Introduction to Phototools in PCB Manufacturing
Phototools, also known as photomasks or artwork films, are essential components in the printed circuit board (PCB) manufacturing process. They are used to transfer the desired circuit pattern onto the Copper-Clad Laminate board through a photolithographic process. Phototools play a crucial role in ensuring the accuracy, precision, and repeatability of the PCB Fabrication process.
In this comprehensive article, we will delve into the world of phototools for PCB Image Transfer. We will explore the different types of phototools, their properties, and their applications in the PCB industry. Additionally, we will discuss the advantages and limitations of using phototools, as well as the latest advancements and future trends in this field.
Table of Contents
- What are Phototools?
- Types of Phototools
- Film-based Phototools
- Glass-based Phototools
- Digital Phototools
- Properties of Phototools
- Optical Density
- Resolution
- Dimensional Stability
- Durability
- Photolithographic Process in PCB Manufacturing
- Step 1: Substrate Preparation
- Step 2: Photoresist Application
- Step 3: Exposure
- Step 4: Development
- Step 5: Etching
- Step 6: Photoresist Removal
- Advantages of Using Phototools
- Limitations of Phototools
- Latest Advancements and Future Trends
- Frequently Asked Questions (FAQ)
- Conclusion
- References
What are Phototools?
Phototools are high-resolution, high-contrast transparent films or glass plates that contain the desired circuit pattern for a PCB. They serve as a template for transferring the circuit design onto the copper-clad laminate board during the photolithographic process. Phototools are typically created using computer-aided design (CAD) software and then printed onto a transparent substrate using a high-resolution printer or plotter.
The primary function of a phototool is to selectively block or allow light to pass through specific areas of the PCB substrate during the exposure step of the photolithographic process. The areas where light passes through the phototool will cause the photoresist to react, while the areas blocked by the opaque regions of the phototool will remain unaffected.
Types of Phototools
There are three main types of phototools used in the PCB industry: film-based, glass-based, and digital phototools. Each type has its own unique properties, advantages, and limitations, which we will explore in the following sections.
Film-based Phototools
Film-based phototools are the most common type of phototools used in the PCB industry. They are made of a transparent polyester film, such as Mylar or polyethylene terephthalate (PET), which is coated with a light-blocking emulsion. The desired circuit pattern is then printed onto the film using a high-resolution photoplotter or imagesetter.
Film-based phototools offer several advantages, including:
– Cost-effectiveness: Film-based phototools are relatively inexpensive compared to other types of phototools, making them a popular choice for small to medium-scale PCB production.
– Ease of handling: Film-based phototools are lightweight and flexible, making them easy to handle and store.
– Availability: Film-based phototools are widely available and can be produced by most PCB Manufacturers or third-party suppliers.
However, film-based phototools also have some limitations:
– Limited resolution: The resolution of film-based phototools is typically limited to around 10-20 microns, which may not be sufficient for high-density or fine-pitch PCB designs.
– Dimensional instability: Film-based phototools are susceptible to dimensional changes due to temperature and humidity fluctuations, which can lead to registration errors during the photolithographic process.
– Limited durability: Film-based phototools can become scratched or damaged with repeated use, affecting the quality of the PCB image transfer.
Glass-based Phototools
Glass-based phototools, also known as emulsion masks or silver halide masks, are made of a glass substrate coated with a light-sensitive emulsion. The desired circuit pattern is then exposed onto the emulsion using a high-resolution laser or electron beam writer.
Glass-based phototools offer several advantages over film-based phototools:
– Higher resolution: Glass-based phototools can achieve resolutions as high as 1-2 microns, making them suitable for high-density and fine-pitch PCB designs.
– Dimensional stability: Glass-based phototools are more dimensionally stable than film-based phototools, as they are less susceptible to temperature and humidity changes.
– Durability: Glass-based phototools are more durable and resistant to scratches and damage compared to film-based phototools.
However, glass-based phototools also have some limitations:
– Higher cost: Glass-based phototools are more expensive to produce than film-based phototools, making them less cost-effective for small to medium-scale PCB production.
– Fragility: Glass-based phototools are brittle and can easily break if not handled carefully, requiring special storage and handling procedures.
– Limited availability: Glass-based phototools are not as widely available as film-based phototools and may require specialized equipment and expertise to produce.
Digital Phototools
Digital phototools, also known as direct imaging (DI) or maskless lithography, are a relatively new technology in the PCB industry. Instead of using physical phototools, digital phototools use a high-resolution digital projector or laser to directly expose the desired circuit pattern onto the photoresist-coated PCB substrate.
Digital phototools offer several advantages over traditional film-based and glass-based phototools:
– Improved flexibility: Digital phototools allow for quick and easy changes to the circuit design without the need to produce new physical phototools.
– Reduced cost: By eliminating the need for physical phototools, digital phototools can significantly reduce the cost and lead time of PCB production.
– Higher resolution: Digital phototools can achieve resolutions as high as 1-2 microns, similar to glass-based phototools.
– Increased throughput: Digital phototools can expose the entire PCB substrate in a single step, reducing the overall exposure time and increasing production throughput.
However, digital phototools also have some limitations:
– Higher equipment cost: The equipment required for digital phototools, such as high-resolution digital projectors or lasers, can be significantly more expensive than traditional phototool production equipment.
– Limited substrate size: Digital phototools are currently limited to smaller PCB substrate sizes due to the limitations of the digital projection or laser exposure systems.
– Potential for stitching errors: When exposing larger PCB Substrates, digital phototools may require multiple exposures that need to be stitched together, which can lead to potential alignment or stitching errors.
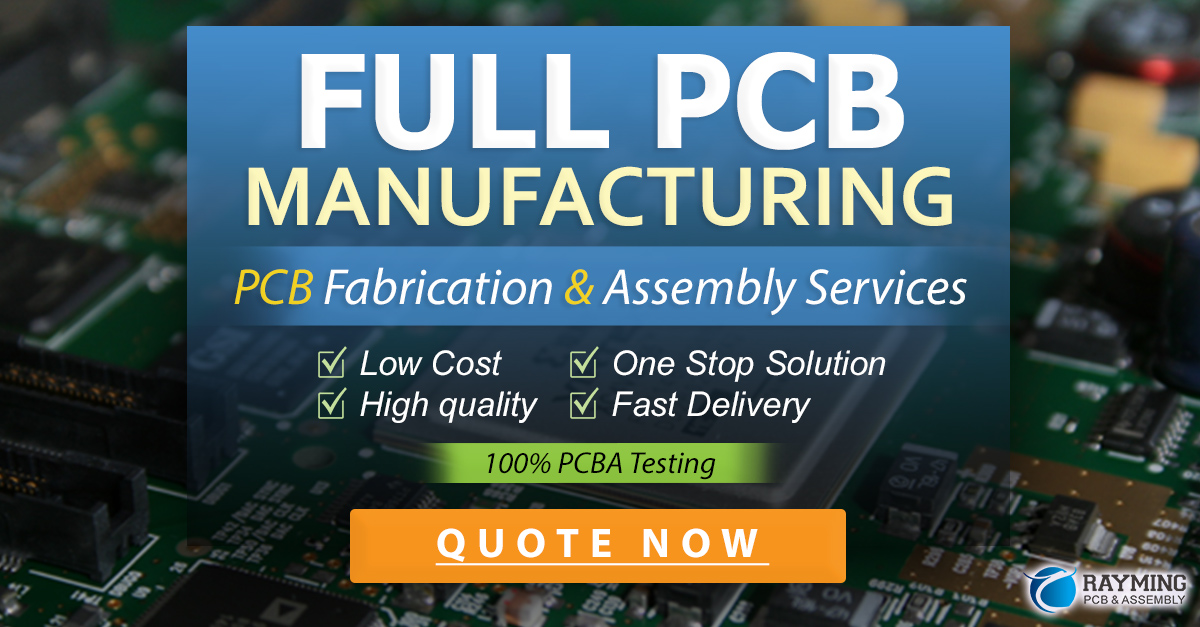
Properties of Phototools
To ensure the quality and accuracy of the PCB image transfer process, phototools must possess several key properties, including optical density, resolution, dimensional stability, and durability.
Optical Density
Optical density (OD) is a measure of the light-blocking capability of a phototool. It is defined as the logarithm of the ratio of the incident light intensity to the transmitted light intensity. A higher optical density indicates a greater ability to block light and create sharper, more well-defined circuit patterns.
Phototools typically have an optical density range of 3.0 to 5.0, with higher values being preferred for high-resolution and fine-pitch PCB designs. The optical density of a phototool can be affected by several factors, such as the type and thickness of the light-blocking emulsion, the quality of the printing or exposure process, and the age and storage conditions of the phototool.
Resolution
Resolution refers to the smallest feature size that can be accurately reproduced by a phototool. It is typically measured in microns (μm) or mils (1 mil = 25.4 μm). The resolution of a phototool depends on several factors, including the type of substrate (film or glass), the quality of the printing or exposure process, and the properties of the light-blocking emulsion.
Film-based phototools typically have a resolution range of 10-20 microns, while glass-based phototools and digital phototools can achieve resolutions as high as 1-2 microns. Higher resolution phototools are necessary for high-density and fine-pitch PCB designs, where the spacing between circuit features is minimal.
Dimensional Stability
Dimensional stability refers to the ability of a phototool to maintain its original dimensions and shape under various environmental conditions, such as temperature and humidity changes. Dimensional stability is critical for ensuring accurate registration and alignment of the circuit pattern during the photolithographic process.
Film-based phototools are more susceptible to dimensional changes compared to glass-based phototools, as the polyester film substrate can expand or contract with temperature and humidity fluctuations. Glass-based phototools, on the other hand, are more dimensionally stable due to the rigid nature of the glass substrate.
To minimize dimensional changes, phototools should be stored and used in a controlled environment with stable temperature and humidity levels. Additionally, the use of low-distortion polyester films and stress-relief techniques during the printing or exposure process can help improve the dimensional stability of film-based phototools.
Durability
Durability refers to the ability of a phototool to withstand repeated use and handling without deterioration or damage. Durable phototools are essential for maintaining consistent quality and reducing the need for frequent replacements, which can be costly and time-consuming.
Glass-based phototools are generally more durable than film-based phototools, as the glass substrate is more resistant to scratches, abrasions, and other forms of physical damage. However, glass-based phototools are also more brittle and can easily break if not handled carefully.
Film-based phototools can be made more durable by using thicker polyester films and protective coatings, such as hard-coat or scratch-resistant layers. Proper storage and handling procedures, such as using clean gloves and storing phototools in dust-free environments, can also help extend their useful life.
Photolithographic Process in PCB Manufacturing
Phototools are a key component of the photolithographic process used in PCB manufacturing. This process involves transferring the desired circuit pattern from the phototool onto the copper-clad laminate board using light-sensitive photoresist and chemical etching. The photolithographic process consists of several steps, which we will discuss in detail below.
Step 1: Substrate Preparation
The first step in the photolithographic process is to prepare the PCB substrate. This involves cleaning the copper-clad laminate board to remove any contaminants or oxides that may interfere with the photoresist adhesion. The substrate is typically cleaned using a chemical solution, such as an alkaline cleaner or a micro-etch solution, followed by a deionized water rinse and drying.
Step 2: Photoresist Application
Once the substrate is cleaned, a thin layer of photoresist is applied to the surface of the copper-clad laminate. Photoresist is a light-sensitive polymer that changes its solubility when exposed to light. There are two types of photoresist: positive and negative.
Positive photoresist becomes more soluble in the developer solution when exposed to light, while negative photoresist becomes less soluble when exposed to light. The choice of photoresist depends on the specific PCB design and manufacturing process.
The photoresist is typically applied using a spin coating process, where the substrate is spun at high speeds while the photoresist is dispensed onto the surface. The spinning action spreads the photoresist evenly across the substrate, creating a uniform layer with a controlled thickness.
Step 3: Exposure
After the photoresist is applied, the PCB substrate is exposed to light through the phototool. The phototool is placed on top of the photoresist-coated substrate, and a collimated light source, such as a mercury vapor lamp or a UV LED, is used to expose the photoresist.
The light passes through the transparent areas of the phototool and causes a chemical reaction in the photoresist, while the opaque areas of the phototool block the light and leave the photoresist unchanged. This selective exposure creates a latent image of the desired circuit pattern in the photoresist layer.
The exposure time and intensity are critical parameters in the photolithographic process, as they determine the quality and resolution of the final circuit pattern. Overexposure or underexposure can lead to problems such as loss of fine features, poor adhesion, or incomplete development.
Step 4: Development
After exposure, the PCB substrate is placed in a developer solution that selectively dissolves the exposed (positive photoresist) or unexposed (negative photoresist) areas of the photoresist layer. The developer solution is typically an aqueous alkaline solution, such as sodium hydroxide or potassium hydroxide.
The development process is carefully controlled to ensure that only the desired areas of the photoresist are removed, while the rest of the photoresist remains intact. The development time, temperature, and agitation are critical parameters that affect the quality and resolution of the final circuit pattern.
Step 5: Etching
Once the photoresist has been developed, the PCB substrate is ready for etching. Etching is the process of removing the unwanted copper from the substrate, leaving only the desired circuit pattern.
The most common etching method is chemical etching, which involves immersing the PCB substrate in an etchant solution, such as ferric chloride or ammonium persulfate. The etchant solution selectively dissolves the copper in the areas not protected by the photoresist, while leaving the copper in the areas covered by the photoresist intact.
The etching process is carefully controlled to ensure that the copper is removed evenly and completely, without undercutting or damaging the desired circuit pattern. The etching time, temperature, and agitation are critical parameters that affect the quality and resolution of the final circuit pattern.
Step 6: Photoresist Removal
After etching, the remaining photoresist is removed from the PCB substrate using a stripping solution, such as sodium hydroxide or monoethanolamine. The stripping solution dissolves the photoresist, leaving the final circuit pattern on the copper-clad laminate.
The PCB substrate is then rinsed with deionized water and dried, completing the photolithographic process. The resulting PCB can then undergo additional processing steps, such as drilling, plating, and surface finishing, to create the final product.
Advantages of Using Phototools
Phototools offer several advantages in the PCB manufacturing process, making them a widely used and essential component. Some of the key advantages of using phototools include:
-
High resolution and accuracy: Phototools enable the transfer of high-resolution and accurate circuit patterns onto the PCB substrate, ensuring the proper functionality and performance of the final product.
-
Consistency and repeatability: Phototools provide a consistent and repeatable method for transferring circuit patterns, reducing the likelihood of errors or defects in the PCB manufacturing process.
-
Scalability: Phototools can be easily scaled up or down to accommodate different PCB sizes and designs, making them suitable for a wide range of applications and production volumes.
-
Cost-effectiveness: Despite the initial cost of producing phototools, they offer a cost-effective solution for PCB manufacturing, particularly for high-volume production runs, as they can be reused multiple times.
-
Compatibility with various PCB materials: Phototools are compatible with a wide range of PCB substrate materials, including FR-4, polyimide, and flexible substrates, making them versatile tools in the PCB industry.
Limitations of Phototools
While phototools offer many advantages, they also have some limitations that should be considered when selecting the appropriate PCB manufacturing process. Some of the main limitations of phototools include:
-
Limited resolution for fine-pitch designs: Film-based phototools may not provide sufficient resolution for very fine-pitch or high-density PCB designs, requiring the use of more advanced techniques, such as glass-based phototools or direct imaging.
-
Potential for dimensional instability: Film-based phototools are susceptible to dimensional changes due to temperature and humidity fluctuations, which can lead to registration errors and reduced accuracy in the PCB manufacturing process.
-
Cost and lead time for phototool production: The production of phototools requires specialized equipment and expertise, which can add to the overall cost and lead time of the PCB manufacturing process, particularly for low-volume or prototype runs.
-
Handling and storage requirements: Phototools, particularly glass-based phototools, require careful handling and storage to prevent damage or contamination, which can add to the complexity and cost of the PCB manufacturing process.
Latest Advancements and Future Trends
The PCB industry is continuously evolving, driven by the demand for smaller, faster, and more complex electronic devices. As a result, new technologies and trends are emerging to address the limitations of traditional phototools and improve the efficiency and accuracy of the PCB manufacturing process.
Leave a Reply