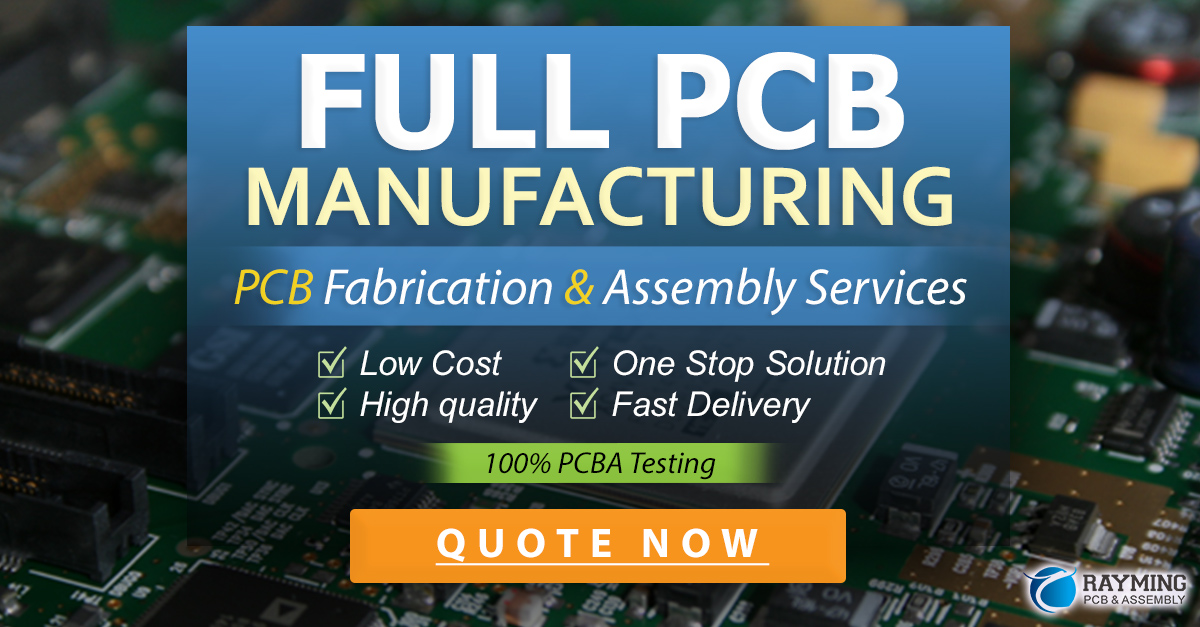
Component Placement Registration
After solder paste printing, components must be placed on the PCB and aligned with their respective pads. Pick-and-place machines use vacuum nozzles to pick up components from feeders and place them onto the solder paste deposits.
Accurate registration is critical during component placement to ensure that leads make proper contact with the solder paste and pads. Misaligned components can result in poor solder joints, skewed parts, and non-functional assemblies.
Component placement machines also rely on fiducial marks to align the PCB. Additionally, many components have their own built-in fiducials or recognizable features that the machine vision system uses to position them correctly. The placement registration process involves:
- Locating the PCB position using fiducials
- Picking up the component and checking its alignment in the nozzle
- Recognizing the component’s placement position based on PCB fiducials or component features
- Placing the component and verifying positioning
Some challenges in placement registration include:
- Components that lack clear optical features
- Shiny or reflective surfaces that interfere with vision systems
- Variations in component packaging
- Extremely small or fine-pitch components
Advanced placement machines use high-resolution cameras, enhanced lighting control, and sophisticated software algorithms to overcome these challenges and maintain placement accuracy.
Drilling and Routing Registration
PCBs require drilled holes and routed edges that must be positioned accurately relative to the copper features and components. Drilling creates holes for vias, component leads, and mounting. Routing cuts the individual boards out of the panel.
Drilling and routing also rely on fiducial marks for registration. The fiducials allow the machines to locate the position of the PCB Layers and drill/route in the correct locations. Challenges for drilling and routing registration include:
- Worn or broken bits that affect hole positioning
- Material thickness variations that change drilling depth
- Alignment issues when drilling through multiple layers
- Burring or tearing of material during routing
Proper registration helps ensure that drilled holes align with component leads and routing does not cut into vital PCB features. Checking hole quality and routing path accuracy is important for catching registration issues.
FAQ
What happens if PCB registration is inaccurate?
Inaccurate registration can cause several problems, including:
- Open circuits due to misaligned traces or unconnected component leads
- Short circuits from Solder Bridges or component leads touching adjacent pads
- Components placed in the wrong locations or orientations
- Non-functional boards due to misaligned or missing features
Catching registration issues early in the manufacturing process is important for minimizing scrap and rework.
How can I improve PCB registration?
Some ways to improve PCB registration include:
- Using clear, high-contrast fiducial marks in appropriate locations
- Ensuring consistent PCB positioning and clamping in machines
- Regularly calibrating and maintaining registration systems
- Investing in advanced machine vision systems and software
- Verifying registration accuracy at each stage of manufacturing
- Designing PCBs with registration in mind, such as providing space for fiducials
What are some common causes of PCB misregistration?
Common causes of misregistration include:
- Worn or damaged fiducials that are difficult to recognize
- Incorrect fiducial design or placement on the PCB
- Warped or inconsistent PCB material
- Machine vision calibration or lighting issues
- Improperly tensioned stencils or screens
- Component packaging variations or irregular shapes
- Mechanical issues with pick-and-place nozzles or drill bits
Identifying and addressing the root causes of misregistration is key to improving quality.
How accurate does PCB registration need to be?
Registration accuracy requirements depend on the specific PCB design and components used. Some general guidelines include:
- Solder paste printing: ±50 microns
- Component placement: ±30 microns for standard components, ±10 microns for fine-pitch
- Drilling: ±100 microns
- Routing: ±500 microns
More advanced PCB designs and smaller components may require even tighter registration tolerances. It’s important to understand the requirements for each specific PCB and ensure that registration systems can meet those needs.
What role does PCB design play in registration?
PCB designers can take several steps to improve registration:
- Providing sufficient space and clearance for fiducial marks
- Choosing appropriate fiducial shapes and sizes
- Placing fiducials close to critical features
- Avoiding designs with extremely tight tolerances that are difficult to achieve
- Specifying clear registration requirements for manufacturers
- Communicating any special needs, such as non-standard components or unique assembly processes
Close collaboration between PCB designers and manufacturers is key to ensuring that registration requirements are understood and achievable. By working together and considering registration at each stage of design and manufacturing, it’s possible to produce high-quality, reliable PCBs consistently.
Leave a Reply