What is PCB tolerance?
PCB tolerance is the permissible deviation from the nominal or designed values for various aspects of a printed circuit board. These aspects include:
- Board dimensions
- Hole sizes and positions
- Conductor widths and spacing
- Solder mask and silkscreen alignment
- Component placement
Tolerances are essential because manufacturing processes inherently introduce some level of variation. By specifying tolerances, designers and manufacturers can ensure that the PCBs produced will function correctly and meet the required specifications, even with slight variations.
Why is PCB tolerance important?
Maintaining appropriate PCB Tolerances is crucial for several reasons:
-
Functionality: Proper tolerances ensure that the PCB functions as intended. If the conductor widths or spacing are outside the specified tolerances, it may lead to short circuits, open circuits, or signal integrity issues.
-
Compatibility: PCBs often need to interface with other components, such as connectors, switches, or enclosures. Adhering to tolerances ensures that the PCB fits properly and aligns with these components.
-
Manufacturing efficiency: Well-defined tolerances help streamline the manufacturing process by providing clear guidelines for production. This reduces the likelihood of errors and improves overall quality control.
-
Cost control: Tighter tolerances generally increase manufacturing costs, as they require more precise equipment and processes. By specifying appropriate tolerances based on the application’s requirements, designers can strike a balance between functionality and cost-effectiveness.
Factors affecting PCB tolerance
Several factors influence the achievable tolerances in PCB manufacturing:
-
Manufacturing process: Different PCB Fabrication processes, such as etching, drilling, and plating, have their own inherent limitations and variability. The chosen manufacturing process will impact the achievable tolerances.
-
Material properties: The properties of the PCB substrate material, such as its dimensional stability and thermal expansion, can affect the tolerances. Some materials are more stable than others, allowing for tighter tolerances.
-
Board complexity: More complex PCB designs with high-density layouts, fine pitch components, or multi-layer structures may require tighter tolerances to ensure proper functionality and manufacturability.
-
Equipment capabilities: The precision and accuracy of the manufacturing equipment used, such as drills, routers, and imaging systems, will determine the achievable tolerances.
-
Environmental factors: Temperature, humidity, and other environmental conditions during manufacturing can impact the dimensions and properties of the PCB materials, affecting the final tolerances.
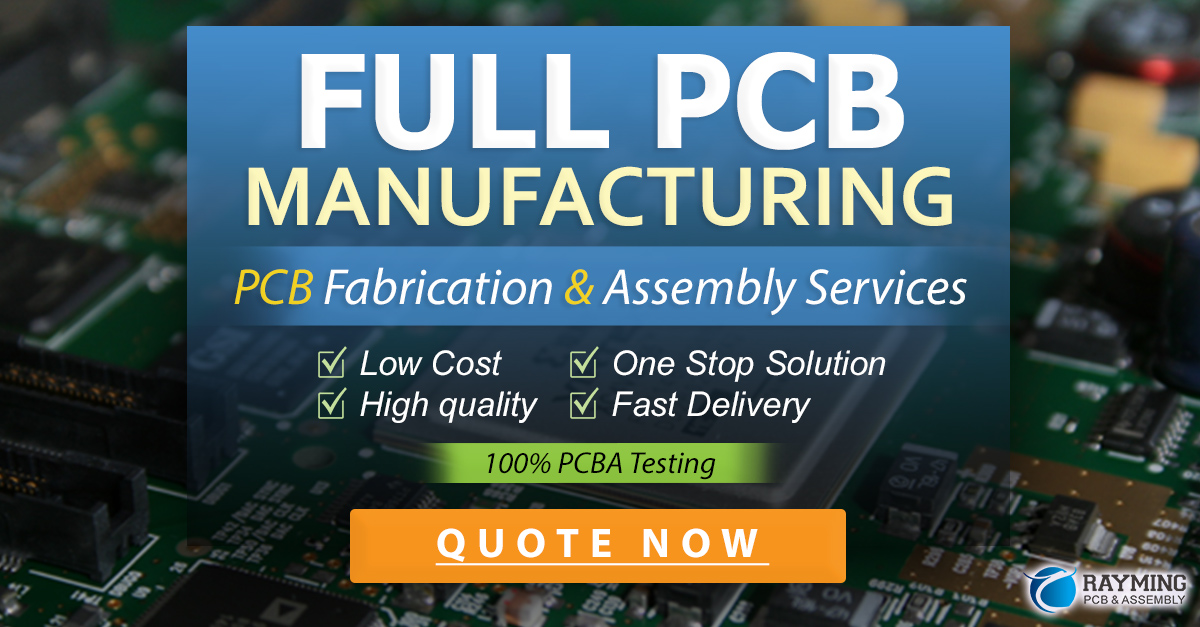
Typical PCB tolerances
The typical tolerances for various aspects of PCB design and manufacturing are as follows:
Aspect | Typical Tolerance |
---|---|
Board outline | ± 0.25 mm |
Hole size (plated) | ± 0.08 mm |
Hole size (non-plated) | ± 0.15 mm |
Hole position | ± 0.15 mm |
Conductor width | ± 0.08 mm |
Conductor spacing | ± 0.08 mm |
Solder mask alignment | ± 0.15 mm |
Silkscreen alignment | ± 0.15 mm |
Component placement | ± 0.25 mm |
These tolerances are general guidelines and may vary depending on the specific manufacturer, PCB technology, and application requirements. It is essential to consult with the PCB manufacturer and adhere to their recommended tolerances for optimal results.
Designing for PCB tolerances
To ensure that your PCB design is manufacturable and functions as intended, consider the following best practices when designing for tolerances:
-
Understand the manufacturing process: Familiarize yourself with the limitations and capabilities of the PCB manufacturing process you will be using. This knowledge will help you make informed decisions about design features and tolerances.
-
Communicate with the manufacturer: Engage in open communication with your PCB manufacturer early in the design process. Discuss your requirements, design features, and any specific tolerances needed. The manufacturer can provide guidance on what is achievable and suggest design optimizations.
-
Use standard tolerances when possible: Whenever possible, design your PCB using standard tolerances that are readily achievable by most manufacturers. This approach reduces manufacturing complexity and costs while improving the likelihood of a successful production run.
-
Consider the impact of tolerances: When designing your PCB, consider how the tolerances of various features may impact the overall functionality and compatibility of the board. For example, ensure that the tolerance stackup of component placement, hole sizes, and pad dimensions allows for proper assembly and soldering.
-
Provide clear documentation: Create comprehensive and clear documentation for your PCB design, including detailed drawings, specifications, and tolerance requirements. This documentation will help the manufacturer understand your expectations and reduce the risk of misinterpretation.
-
Allow for reasonable tolerances: While it may be tempting to specify extremely tight tolerances for all aspects of your PCB, this can significantly increase manufacturing costs and complexity. Strike a balance between functionality and cost by allowing for reasonable tolerances where possible.
-
Perform design reviews: Conduct thorough design reviews, including a manufacturability review, to identify any potential issues related to tolerances. This process can help catch and address problems early in the design cycle, saving time and resources.
FAQ
1. What happens if the PCB tolerances are not met?
If the PCB tolerances are not met, several issues can arise, such as:
- Difficulty in assembling the PCB or integrating it with other components
- Reduced functionality or performance due to improper connections or signal integrity issues
- Increased risk of short circuits or open circuits
- Potential reliability issues over time
To avoid these problems, it is crucial to work closely with the PCB manufacturer and ensure that the specified tolerances are achievable and maintained throughout the production process.
2. Can I request tighter tolerances for my PCB?
Yes, you can request tighter tolerances for your PCB, but it is essential to consider the following:
- Tighter tolerances may increase manufacturing costs, as they require more precise equipment and processes
- Not all manufacturers may be capable of consistently achieving the requested tolerances
- The specific PCB technology and materials used may limit the achievable tolerances
It is advisable to discuss your requirements with the PCB manufacturer and find a balance between the desired tolerances and cost-effectiveness.
3. How can I ensure that my PCB design is manufacturable?
To ensure that your PCB design is manufacturable, follow these steps:
- Familiarize yourself with the capabilities and limitations of the intended manufacturing process
- Communicate openly with your PCB manufacturer and seek their guidance on design optimization
- Use standard tolerances whenever possible
- Consider the impact of tolerances on functionality and compatibility
- Provide clear and comprehensive documentation, including drawings and specifications
- Conduct thorough design reviews, including a manufacturability review
By following these best practices, you can improve the chances of a successful and cost-effective PCB Production run.
4. What are the most critical tolerances in PCB design?
The most critical tolerances in PCB design depend on the specific application and requirements of the board. However, some of the most commonly critical tolerances include:
- Conductor width and spacing: These tolerances impact signal integrity, current-carrying capacity, and the risk of short circuits or open circuits.
- Hole size and position: Accurate hole sizes and positions are crucial for proper component assembly and alignment.
- Solder mask and silkscreen alignment: Misaligned solder mask or silkscreen can lead to assembly difficulties and visual defects.
The criticality of tolerances may also vary based on the PCB technology, such as high-density interconnect (HDI) or high-frequency designs.
5. How can I balance PCB tolerances with cost-effectiveness?
To balance PCB tolerances with cost-effectiveness, consider the following strategies:
- Use standard tolerances whenever possible, as they are more easily achievable and less expensive to manufacture
- Identify the critical tolerances for your application and prioritize them, while allowing for reasonable tolerances in less critical areas
- Engage in open communication with your PCB manufacturer to understand their capabilities and get their input on cost-effective design choices
- Consider the overall impact of tolerances on the PCB’s functionality and long-term reliability, as investing in appropriate tolerances can save costs in the long run
- Optimize your design to minimize the need for extremely tight tolerances, such as by using wider traces or larger components when possible
By striking a balance between required tolerances and cost-effectiveness, you can ensure that your PCB meets its functional requirements while staying within budget constraints.
Conclusion
PCB tolerance is a critical aspect of printed circuit board design and manufacturing. By understanding the concept of tolerances, their impact on PCB functionality and manufacturability, and the typical tolerance values for various PCB features, designers can create boards that meet their intended requirements while being cost-effective to produce.
Effective communication with PCB Manufacturers, adherence to best design practices, and a focus on balancing functionality with cost-effectiveness are key to successfully managing PCB tolerances. By following these guidelines and working closely with experienced professionals, designers can ensure that their PCBs are manufactured to the highest standards and perform reliably in their intended applications.
Leave a Reply